本文小编分享大家双光子打印的另外一篇应用,用双光子3D打印技术,打印MEMS加速度传感器。微机电系统 (MEMS) 设备(如加速度计)广泛应用于各行各业,包括汽车、消费电子和医疗行业。MEMS使用大规模半导体制造技术以非常高的产量高效生产。然而,这些技术对于中小批量生产专用MEMS器件的经济高效是不可行的。因此,对于年产量低于 5000–10,000 个元件的中低规模市场,需要定制设计的 MEMS 器件的应用极难有效解决。MEMS器件的3D打印可以有效地实现和生产这些中低规模的MEMS器件。然而,目前的微型3D打印技术在打印功能性MEMS方面的能力有限。在此,我们展示了一种功能性3D打印的MEMS加速度计,该加速度计使用双光子聚合的3D打印,并结合金属蒸发的应变计换能器的沉积。我们表征了MEMS加速度计的响应度、谐振频率和随时间变化的稳定性。我们的研究结果表明,功能性MEMS的3D打印是一种可行的方法,可以有效地实现各种定制设计的MEMS器件,解决使用传统MEMS制造难以或不可能解决的新应用领域。
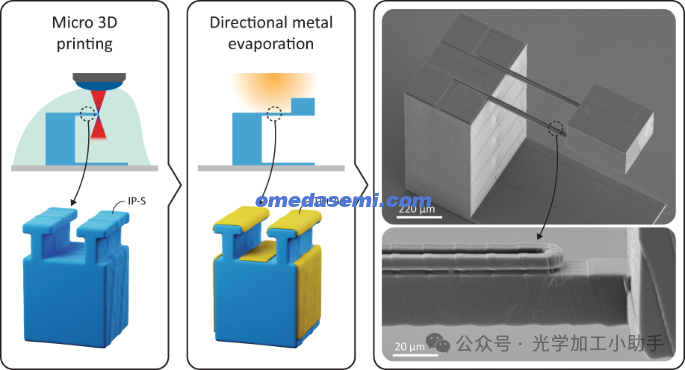
划重点(双光子3D打印代工)
在光纤端面亦或其他基底材料上通过双光子3D打印的方式一直是科研工作者研究的关注点,但是由于高精度双光子3D打印的设备极其昂贵,技术也较为前沿,许多科研工作者乏于寻找可靠的,高效率的加工提供商。
小编也很有幸,曾经见到国内有团队已经实战在光纤端面做各种超结构,并且得到了客户满意的效果。
因此如果您有需求,可以联系小编为您推荐成熟的双光子3D打印企业,加速您的创新。
如果你也爱好 半导体,光学,光纤,硅光集成等技术及应用,可以添加小编,一起畅聊技术,市场和应用。
看原文请联系小编免费领取
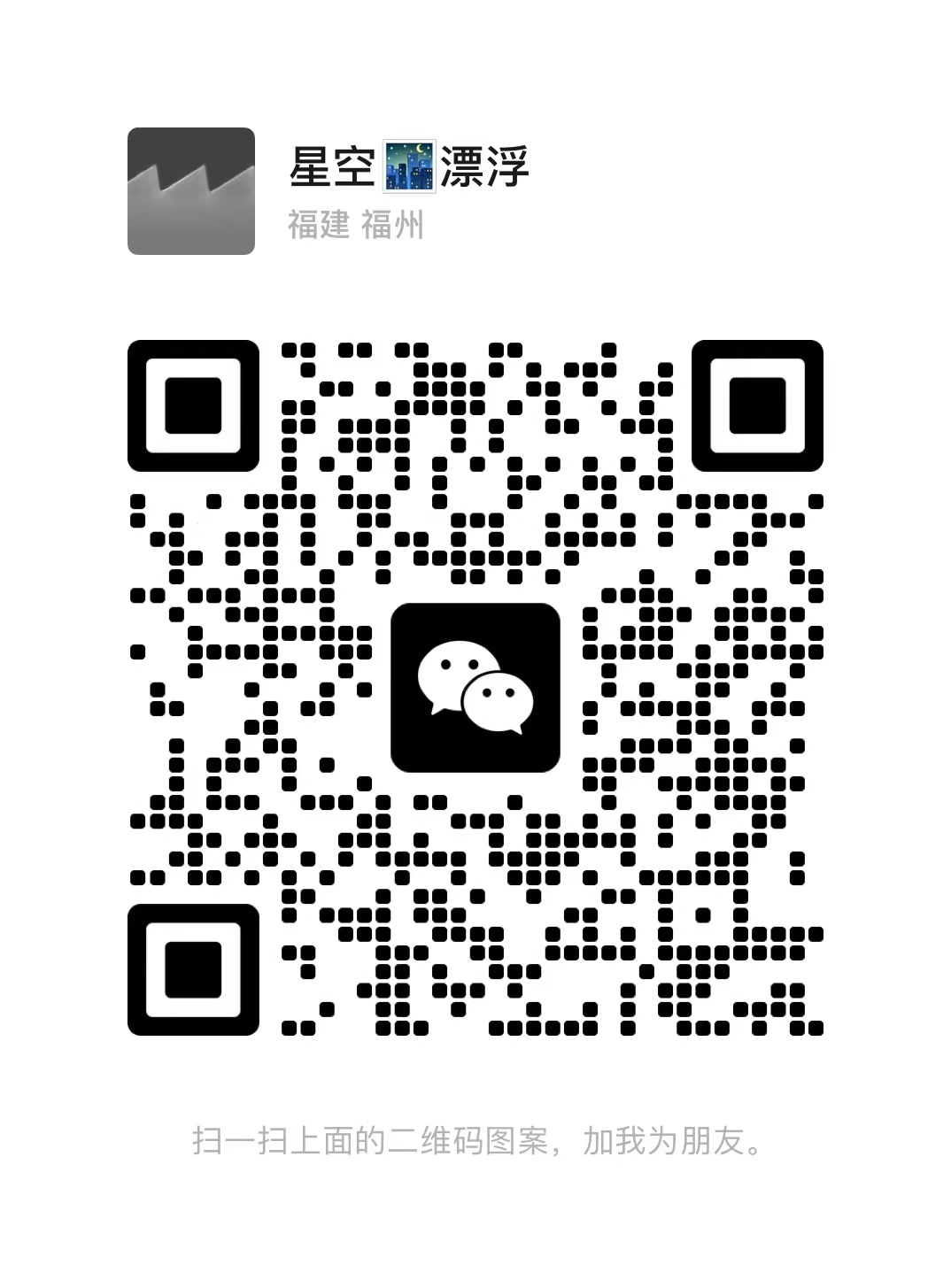
介绍
近几十年来,微机电系统 (MEMS) 传感器(包括加速度计、陀螺仪、压力传感器和麦克风)取得了巨大成功。如今,它们在许多应用中无处不在,例如手机、汽车、游戏机和导航系统。然而,用于机器人、航空航天和医学等专业高价值应用的中小批量 MEMS 组件的生产往往受到制造工艺开发和器件设计优化的高启动成本的阻碍。这些启动成本是固定成本,不会随着产量 1 的增加而增加。因此,可扩展性不仅是MEMS生产的优势,也是确保高投资回报的必要条件。因此,新型商用MEMS器件的开发通常仅限于满足大批量市场的器件。对于一些中小尺寸的应用领域,这要求工程师使用市场上的次优MEMS器件。甚至可能无法以经济上可行的方式解决其他应用。新兴的微型3D打印技术可以填补这一空白,并实现中小批量MEMS组件的制造。这包括MEMS的快速原型设计,以实现高度专业化的定制应用,以及以中小型制造量(即几百到几千个器件)的经济高效制造MEMS制造。
近几十年来,宏观3D打印技术因其灵活性和多功能性而被广泛用于机械零件 2 的快速原型制作。最近,它们也被引入许多行业的最终组件制造中,例如汽车 3 和航空电子设备 4 ,特别是在需要复杂组件几何形状和低制造量的情况下。最近,不同的3D打印技术已被用于实现功能性的宏观和中尺度传感器设备 5,6 。其中,宏观惯性传感器采用熔丝制造、激光粉末床熔融 9 和立体光刻等技术 7,8 制造 10,11,12 。这些器件的尺寸从几毫米 2 到几厘米 2 不等,因此不适合小型化至关重要的应用。由于所使用的3D打印技术的固有局限性,这些类型的3D打印传感器设备的占地面积减少仍然具有挑战性,这些技术最多只能达到几十或数百微米 5,6 的尺寸,从而为传感器的小型化和精度以及相关的带宽限制设定了实际限制。
