本文小编分享一篇来自国内某单位的文章,是一篇双光子3d打印玻璃衍射透镜的实际应用案例文章。这个技术有很多非常实际的应用,比如,快速制造玻璃材质光学系统的样品,等等,以及复杂光学结构的制造
本文利用的工艺和前面提到的一样
工艺流程:
在含sio2的光刻胶上打印出所需的微观结构
并将未聚合的材料洗掉从而产生所谓的生坯部分。
对生坯部分进行热处理。在这里,首先在600°C下去除聚合的粘合剂基质,然后在1,300°C下进行烧结过程。在此步骤中,当二氧化硅纳米颗粒融合时,零件的体积会缩小,从而显示出纯熔融石英玻璃的 3D 微观结构。
划重点(双光子3D打印代工)
在光纤端面亦或其他基底材料上通过双光子3D打印的方式一直是科研工作者研究的关注点,但是由于高精度双光子3D打印的设备极其昂贵,技术也较为前沿,许多科研工作者乏于寻找可靠的,高效率的加工提供商。。
因此如果您有需求,可以联系小编为您推荐成熟的双光子3D打印企业,加速您的创新。
如果你也爱好 半导体,光学,光纤,硅光集成等技术及应用,可以添加小编,一起畅聊技术,市场和应用。
看原文请联系小编免费领取
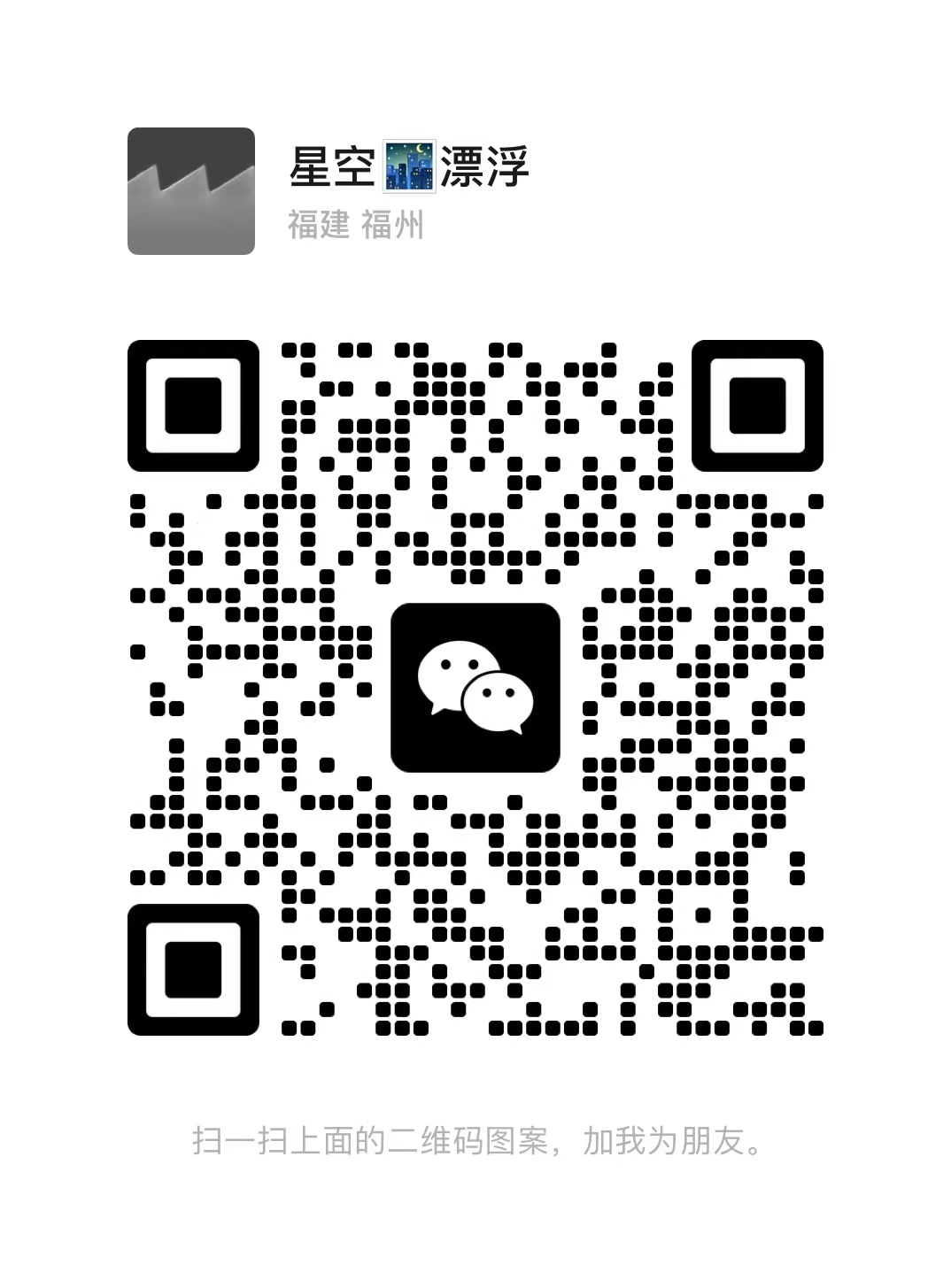
三维打印可以制造具有复杂结构的石英玻璃光学器件。然而,收缩仍然是玻璃光学器件高精度3D打印的重大障碍。在这里,我们使用双光子聚合 (2PP) 技术 3D 打印了具有低横向收缩率 (<4%) 的 Dammann 光栅 (DG)。该过程包括两个步骤:用 515 nm 飞秒激光对双光子可聚合玻璃浆料进行图案化以形成所需的结构,并将结构脱脂/烧结成透明致密的二氧化硅玻璃。烧结结构在横向和纵向上表现出明显的收缩率。随着结构长径比的增加,横向收缩减小,纵向收缩增大。具体而言,纵横比约为60的结构实现了1.1%的最小横向收缩率,相应的纵向收缩率为61.7%。表面粗糙度低于20 nm的打印DG表现出良好的光束整形性能。所提出的技术为二氧化硅衍射光学元件的快速原型制作开辟了可能性。
1. 引言
