本文介绍的是一种新型材料的波导平台,该平台采用了InGaP材料,这个材料被用于,开发出来了一种绝缘体上的InGaP的波导平台 。
其实从最近学术界发文章的趋势我们不难看出 ,最近比较火的几篇文章
Ti:Sapphire激光器(这个文章的作者的老师也是搞SICOI的)
碳化硅光子集成线路
当然包括以前大家常用的SOI,LNOI,LTOI
硅光铌酸锂异质键合
氮化硅铌酸锂异质键合
上述工艺平台都是基于一类工艺,键合+SMARTCUT/减薄抛光工艺,这是因为单晶材料具有极好的光学特性,通过smartcut或者煎薄抛光工艺可以获得单晶薄膜。
这套工艺平台,可以在热氧片或者其他材料上实现多材料的键合,最终可以开发多材料的波导平台,对光子集成线路的发展提供了更多的自由性。
划重点
而目前国内提供绝缘体上多材料波导平台的供应严重不足,严重限制了国内科学家在这块的探索,小编为大家提供多材料(铌酸锂,晶体,碳化硅,磷化铟,砷化镓,钽酸锂,碳化硅,氮化镓,砷化镓,氮化硅,等等等等)和多材料键合加工,离子注入,抛光煎薄的全流程 全产线,自主可控复合衬底加工,您收到我们的衬底后,可以基于自己单位的平台进行后道的刻蚀工艺的开发。
同时可以提供两类工艺
键合可以亲水键合+退火或者室温表面活化键合+改性层
薄膜层的获取可以通过smartcut离子注入(厚度控制精准,膜层有损伤)+退火cmp或者机械减薄+cmp(厚度控制不精准,但是膜层没损伤)
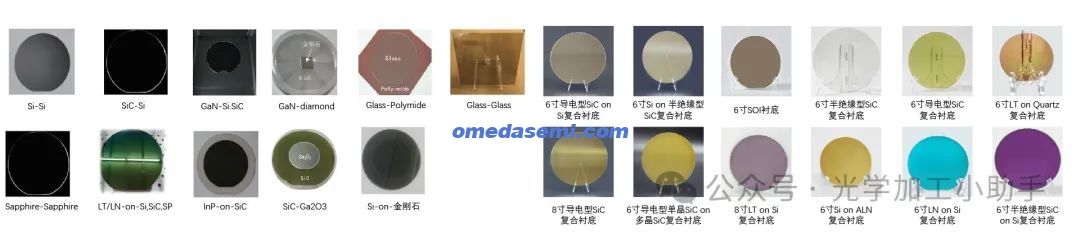
如果想要了解更多可以联系小编
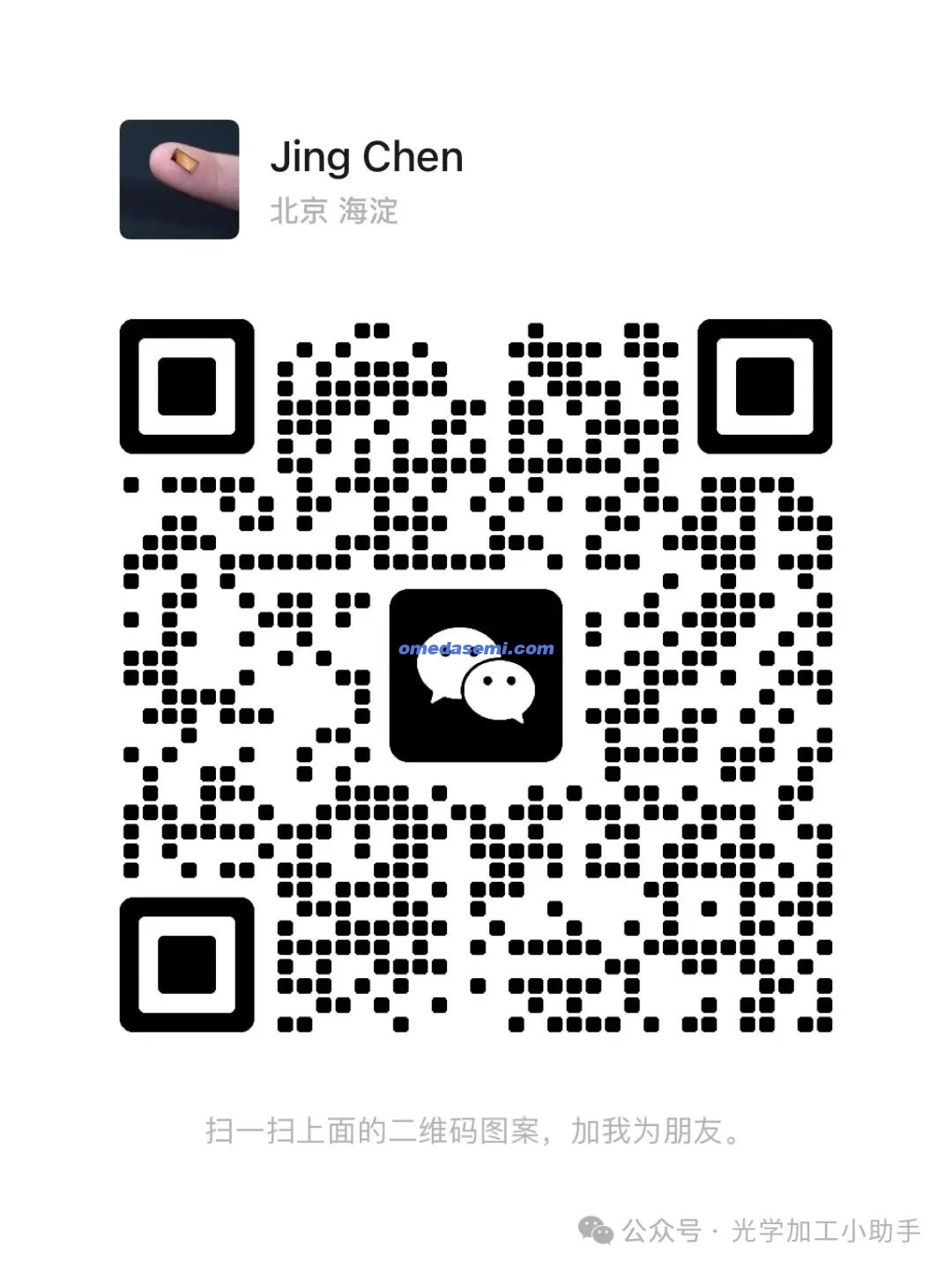
摘要
可制造和可扩展的集成非线性光子材料的开发正在推动高速通信、信号处理、传感和量子信息等不同领域的关键技术。在这里,我们展示了一个非线性平台——绝缘体上 InGaP——针对可见光至电信波长 x(2) 非线性光学过程进行了优化。在这项工作中,我们详细介绍了通过晶圆键合、光学光刻和干蚀刻技术实现的 100 毫米晶圆级绝缘体上 InGaP 制造工艺。由此产生的晶圆在每个制造周期中产生 1000 个组件,初始设计包括芯片到光纤耦合器、12.5 厘米长的嵌套螺旋波导和自由光谱范围跨越 400-900GHz 的微环谐振器阵列。我们证明了 1550nm 附近的单谐振(分裂谐振)模式的固有谐振器品质因数高达 324000(440000),这对应于 1.56dB/cm(1.22dB/cm)的传播损耗。我们分析了损耗与波导宽度和谐振器半径的关系,以确定最佳 775–1550nm 相位匹配的工作状态。通过将 InGaP 的高 x(2) 和 x(3) 光学非线性与晶圆级制造和低传播损耗相结合,这些结果为纠缠光子、多光子和压缩光的产生开辟了广阔的可能性。