在适用于实现微尺度器件的3D打印技术中,双光子聚合,也称为多光子聚合或直接激光写入,非常适合打印MEMS器件。通过双光子聚合的3D打印在所有空间方向上提供低于1μm的分辨率 6,13 ,匹配并在某些情况下克服了基于洁净室的光刻工艺的分辨率。如此高的分辨率对于MEMS器件的实现至关重要;因此,该技术已被用于实现微流控电路 14 、光学器件 15 和组织工程 16 支架。除了能够进行微米级和纳米级打印外,双光子聚合还允许在3D空间中以高度的设计自由度进行3D打印。然而,使用这种技术在微尺度上实现电功能传感器和传感器结构非常具有挑战性。虽然通过双光子聚合和随后的铝溅射进行3D打印已被用于制造热机械和静电致动器 17,18 ,但3D打印的微尺度惯性传感器,如MEMS加速度计和陀螺仪,尚未实现。在本工作中,我们展示了第一个3D打印的功能性MEMS加速度计,该加速度计使用双光子聚合与金属蒸发相结合形成应变计传感器。我们对3D打印的MEMS加速度计进行了表征,并确认了其成功运行。
结果
3D打印MEMS加速度计
为了证明3D打印功能MEMS加速度计的实际可行性,我们设计了一种加速度计结构,可以通过双光子聚合进行3D打印,随后的定向金属沉积步骤用于形成应变片传感器元件、电气互连和探测电极(图1a)。我们使用 Nanoscribe Photonic Professional GT2(Nanoscribe GmbH,德国)3D 打印机和商用 IP-S 树脂(Nanoscribe Gmbh,德国)在玻璃基板上打印了加速度计结构。机械加速度计结构由一个支撑柱组成,该支柱带有两个单侧夹紧的水平悬臂,并在两个悬臂的末端连接一个验证质量(图1a和补充信息,图S1)。3D打印工艺提供的设计自由度使我们能够在悬臂和支撑柱的顶部使用T形横截面(图1b)对阴影掩蔽结构进行图案化,以定义应变片传感器、电气互连和探测电极的区域(图1d,e)。T形阴影掩蔽结构与使用定向蒸发工艺沉积10 nm厚的Ti层和30 nm厚的Au层相结合(图1c,参见“材料和方法”部分),导致在3D打印加速度计结构的不同表面上形成电分离金属涂层,从而形成电隔离探测电极, 互连,电阻器充当金属应变片。我们选择了T形结构的尺寸(图1)。1b) 确保 (a) 使用所选树脂和显微镜物镜对结构进行可靠的 3D 打印,以及 (b) 在金属沉积过程中有效的阴影掩蔽,导致金属线和涂层电断开。支撑柱和悬臂的顶面放置在相同的高度,以便在应变计电阻器和探测电极之间轻松形成电气互连(图 1d)。校样块的底面与悬臂的底面平整,以避免印刷过程中出现所谓的“飞块”,即印刷时未附着在固体结构上的打印块。
图1:3D打印加速度计。
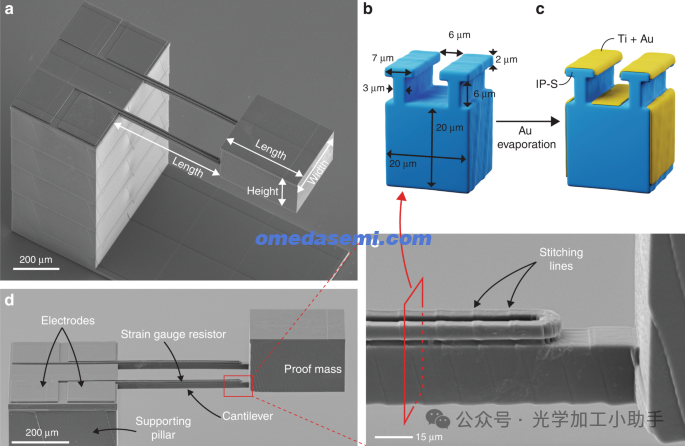
3D打印加速度计结构的SEM图像。b 金属蒸发前悬臂横截面的三维示意图。c 金属蒸发后悬臂横截面的 3D 示意图,显示了实现电阻器电气隔离的阴影掩蔽机制。d 设备顶部侧视图的 SEM 图像。e 悬臂顶部T形电阻器的特写视图。SEM图像中显示的结构涂有一层薄的溅射Au-Pt层,以提高SEM图像质量。
