本文的实战案例,作者打印了 玻璃光栅,和 玻璃微透镜
为了满足日益增长的高精度玻璃微光学需求,并解决当前三维(3D)打印光学器件的主要局限性,我们开发了一种液体、无溶剂、二氧化硅前驱体和双光子3D打印工艺。印刷的光学元件可以在低至600°C的温度下完全转化为透明的无机玻璃,收缩率为17%。我们已经展示了整个过程,从材料开发、印刷到印刷玻璃微光学器件的性能评估。实现了各向同性收缩率、微米分辨率、低峰谷偏差( <100nm<100nm )和低表面粗糙度 ( <6nm<6nm ) 的玻璃微光学器件的 3D 打印。该报道的技术将能够实现以前使用传统玻璃光学制造工艺无法实现的复杂玻璃微光学器件的快速原型制作。
划重点(双光子3D打印代工)
在光纤端面亦或其他基底材料上通过双光子3D打印的方式一直是科研工作者研究的关注点,但是由于高精度双光子3D打印的设备极其昂贵,技术也较为前沿,许多科研工作者乏于寻找可靠的,高效率的加工提供商。。
因此如果您有需求,可以联系小编为您推荐成熟的双光子3D打印企业,加速您的创新。
如果你也爱好 半导体,光学,光纤,硅光集成等技术及应用,可以添加小编,一起畅聊技术,市场和应用。
看原文请联系小编免费领取
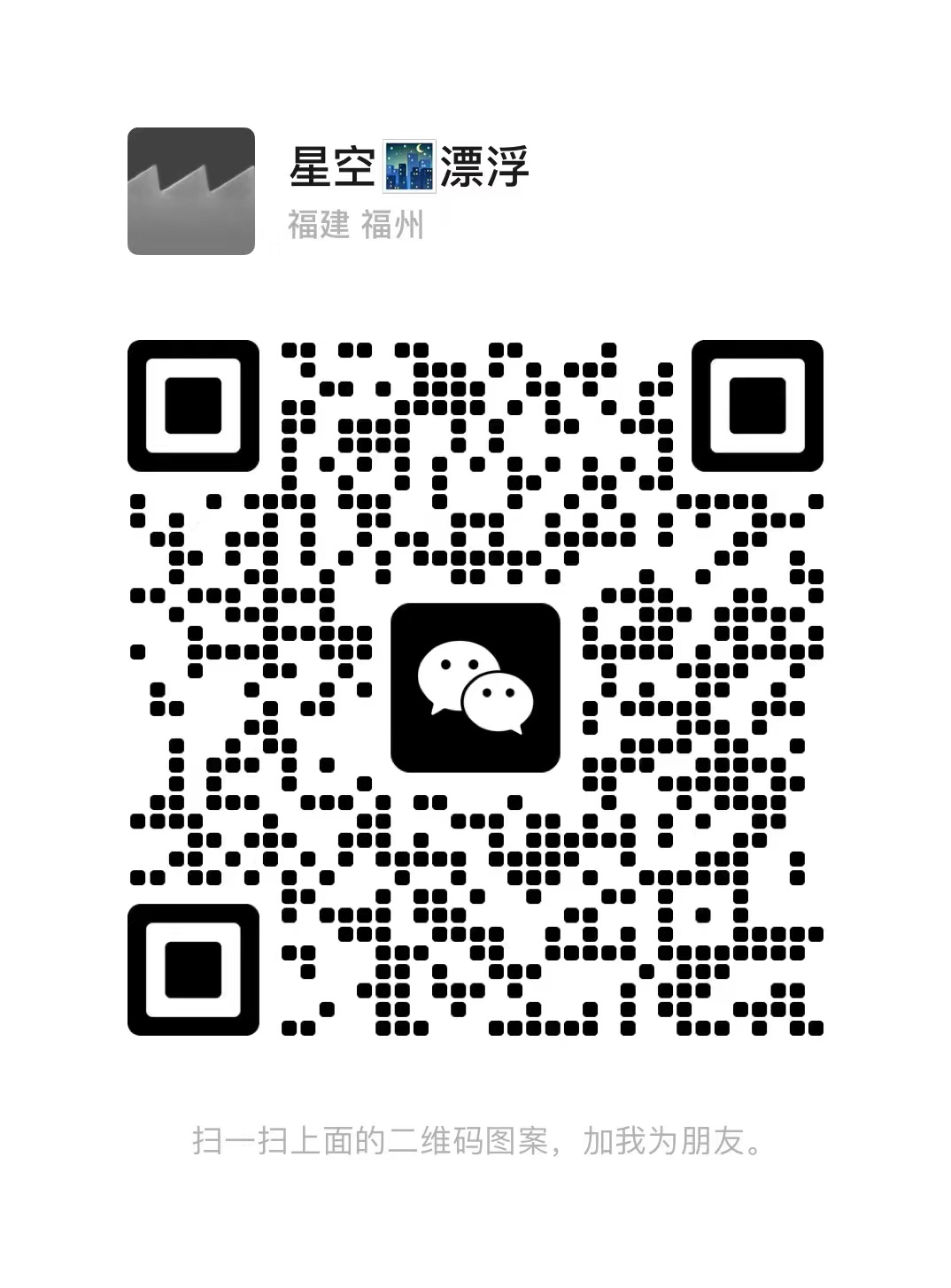
1. 引言
由于其优异的光学、化学和热性能,无机玻璃被广泛应用于工业、国防、航天和高端消费应用[1,2]。传统的研磨和抛光方法是制造球面、非球面和平面的标准,但速度慢且无法制造自由曲面 [ 3, 4]。此外,传统的研磨和抛光不适合制造玻璃微光学器件。精密冲压成型是制造自由曲面光学元件的有效方法,但由于制备高精度模具的时间和成本,它不适合快速成型。具有微观结构的光学元件,例如衍射光学元件和光栅,通常通过微光刻、蚀刻和成型形成。尽管现代制造工艺已经实现了高水平的效率和可重复性,但仍需要新的策略来制造复杂形状的玻璃光学器件,尤其是微尺寸的玻璃光学器件[5]。