能够高效、高速率、高质量地产生双光子对的芯片级非线性量子光源是光量子计算1,2、基于纠缠的量子密钥分发3,4、量子时间传输5和量子传感6的关键组成部分。由非线性光学材料组成的集成光子微环谐振器可以通过x(2)自发参量下转换(SPDC)或x(3)自发四波混频(SFWM)过程产生纠缠双光子对,7,8并且它们可以轻松地与可扩展的基于芯片的光子集成电路(PIC)集成。此类光源已在许多不同的材料平台上得到验证,所有这些平台都面临着最佳材料特性与现有制造技术限制之间的权衡,如表 I 所示。
表 I. 各种非线性平台的非线性材料特性和制造能力的比较。
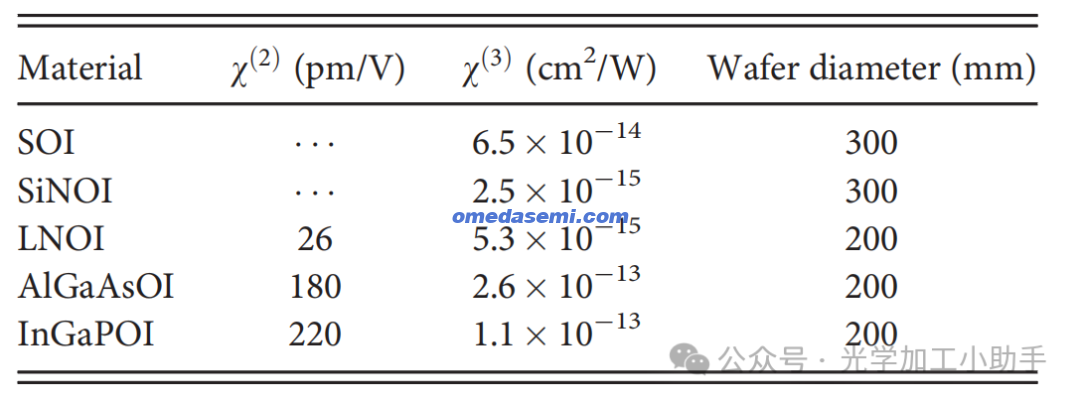
硅和氮化硅光子学已经扩展到低损耗 PIC 的大规模生产,10,11 但在光学非线性方面,它们与其他材料相比处于劣势。12这两种材料都没有固有的 x(2) 响应;它们还表现出弱的 x(3) 非线性(氮化物)或在 1550nm 处遭受双光子和自由载流子吸收(硅),这从根本上限制了基于这些平台的量子光源的性能。许多不同的 III-V 族材料(包括砷化镓 (GaAs)、砷化铝镓 (AlGaAs)、氮化铝 (AlN) 和磷化铟 (InP))都适用于此目的,因为它们具有强大的 x(2) 和 x(3) 响应、大的折射率对比度,并且随着制造技术的进步,它们已经能够实现明亮的纠缠光子对源。13-16例如,来自绝缘体上 AlGaAs 谐振器的 SFWM 已实现 > 20 GHz/mW2 的对生成速率、巧合与意外 (CAR) 比 > 3000、每秒高达 106 次检测到的巧合、优于 99% 的单光子纯度和 > 99% 的纠缠可见度。17,18这些芯片级源现在产生的纠缠光子对的速率可与最好的固态单光子发射器和体非线性光学但同时具备室温 PIC 器件所具有的固有可扩展性、紧凑性和效率。12