我们的MEMS加速度计的工作原理类似于标准压阻式MEMS加速度计的工作原理,即,在垂直于基板表面的方向上作用在证明质量上的外部加速度产生导致悬臂弯曲的力(根据牛顿第二定律 F = m*a,F = 力,m = 证明质量, 和 a = 加速度)。悬臂的弯曲导致悬臂顶部的电阻式金属应变片的应变以及应变片电阻的相关变化。应变片的电阻变化与感应应变相关,并最终与施加的加速度相关。
对于加速度计设计的布局,我们在 COMSOL 中开发了一个参数化有限元模型, ® 用于计算获得加速度计 1–10×g 测量范围所需的几何参数,这是消费电子、导航或工业应用 19 中的典型规范。建模的详细信息在“材料和方法”部分进行了描述。为了保证机械加速度计结构的高灵敏度,即在低加速度下具有较大的弯曲位移,必须最小化悬臂的厚度和宽度,同时必须最大化其长度和证明质量的大小。基于我们之前在3D打印长悬臂结构方面的经验,我们选择悬臂的厚度和宽度各为20μm,这样可以很好地控制悬臂和两个平行的T形线结构的打印,这些结构在悬臂顶部形成应变计电阻器(图1d,e)。接下来,使用 COMSOL® 模型,我们对剩余的几何参数进行了全面分析,这些参数是悬臂的长度和附着的证明质量的质量,计算方法为证明质量的体积乘以聚合物的密度。在参数扫描中,我们选择了 500 μm 的悬臂长度和 350 μm × 300 μm × 210 μm(长度×宽度×高度)的证明质量尺寸。对于3D打印的加速度计结构,我们发现悬臂的实际长度始终偏离设计的500μm长度;因此,我们将 COMSOL® 模型的尺寸调整为测量的悬臂长度 480 μm。
加速度计表征
为了表征 3D 打印加速度计的性能,我们制造了三个设计相同的设备,并测量了它们随时间变化的共振频率、响应度和响应稳定性。为此,我们使用了一种由压电振动器和激光多普勒测振仪(LDV)组成的装置,它们都连接到锁相放大器。锁相放大器以所需频率驱动压电振动器,同时解调来自激光多普勒测振仪的信号,该信号与证明质量的机械振荡幅度和电阻应变片探头在相同频率下的振幅相关。在校准压电振动器后(参见“材料和方法”部分),我们表征了加速度计在其共振频率下的机械响应。我们通过扫描 1.4 到 2 kHz 之间的驱动电压频率来评估机械响应。该信号以不同的振幅发送到压电振动器,范围从 1 到 7 V rms 。我们测量了三个加速度计的谐振频率,使其可靠地在1.775 kHz±5 Hz范围内,Q因子范围在31至36之间(图2a,补充信息,第S6节中的详细信息)。我们观察到,与没有接触式探头测量的相同设备的 Q 因子 (41.5 ± 1.4) 相比,探头在加速度计电极上的位置影响了 ±30% 范围内的 Q 因子。同时,我们没有观察到探头对3D打印加速度计测量的共振频率有任何显着影响。对于每个器件和驱动电压幅度,我们绘制了最大振荡幅度与施加加速度的关系图(图 2b)。这些图显示了加速度计的机械响应在评估的垂直质量位移范围内的线性行为,最高可达 1.9 μm。位移幅度测量是在证明质量之上进行的,并且在每个设备上选择不同的确切位置,以最大限度地提高激光反射并最大限度地减少激光多普勒测振仪读数中的噪声。我们将测得的谐振频率和位移幅度与改编后的 COMSOL ® 模型的仿真数据进行了比较。假设聚合物的杨氏模量为6.5 GPa,模拟共振频率与测得的共振频率1.775 kHz一致。位移幅度是根据质心处的平均Q因子34提取的,并绘制在图2b中。正如预期的那样,模拟数据位于不同测量数据集的范围内。此外,为了基本了解不同设计参数对加速度计力学行为和共振频率的影响,我们开发了两个基于欧拉-伯努利梁理论的理论模型(参见补充信息,第S5节)。通过这些模型,我们使用从 COMSOL ® 仿真中提取的弹性模量预测了共振频率在测量值的 10% 以内。