三维 (3D) 打印之所以有吸引力,是因为它可以通过增材制造工艺构建复杂形状的灵活性。有许多报道使用聚合物材料通过增材制造打印具有良好性能的有机光学器件 [ 3–9]。然而,由聚合物基组件打印的有机光学器件由于热稳定性差、短波长透射率低和折射率低,在实际应用中受到限制。由于对表面形状、表面粗糙度和光学性能的均匀性有严格的要求,以及可打印光学材料的选择有限,无机光学器件的 3D 打印已经滞后。使用激光烧结、熔丝沉积、直接油墨书写 (DIW)、立体光刻 (STL)、投影微立体光刻 (PμSL) 或双光子立体光刻 (TPSL) 直接打印透明无机玻璃光学器件通常没有达到光学应用所需的质量 [ 10–14]。这些方法受到有机成分烧坏和高温烧结的收缩、缺陷(气泡、隐藏层等)和材料范围有限的限制。无机玻璃纤维的熔融玻璃丝沉积由于灯丝的尺寸而具有较低的打印分辨率[10,11]。纳米复合材料的DIW收缩率大,因为油墨溶剂蒸发并发生悬浮二氧化硅颗粒的烧结[12,15,16]。使用悬浮在可固化液态有机树脂中的无机颗粒的STL、PμSL和TPSL方法受到不可接受的高粘度、更高的颗粒负载和由于有机物的烧毁和剩余颗粒熔化到玻璃中的收缩而受到阻碍[ 13, 17]。同时,纳米复合材料中可能存在纳米颗粒团簇,这会对表面形貌和粗糙度造成负面影响。当有机树脂被有机硅类似物取代时,有机硅类似物在热解过程中转化为二氧化硅时,观察到了一些改善,但高收缩仍然是不可避免的[ 14]。一些硅氧烷基聚合物已被用于制造聚合物衍生的陶瓷,但有机基团的高比例使其不适合制造低收缩率的透明玻璃[ 18]。考虑到收缩是成功3D打印无机玻璃光学器件的核心障碍,用低粘度、液体、无机树脂代替有机溶剂将允许高分辨率STL、PμSL和TPSL打印,收缩率最小[11,12]。
在这里,我们报道了一种使用双光子聚合 (TPP) 工艺 [图 1(a)] 和基于预缩合二氧化硅的光敏液态二氧化硅树脂 (LSR) 的 3D 打印方法,该方法具有最小的收缩率 [图 1(b)] [ 19]。TPP能够实现小体积固化,并已被广泛研究用于基于液态有机树脂的光学元件的高分辨率打印[3,9,20]。LSR是一种低聚物,由四甲氧基硅烷和少量甲基丙烯酰氧基改性的三甲氧基硅烷与亚化学计量量的水进行酸催化水解和缩合而得。由于我们使用分子水平树脂,因此不存在颗粒簇的问题。