与SFWM相比,对于具有破缺反演对称性的材料,更强的x(2)响应可以通过自发参量下转换(SPDC)更有效地产生光子对。19–21 一种具有未充分开发潜力的有前途的x(2)材料是与GaAs(另一种III-V族半导体)晶格匹配的铟镓磷化物(In0.49Ga0.51P)。除了高 x(2) 和 x(3) 非线性(x(2) ≈ 220pm/V,比 AlGaAs 大 1.5 倍,比铌酸锂大 10 倍)外,与为量子 PIC 开发的许多其他 III-V 材料相比,InGaP 还具有相对较宽的带隙 1.9eV(645nm)。22 因此,InGaP 器件已经在利用电子束光刻制造的悬浮微腔中利用 SFWM 和 SPDC 展示了高效的对生成。23–25 如果能够克服高质量器件的可扩展制造挑战,InGaP 有可能成为集成量子光子学的领先平台。这一挑战并不简单,正如多年来在硅、氮化硅和 AlGaAs 等更成熟的平台上的工作所表明的那样。为此,我们开发了一种绝缘体上 InGaP (InGaPOI) 工艺,可以满足集成规模和兼容性的要求。我们展示了 InGaPOI 微环谐振器和 12.5 厘米长螺旋的晶圆级制造,其传播损耗低至 1.22dB/cm,固有品质因数在 1550nm 处大于 4 × 105,如图 1 所示,针对 100mm 晶圆上的器件进行了演示。这些结果详细介绍了绝缘体上 InGaP 的 100mm 晶圆级制造工艺,利用我们现有的晶圆键合能力可以立即扩展到 200mm 生产,为制造高度非线性量子光子晶圆开辟了令人兴奋的前景(图 2)。
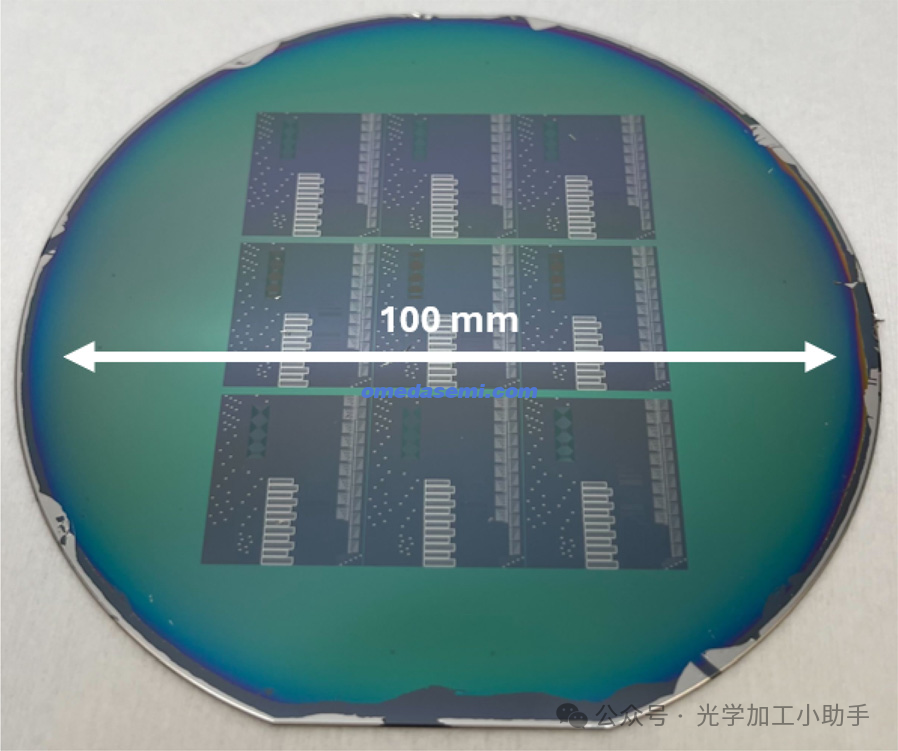
图 1. 经过完整制造过程的 100 毫米绝缘体上 InGaP(InGaPOI)晶片。
InGaPOI 制造工艺始于晶圆级低温等离子激活键合工艺,该工艺利用衬底转移外延结构方面的专业知识来开发绝缘体上复合半导体器件 14 和高性能精密激光光学器件 26。对 InGaP 外延晶圆(由 Twenty-One Semiconductors GmbH 通过 MOCVD 生长)进行检查,以确保其适合键合。使用原子力和扫描光学显微镜确认 RMS 表面微粗糙度 < 1nm 和微米级缺陷密度 1000 cm-2。然后在旋转清洗系统中用溶剂(丙酮和异丙醇)、非离子表面活性剂和去离子水的混合物彻底冲洗晶圆。清洗后,重新检查晶圆,以确保其表面没有颗粒或残留有机污染物。
在键合之前,对 InGaP 和硅基热氧化物衬底晶片进行氧等离子体激活工艺。经过最终检查后,将两个晶片装入商用键合工具(EVG 520 IS 半自动晶片键合系统)。键合室抽真空至压力 < 1 × 10-4 mbar,在室温下以 9kN 的力将晶片机械压在一起。然后在键合机外部进行 150 o C 下 12 小时的退火,以增强接触晶片的界面能。