图2:机械特性。
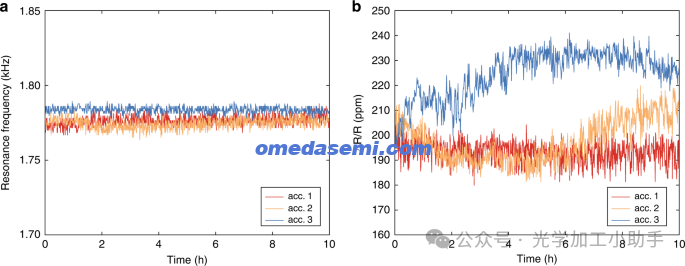
a 使用压电振动器驱动电压7 V时,MEMS加速度计证明质量在不同频率下的振荡幅度。所有器件的最大振荡幅度均在 1.77 至 1.78 kHz 之间,而不是 COMSOL ® 中开发的模型预测的 1.58 kHz,使用材料数据表 30 中指定的 5.1 GPa 杨氏模量测量谐振频率。测得的谐振频率对应于实际的杨氏模量 6.5 GPa。拟合洛伦兹曲线可产生 36(加速度计 1)、31.7(加速度计 2)和 35.7(加速度计 3)的 Q 因子。b 在压电振动台施加的不同加速度下测量和模拟证明质量的振荡幅度。在谐振频率下测量振幅,并将模拟力乘以平均 Q 因子 34 以匹配共振时的行为。
我们的 3D 打印加速度计的响应度定义为相对电阻变化 (ΔR/R) 与施加加速度的函数,是在共振频率下测量的。与我们的机械特性类似,我们在 1 至 7 V 的电压下扫描了 1.4 至 rms 2 kHz 的驱动电压。对于每个3D打印的加速度计和电压,我们进行了两次频率扫描。从锁相放大器每次扫描输出的下混电压中,我们提取了应变片传感器的相对电阻变化值并绘制了图(图3a,b,c)。根据锁相放大器输出信号的最大幅度,该幅度发生在器件的谐振频率上,我们计算了关断谐振相对电阻变化,并将其与压电振动器为每个器件施加的相应加速度(Fig. 3d)作图。因此,我们提取了三种不同器件在谐振频率下的响应度范围为 322 和 420 ppm/g,除以每个器件的测量 Q 因子,在标准测试频率 (100–160 Hz) 下,所有三个器件的响应度为 11 ± 0.7 ppm/g。根据这些响应度值和测量的质量位移,我们计算出所有器件的薄膜应变片探头的表规系数在 3.5 ± 0.6 之间。测得的标距因子高于我们在 COMSOL 中模拟的改编模型中提取的标距因子,该值为 2 ® ,这对于块状金导体而不是薄膜导体是预期的(参见“讨论”部分)。
图3:电气特性。
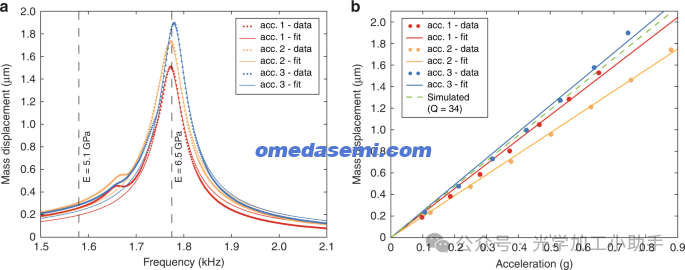
在加速度计 1 in (a)、加速度计 2 in (b) 和加速度计 3 in (c) 上测量压电振动器不同频率和驱动电压下的相对电阻变化 (ΔR/R)。共振频率的明显变化归因于聚合物在大振荡幅度下温度升高。d 应变片传感器的相对电阻变化与施加在MEMS加速度计上的加速度的函数,计算出的非谐振。