石英玻璃是一种非常有价值且在光学系统中广泛使用的材料,因为它具有卓越的光学透明度等卓越性能,以及其强大的热、化学和机械稳定性[1,2]。近年来,二氧化硅玻璃的三维(3D)打印因其在创建具有复杂结构的组件方面的灵活性而引起了越来越多的兴趣,这些组件具有挑战性使用传统技术(如研磨,抛光或湿化学蚀刻)制造[3]。通过熔融沉积成型(FDM)直接打印可以生产大型透明组件,但不适合生产高分辨率玻璃组件[4,5]。间接3D打印技术,如立体光刻(SL)[6-8]、直接墨水书写(DIW)[9-10]和双光子聚合(2PP)[11-13],使用纳米复合材料或溶胶-凝胶混合物等玻璃前体来制造玻璃结构。通过随后的热处理,印刷的前驱体可以转化为透明和致密的玻璃。这些技术能够生产具有良好光学性能和高分辨率的玻璃组件。在这些技术中,2PP以最高的加工分辨率脱颖而出,可以制造出具有微米级精度、最小峰谷偏差和低表面粗糙度的微观结构[14]。然而,这些使用玻璃前驱体的间接3D打印技术由于有机物的烧毁和剩余无机基团的固结而引起较大的收缩。这种收缩通常是各向同性的,大约在20%-60%的范围内,这取决于前体中存在的无机基团的比例[14-16]。这种不可避免的收缩对达曼光栅 (DG) 等无机玻璃衍射光学元件 (DOE) 的成功 3D 打印提出了重大挑战。DG是仅通过二元表面浮雕剖面在远场中产生结构照明的重要元件[17–19]。收缩会导致DGs内相变点的相对位置发生变化,从而显著影响其分束性能。
在本文中,我们提出了一种用于 Dammann 光栅 3D 打印的 2PP 工艺,具有最小的横向收缩率。为515 nm 2PP体系开发了一种由SiO 2 纳米颗粒和双光子固化树脂组成的玻璃浆料。随后,结构化玻璃浆料通过热处理工艺转化为二氧化硅玻璃。打印结构在横向和纵向上表现出不同的收缩率。在纵横比约为60的结构中,最小横向收缩率为1.1%,而相应的纵向收缩率达到61.7%。低横向收缩率确保了所制备的二元相结构的精度,而较大的纵向收缩率有助于烧结后表面明显更光滑。打印的DGs表现出较好的光束整形性能,表面粗糙度在20 nm以下。
2. 方法
2.1 材料
