本文小编分享一篇文章,关于超低损耗SiN4薄膜的超厚800nm,超低损耗的氮化硅光波导基片,看到这篇文章被慢慢的工艺细节和创意所吸引,因此分享给大家,我把我观察到的工艺细节,写在下面更多细节,请自己去文章内探索。
氮化硅光波导的底层是制造,基片的质量影响器件的质量,1等设计+3等基片=3等产品。
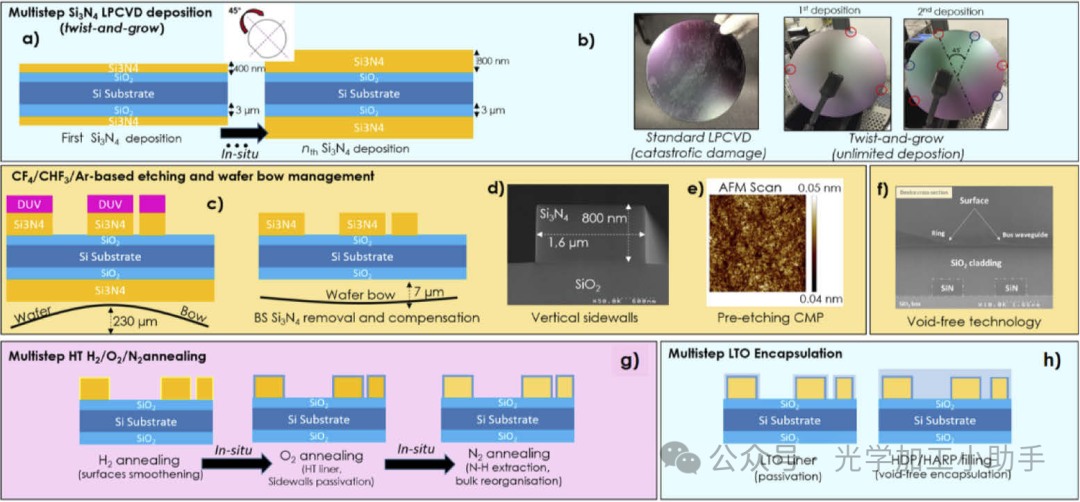
本文的工艺细节(重点看第二章)
在生长Si3N4时采用多步扭曲LPCVD生长工艺来生长800nm的厚Si3N4薄膜,而不会裂
为了控制应变并防止出现裂纹,氮化硅层通过低压化学气相沉积 (LPCVD) 分两步(或多步)沉积,每步厚度为 365 nm。在随后的沉积阶段之间,载体晶圆旋转 45°,以便沿整个膜厚度分布单轴应变。如简介中所述,在不旋转晶圆的情况下,单轴应力会累积,导致显着弯曲,阻碍对 CMOS 生产线其他工具的操作,并在氮化物薄膜中产生裂纹。每次沉积运行在 780 °C 下进行,沉积后冷却至约 630 °C,持续 20 分钟,然后以 10 °C/分钟升温至 780 °C,以完成第二次沉积。该工艺可确保防止与拉伸应变相关的裂纹,同时提供相对较厚的氮化物薄膜,在整个晶圆上表现出良好的光学性能。
在薄膜沉积完成后,采用多步退火工艺,
进一步降低薄膜的 吸收(H2退火),降低薄膜的粗糙度(O2退火),使膜层更为致密,有效的降低薄膜的损耗。
划重点:
针对氮化硅光波导--我们可以提供
1.Si+Sio2(湿法热氧)+Si3N4(PECVD/LPCVD)晶圆(LPCVD最大12寸)2.CMP+快速退火3.一站式服务
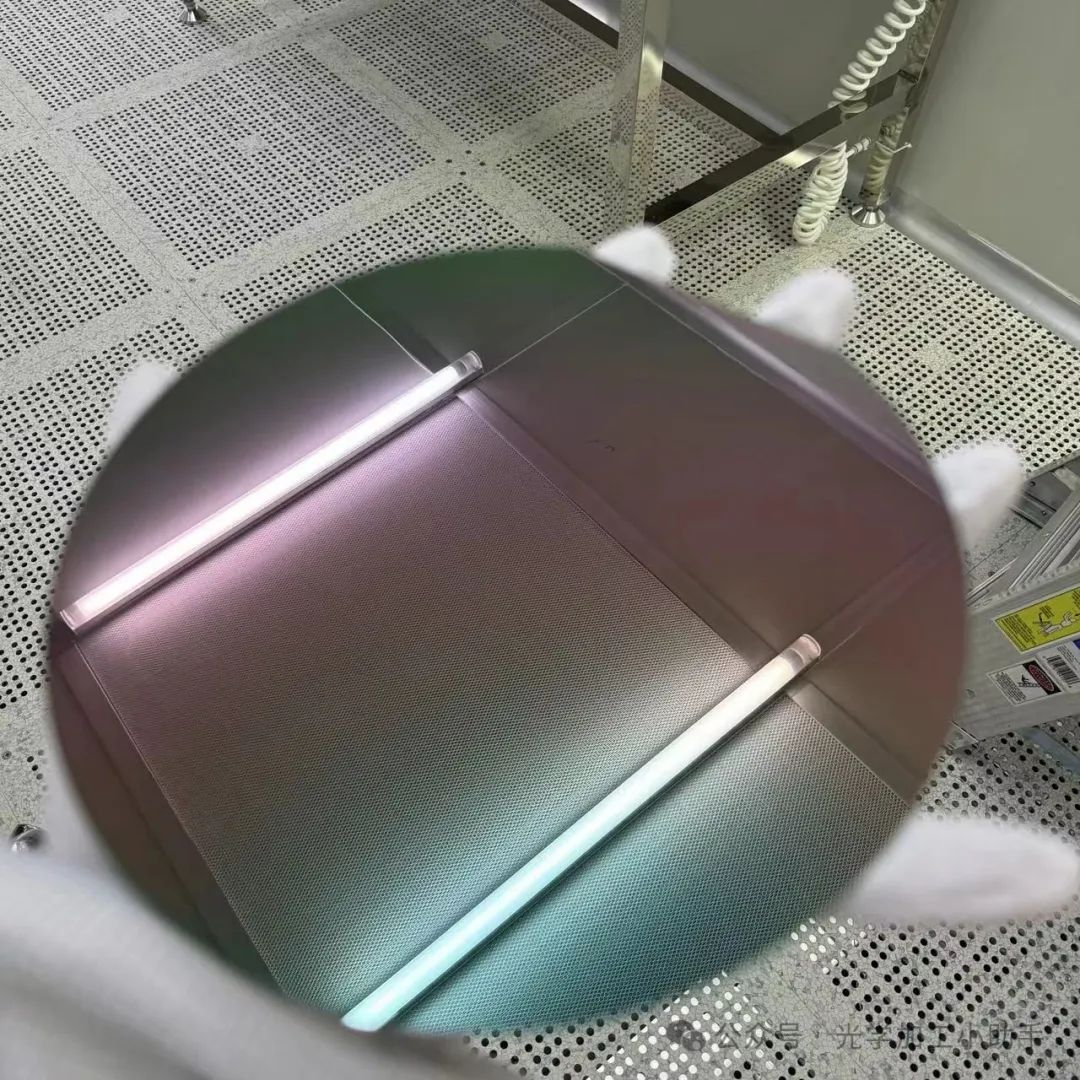