使用聚合物作为结构材料的MEMS传感器的重要考虑因素是传感可重复性和长期稳定性。为了评估我们的 3D 打印 MEMS 加速度计随时间推移的稳定性,我们对每个设备进行了 10 小时的测量。在这些实验中,我们在5 V rms 的恒定驱动电压下连续对压电振动台进行频率扫描,同时跟踪应变片传感器的相对电阻变化。对于每次扫描,我们提取了加速度计的共振频率和最大相对电阻变化,并绘制了它们随时间的变化(图 4)。在整个测量过程中,测得的谐振频率不会随时间推移而出现明显的漂移,保持在每个器件的平均值±4 Hz的范围内(图4a)。这证实了我们的加速度计的机械响应是稳定的,不会降低聚合物的机械性能。此外,在测量期间,应变片传感器的相对电阻变化对于三个器件没有显着变化(图4b)。对于其中两个器件,我们观察到在20分钟的测量中,滚动平均值的相对电阻变化约为20 ppm,而第三个器件的值与初始值保持±4 ppm。这些响应度的变化可能是由于施加在器件上的加速度的变化,该加速度已被测量为在相似的范围内(参见“材料和方法”部分),和/或由于沉积在聚合物上的金属薄膜的相对电阻变化的变化,这些金属膜受到机械载荷和电流的影响。后一种效应以前已有报道,主要归因于脆性粘附层 20 的局部开裂和/或多晶金属膜 21 中晶粒的重新排列。在这些实验中监测温度和相对湿度,以评估环境参数对实验设置中设备性能的影响。这两个环境参数都显示出最小的变化,对设备性能的变化没有显着影响(参见补充信息,第 S7 节)。
图4:稳定性评估。
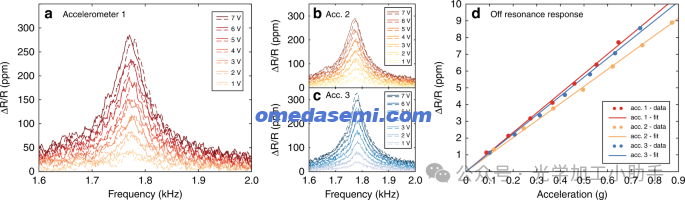
使用5 V rms 的恒定压电振动器驱动电压测量三个器件在10小时内的相对电阻变化和谐振频率。a 对于每个设备,谐振频率在平均谐振频率的±3.8赫兹的范围内保持稳定。b 在共振频率下计算的相对电阻变化ΔR/R相对于加速度计2和3的初始值205 ppm偏移约20 ppm,而加速度计1的相对电阻变化稳定在193±5 ppm。
讨论
在这里,我们演示了使用微型 3D 打印和随后的简单定向金属蒸发步骤制造三个功能齐全的 MEMS 加速度计。一个加速度计结构的3D打印,包括显影和紫外线泛光暴露,耗时1小时45分钟(未优化,实现最短打印时间),金属蒸发耗时40分钟,其中30分钟是由于我们设备的真空泵送。因此,制造单个MEMS加速度计所需的总时间不到2个半小时,只需要两个相对便宜的商业制造工具(双光子聚合3D打印机和金属蒸发器),并且不需要洁净室。此外,在制造一批多个设备时,一些过程,如紫外线照射和金属沉积,可以在许多设备上并行进行,从而大大减少了每个加速度计所需的制造时间。此外,虽然与其他3D打印技术相比,双光子聚合3D打印机的购买和操作成本仍然相对较高,但随着对平行光束 13 和更灵敏的 22 光聚合物的研究显示出有希望的结果,这些类型的3D打印机的生产率预计将在未来几年内提高。提供亚微米分辨率 23,24,25 的替代 3D 打印技术在几何形状和打印速度 13 方面比双光子聚合更受限制。我们的演示表明,这种方法对于MEMS器件的原型设计以及以经济可行的方式每年制造数十到几千个MEMS传感器的中小批量是可行的。这是直到现在还不可能实现的,因为使用传统半导体技术制造MEMS产品的启动成本约为数十万美元,交货时间为几个月或更长时间。3D打印MEMS提供的新功能可能会导致MEMS和传感器制造的范式转变,使MEMS创新能力可供更广泛的社区使用,并有可能通过定制设计的MEMS产品有效地解决专业应用和利基市场。此外,与传统的硅表面和体微加工技术相比,3D打印提供了更高的设计自由度,能够实现以前不可能实现的结构复杂性。在这项工作中,我们选择了一种相对简单的加速度计悬臂设计,其横截面为方形,以展示这种新制造方法的简单性和易用性。然而,双光子聚合的3D打印能力允许更先进的传感器设计,例如具有不同横截面 26 或蜂窝微架构的传感器设计 27 ,这将对器件的性能和功能产生重大影响,并最终产生新的和改进的MEMS器件。