为515 nm 2PP开发的玻璃浆料是22wt%羟基-乙基甲基丙烯酸酯(HEMA,阿拉丁,上海,中国),33wt%三羟甲基丙烷乙氧基化物三丙烯酸酯(阿拉丁,上海,中国)和45wt%无定形二氧化硅纳米颗粒(Aerosil OX50,赢创,德国)的混合物,与0.2 phr双-(2,4,6-三甲基苯甲酰基)苯基膦氧化膦(Irgacure 819,阿拉丁,上海,中国)和2phr对苯二酚(阿拉丁, Shanghai, China)作为抑制剂。
在制备过程中,将HEMA和三羟甲基丙烷乙氧基化物三丙烯酸酯按比例混合。随后,通过机械搅拌器将二氧化硅纳米颗粒缓慢地添加到混合物中。接下来,将光引发剂和抑制剂添加到浆液中。发现均质浆料含有大量气泡,随后通过超声波脱气去除这些气泡。
2.2 2PP直接激光书写
衍射微光学元件是使用实验室开发的2PP激光系统制造的,如图1(a)所示。2PP 装置的主要组件包括飞秒激光源、高精度平移台和扫描振镜。激光源的工作波长为 515 nm,重复频率为 1 kHz,脉冲持续时间为 400 fs。扫描振镜用于精确控制激光束在水平XY平面上的位置,因为它根据设计沿着指定的路径进行扫描。在Z方向上,焦点位置由平移级调节。平移平台的行程范围和定位精度分别为25 mm和0.1 𝜇𝑚�� 。使用数值孔径 (NA) 为 0.42 的 20 ×× 物镜将 515 nm 飞秒激光束聚焦在玻璃浆料内,导致 2PP 并在焦点处凝固,如图 1(b) 所示。玻璃浆料以 7000 rpm 的速度旋涂在石英玻璃基板(25 × 25 mm,厚度为 2 mm 2 )上,以获得薄而平坦的液层。这有助于减少加工过程中由于液体表面不平整而导致的折射造成的误差,并有助于在显影过程中去除未固化的树脂。在印刷过程之后,将样品浸入甲醇中 10 分钟以去除未固化的玻璃浆料。在随后的整个热处理过程中,所得的生坯成分一直保留在基材上。
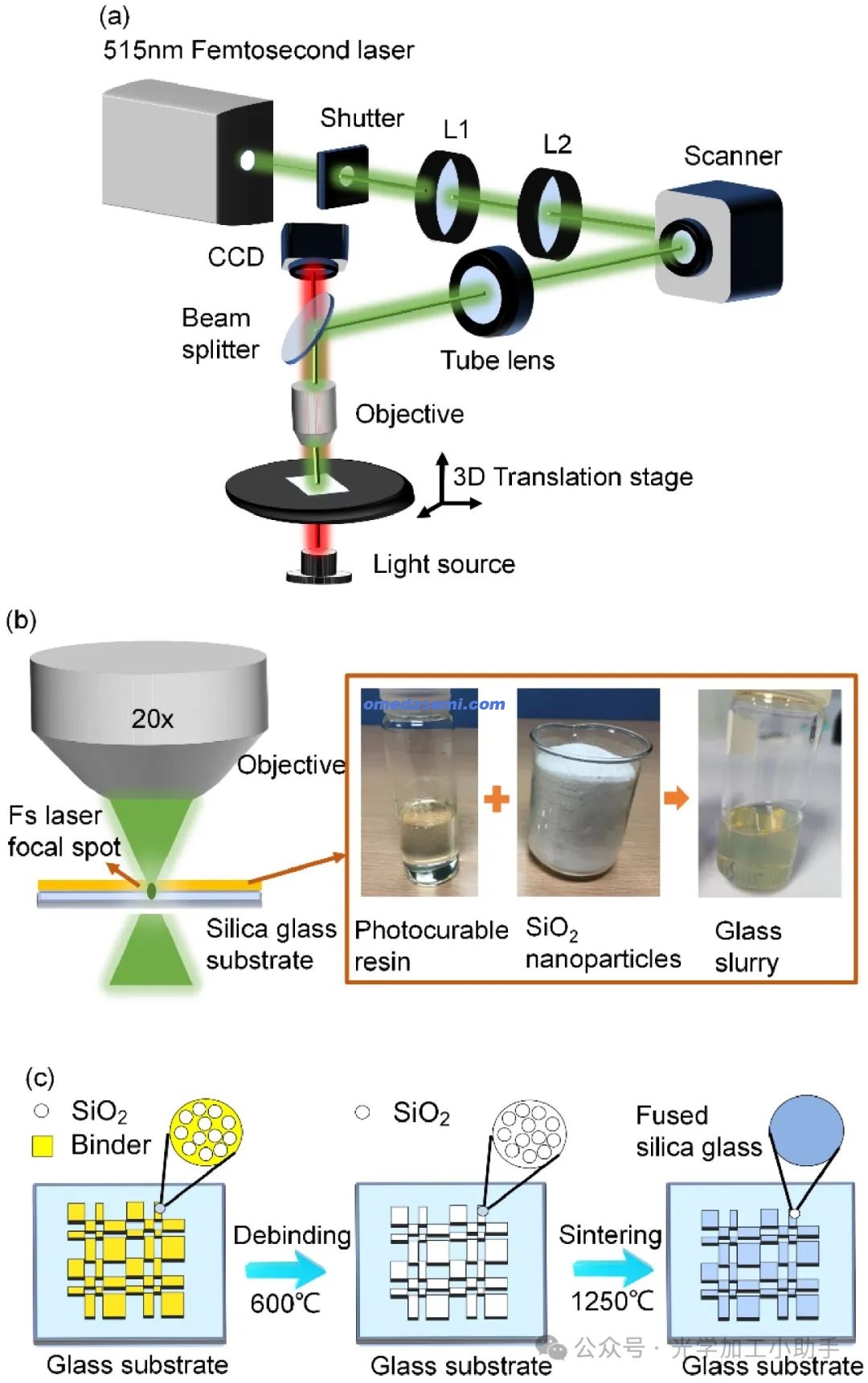
图 1.(a) 2PP 3D打印系统示意图。(b)玻璃浆料的2PP工艺,由SiO 2 纳米颗粒和光固化树脂组成。(c) 热处理工艺示意图。有机粘结剂在600度下脱脂除去 ∘C∘C ,所得多孔结构随后在1250度下烧结致密成二氧化硅玻璃 ∘C∘C 。