使用 NH4OH: H2O2 湿法蚀刻去除 GaAs 衬底,无需事先对 GaAs 晶片进行任何机械研磨。蚀刻终止于 Al0.8Ga0.2As 蚀刻停止层,然后使用稀释的 HF 基湿化学蚀刻选择性地去除该层。在进一步处理之前,彻底清洁并检查了 102nm 厚的 InGaP 波导层的表面,以验证表面质量和缺陷密度。为了定义波导特征,使用原子层沉积 (ALD) 沉积了 90nm 厚的 SiO2 硬掩模。旋涂抗反射涂层和光刻胶 (DUV42P6 和 UV0.8-6),然后使用 ASML 步进工具通过深紫外光学光刻进行图案化。显影后,使用热回流工艺来平滑光刻胶侧壁的粗糙度,因为在蚀刻过程中,粗糙度可能会转移到硬掩模上,然后转移到波导轮廓上。27 必须仔细校准回流工艺,以最大限度地改善侧壁粗糙度,同时保持整个晶圆的特征尺寸和均匀性。
回流工艺后,使用电感耦合等离子体 (ICP) 蚀刻来定义硬掩模中的特征,然后进行彻底清洁以去除光刻胶和 AR 涂层残留物。然后使用 BCl3/Cl2/N2 ICP 蚀刻来定义 InGaP 中的波导。接下来,沉积 30nm 的 ALD SiO2 和 1.5μm 的 PECVD SiO2 作为波导包层,并在包层顶部的器件特定区域上方图案化 Ti/Pt 电阻加热器,以进行热光相位调谐。最后,晶圆经过刻蚀工艺,被切成 45 个独立的芯片,用于筛选和特性分析。
SFWM 和 SPDC 工艺均可通过绝缘体上 InGaP 器件实现;然而,每种工艺的最佳设计需要非常不同的波导横截面。对于任何非线性工艺,能量守恒、相位匹配、波导内光学模式的高度限制以及大量的模式重叠对于优化效率都非常重要。对于基本横向电 (TE) 模式的 SFWM,接近零色散的波导设计允许生成跨越更大带宽的纠缠对,以及单个谐振器更大范围的频率区间。使用 Tanaka 等人的色散曲线,28 我们计算了各种 SFWM 设计中 1550nm 处基本 TE 模式的波导色散,并找到了 400 × 650nm 的最佳横截面[图 3(a) 和 3(d)]。
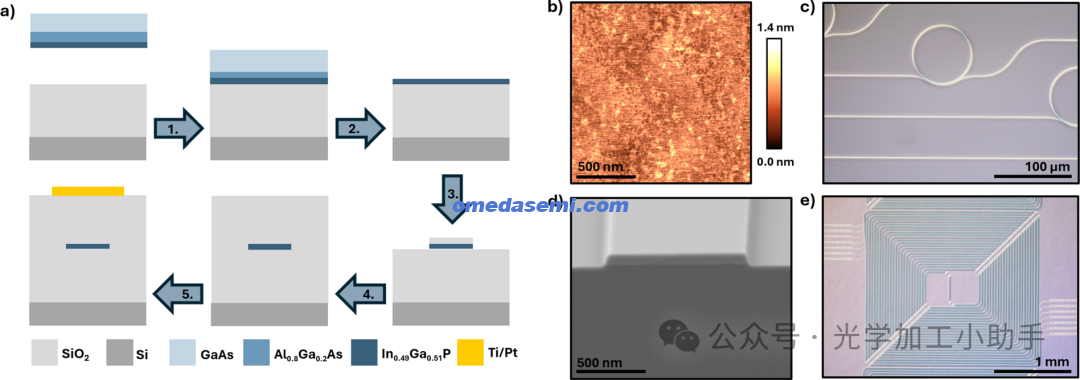
图 2. (a) InGaPOI 工艺流程图。步骤 1:将 InGaP 直接晶圆到晶圆键合到热氧化硅基晶圆上。步骤 2:通过湿法蚀刻去除 GaAs 生长衬底。步骤 3:通过深紫外光学光刻和 ICP 蚀刻在 InGaP 层中定义波导。步骤 4:氧化物包层 ALD 和 PECVD 沉积。