我们演示的3D打印MEMS加速度计涉及使用聚合物作为结构材料。虽然大多数MEMS由于其出色的机械性能而由硅制成,但聚合物越来越多地被探索为MEMS和传感器材料,包括用于柔性和可生物降解的器件 28 。使用聚合物作为结构MEMS材料的一个重要问题是其性能和稳定性随时间 29 推移的可重复性。此外,聚合物的机械性能,如弹性模量和拉伸强度,会受到温度和湿度等环境条件的影响,尽管这可以通过器件封装来缓解。我们通过在10小时内测量其800多次频率扫描的共振频率,证明了聚合物MEMS加速度计的机械稳定性,其中包括超过6000万次振荡。我们发现,在这些实验中,共振频率以及聚合物结构的力学和尺寸性能保持稳定。测得的共振频率(1.775 kHz)与仿真模型预测的频率一致,考虑到3D打印悬臂的实际测量长度为480 μm(标称长度为500 μm),并假设打印的IP-S聚合物的杨氏模量为6.5 GPa(材料数据表中所示的值为5.1 GPa),密度为1100 kg/m 3 (来自材料数据表 30 30 )).悬挂式悬臂的长度比标称设计的长度短约4%(补充资料,第S4节)。这种收缩水平在IP-S聚合物的典型预期范围内 29 。印后收缩是双光子聚合中的一种已知现象,它会影响基于丙烯酸酯(如IP-S)的聚合物树脂,但这是一种一致的影响,可以通过使用收缩补偿方案来减轻 31 。调整后的杨氏模量值在可以预期的公差范围内,因为众所周知,双光子聚合材料的机械性能可能取决于打印参数,例如激光脉冲能量、打印速度和激光脉冲之间的重叠 32 。双光子交联聚合物材料的刚度增加先前已被证明发生在更高水平的交联中,这也是由于开发后进行的紫外线泛滥暴露以及沿悬臂长度的相邻打印块之间的界面处的大量缝合区域 33 ,接受了双重暴露剂量。在MEMS中使用聚合物作为结构材料的一个潜在优势是其非常低的弹性模量,即使在低加速度和相对较短的悬臂下,也可以实现非常大的证明质量位移,这可以在小尺寸的器件中实现低至1μg/\(\sqrt {{{{\mathrm{Hz}}}}}\)的检测限 34 。未来,打印后可以烧结成非聚合物结构的3D打印复合材料可以用作3D打印MEMS的结构材料,以避免聚合物的缺点,尽管烧结步骤通常会引起较大的内应力,从而导致打印 35,36 结构变形。
在我们的3D打印MEMS加速度计中,我们使用了40纳米厚的金属层作为应变片传感器的电阻器。在使用应变片的加速度计中,加速度计的响应性取决于其将加速度转换为电阻应变的能力,以及电阻将应变转换为电阻变化的能力。电阻器的应变是由作用在证明质量上的加速度引起的悬臂弯曲引起的。悬臂弯曲取决于悬臂的几何形状和材料。正如我们的理论模型(补充信息,第 S5 节)所描述的,悬臂和证明质量位移与悬臂长度的立方成正比,与悬臂截面面积的第二弯矩和悬臂材料的弹性模量成反比。悬臂弯曲会在悬臂的垂直横截面上引起应力和应变的变化,在悬臂的底部和顶面上最大,应变计电阻器的位置可以充分利用悬臂弯曲。由于悬臂弯曲而在电阻器中引起的应变可以使用分析模型 37 进行计算(参见补充信息,第 S5 节)。相对电阻变化ΔR/R与应变的比值通常称为规因数,它是电阻器的几何变化与应变片材料电阻率因施加应力而变化的总和。