2.3 热处理
热处理工艺示意图如图1(c)所示。脱脂过程在马弗炉的空气气氛中进行,加热速率为0.5 ∘C/𝑚𝑖𝑛∘C/��� ,最高温度为600 ∘C∘C 。脱脂后,将所得多孔部分转移到管式炉中,在1250 ∘C∘C 下以低于5Pa的压力以3°C的升温速率烧结 ∘C/𝑚𝑖𝑛∘C/��� 。
3. 结果与讨论
3.1 印刷结构的收缩率
在脱脂过程中,打印结构中的有机粘结剂通过热变形去除,产生多孔的“棕色部分”。“棕色部分”可以通过高温真空烧结致密化成透明的石英玻璃。烧结后,由于有机物的燃烧和剩余颗粒的固结,结构不可避免地会收缩。烧结零件的收缩率通常是各向同性的,在20%至60%的范围内,取决于无机颗粒的负载[6,11,14,16]。然而,在我们的实验中,烧结结构表现出非各向同性收缩,其特点是横向和纵向收缩率之间存在显着差异。
图 2 显示了具有不同宽度和高度的制造矩形结构的扫描电子显微镜 (SEM) 图像和表面轮廓。这些表面轮廓的测量是通过激光共聚焦显微镜进行的。激光共聚焦显微镜能够通过光学切片来测量微观结构的三维形态特征。这个过程涉及从样品中的不同焦平面捕获图像,然后用于重建样品形态的详细三维表示。使用专用分析软件提取烧结前后打印结构的表面轮廓。为了便于定量比较,表1显示了烧结前后打印结构的平均高度和宽度。由于打印结构的侧壁略有倾斜,因此使用半高全宽 (FWHM) 来表示结构的宽度以进行比较。结构 1 至 4 表现出相似的高度,范围从 3.4μm 到 5.0μm,同时宽度从 21.0μm 到 200.2μm 增加。随着结构宽度的扩大,横向收缩率从18.6%减小到1.1%,而纵向收缩率从56.0%增加到61.7%。此外,对于宽度一致约为50μm且高度从4.3μm增加到25.7μm的结构2、5和6,高度的增加会导致横向收缩率从7.4%上升到22.1%,而纵向收缩率从60.5%下降到37.7%。总之,印刷结构的纵横比在决定其横向和纵向收缩率方面起着关键作用。随着纵横比的增加,横向收缩率减小,而纵向收缩率增加,如图3所示。结构 4 的横向收缩率最小为 1.1%,纵横比为 58.8。除非我们打印具有特定纵横比的结构,以确保等效的水平和垂直收缩率,否则不会出现各向同性收缩。