步骤 5:定义 Ti/Pt 电阻加热器。(b) 原子力显微镜扫描显示 RMS 表面粗糙度为 0.22nm。(c) 环形谐振器的光学显微镜图像。(d) 波导横截面的扫描电子显微镜图像。(e) 嵌套螺旋的光学显微镜图像。
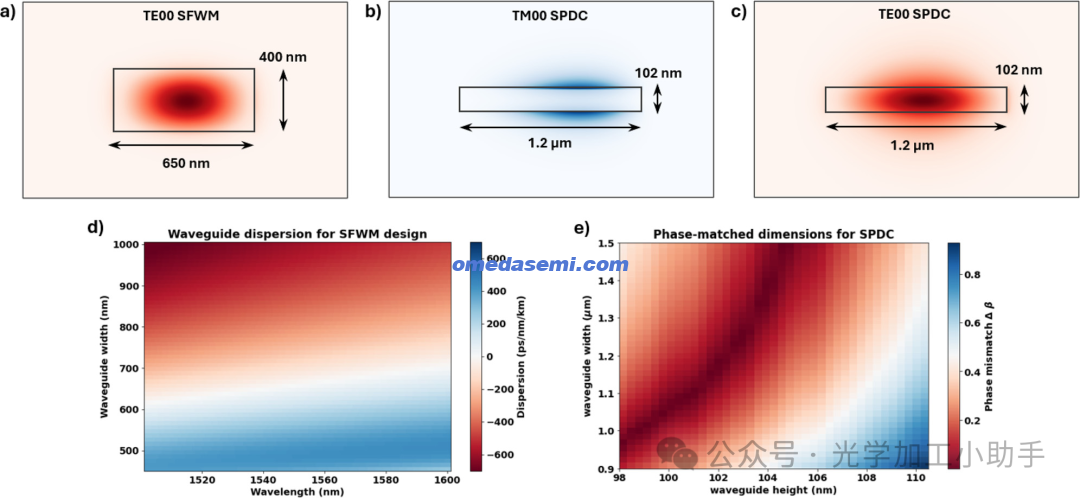
图 3. (a) 相位匹配 SFWM 1550nm TE00 模式的模式横截面。(b) 相位匹配 SPDC TM00 模式的模式横截面。(c) 优化相位匹配 SPDC 1550nm TE00 的模式横截面。(d) 厚度为 400nm 的 InGaP SFWM 设计在 1550nm 附近的波导色散。e) 厚度为 98–102nm 的 InGaP 775–1550nm SPDC 设计的频率失配与波导宽度的关系。对于厚度为 102nm 的 InGaP,模拟的片上/片外耦合损耗为边缘耦合器的 -2.5 和 -5.0dB(1550 TE00 和 775 TM00),光栅耦合器的 -4.0 和 -6.4dB。
由于 InGaP 的强色散(折射率 n = 3.41(在 775nm 处)和 n = 3.12(在 1550nm 处),SPDC 的准相位匹配只能通过使用高纵横比横截面来获得,如图 3(b)和 3(c)所示,分别针对 775nm 处的基 TM 模式和 1550nm 处的基 TE 模式。考虑能量守恒(2xTE;1550=xTM;775)和相位匹配条件 j2mTE;1550-mTM;775j = 2,其中 x 表示所示模式的角频率,m 表示谐振器中模式的方位角数,我们表明,在谐振器中,相位匹配波导宽度随波导高度急剧变化,这为 SPDC 的谐振器设计提供了额外的考虑因素。对于 102nm 的波导高度,理想宽度约为 1.2μm,尽管波导高度的 2nm 变化需要波导宽度的约 100nm 变化才能实现相位匹配。
考虑到这些因素,我们制作了一个完整的晶圆[图 1(b)],其中包括九个名义上相同的裸片(每个裸片上有五个子裸片,总共 45 个芯片),这些裸片具有环形谐振器和螺旋波导设计,并具有各种参数扫描。裸片分离后,在定制的 PIC 测试台上测试各个芯片,使用透镜保偏光纤进行光纤到芯片端耦合,芯片温度稳定在 20 o C,使用电探针进行热光调谐,并使用显微镜进行探针和光纤对准。对于每个设备,光通过波导锥形在芯片内外耦合。