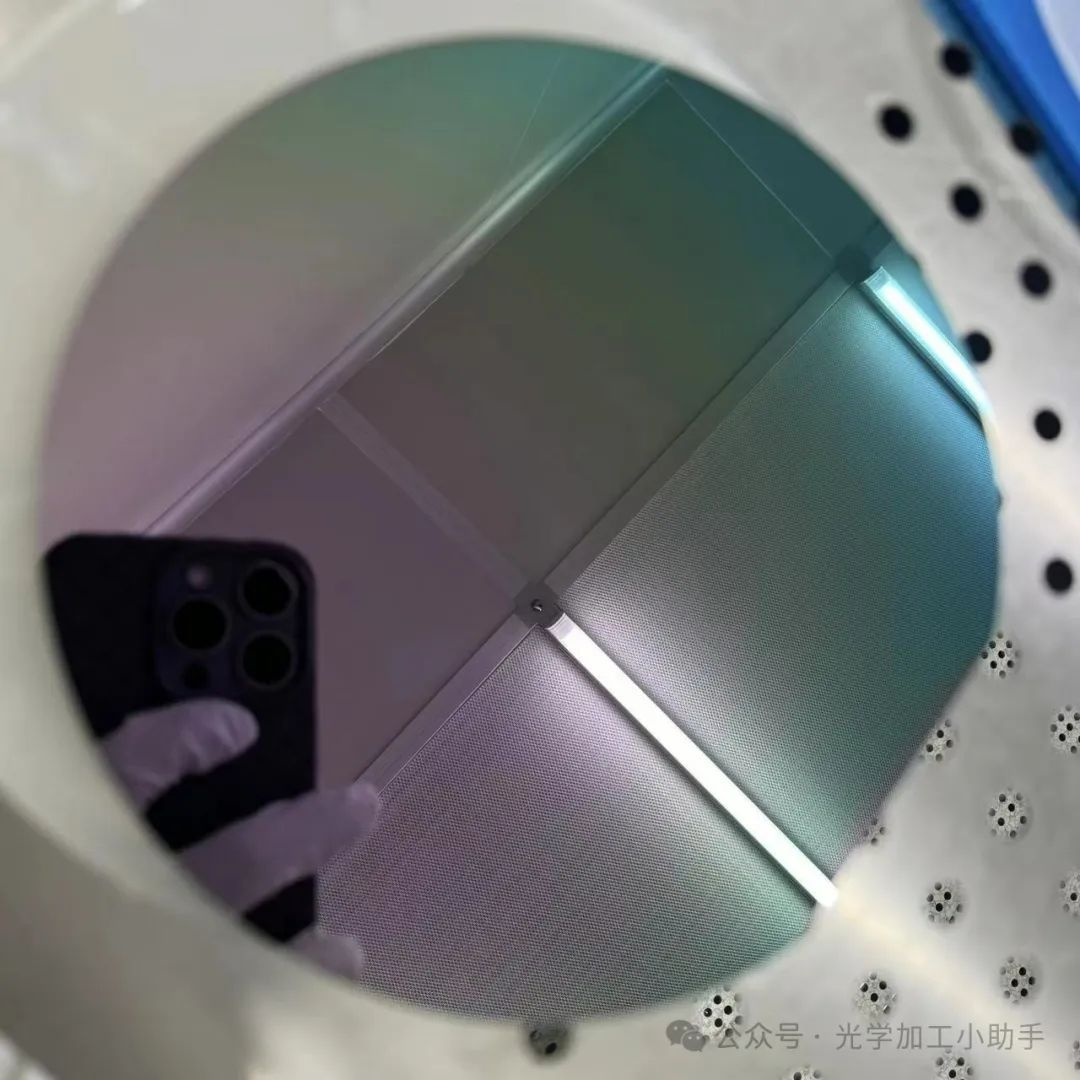
我们为客户提供晶圆(硅晶圆,玻璃晶圆,SOI晶圆,GaAs,蓝宝石,碳化硅(导电,非绝缘),Ga2O3,金刚石,GaN(外延片/衬底)),镀膜方式(PVD,cvd,Ald,PLD)和材料(Au Cu Ag Pt Al Cr Ti Ni Sio2 Tio2 Ti3O5,Ta2O5,ZrO2,TiN,ALN,ZnO,HfO2。。更多材料),键合(石英石英键合,蓝宝石蓝宝石键合)光刻,高精度掩模版,外延,掺杂,电子束直写等产品及加工服务(请找小编领取我们晶圆标品库存列表,为您的科学实验加速。
EBL代工(非晶硅,TiO2,SiO2,GaN,Ta2O5,Al,Au,GaAs(PCSEL)...更多材料体系),母版制作,铬版销售,纳米压印,DUV光刻超结构服务,
激光器芯片/探测器芯片/PIC芯片封装耦合服务"芯片类型:激光器/探测器/PIC芯片(硅光,铌酸锂,氮化硅)"封装形式:TO封装/BOX封装/蝶形封装/COB封装/PIC芯片封装"应用市场:光通信/激光雷达/量子通信/陀螺仪/生物传感/量子计算等其他,独特优势:封装技术人员具有10+年的封装经验,具有成熟的封装研发及量产经验,参与过多款铌酸锂、硅光,窄线宽激光器等产品的量产同时能够提供热仿真,光学仿真等技术支持,提供全套的封装解决方案。同时基于我们在业内10+年的行业经验,对于供应链,原材料(热沉,透镜棱镜,光纤阵列,陶瓷管壳等)的选型,采购,使用,具有极其成熟的经验,可以有效地解决封装过程中遇到的各种问题,大大降低试错成本。
请联系小编免费获取原文,也欢迎交流半导体行业,工艺,技术,市场发展!