因此,所提出的LSR有可能获得具有更光滑表面的玻璃光学器件。此外,由于热处理前的无机物含量较高,所提出的LSR具有较低的收缩率。在600°C下热解,然后在1000°C下烧结,可以消除任何残留的有机物,并将固化的树脂转化为二氧化硅。与先前报道的收缩率(通常为30%至60%以上)相比,LSR在热解时仅显示出17%的收缩率,在烧结时仅显示出4%的额外收缩率[13,14]。打印是通过在带有飞秒 780 nm 激光的石英载玻片上直接写入 LSR 进行的。我们证明了玻璃微透镜和光栅可以高分辨率打印。最终玻璃光学器件的表面可以精确控制,峰谷 <100nm<100nm 和表面粗糙度低于 6 nm。
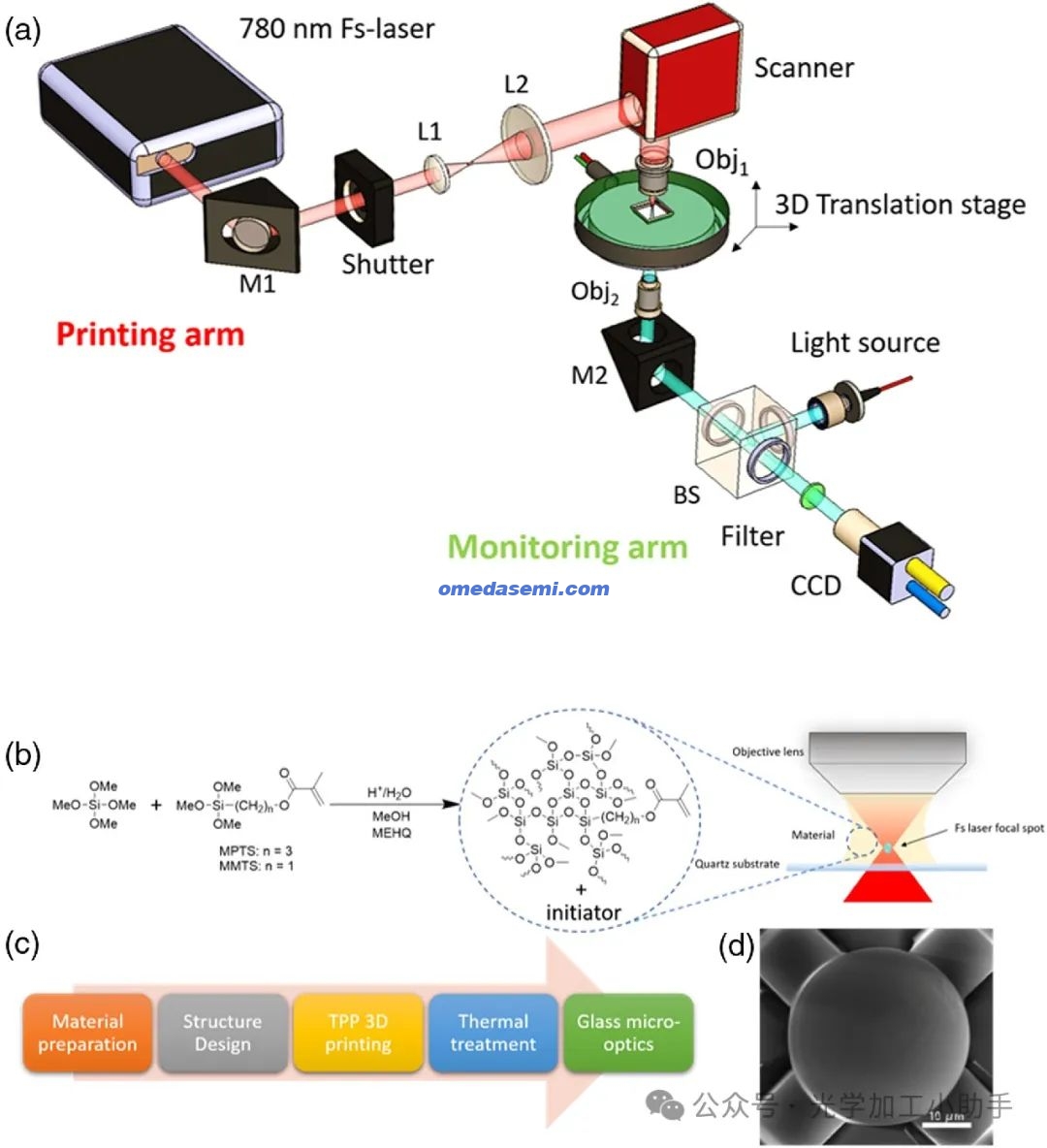
图1.印刷系统及印刷工艺。(a) 3D打印系统示意图。M1 和 M2 是折叠镜; L1L1 并且是 L2L2 扩束器的透镜; Obj1Obj1 和分别是用于固化材料和 Obj2Obj2 监测印刷过程的显微镜物镜;BS是分束器;(b)液态硅橡胶的合成;(c)玻璃微光学器件的制造工艺;(d) 支撑结构上的3D打印玻璃微透镜。
2. 无溶剂LSR、热解、烧结和收缩的单体选择
在SLA或DIW期间必须应用热固化或光化学固化的液态树脂,这使得无机玻璃的印刷更加困难,因为大多数无机化合物往往会形成固体。有机液体树脂是低分子量低聚物,具有悬垂单体取代基,最常见的是与引发剂的光或热诱导自由基生成交联。这些树脂收缩率很小,因为单体之间的大部分键已经到位,只需要几个额外的键就可以将所有低聚物连接成玻璃状固体。
对于无机氧化物玻璃,树脂应具有相当一部分 M-O-M 键。线性有机硅低聚物具有二氧化硅所需的一半Si-O-Si键,但具有至少40重量%的有机基团。将密度为 0.965g/mL30.965g/mL3 2.26 g/mL 的无定形二氧化硅转化为无定形二氧化硅,在氧化和烧结后会导致 68% 的收缩率。Si-O-Si含量可以用倍半硅氧烷增加, RSiO1.5RSiO1.5 但最终的液态树脂是为制造超低密度气凝胶而开发的预缩合LSR [ 19, 21]。