对于谐振器设备,滑轮耦合器设计用于波导总线到环的功率传输。扫描的参数包括环半径、环波导宽度以及滑轮耦合器总线波导宽度和角度。对于滑轮耦合器设计,耦合间隙固定在 300nm,并通过扫描角度来控制耦合。使用连续可调激光扫描 1530–1600nm 来测量每个器件的透射光谱。使用快速光电二极管和示波器测量芯片耦合的光,并使用单独的基于光纤的 Mach-Zehnder 干涉仪进行波长校准。在这项工作中,我们专注于表征 1550nm 附近的器件性能。
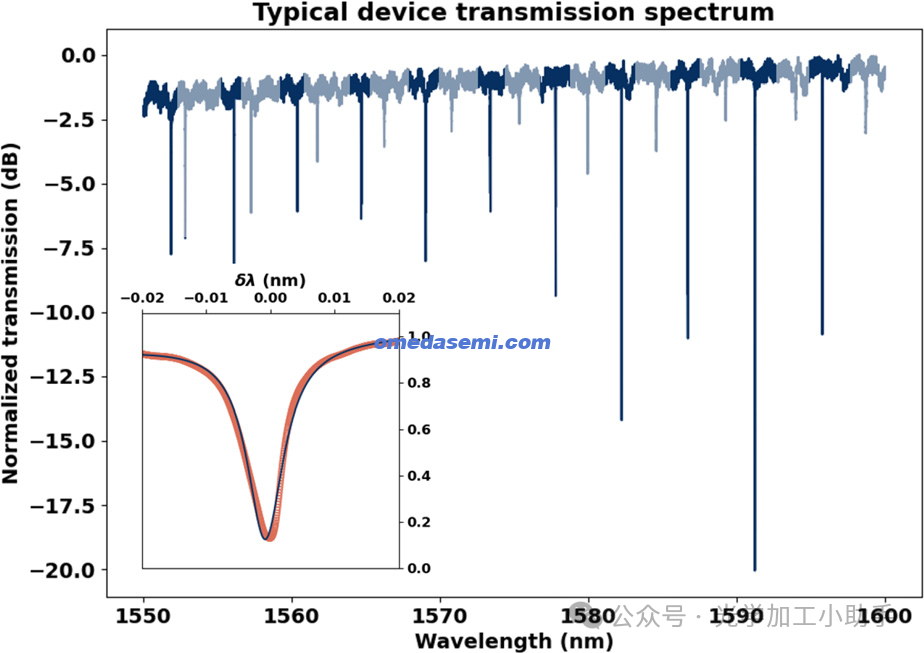
图 4. 1550–1600nm 范围内的典型环形谐振腔透射光谱。自由光谱范围分析用于确定 1550nm TE00 模式为较高消光模式系列。插图:Lorentzian 拟合谐振,QL = 213000、Qi = 342000 和 a = 1.56dB/cm。
图 4 显示了具有 32μm 半径和 1.35μm 宽度的谐振器的代表性线性传输光谱。对于 SPDC 环设计,准相位匹配所需的尺寸导致谐振器可以支持电信波长范围内的高阶 TE 模式。对于具有多个模式系列的设备,通过分析每个模式系列的自由光谱范围来识别和隔离目标基本 TE 模式。与基本 TE 模式相关的共振在图 4 所示的光谱中以深蓝色突出显示。每个共振都使用 Moresco 等人开发的分析模型进行拟合。该模型考虑了由于反向散射导致的驻波模式之间的相互作用,这会导致某些设备发生共振分裂,而所有设备中都会发生行波环模式。29 通过拟合,我们可以确定加载的品质因数 QL 、与波导传播损耗 a 成反比的固有品质因数 Qi ,以及决定相关长度和导致反向散射的表面粗糙度 RMS 值的反射系数 q 。对于没有共振分裂的模式,该模型的拟合与 Lorentzian 拟合的一致性在 ~ 1% 以内。图 4 的插图显示,从该特定设备测得的 Qi 高达 324000,对应的传播损耗为 1.56dB/cm。
环设计的参数扫描可用于提取传播损耗与环半径和环波导宽度的关系趋势,这两者都有助于评估 InGaPOI 设备在非线性频率转换和量子光生成方面的潜在性能。在较小的环半径下保持较低的传播损耗可以实现更小的模式体积,从而实现更高的转换效率。图 5(a) 显示了当微环谐振器半径从 20 μm 增加到 40 μm 时,从晶圆上的三个芯片测得的平均传播损耗。对于最接近与总线波导临界耦合的器件设计,选择每个芯片上波导宽度为 1.45μm 的相同谐振器。随着半径的增加,平均传播损耗从 ~ 5.4 dB/cm 降低到 ~ 2.4 dB/cm。根据该曲线,我们估计,对于低于 ~ 20 - 25 μm 的半径,由于与侧壁的模式重叠较大而导致的谐振器散射开始超过材料吸收损耗并决定加载的品质因数 QL 。