在金属中,电阻率的这种变化通常可以忽略不计,标距系数通常只是金属线几何形状变化的结果。然而,据报道,厚度为 30 nm 或以下 38 的 Au 薄膜的规格系数略高,其中电阻率的额外变化归因于表面粗糙度和多晶金属膜 39 中晶粒之间边界的存在。我们通过测量传感器的相对电阻变化ΔR/R(如“结果”部分所述)±测量应变,并使用测量的质量位移幅度用理论公式 37 计算应变,估计了三种器件的薄膜Au传感器的标距系数为3.5 0.6,这表明应变片变形和电阻率变化都有贡献。我们的加速度计测得的响应度为 11 ppm/g,在其他已发布的加速度计和市售加速度计的范围内,例如用于冲击测试的加速度计 40 41 。原则上,我们的加速度计设计可以通过与较低谐振频率的权衡来调整几何参数,从而实现更大的响应度。在不降低谐振频率的情况下,也可以通过实施优化的加速度计设计 42 或使用由具有更大规格系数的压阻材料制成的电阻器来实现更大的响应度。电阻应变片的金属的有趣替代品可能是蒸发的锗 43 和溅射的非晶态碳 44,45 ,它们已经被用作柔性基板上的应变片,并具有高于30的应变系数。然而,重要的是,材料沉积中涉及的温度与3D打印聚合物兼容,通常低于300°C。
为了表征加速度计的响应度,我们在共振频率下进行了测量,以确保输出信号明显高于输出噪声,即使在施加的加速度低至0.1 g的情况下也是如此。当没有信号施加到压电振动器时,我们测得的噪声密度为90 nV/√Hz,这对应于谐振时约4 mg/√Hz和标准测试频率(100–160 Hz)下约0.2 g/√Hz的噪声等效加速度。通过进一步优化读出电路,输出信号的噪声密度可以降低到4 nV/√Hz,或者通过使用压阻式加速度计 34 的特殊低噪声专用集成电路(ASIC)来降低。在标准测试频率下,这种低噪声功率密度将导致10 mg/√Hz的噪声等效加速度,这与市售MEMS加速度计 19 相当。此外,当在共振频率下操作加速度计时,我们在0.9×g的加速度下实现了较大的证明质量位移。通过这种方式,我们证明了在高达1.9 μm的证明质量位移下加速度计响应的线性度。这相当于悬臂末端约1.2μm的悬臂挠度,并且仅在标准测试频率下的加速度>35×g时发生。
综上所述,我们的研究结果表明,功能性3D打印MEMS加速度计实际上是可行的,并有望实现竞争性能。我们提出的MEMS增材制造方法有可能应用于各种MEMS传感器,如压力传感器、麦克风、陀螺仪和流量传感器。此外,3D打印将为新型MEMS传感器提供创新和复杂的器件几何形状,这是目前使用传统的2.5D硅微加工无法实现的。我们通过集成阴影掩蔽元件与定向材料沉积相结合来选择性地功能化 3D 打印 MEMS 结构表面的策略是通用的,有助于创新设计和各种换能器元件的集成,例如压敏电阻器、压电元件和纳米线元件。重要的是,小批量3D打印MEMS的设计和制造之间的快速周转使我们能够评估设备的性能并在几个小时内对其进行优化。从工业角度来看,这大大降低了为中小批量应用制造新型定制MEMS器件的启动成本,而使用标准微纳加工技术的制造成本将高得令人望而却步。因此,我们对功能性MEMS的增材制造方法,以及该技术所实现的广泛有前途的创新,促进了MEMS的全新3D设计和制造范式,这为机器人、航空航天和医学等重要领域的未来研究和应用带来了巨大的希望。
材料和方法