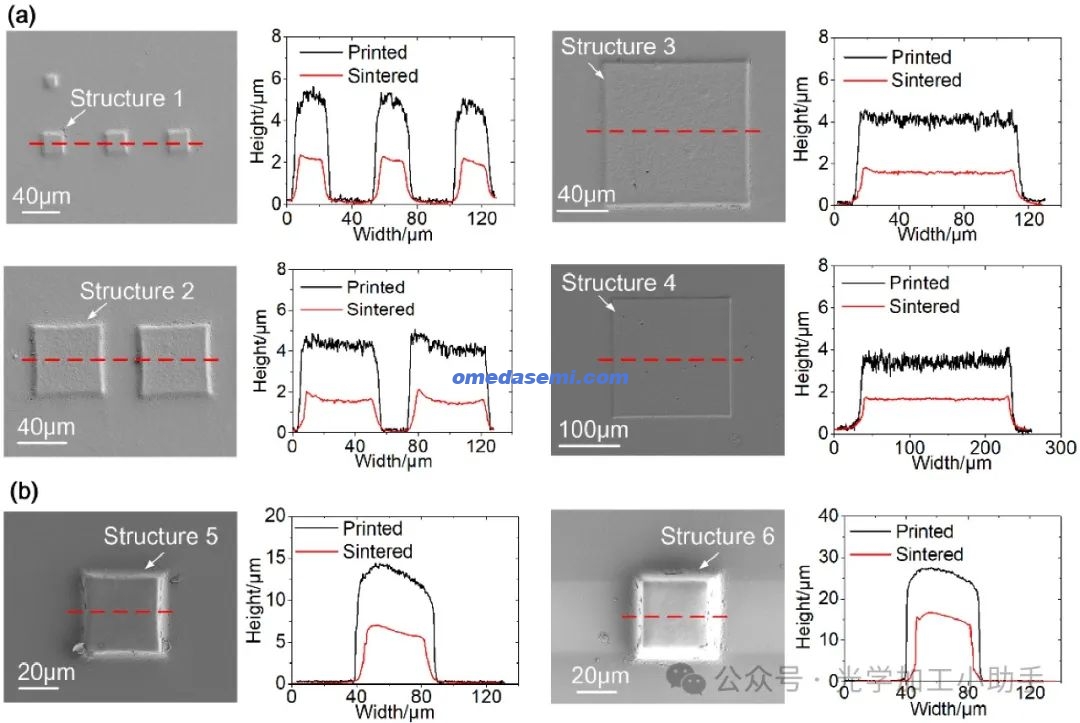
图2.采用激光共聚焦显微镜测量了不同几何尺寸矩形结构的SEM图像,利用激光共聚焦显微镜测量了热处理前后沿红色虚线的结构轮廓。(a) 不同宽度的结构。(b) 不同高度的建筑物。
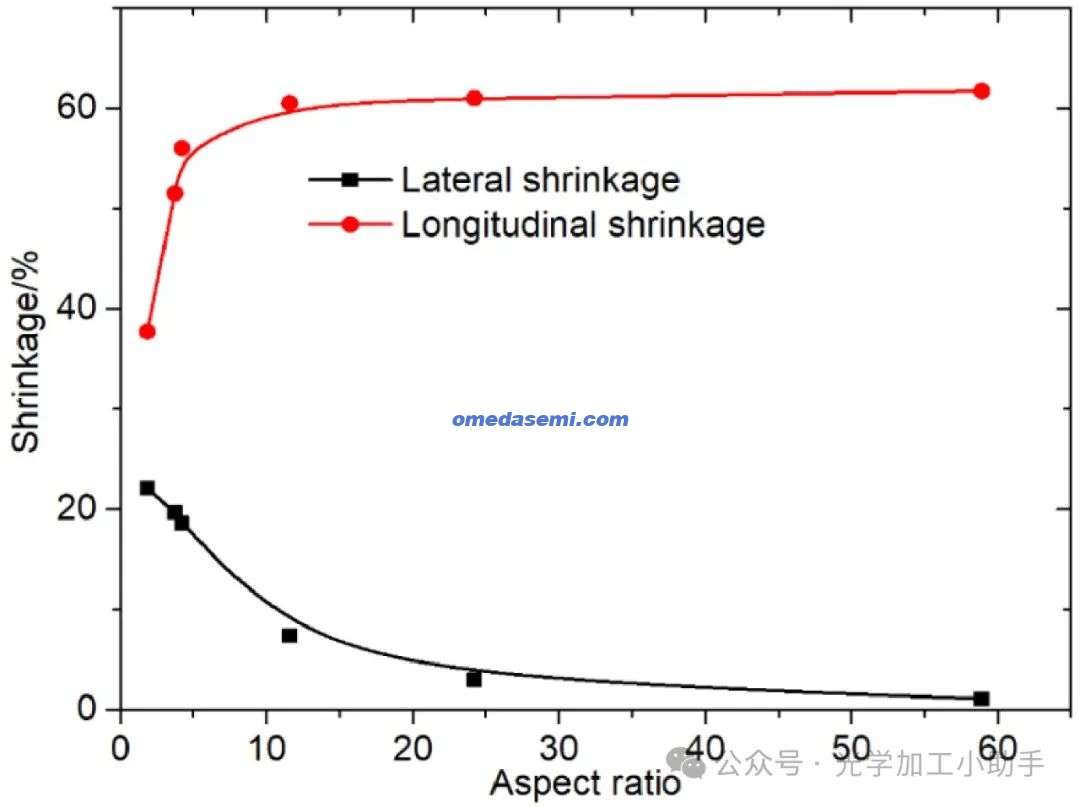
图3.不同长径比的横向收缩和纵向收缩评估。
我们认为,横向收缩率和纵向收缩率的差异可归因于烧结过程中SiO 2 纳米颗粒与玻璃基板之间的结合强度。图4显示了在不同温度下烧结的印刷结构的微观结构,可以帮助我们了解固结过程。在600°C下脱脂后,除去打印结构中的有机粘合剂,从而形成由SiO 2 颗粒形成的松散互连网络。在1150°C下烧结的样品显示了由表面扩散引起的颗粒之间的初始颈部形成[20]。随着烧结温度的升高,纳米颗粒网络被平滑(在1200°C时),并去除孔隙以形成致密的玻璃(在1250°C下)。据报道,非晶纳米颗粒的烧结机理是粘性流动,颗粒间范德华相互作用作为额外的驱动力[ 21–23]。在这项工作中,结构被打印在石英玻璃基板上,并在整个热处理过程中留在基板上。纳米颗粒和基板之间的键合限制了纳米颗粒在靠近基板的粘性流动,从而导致最小的横向收缩。同时,在致密化过程中,这些纳米颗粒之间的剩余空隙被上覆的纳米颗粒通过粘性流动过程填充,导致显着的纵向收缩。然而,随着结构高度的增加,基体施加在纳米颗粒上的力减小,导致横向收缩率增加和纵向收缩率降低。
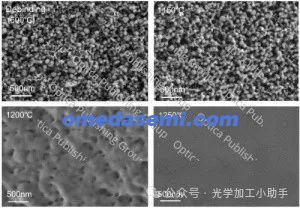
图4.不同温度下烧结样品的微观结构。
我们认为,我们研究中的低横向收缩可归因于两个主要因素:(1)在我们的2PP工艺中使用基于纳米颗粒的玻璃浆料,以及(2)在整个热处理阶段将制造的结构保留在石英玻璃基板上。特别是,只有当微观结构的纵横比超过20时,低横向收缩效应才显著,如结构3和4所示。同时,值得注意的是,这些结构表现出相当大的纵向收缩率,高达60%。为了抵消这种纵向收缩,必须提高印刷结构的高度。此外,增加玻璃浆料中的固体负荷可以减少横向和纵向收缩。然而,过多的固体负载会导致浆料粘度增加,从而影响印刷过程的成功完成。