接下来,我们检查了不同谐振器波导宽度的平均传播损耗,如图 5(b) 所示。随着宽度的增加,由于与蚀刻波导侧壁的模式重叠减少,损耗降低至约 2.5 dB/cm。对于图 5 中半径和宽度扫描的数据,误差线显示为与至少三个不同的名义上相同的设备的平均值的标准偏差。对于较小的半径和宽度,由于与侧壁的模式相互作用较大,因此观察到较大的设备间差异。在这些设计中,制造工艺变化对散射有更大的影响,因此对测量的 Q 有更大的影响。图 5(b) 说明,在一系列环形波导宽度上低传播损耗确保了此处展示的高设备性能反映了也满足此波导厚度相位匹配要求的设备设计的性能。
最后,我们在图 5(c) 中展示了晶圆上每个芯片中 Q 值最高的器件的线性传输图,范围从 194000 到 440000(不一定与谐振器 FSR 或波导宽度相似)。我们看到,对于一些 Q 值最高的谐振器,谐振由于反向散射而分裂,这随着 Q 值的增加而更加明显,正如 Moresco 等人之前讨论的模型所预期的那样。在表 II 中,我们将从这些测量中确定的线性传播损耗与其他专为非线性光学转换和对生成过程而开发的 x(2) 光子平台的线性传播损耗进行了比较。
值得注意的是,虽然许多其他平台的损耗已达到 1dB/cm 以下,但除 AlGaAsOI 外,它们都是使用电子束光刻 (EBL) 制造的,而我们研究中的 100 毫米晶圆级制造则使用深紫外光刻。本文报道的 1550nm 传播损耗为 1.22dB/cm,是最近提出的异质集成非线性平台(ScAlNOI 和 GaNOI)中最低的,具有器件性能改进的良好前景。研究表明,使用 Al2O3 层对 InGaP 进行表面钝化可将电信波长的固有品质因数提高 3 倍。24 研究表明,使用氘代 SiO2 可将 1550nm 处包层的材料吸收率降低约 7 倍,并有可能提高可见光波长范围内的性能。30
总之,我们提出了一种绝缘体上 InGaP 100 毫米晶圆级制造工艺,特征尺寸为 200nm,采用直接晶圆键合和基板去除、深紫外光刻和干法蚀刻方法。每个晶圆可生产 1000 个光子元件,波导传播损耗低至 1.22dB/cm,1550nm 谐振器品质因数高达 440000。对波导横截面的损耗和色散的数值和实验表征为 SFWM 和 SPDC 非线性过程建立了最佳方案。考虑到较大的 x(2) 和 x(3) 非线性,