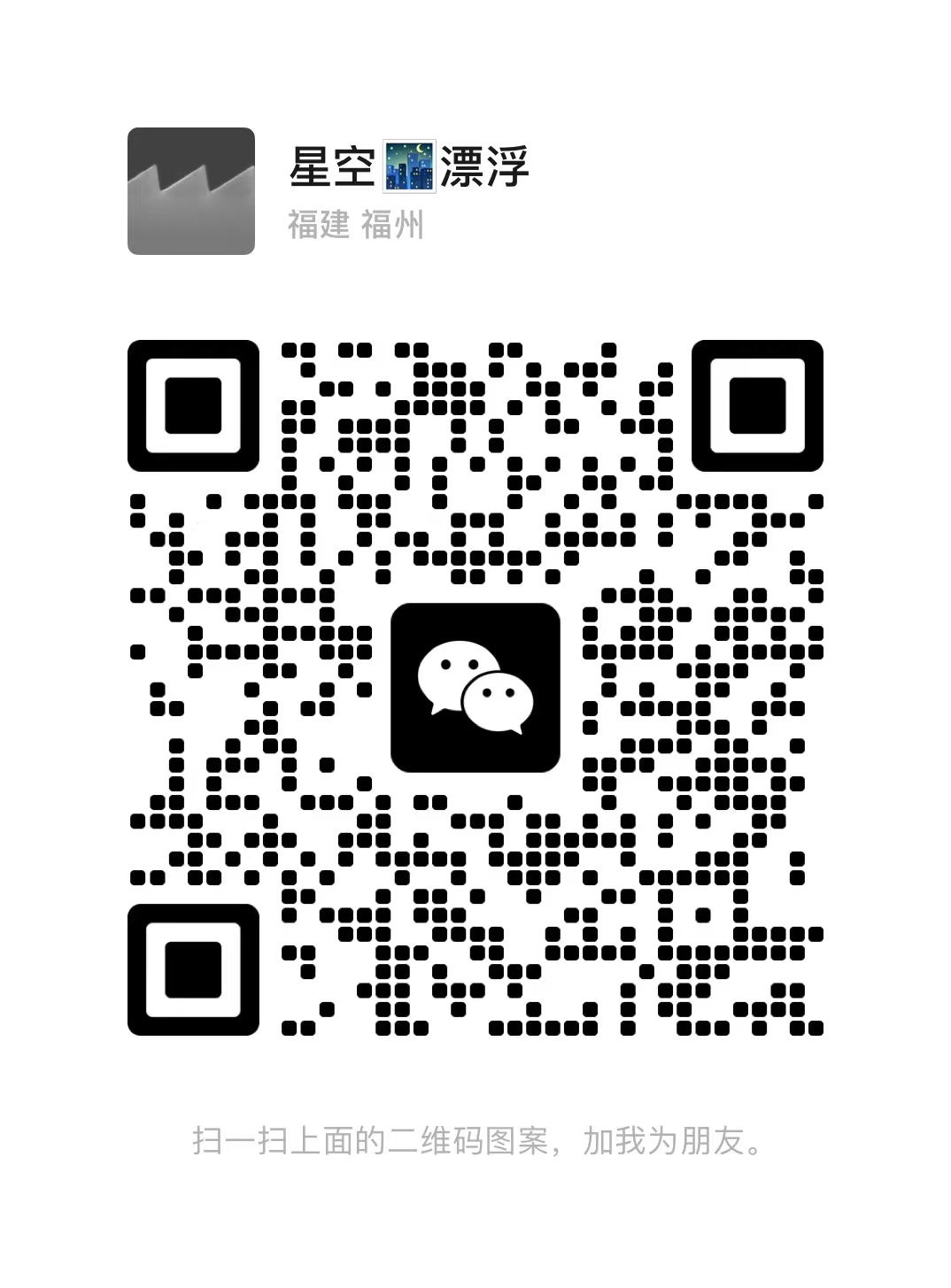
超低损耗紧密限制 Si3N4 波导和高 Q 值微谐振器
摘要:在集成波导中实现高效的非线性现象仅仅是在非线性材料中实现密集限制波导,这些波导支持具有小有效面积的导模,具有超低传播损耗和高功率损伤阈值。然而,当波导横截面尺寸不断缩小时,传播损耗和故障事件的概率往往会急剧增加。在这项工作中,我们报告了高限制、超低损耗的硅氮化物波导和谐振器的制造和测试结果,展示了在1.6微米宽×800纳米高尺寸下,S波段、C波段和L波段的平均衰减系数低至约3 dB/m,C波段的内在品质因子接近10^7。目前的技术导致了非常高的跨晶片器件性能一致性、低热敏感性和高功率损伤阈值。特别是,我们开发了一种优化的全减法工艺,引入了一种新颖的化学-物理多步退火和封装制造方法,从而得到了适用于能效非线性光子学和量子光学的高质量Si3N4基光子集成电路。
1.介绍
低传播损耗对于芯片上的光波导在多种应用中至关重要,例如非线性和量子光子学[1,2]、光陀螺仪[3]和窄线宽激光器[4]。在过去的十年中,基于Si3N4的非线性集成光学受益于制造技术和对涉及光学现象的物理理解的巨大进步[5]。由此产生的相干光频梳已实现超高数据速率光通信[6]、低噪声微波生成[7]和全光集成频率合成器[8]。
能效非线性过程,如四波混频和频率转换,需要在波长尺度上最大化光-物质相互作用。此外,相干光频梳源需要在低缺陷块材料中制造具有精确控制色散的工程波导,以实现稳定的耗散克尔孤子(DKS)形成。为了做到这一点,光波导必须具有极低的传播损耗、高功率损伤阈值和尽可能高的限制因子。
最高品质因子曾在硅楔子[9]和MgF2微型圆廊模式谐振腔[10]中实现。相比之下,硅氧化物的非线性折射率较低[11](在1.5µm波长的通信波长下为2.7×10−20m^2/W)。此外,硅的低折射率要求采用空气包层并增加了集成的复杂性。这就是为什么具有高折射率和光模式高限制的高品质因子谐振腔会带来相当大的好处。此外,当折射率高时(例如在硅中),非线性折射率n2 往往更高。然而,材料的带隙也倾向于更小,非线性损失过程(如双光子吸收(TPA))通常会发生,这对于能效非线性光学是有害的。在这方面,硅氮化物(Si3N4)是一种折衷的CMOS材料,它提供了相对较高的非线性(是硅的10倍)、低传播损耗、不存在直接与TPA相关的吸收过程,同时保持获得高限制波导的能力。
最近的研究工作基于大型、高度多模波导(横截面宽度范围从2.5µm到10µm),显示出超高的品质因子(37×10^6和67×10^6)[12–14]。然而,这样大的波导限制了获取高异常色散的能力,而高异常色散是低功率孤子基频梳生成的条件。此外,谐振腔支持的不同模式族之间的相互作用可能会阻止孤子的形成,而在耦合部分由于模间相互作用引起的系统性过量损耗可能会发生。对于在通信波长下低阈值宽带Kerr频率梳的生成,紧限制的1.5–2µm宽和0.75–0.85µm厚的异常色散波导是必不可少的,而对于高效量子光学应用则需要单模低损耗电路。使用紧限制波导的另一个优势是相关的非线性参数γ_nl的增加,它与波导有效模式面积A_eff成反比。
利用专有的Damascene回流工艺报告了一种密集限制的Si3N4波导,其衰减系数通常在5dB/m和6dB/m之间[16,18]。然而,这种方法在整个晶圆上带来了固有的严重薄膜厚度不均匀性,因为它涉及在填充预形成的回流蚀刻二氧化硅后用于硅氮化物去除的化学机械抛光(CMP)步骤。事实上,在这种Damascene方法中,CMP涉及数百纳米的厚度减小,从而引起远高于低压化学气相沉积的典型均匀性的方差(<1%的标准差方差),无论制造工具成熟度和晶圆缩放如何。最重要的是,用于平滑二氧化硅预挖槽侧壁的预形成回流技术系统地引入了波导宽度(即侧壁斜率)的强烈垂直不均匀性,数十甚至数百纳米[18]。垂直和水平不均匀性的结合强烈影响了色散工程和从总线波导到微环的耦合速率,使得实现对微腔载荷的确定性控制以及接近临界耦合条件变得更加困难。而在我们的制造技术中,执行的浅CMP最多仅影响整个薄膜厚度的5-10纳米,从而限制了整个晶圆的层厚度均匀性方差。
在这项工作中,我们报告了超低损耗、密集限制的Si3N4波导的制造和线性特性的表征,其衰减系数接近∼3dB/m,这是非线性量子光子学的关键构建模块。这些器件是通过基于化学-物理多步退火、封装和定制氟碳干法刻蚀Si3N4薄膜的全减法工艺制造的。通过这种处理,我们可轻松获得内在品质因子接近10^7的器件,其中200GHz环形谐振器是由1.6微米宽×800纳米高的高限制异常色散波导形成的。此外,这种方法使得晶圆级的高复现性和高功率损伤阈值成为可能,这要归功于沉积Si3N4薄膜的低污染水平和无孔隙的二氧化硅封装方法。该工作还将为未来的突破性研究提供指导,特别是通过分析散射相关的损耗以及残留金属污染引起的体态和表面态相关的吸收机制。