四甲氧基硅烷 (TMOS) 的部分缩合用 Si-O-Si 键取代了几乎所有的甲醇基团,形成支链和富含环状的 LSR,如果分子量足够低,可以保持液态。例如,在甲醇中,以1.5 eq的水和HCl为催化剂,可以用27 wt%的TMOS获得LSR。每摩尔TMOS含水量为1.6 eq,得到固体但可溶的树脂,当水量超过1.6 eq时,树脂不可逆地形成凝胶[ 22]。不幸的是,纯基于TMOS的LSR在紫外线照射下无法固化。通过在水解和缩合反应中加入少量 3-甲基丙烯酰氧基丙基三甲氧基硅烷 (MPTS) 或甲基丙烯酰氧基甲基三甲氧基硅烷 (MMTS) 来解决这个问题。将TMOS和6.5 mol% MMTS与1.45 eq水反应得到适合印刷的粘度[10131 mP-s,剪切速率为 40s−140s−1 ,[图2(a)]的LSR。反应过程中加入4-甲氧基苯酚(MEHQ),以防止MPTS或MMTS的聚合。傅里叶变换红外(FTIR)光谱和氢核磁共振( 1H1H NMR)均用于证明合成后甲基丙烯酸酯官能团的存在[图2(b)和2(c)]。通过比较甲基丙烯酸甲酯基团的甲基峰(1.96 ppm)和甲氧基峰(3.62 ppm)在核磁共振中的缩合度,验证了LSR中的 1H1H 缩合度[图2(c)]。我们的预缩合液态硅橡胶的密度接近 1.5 g/mL(例如,用 6.5 mol% MMTS 制备的液态硅橡胶的密度为 1.48 g/mL),这比硅树脂更接近无定形二氧化硅的密度。在TPP制备之前,将光引发剂(双(二乙氨基)二苯甲酮)溶解到合成的LSR中。
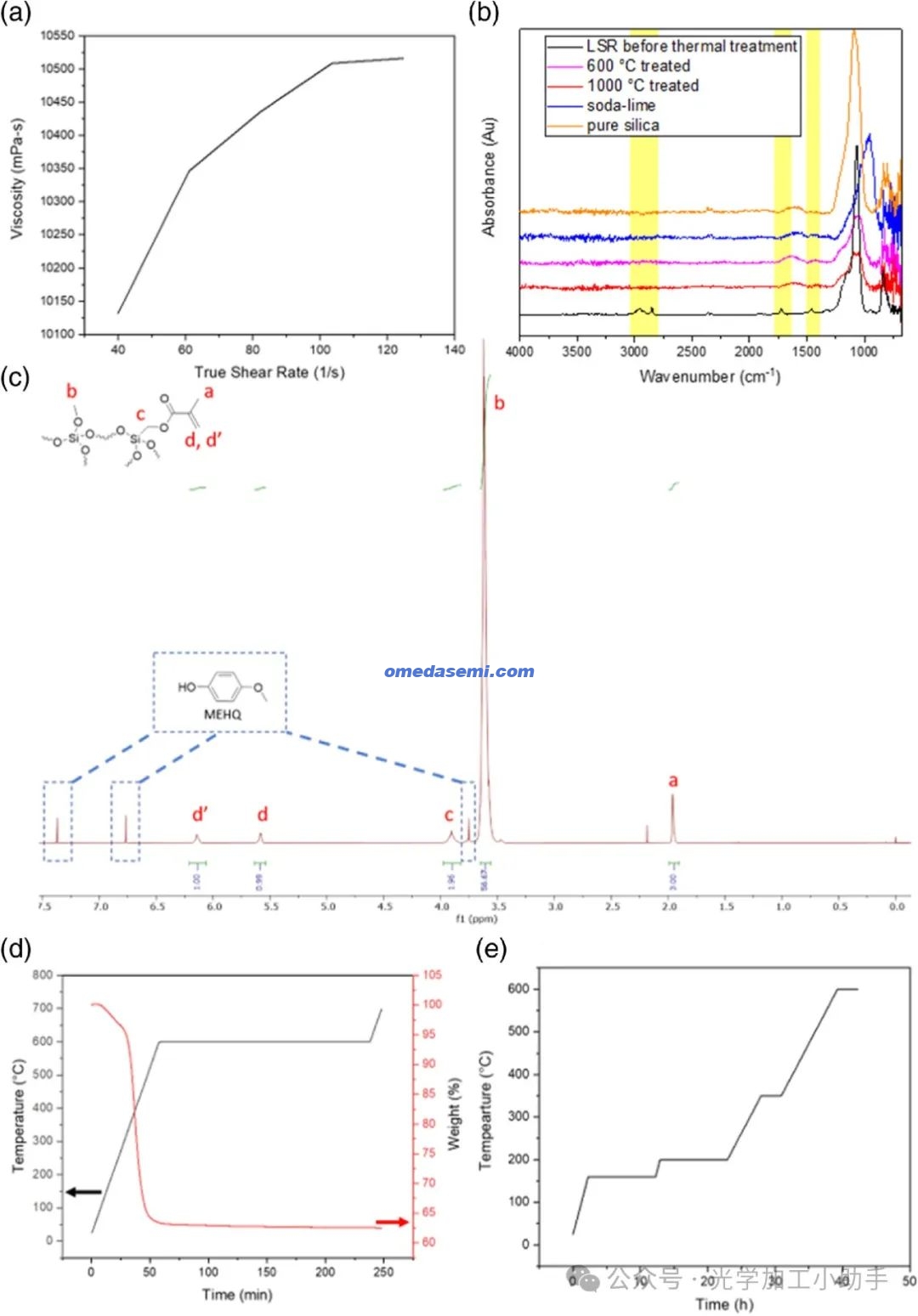
图2.TPP用LSR的表征(a) 用6.5 mol%的MMTS制备的前体的粘度。黏度随剪切速率的增加 40−140−1 而逐渐增加 120−1120−1 ,表明前驱体具有剪切增稠性能;(b) 热处理前后打印样品的傅里叶变换红外-衰减全反射光谱(FTIR-ATR);(c) 1H1H 用 1.45 eq 水和 6.5 mol% MMTS 制备的 LSR 的 NMR 谱图。