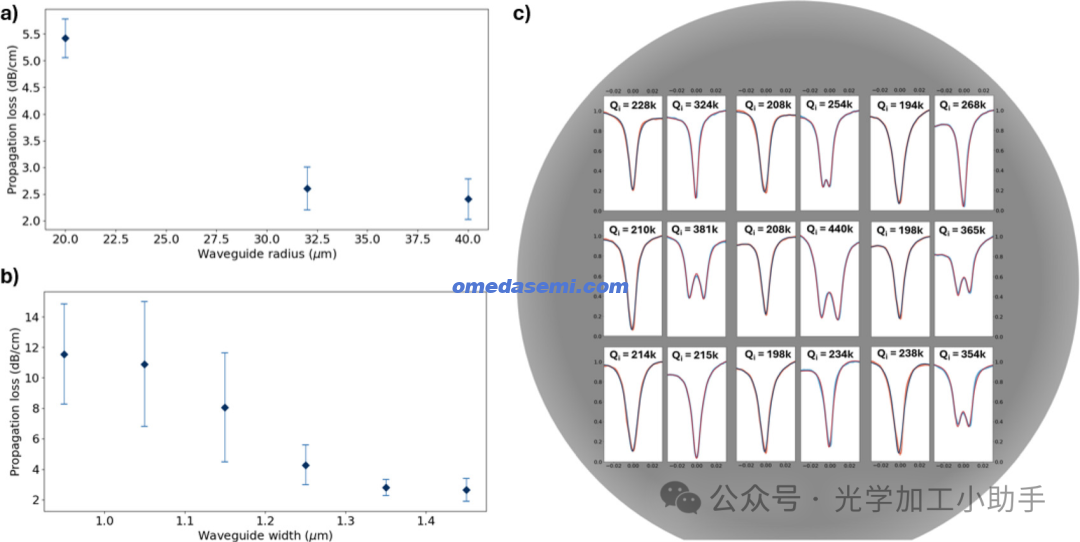
图 5. (a) 宽度为 1.45μm 的环的传播损耗与半径的关系。(b) 半径 = 32μm 的环的传播损耗与环波导宽度的关系。对于 (a) 和 (b),每个值都是从至少三个芯片的相同设备设计中取平均值,以最接近临界耦合的设备设计为准。(c) 晶圆上九个芯片中每个芯片的两个设备的最高固有品质因数。在每个芯片面板的左侧,相同的设备设计,半径 = 32,宽度 = 1.45μm。右侧,具有最高固有品质因数的任何设计参数的设备。所含设备的半径为 32–40μm,宽度为 1.35–1.55μm。使用文中描述的分裂共振传递函数拟合共振,并使用正弦背景校正来解释轻微的面反射。对于相同的设备设计,内在品质因数范围从 194000 到 238000,平均值为 211000,标准差为 14400(变化高达 7%)。
表 II. 为非线性频率转换和量子光生成而开发的不同 x(2) 集成光子平台的 1550nm 线性传播损耗比较。GaNOI 损耗是根据已发表的数据估算的;其他数据来自列出的引文。DUV-PL:深紫外光刻。EBL:电子束光刻。
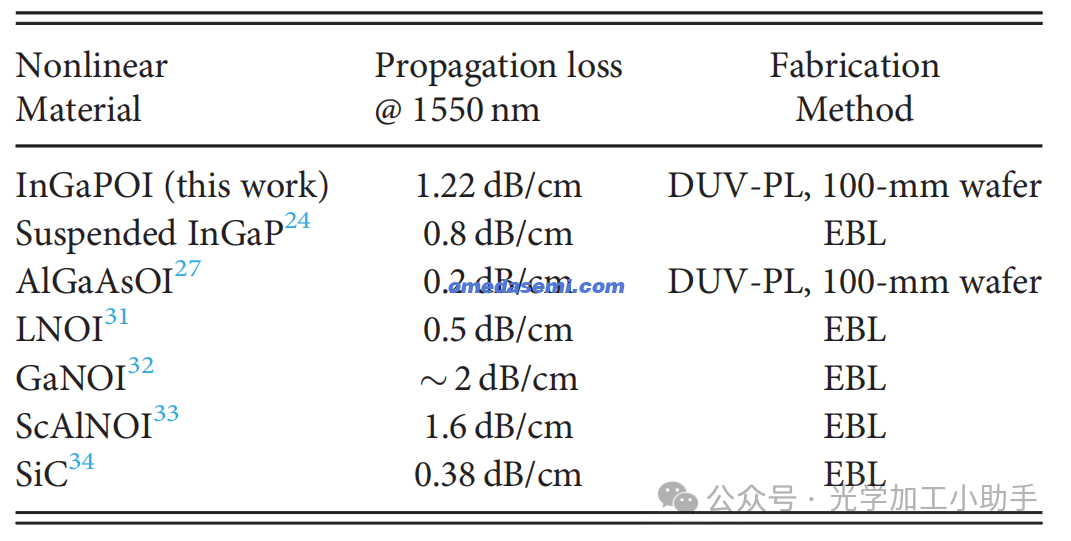
由于 InGaP 具有宽带隙 (1.9eV) 和高折射率 (> 3),这些结果表明 InGaP 是各种非线性光子应用的有希望的候选材料,包括二次谐波产生、量子频率转换、宽带纠缠对产生和压缩光产生。
这项工作的一部分是在 UCSB 纳米制造设施进行的,这是一个开放的实验室。我们感谢 SRI International 的 Ifeanyi Achu、Navin Lingaraju、Joseph Christesen 和 Cale Gentry 在设备建模和设计方面提供的技术投入和帮助。晶圆由 Twenty-One Semiconductors GmbH 提供。这项工作得到了 NSF Quantum Foundry 通过 Q-AMASE-i 计划(拨款编号 DMR-1906325)、NSF CAREER 计划(拨款编号 2045246)和空军科学研究办公室(拨款编号 FA9550- 23-1-0525)的支持。L.T.感谢美国国家科学基金会研究生奖学金计划的支持。