这篇研究文章的组织如下。第二部分描述了制造过程,特别是多步化学-物理退火、氟碳等离子体刻蚀和Si3N4波导的适当多层封装等创新元素。在第三部分,我们通过测量超高Q值的Si3N4微环谐振器的光谱特性来报告这种平台的广泛线性光学特性。在一系列名义上相同的微环上进行的测量为跨晶片统计提供了有价值的信息,特别是对200毫米晶圆上总和内在谐振器损耗以及关键耦合条件偏差的了解。第四部分定量评估了波导连续波(CW)功率损伤阈值,同时展示了微腔的热敏感性以及对制造结构的定量污染分析,这对于理解残余背景损耗机制及其起源至关重要。
2.超低损耗Si3N4基光子集成电路的制造
2.1. 薄膜沉积
与最近的文献相比,用于密集限制的1.5微米宽Si3N4波导的最低衰减系数报告为5.5–6.5 dB/m[18]。与光子学Damascene加工相比,在我们的情况下,Si3N4薄膜是使用已经发表在[19,20]中的技术沉积的。我们后来将此方法称为扭曲生长过程,通过应对高张力应变,提供了高厚度(>1µm)薄膜沉积能力,否则会导致这些薄膜开裂。当需要沉积较厚薄膜用于III-V/SiN激光器集成、集成量子光子学和光频梳等多种应用时,这种特性尤其引人关注。这种特性为我们的平台在应用于不同的Si3N4基光子集成电路流程设计工具包(PDK)时提供了出色的灵活性。下面,我们解释了我们如何优化这些薄膜的加工,以充分利用这个平台,并且特别达到了非常高的品质因子微环,比我们以前的工作高100倍[19,20]
2.2. 图案化和晶片弯曲管理
制造过程始于对直径为200毫米的硅基底进行3微米厚度的热氧化处理。然后,采用低压化学气相沉积(LPCVD)沉积一层厚度为800纳米的硅氮化物层(Si3N4),该沉积方法是作者在[19,20]中发表的,通过量身定制的沉积方法,最小化了氢含量并防止了沉积Si3N4由于其固有的高拉伸应变而开裂,如图1(a)和1(b)所示。
这种扭曲生长LPCVD技术具有沉积相对厚、纯净和化学计量比的Si3N4的优势,与标准PECVD技术不同,后者由于C波段的N-H键谐波吸收导致固有的体吸收,尽管具有减少薄膜应变的优点。
关于Si3N4的图案化,首先使用820纳米厚的光刻胶掩膜进行248纳米深紫外光刻,其前面有一层厚度为49纳米的底部防反射涂层(BARC),如图1(c)所示。该BARC层利用破坏性干涉以防止光刻步骤中由于背反射光而导致的额外粗糙度。在Si3N4刻蚀之前,光刻胶图案经HBr等离子体固化,以增加其对刻蚀等离子体的抵抗力,从而提高刻蚀选择性。首先使用Ar/Cl2/O2等离子体过程开放BARC层,然后在感应耦合等离子体(ICP)反应器中使用CF4/CHF3/Ar等离子体刻蚀Si3N4。Si3N4与固化光刻胶之间的刻蚀选择性为1.2:1。通过调整刻蚀配方参数,特别是反应气体流量和夹持偏置功率,我们能够确保较低的刻蚀速率(∼4nm/s),导致足够的选择性对Si3N4进行刻蚀,使得波导侧壁垂直(<1°侧壁斜率)并且具有准确的尺寸控制。刻蚀后,在Si3N4侧壁上存在的光刻胶掩膜和氟碳聚合物通过连接到ICP反应器的磁增强反应离子刻蚀(MERIE)反应器中的氧等离子体过程进行去除。等离子体图案化后,Si3N4表面通过基于H2SO4的湿法溶液进行清洗。图1(d)突出显示了本研究中开发的等离子体图案化过程的良好质量,产生了波导形状良好的各向异性剖面,无残留物。
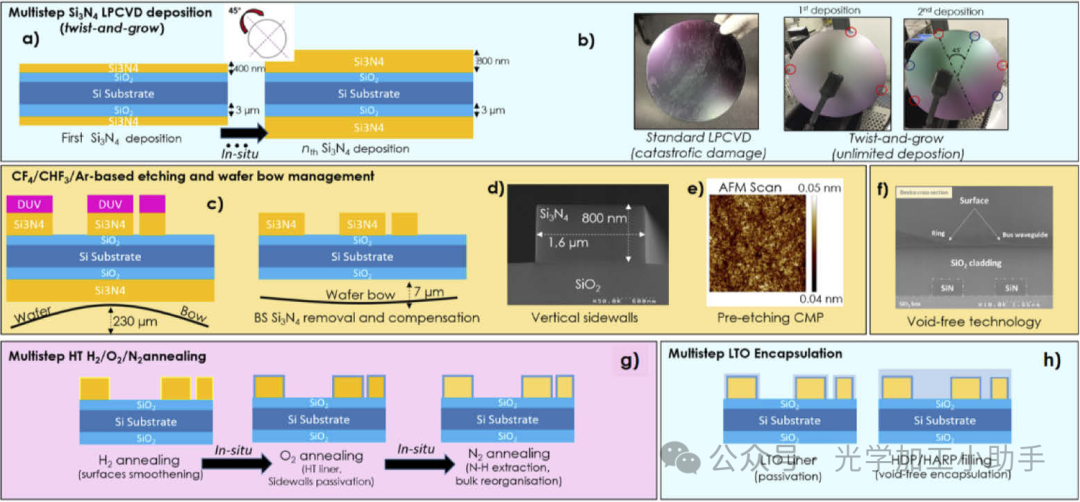
图1. 超低损耗密集限制Si3N4波导的扭曲生长和多步化学-物理退火过程示意图。a) 200毫米硅晶片进行3微米厚度湿氧化处理,然后进行扭曲生长沉积Si3N4薄膜,直到达到所需的膜厚(800纳米)。
b) 使用此方法的Si3N4薄膜图像对比。
c) 基于氟碳的干法刻蚀和晶片弯曲补偿以及
d) 通过CMP在非图案化薄膜上将顶部波导的粗糙度降低到亚英寸水平。
e) 使用CMP和基于氟碳的等离子体刻蚀工艺制备的1.6微米宽、800纳米厚的Si3N4波导示例,侧壁斜率角度小于2°。
f) 封装总线波导和微腔的SEM横截面图。
g) 多步H2/O2/N2原位退火图案化核心Si3N4波导。