峰a(1.96 ppm)和峰b(3.62 ppm)的积分表明,预缩合后,每100个甲氧基约有5.3个甲基丙烯酸甲酯基团;(d) 用 6.5 mol% MMTS 制备的固化样品的 TGA 结果。第一次质量下降始于130°C左右,表明-OMe基团开始冷凝;(e)加热处理过程。200°C前的升温斜坡控制为1°C/min,200°C后的升温斜坡控制为0.5°C/min。在160°C和200°C下保持的目的是完成-OMe基团的冷凝。
为了获得无机玻璃元件,将3D打印样品加热到600°C和1000°C,根据热重分析(TGA)结果[图2(d)和2(e)],残留的甲醇和水在100°C左右损失,随后甲醇和水从甲醇基团和硅醇缩合反应中损失,有机取代基氧化[10]。高于570°C,质量变化不大。使用FTIR通过热处理监测打印样品的化学成分变化。虽然LSR的FTIR光谱显示碳氢化合物( 2832−3050cm−12832−3050cm−1 , 1465cm−11465cm−1 )和甲基丙烯酸酯C = O()的峰 1725cm−11725cm−1 ,但热处理的打印样品在600°C和1000°C后的光谱仅显示Si-O()的峰,二氧化硅和微量吸收水的特征()(图2(b)[图2( ∼1610cm−1∼1610cm−1 b 927−1300cm−1927−1300cm−1 )]。在这一点上,该材料是无机二氧化硅,具有与无孔玻璃一致的出色透明度,但温度明显低于其他报道的3D打印方法。600°C处理 1.46±0.011.46±0.01 后的印刷玻璃折射率为632.8 nm。
使用12 mol%的MPTS,在热解的打印样品中观察到26%的收缩。当MPTS降低到6.5 mol%时,600 °C后的收缩率降低到19%。通过从MPTS中甲基丙烯酰氧基和三甲氧基硅烷基团之间的丙烯系绳切换到MMTS中较短的亚甲基,可以进一步降低收缩率。使用用6.5 mol%MMTS制备的LSR打印的玻璃环[图3(a)]在600°C下加热3小时后仅表现出17%的线性收缩[图3(b)]。再加热至1000°C3小时后,仅观察到另外4%的收缩[图3(c)]。图3(d)是处理后打印部件从200到1000的测量收缩率。