3.2 危险品的制造和表征
印刷结构的这些收缩特性使 2PP 工艺非常适合制造二元光学器件,例如 DG。在危险品中,结构通常具有较大的纵横比(>20),宽度范围为数十微米,高度范围为数百纳米。当利用 2PP 工艺制造 DG 结构时,低横向收缩率导致印刷 DG 的相变点误差最小。此外,显着的纵向收缩将有助于烧结后的表面更光滑。
在这里,我们设计并制造了奇数阶的 2D DG,并进行了性能表征。我们实验中的DG被设计为将入射光束分成具有均匀功率强度的N×N点阵列(阶数O = N)。利用模拟退火算法[ 19],得到了奇数阶数为O = 7的DG,其过渡点位于(0.23191, 0.42520, 0.52571)。图5(a)显示了DG的一个单位,其中浅灰色块表示零相位,蓝色表示过渡点上π相移。危险品的局部相位由相应的结构高度决定。为了实现π相,每个相块的高度可以通过以下公式计算
ℎ=𝜆/2(𝑛−1)
其中 𝜆� 表示入射光的波长,n是玻璃的折射率。在我们的实验中,我们使用波长为 650 nm 的准直激光作为入射光束。该特定波长下石英玻璃的折射率为1.456。因此,计算出对应于相移π的相块的理论高度为712.7 nm。相块的宽度与衍射阶数(O值)和光栅周期相互关联。光栅周期设置为200 μm,确保每个相块保持超过25的纵横比。这种深思熟虑的选择保证了低于 5% 的横向收缩率。
最小的横向收缩在危险品的制造中至关重要。对于单个扁平结构,通过了解收缩率,然后适当地设计结构,可以很容易地解决收缩问题,如图5(b)所示。然而,对于由具有对角线连接的单个矩形结构组成的二维危险品,收缩问题无法通过调整结构尺寸来轻松解决。如图5(c)所示,如果我们放大整个DG的尺寸,显着的横向收缩将导致相块的相对位置发生变化。图5(d)显示了三个矩形结构的实验结果,其横向收缩率为25.6%。这种横向收缩会导致DG内相块的相对位置发生显著变化,从而大大影响分束性能[ 24]。收缩也是无法通过修改单个结构的尺寸来补偿的,因为扩大每个块会导致截面相互重叠,如图5(e)所示。这项工作提供了一种实现最小横向收缩的简单方法,使其适用于二元光学制造。