h) 在高密度等离子体硅层封装之前通过低温二氧化硅衬垫进行多步封装。
值得一提的是,在我们之前的工作中,用于图案化Si3N4波导的CF4/CH2F2/O2等离子体过程系统地导致了硅氮化物侧壁和关键高宽比区域(如总线波导与微腔之间的耦合间隙)的聚合物残留物存在。然后,聚合物残留物不可避免地会导致线边粗糙度增加,并在这些结构的关键区域引入有机污染物。一种提出的解决方案是增加氧气流量以减少聚合物残留物的厚度。然而,在这种情况下,氧气会使光刻胶变薄,导致选择性降低,进而增加侧壁粗糙度。这也会导致波导厚度受限,梯形波导剖面,从而导致外部损耗率κex/2π(即从微腔到总线波导的功率损耗)的不可预测性。CF4/CH2F2/O2等离子体显示出一些工艺限制,本研究中采用了一种不易聚合的氟碳化学物质CHF3替代CH2F2。此外,由于CHF3具有较高的C/F比,因此将其添加到CF4中,因此它可以形成聚合物以补偿CF4的高度各向同性刻蚀。此外,添加氩气可以通过强烈轰击和更高的RF增强直波导剖面。图案化后,晶片的弯曲度相当高,为230微米,需要进行补偿以使晶片能够继续制程。这种弯曲度是由于晶片背面存在拉伸的Si3N4导致的。通常情况下,对晶片弯曲度的影响在整个制程流程中至关重要,特别是在主要使用200和300毫米晶片的大通量平台上。Si3N4薄膜叠层的压缩(对湿氧化SiO2典型)和拉伸应变的累积导致硅载体基片的强烈变形。这种晶片弯曲度,可以增长到250-350微米,不仅可能导致薄膜的一些损坏,还可能在图案化后的波导上形成肉眼不可见的亚微米裂纹。如图1(c)所示,这可以通过选择性去除图案化前后晶片背面上剩余的Si3N4薄膜来管理。这确保了几乎超平坦的晶片,晶片弯曲度仅为几微米(测量弯曲度约为7微米),也为通过晶片键合实现Si3N4和Si光子学的集成提供了有趣的前景。然而,与应变PECVD膜观察到的高拉应力相比(600nm厚的SiN层为1735MPa),采用我们的沉积技术后的晶片弯曲度仍然是可控的。关注散射相关损耗,波导的衰减系数α(以dB/m表示)取决于波导的侧壁、顶部和底部粗糙度。事实上,在进行波导图案化之前,我们使用原子力显微镜(AFM)测量了沉积后膜的表面粗糙度。AFM测量显示,未经任何处理的Si3N4膜的表面粗糙度为0.4纳米。为了将这种表面粗糙度减小到亚埃的振幅,对未图案化的晶片进行了全片10纳米深的CMP处理。如图1(d)所示,通过浅CMP的单一有益作用,现在表面粗糙度从0.4纳米降低到了约0.1纳米(或1埃,这大约是AFM测量的分辨率极限)。通过倾斜的AFM和关键尺寸扫描电子显微镜(CD-SEM)形态观察,刻蚀后的Si3N4波导的左/右侧壁粗糙度平均在1.2-1.3纳米范围内。
2.3.Si3N4波导的多步化学物理退火
采用低压化学气相沉积(LPCVD)沉积的化学计量硅氮化物并不完全不含氢[20,29],即使使用旨在最小化氢含量的超低沉积速率。尽管在未经退火处理的情况下也可以获得光频率梳[29],重新强调了这种原始材料的高质量,但所得微环的品质因子仍然受到C波段的限制,仅达到数十万。为了将衰减系数降至最低可能的值,我们在这项工作中开发了一种多步化学-物理原位高温退火序列,使用H2、O2和N2进行波导图案化后进行处理。N2和O2的退火在同一管内在常压下进行,而氢的退火则在垂直外延室中在10Torr下进行。我们在下面的三段详细介绍了这种优化的退火序列的不同步骤。最近的研究表明,在特定的压力、温度和时间暴露条件下,纯氢流能够将单模硅波导的侧壁粗糙度平滑至记录低值,用于TE操作[30]。基于相同的理念,
我们首先应用了一次(即几分钟长)1100°C的氢基退火,以诱导波导的形态改变。通过形态学和光学特性测试,分析了这种处理的益处,见下一节。
作为第二个步骤,将波导暴露在全O2基1200°C的退火环境中几分钟。这一步旨在通过有效的钝化和机械稳固的波导芯封装来减少表面态,通过对硅氮化物表面进行致密、高温度的自然氧化,防止在间隙内形成散射吸收中心。最后,硅氮化物膜应该通过驱除氢的过量并断裂N-H键,以接近化学计量的Si3N4膜,进而减少C波段的材料吸收损耗。然而,在退火序列之前和之后,我们并未观察到明显的厚度变化。这一发现基于退火序列之前和之后波导的SEM横截面厚度。这样的事实是由于氢的微小尺寸,以至于尽管通过多步退火处理将氢从膜中排出,但并未观察到层厚度的变化。为了驱除残留的氢,断裂N-H键并减少其残留的数量,在未包覆的波导上施加纯氮退火(1200°C,3小时)。这提供了足够的活化能来重新组织波导的体结构,以最小化体缺陷态的存在,否则会导致有害的体吸收。