将MMTS降低到3 mol%与收缩率的差异不显著 ≤1%≤1% ( )。此外,我们注意到,在3 mol%时,附着在低聚二氧化硅上的甲基丙烯酸酯浓度太低(每100个Si原子中只有3个甲基丙烯酸酯),无法有效地交联LSR。因此,本研究使用了用 6.5 mol% MMTS 制备的 LSR。
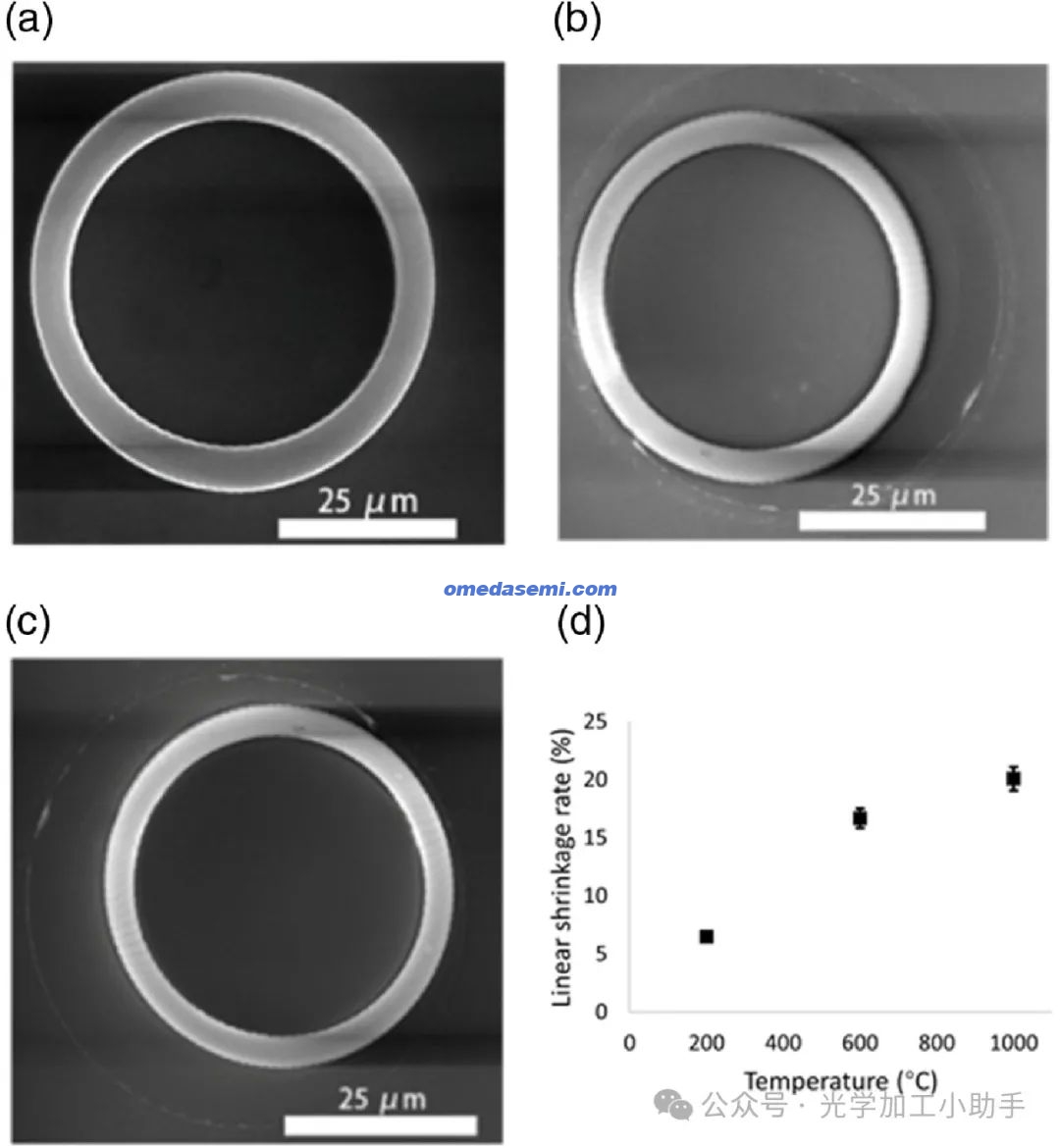
图3.热处理后的收缩率。样品用6.5 mol%MMTS制备的LSR打印。(a)–(c)是600°C和1000°C处理后打印的环的SEM图像;(d)热处理后从200°C到1000°C的收缩率。
另一个被注意到的现象是,未经热处理的印刷物体在室温下储存在空气中两个月后,发生了约8%的线性收缩,这可能是由空气中的水分引起的[ 14]。但是,与印刷状态相比,这不会影响热处理后的整体收缩率。
3.优化打印参数和打印分辨率
为了优化打印过程,在具有一系列激光脉冲能量 (0.89–1.62 nJ) 和曝光时间 (0.2–100 s) 的石英基板上打印了一组薄方块。这里的曝光时间是打印每个方块的总时间。图4(a)是印刷方阵区域的SEM图像,图4(b)是用白光干涉显微镜测量的表面轮廓。图4(c)显示了不同激光脉冲能量和曝光时间下打印方块高度的分布。很明显,随着脉冲能量的增加和/或曝光时间的增加,厚度增加,这意味着激光脉冲能量或曝光时间可以很好地控制打印系统的轴分辨率[23]。虽然较高的脉冲能量可以提高印刷速度,但它也可以从固化化学中产生足够的甲醇或水蒸气以形成气泡。另一个重要的发现是,即使施加了更长的曝光时间( >100s>100s ),层厚度也饱和到5.2μm。使用1.25 NA物镜、780 nm fs激光、0.89 nJ脉冲能量和 ∼0.2s∼0.2s 曝光时间,最小的打印点直径约为560 nm[图4(d)],这表明可以达到亚微米级的打印分辨率。
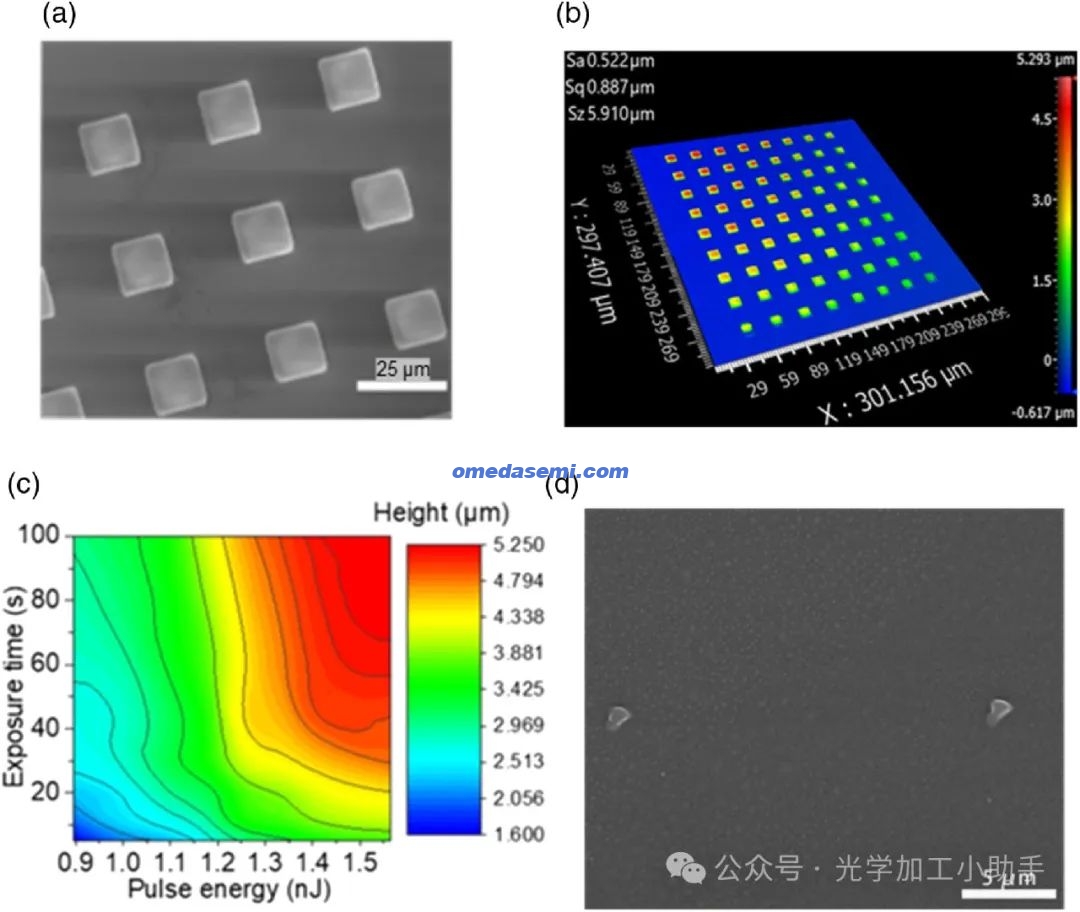