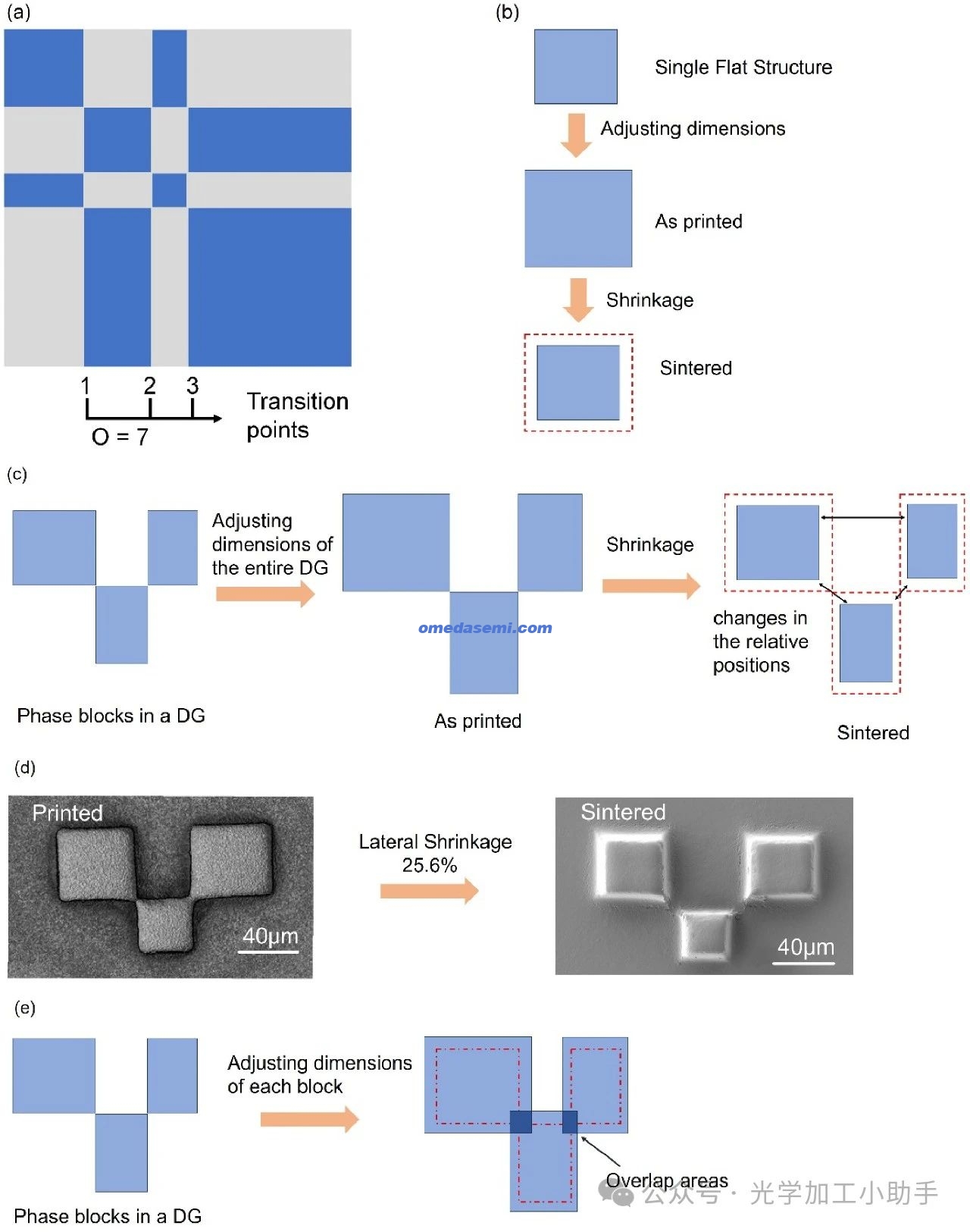
图 5.(a) 设计危险品的一个单位,按O=7级计算,并标明过渡点。浅灰色区域表示零相位,而蓝色表示过渡点上π相移。(b) 通过调整尺寸可以很容易地解决单个扁平结构的收缩问题。(c) 扩大整个危险品的尺寸将导致相块的相对位置发生变化。(d) 3个横向收缩率为25.6%的矩形结构的例子。(e) 扩大每个单独的块将导致各部分相互重叠。
使用以下参数进行打印:激光功率 20%,阴影距离 1 μm,扫描速度 1000 μm/s。在打印DG的相块之前,使用相同的参数打印厚度约为2μm的基层。该基础层旨在补偿准确识别基板和玻璃浆液之间界面位置以及任何基板倾斜的错误。基层完成后,平移台的z轴向下移动1.8μm,以开始DG的打印。
O = 7 阶的制造危险品如图 6(a) 所示。基板尺寸为 700 μm 700 μm,DG 尺寸为 600 μm 600 μm ×× 。图6(b)显示了烧结前后20 μm×20 μm区域表面粗糙度的比较。用原子力显微镜(AFM)表征的表面粗糙度在烧结后从Rq = 52.6 nm降低到Rq = 19.9 nm,明显小于红色激光的波长。
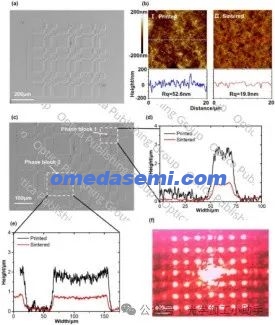
图 6.(a) 印刷和烧结DG的SEM图像。(b) 烧结前后 20 μm × 20 μm 区域的表面粗糙度。(c)-(e) 使用激光共聚焦显微镜捕获烧结前后不同尺寸的两相块的表面轮廓,以分析收缩率。相块1的横向收缩率为3.3%,纵向收缩率为64.4%,而相块2的横向收缩率为2.2%,纵向收缩率为59.0%。(f) DG在CCD上产生的激光光斑阵列。