2.4. 多步NO/LTO封装
通常,设备的适当矿物无空隙封装提供了实现超低损耗光传播所需的光学特性。尽管可能看起来微不足道,对于退火过程,我们在低温氧化物沉积(LTO,400°C)中执行多步封装,首先是在原生氧化物(NO)表面上沉积四乙基正硅酸酯(TEOS)为基础的低速率衬底层。随后,如图1(h)所示,通过交替相的蚀刻和高密度等离子体增强化学气相沉积(HDP-ECVD)的适当填充,沉积了几层高密度硅。此过程使我们同时实现了a) 波导的适当原生氧化物界面,b) 保护免受HDP等离子体在波导顶部以及沿其侧壁的轰击,以及c) 在关键的高纵横比区域,特别是在总线与谐振器之间的耦合区域,实现无空隙封装。此外,无空隙封装对于保证耦合区域的减少散射至关重要,从而最小化由于模间相互作用而导致的系统过剩损耗,并增加失效事件的阈值功率。这在将III-V基反射半导体放大器(RSOAs)甚至自由运行的多模激光源与超高Q Kerr微谐振器进行芯片级和功率效率的光学频率梳源的紧凑联合方面至关重要。
3. 光学特性和统计分析
为了评估前一节中介绍的不同加工步骤对Si3N4微谐振器性能及其跨晶片分散的影响,采用TE极化表面光栅耦合器(SGCs)对谐振器进行光学特性表征,放置在300mm光纤探测站上,SGCs的输入/输出(I/O)插入损耗约为6dB。在本研究中,主要选择了TE极化,因为光栅耦合器在TE模式下运行,尤其是因为采用了半自动探测站使用光栅耦合器光纤阵列。这种方法确保了对整个200mm晶片的多个晶片的设备特性进行了广泛的统计分析。这比采用边缘耦合配置更节省时间,后者需要采用逐片方法。使用可调激光源提供稳定的1mW输入功率进行直接谐振扫描,跨S、C和L波段进行谐波扫描,波长调节步骤为0.1pm(12.5MHz),这是我们激光源的最小波长采样步骤。在耦合到芯片之前使用-20dB的光衰减器,以精确评估低下降功率水平对微环的谐振光谱特性(即,谐振线宽)进行抑制,以抑制由微谐振器的热敏感度χth引起的谐振偏移[16]。
通过拟合测量的谐振透射谱与以下双峰模型,提取固有的品质因子:

其中,κ01/2π和κ02/2π分别是谐振腔内顺时针(CW)和逆时针(CCW)模式的固有半线宽,而f1和f2是谐振腔内两种模式的共振频率。
实验装置示意图以及环形谐振器的顶视光学显微镜图像如图2(a)和2(b)所示。
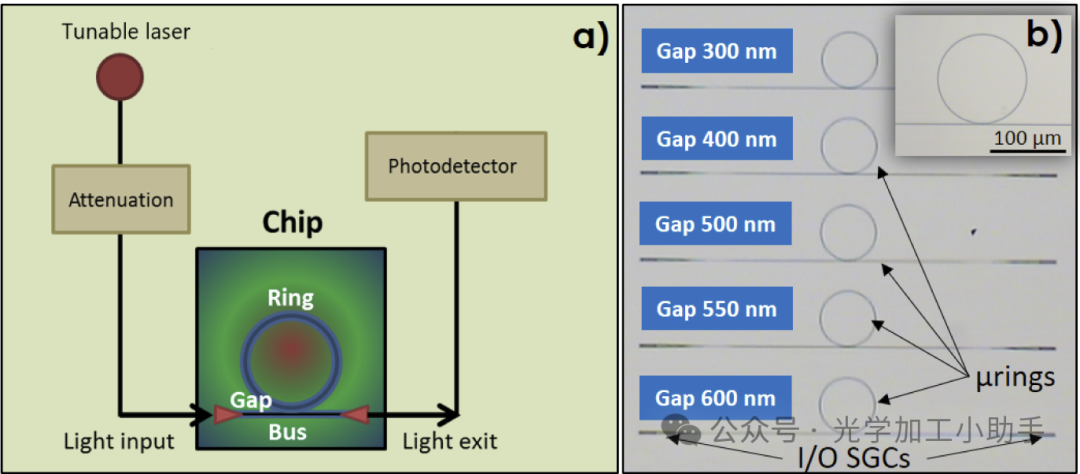
图2. (a) 用于对微腔和测试结构进行表征的光学测量装置的示意图。采用高灵敏度光电探测器进行直接激光扫描光谱学。(b) 不同总线/环间隙配置的200-GHz-FSR环谐振器的显微镜图像。输入/输出(I/O)信号通过TE极化操作的表面光栅耦合器(SGCs)收集。
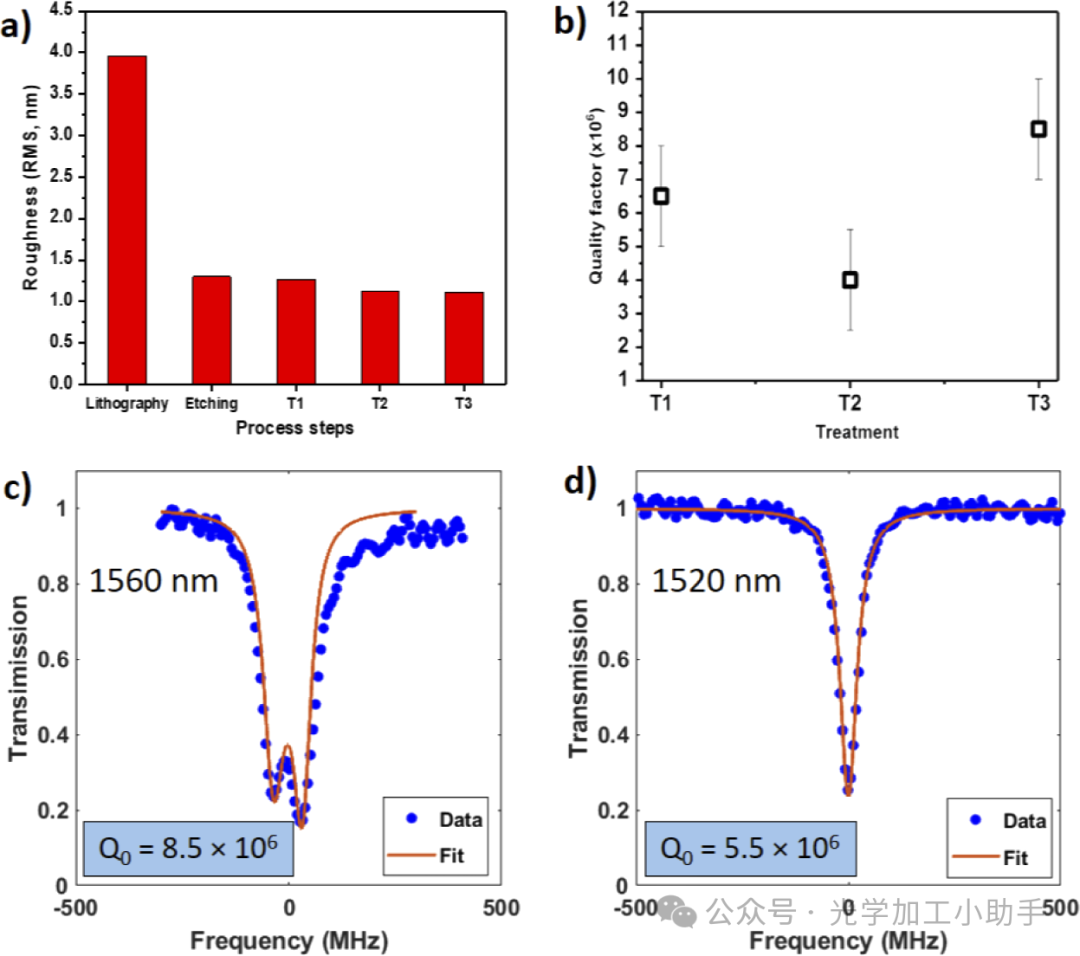
图3.(a) 制作过程中(光刻、干法蚀刻)波导侧壁粗糙度的演变,包括不同后蚀刻退火策略(T1、T2和T3)的比较。(b) 品质因子及其对应的标准偏差随退火处理的变化。数据显示了1550-1570nm波长范围内的平均Q0值及其统计分布,中心波长为1560nm,跨越20个不同晶圆。(c) λ=1560nm处的共振双峰,提取出的内在线宽κ0/2π为23MHz,对应于内在Q0约为8.5×106,并拟合出的分裂率Ω/2π=62MHz(晶片T3)。(d) λ=1520nm处的共振,提取出的内在线宽κ0/2π为36MHz,对应于内在Q0约为5.3×106。
为了评估在经历H2退火处理的wafer T3上的谐振器波导的衰减系数,通过内在品质因子,我们开始分析在欠耦合状态下运行的谐振器,以最小化由耦合非理想性引起的过量损耗的贡献,从而使内部损耗率κ0/2π主导总损耗率。具体而言,通过测量传输谱中的谐振线宽来进行分析。这提供了谐振器的总损耗率κ/2π=(κ0+κex)/2π,即总耦合损耗率κex/2π从总线到微环的和以及内在微腔损耗率κ0/2π。只有在掩模集上最大可用间隙的情况下(即间隙宽度为600纳米),才发现了工作在欠耦合状态的谐振器。如图3(c)和3(d)所示,来自微腔中的相干背向散射的谐振双峰可以在整个晶片上很容易地观察到,对于这种耦合速率。内在品质因子是通过谱分辨的谐振双峰(其分裂率高于设备分辨率)来推导的,以确保我们不是从分裂率低于我们设备分辨率的双峰中提取品质因子,然后将谐振视为简单的洛伦兹线。如图3(c)所示,通过使用谐振双峰线形拟合模型,可以从测量中提取出23MHz的内在损耗率κ0/2π,对应于在1560nm波长(C波段)处的内在品质因子Q0∼8.5×106,并且拟合的分裂率Ω/2π=60MHz。