图4.用6.5 mol%MMTS制备的材料的打印性能评价。所有样品均在热处理前进行测量。(a) 3D打印正方形的SEM图像(比例尺=25 μm);(b)用不同激光脉冲能量和曝光时间打印的正方形阵列的表面轮廓;(c) 印刷方块高度的分布;(d) 最小固化点(直径560 nm)的SEM图像,用于评估打印分辨率。
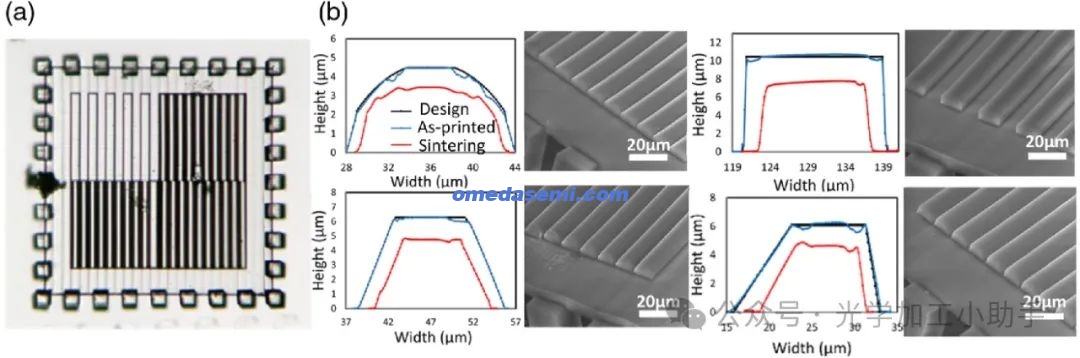
图5.不同几何形状下材料收缩率的评估。(a)在1000°C烧结后印刷光栅阵列的显微图像,以及(b)(a)中四个光栅的光栅轮廓和SEM图像。
4. 印刷玻璃微光学及其性能
根据图4中讨论的研究获得的信息,将许多不同的微光学器件直接打印在石英基板上,以证明其打印能力。然而,由于基材的热膨胀和印刷元件的收缩,以及印刷品的易碎性,在热处理过程中观察到裂纹,特别是对于长宽比大或与基材接触面积大的元件。即使没有观察到裂缝,也观察到边缘变形。为了解决这一关键问题,通过预打印支撑结构来减少印刷结构与基材之间的接触面积。
图5(a)是具有四种不同光栅轮廓的光栅阵列[半球形、矩形、等腰梯形和直角梯形,如图5(b)所示]。光栅印在由几根柱子支撑的平台上。在热处理前后,使用 Zygo Newview 8300 光学轮廓仪测量光栅的形状。与设计型材相比,光栅的打印准确无误,除了拐角处有一些小错误。在1000°C下进行热处理后,光栅各向同性收缩,测得的收缩率为 21±0.5%21±0.5% 。需要指出的是,图5(b)中测得的光栅轮廓与每个光栅之间存在一些错位,因为在热处理之前和之后进行了两次测量,因此线轮廓的方向和位置并不完全相同。
将半径为25 μm的平凸微透镜打印在顶部四个预打印柱上,如图6(a)所示。基于线性收缩率(600°C时为17%),将透镜的半径曲率打印为29.25 μm以补偿收缩率。RMS表面粗糙度为5.65 nm [图6(b)]。中心区域与理想透镜表面的表面偏差小于 ±50nm±50nm [图6(c)]。为了评估打印微透镜的成像性能, 40×40× 使用0.6 NA显微镜物镜观察打印微透镜形成的中间图像[图6(d)]。图6(e)和图6(f)是1951年美国空军在600°C和1000°C下热处理后印刷微透镜第7组中第一个元件的图像,表明印刷玻璃透镜具有巨大的成像应用潜力。由于微透镜的设计不是为了在图6(d)的实验条件下校正像差,因此图像不受衍射限制。