通过使用激光共聚焦显微镜捕获相块的表面轮廓来分析烧结过程中的收缩。图6(c)显示了相块1和相块2,分别代表DG中最小和最大的相块。它们在烧结前后的表面轮廓的比较在图6(d)和图6(e)中相应地描述。相块 1 的横向收缩率为 3.3%(宽度从 21.2 μm 减小到 20.5 μm),而纵向收缩率为 64.4%(平均高度从 2.28 μm 减小到 0.81 μm)。同样,测得的相块 2 的横向收缩率为 2.2%(宽度从 94.4 μm 减小到 92.3 μm),纵向收缩率为 59.0%(平均高度从 1.76 μm 减小到 0.72 μm)。由于相块 1 和相块 2 都印在相同的基层上,因此它们表现出相似的收缩率。图6(f)显示了DG使用CCD生成的7 ×× 7个激光点阵列记录。突出的中心亮点的存在源于激光束尺寸超过光栅尺寸,并进一步受到光栅结构中高度误差的影响。我们测量了每个光斑的相对强度(相对于总入射激光强度)以确定衍射效率。计算出衍射效率为23.46%,低于理论值61.82%。衍射效率的这种差异主要归因于相块内存在高度误差[24]。在这项研究中,采用了 20× 目标,数值孔径为 0.42。采用更高数值孔径的物镜有可能提高加工精度。
4. Conclusion 4. 结论
综上所述,我们开发了一种由SiO 2 纳米颗粒和光固化树脂组成的玻璃浆料,用于515 nm 2PP工艺,并首次展示了石英玻璃DGs的3D打印。通过在600°C下脱脂和在1250°C下烧结,印刷结构可以转化为透明和致密的石英玻璃。烧结结构在横向和纵向上表现出不同的收缩率。随着结构长宽比的增加,横向收缩减小,而纵向收缩增大。我们在纵横比约为 60 的结构中实现了 1.1% 的最小横向收缩率。此外,超过60%的相对较大的纵向收缩有助于烧结后的表面更加光滑。这些收缩特性使我们的 2PP 工艺非常适合制造二元光学器件,例如 DG。我们设计并打印了奇数阶为 O = 7 的 DG,其横向收缩率小于 4%,表面光滑,Rq =19.9 nm。通过使用打印的 DG,入射红色激光成功地形成了 7 × 7 激光光斑阵列。开发的玻璃浆料具有最小的横向收缩率,结合 2PP 3D 打印,引入了一种生产二元 DOE 的新方法。此外,我们的方法还可以应用于多级或连续表面轮廓结构的制造,从而实现复杂的光学功能。