通过在1520nm(S波段)处重复相同的测量,如图3(d)所示,我们提取出了一个内在线宽为36MHz的值,对应于Q0∼5.3×106。这表明Si3N4材料中残留的N-H泛音吸收几乎完全通过原位退火步骤消除了。然而,当比较图3(c)和3(d)时,这种蓝移波长处的损耗增加来自于膜中仍然存在的N-H键吸收的高频吸收。事实上,在1520nm处,品质因子仍然保持较高,表明高温处理以及H2/O2/N2环境是有效的,可以消除大部分N-H键。然而,由于品质因子向蓝移,N-H键残留量存在,尽管数量减少了。图3(b)显示了从这些测量中提取的平均内在品质因子及其对应的标准偏差,比较了三种不同退火处理T1、T2和T3的使用情况。特别是,这些值报告了在1560nm波长中心的20nm波长间隔内的平均值和Q0值的统计离散度,并对每个晶片上的20个不同区域进行了采样。值得注意的是,从这些结果我们可以推断出,在wafer T3上获得了最佳的衰减系数α,这经历了快速H2退火处理。正如已经提到的,T3处理导致了测得的内在Q0因子相对于其他两种退火工艺的增加。这可以解释为这种处理允许进一步平滑(尽管微小)波导,如图3(a)所报告的,因此,散射相关损耗大幅减少。
从分析微腔谐振器谐振特性可以推断出波导的衰减系数。内在的Q0与衰减系数有关,其关系为α=κ0neff/c,其中κ0是内在损耗率,neff是TE偏振光基本模的群折射率(在我们的情况下为1.79)。因此,在我们的情况下,这对应于在1560nm波长处至少α∼3.5dB/m的波导衰减系数,不确定性为0.5dB/m,这是报告的类似截面尺寸的高阶氮化硅波导在此波长(1560nm)方面的最低传输损耗[18]。需要注意的是,这样估计的传播损耗构成了对真实衰减系数的保守估计,因为我们仍然在欠耦合状态的边缘操作,使用掩模集上可用的最大间隙尺寸。第二个传播损耗过高的来源来自于我们从微环中提取损耗,而不是直接波导截面的截面测量。在环中,光模式与侧壁粗糙度的相互作用更多,尤其是在TE偏振下操作时。
总之,通过H2/O2/N2多步退火和顺序封装处理获得的超低光损耗来自于几种内在材料和器件制模改进的结合。具体来说,首先是a)结构性的整体重组和b)通过N2退火去氢化Si3N4薄膜,然后是c)有效的表面状态钝化和d)波导核心保护,抵御离子轰击和机械冲击,通过控制O2退火,其天然氧化物(NO)和LTO衬底,最后是e)通过快闪H2退火使侧壁光滑度减小,减少散射损耗。
3.2. 关键耦合谐振器的统计分析
对器件进行全面的光学表征是研究不同后退火处理对整体器件性能影响的必要步骤。这包括谐振器的内在带内和带外传输的消光比、内在线宽κ0/2π以及初始制造时的谐振绝对波长在1561nm处的偏差。如图4(a)所示,对上述五种母线至微腔间隙配置进行了统计研究,以区分过耦合(区域I)、近临界耦合(区域II)和欠耦合(区域III)的器件。这些器件分布在上述三个区域是基于微腔谐振器的消光比。区域III中的欠耦合器件具有600nm的母线至微腔耦合间隙,这是我们掩模集中可用的最大值。另一方面,使用550nm耦合间隙的器件,在1561nm波长处统计上展现出最高的消光比,因此在临界耦合条件附近运行。值得注意的是,该分析是在经过快闪H2退火并且具有最低衰减系数和波导侧壁粗糙度值的类型-3(T3)晶片上进行的。
为了估计在完全减法制造过程中光损耗和品质因子的高再现性,对550nm宽耦合间隙的20块芯片(来自同一片200mm晶圆的一部分)进行了统计研究,以便在临界耦合条件下运行。这些值已经在以1560nm为中心的20nm波长间隔内的多个谐振峰上进行了平均,并在20个不同晶圆上进行了抽样。
最后,关于微腔谐振器的消光比,当环和母线波导之间的间隙为550nm时,95%的测试器件中获得了超过10dB的消光比,如图4(e)所示。此外,消光比的平均计算值为13.1dB,标准偏差仅为2.1dB,跨越了200mm晶圆。这样的结果反映了Si3N4薄膜厚度沉积的高均匀性,同时支持了整个技术在晶圆上的高再现性。
如图4(c)所示,在1560nm附近的内在线宽κ0/2π的平均值为41.2MHz,标准偏差仅为6.8MHz。同样,在这种情况下,这些值已经在以1560nm波长为中心的20nm波长间隔内的多个谐振峰上进行了平均。此外,正如图4(b)所报告的,200GHzFSR谐振器的内在线宽随波长的演变显示出在S、C和L波段(1500nm至1600nm)中具有良好的均匀性。在图4(d)中,我们还绘制了同一波长范围内单个谐振峰与平均内在线宽的变化。