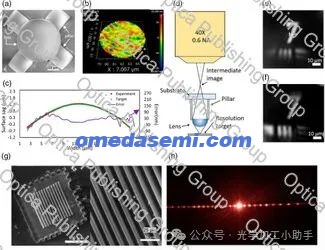
图6.印刷微透镜和光栅的性能。(a) 印在支撑柱上的微透镜(在600°C下处理);(b) 和 (c) 印刷镜片的表面轮廓以及与设计的偏差;(d) 用于评估成像性能的实验装置图;(e) 1951 年美国空军第 7 组中第一个元件的图像,用于在 600 C 下进行热处理后的印刷镜头分辨率目标;(f) 1951 年美国空军第 7 组中第一个元件的图像,用于在 1000°C 下进行热处理后的印刷镜片分辨率目标;(g) 在 600°C 下热处理后的印刷光栅的 SEM 图像和 (h) 632.8 nm 激光束的衍射图。
还制造了单个衍射光栅。图6(g)显示了具有直角三角形轮廓的光栅的SEM图像,周期为15 μm,高度为8.5 μm。图6(h)是来自光栅的准直632.8 nm激光束的衍射图。由于激光束大于光栅,因此观察到中心亮点。
5. 结论
总之,我们已经开发了用于玻璃微光学的无溶剂、甲基丙烯酰氧基改性液态硅与态硅和基于TPP的3D打印。用低至6.5 mol% MMTS对LSR进行改性,可显著降低有机成分和热解收缩。在600°C下进行热处理后,可以获得透明玻璃光学器件,收缩率低至17%,这也被证明是各向同性的。通过预打印的支撑结构,可以避免热处理过程中印刷光学元件的变形和损坏。成功制备了玻璃微透镜和光栅,并对其光学性能进行了评价。峰谷面偏差小于1/6 𝜆� ( 𝜆=632.8nm�=632.8nm ),RMS表面粗糙度小于6 nm。
我们目前的微光学打印工艺是使用用6.5 mol%MMTS制备的LSR实现的。当需要更大的透镜或多透镜系统时,可能仍需要调整MMTS的比例以达到更高的交联密度,以便在印刷期间/之后获得更好的机械性能。因此,有必要优化LSR,以便在收缩率和适印性之间取得更好的平衡。还应针对不同的LSR进一步优化打印参数,以优化分辨率和打印速度。同时,应开发具有更高折射率和更大色散的材料,以更好地控制单色和色差。