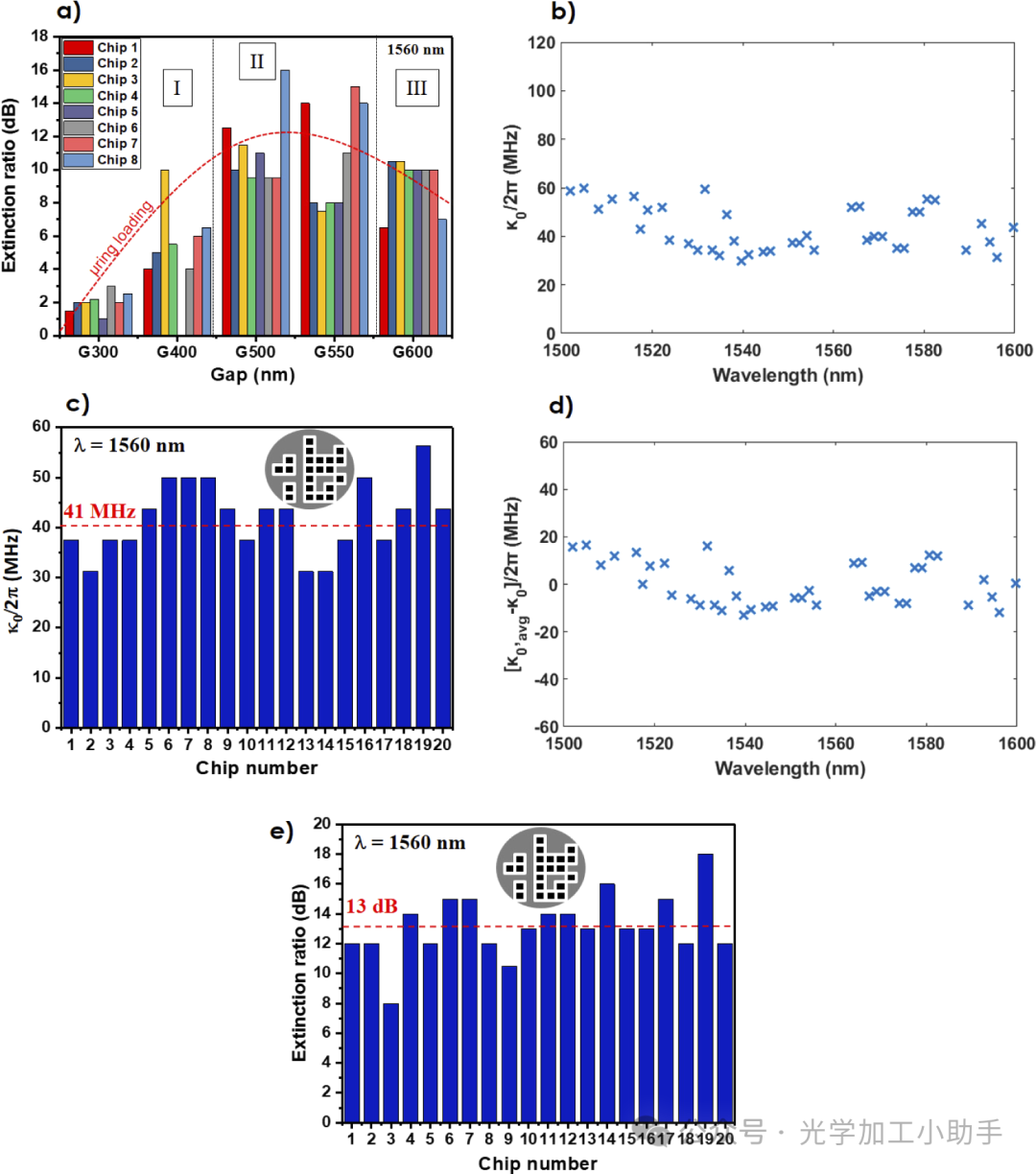
图4.(a)超耦合(区域I)、接近临界耦合(区域II)和欠耦合(区域III)200GHz谐振器器件的消光比跨晶片对间隙分布。(b, d)自身固有线宽(MHz)及其相对于1500-1600nm波长(S、C和L波段)平均线宽的绝对变化。(c)固有线宽(MHz)和(e)临界耦合器件的消光比(耦合间隙=550nm),在以1560nm为中心的20nm波长间隔内测量,并在20个不同晶片上采样(各自的平均值由红色虚线表示)。图(c, e)的插图中显示了200mm T3晶圆上20个晶片的相对位置。
4. 堆积吸收限制、热敏感性和器件可靠性
作为评估微谐振器残余损耗来源的最后一步,超越侧壁粗糙引起的散射,我们通过全反射X射线荧光(TXRF)测量研究了Si3N4膜中金属污染物的性质和相对浓度。事实上,这些金属元素的存在可能作为中间散射中心,在波导的体积和表面都负责光子吸收。值得注意的是,在125块晶片上进行了金属杂质浓度的统计分散,红点表示“异常值”测量点。红线(标有UCL)显示了在生产兼容的CMOS试生产线上允许的“上限污染”,硬性限制为每平方厘米的5×1010个原子和5×1011个原子。图5(a)的结果显示,存在非常低水平的污染物,特别是Ca和K(1011个原子/平方厘米),而来自Fe、Co、Cr、Cu的污染物水平介于1010-1011个原子/平方厘米之间。Ca和K的存在与去离子水用于晶圆清洗的残余污染有关,而Cu、Al、Ni、Ti则来自基于CMOS的接触金属技术。Fe、Al、Zn污染的来源可能与InP和GaAs外延和衬底掺杂以及III-V三元和四元合金成分有关。在本文中使用的膜中检测到的污染水平比Si3N4基光子达马斯克工艺报告的值低6到7个数量级。然而,我们认为我们的污染水平符合生产兼容的CMOS线要求的标准。
图5.(a) 对本工作中描述的沉积Si3N4膜的金属污染进行TXRF分析。在125块晶圆上的金属杂质在膜中的统计分散(蓝色方框),红点表示“异常值”测量点。红线(标记为UCL)显示了在生产级CMOS试验线中允许的“上限污染”,具体金属元素的硬性限制为每平方厘米的5×1010个原子和5×1011个原子。(b)对不同下降功率(mW)提取的共振频率漂移(MHz),揭示了共振器在1560nm波长处的热敏感性χth=185MHz/mW。(c)当将+38dBm的连续波输入光功率耦合到Si3N4波导时,发生故障事件的图像。在这种功率水平的测量中只观察到一次故障事件。在任何微谐振器上在此高功率水平下的设备测试期间未观察到任何故障事件。
这显然为确定和达到Si3N4体吸收的最终限制以及进一步减小波导衰减系数提供了有趣的前景。此外,低污染水平有助于减少器件的热敏感性,这对于量子光学器件在运行时的稳定性非常重要。显然,超低损耗Si3N4集成谐振器的热敏感性χth与金属杂质的体密度有关,这些杂质作为散射中心导致非辐射复合事件,主要产生声子发射。热敏感性又与吸收损耗率及波导的非散射相关损耗的整体贡献有关。如图5(b)所示,我们从共振频率漂移(以MHz为单位)与功率下降到环上的线性相关性中提取了热敏感性χth(以mW为单位)。这揭示了在1560nm波长下临界耦合谐振器的热敏感性χth为185MHz/mW。与之前报告的数值相比[16,图3(b)],在相同的方法和数据下提取的χth时,该值约小了约30%。
也非常重要评估设备的可靠性和老化情况。在连续波注入功率高达+20dBm的情况下,对同一芯片进行了长达3个月的广泛光学测试,但在光谱(和材料)属性方面没有明显变化。设备还经历了非常高的连续波功率水平的应力测试,与毫米波导耦合的功率约为+40dBm。在这些功率水平下,微腔谐振器在整个测试期间没有观察到任何故障事件。然而,一次故障事件发生在一个毫米波导上,其结果如图5(c)所示。更确切地说,故障起始于芯片的左侧,光纤输入镜头与Si3N4波导之间进行光耦合的地方。
结论和展望
在这项工作中,我们展示了高限制超低损耗Si3N4波导和高Q微腔谐振器的制造和测试,其衰减系数低至约3-3.5 dB/m,而固有品质因子在C波段接近107。这些器件在全片尺度上表现出非常低的性能偏差和高度均匀性,具有低热敏感性和高功率连续波损坏阈值。这得益于优化的全剥离工艺的发展,引入了一种新型的化学-物理多步退火和精心设计的封装工艺。这种技术生产出高质量的Si3N4基光学电路,非常适用于能源高效的非线性光子学和集成量子光学。