3D打印MEMS加速度计的制造
MEMS加速度计结构是使用Nanoscribe Photonic Professional GT2工具(Nanoscribe GmbH,德国)通过双光子聚合3D打印的。因此,负性光刻胶IP-S(Nanoscribe Gmbh,德国)与浸入式激光光刻印刷模式结合使用。印刷基板是镀铟锡氧化物玻璃基板。使用 ×25/NA 0.8 物镜(Carl Zeiss AG,德国)以 50 mW 的激光功率进行打印,扫描速度为 100 mm/s,切片和影线距离分别为 1 和 0.5 μm(参见补充信息,第 S2 节)。对于打印,加速度计结构由几个拼接在一起的打印块定义。一些块以“实体”打印模式打印,而另一些块则以“外壳和脚手架”打印模式打印。在固体模式下,激光扫描整个打印体积,而在外壳和支架模式下,激光仅扫描体积的外壳和体积内部的支撑支架。壳牌和脚手架打印模式比实体打印模式快得多,但它的分辨率较低。大型支撑柱是使用外壳和脚手架打印模式打印的。电极、电线和自由悬挂元件,即悬臂和打样块,改为使用固体打印模式进行打印,以确保最高的打印质量(补充信息,图 S3)。打印文件是使用 Describe 软件(Describe 2.5.5,Nanoscribe GmbH,Germany)生成的。首先,从同一个 3D CAD 文件 (.stl) 生成两个打印作业文件,每个打印模式(壳和脚手架模式以及实体模式)一个,确保拼接线完美匹配。然后,将这两个文件合并为一个打印作业文件,其中悬臂和质量块从壳体和脚手架文件中删除,并替换为实体文件中的块。
3D打印后,在丙二醇甲醚乙酸酯(PGMEA)中开发结构20分钟,在异丙醇(IPA)中开发5分钟,同时将载玻片保持在垂直位置。然后,将3D打印的结构在室温下在空气中干燥。开发后,使用LED曝光单元将结构暴露在紫外线泛光下5分钟(12 mW / cm 2 @ 365 nm),以交联在壳牌和脚手架打印模式下打印的结构的所有内部体积,因此不会通过激光曝光交联。接下来,在垂直于玻璃基板表面的方向上,使用定向电子束蒸发(Provac PAK 600 涂层系统)在 3D 打印结构的顶面上涂上 10 nm 厚的 Ti 层和 30 nm 厚的 Au 层。同时对三个装置进行涂层,将行星的旋转速度设置为零,并将样品架小心地放置在坩埚上方。用机械轮廓仪测量金属堆的厚度为40±2 nm,而Au湿法蚀刻后测量的Ti厚度为10±1 nm。金属沉积后,通过SEM(FEI Nova 200 Dual Beam,FEI Company Inc.,USA)对成品MEMS加速度计进行检测。
MEMS加速度计的仿真模型
使用 COMSOL ® 软件(COMSOL Multiphysics ® v. 5.6,COMSOL AB,瑞典)中的有限元法 (FEM) 创建了加速度计结构的仿真模型。用于较大体积加速度计结构的四面体网格和用于悬臂和电阻器的二次网格用于在不损失精度的情况下减少较小器件特征中的网格点数量。在用于设计结构的初始模型中,对于固化的IP-S聚合物,使用了5.1 GPa的杨氏模量和1100 kg/m 3 30 的密度。该模型用于估计悬臂的长度和在器件制造之前达到加速度计目标规格所需的证明质量的大小。因此,利用物理模块“结构力学”和“稳态”求解器对悬臂长度和证明质量尺寸进行了参数化扫描分析。为了最大限度地减少计算时间,仅模拟了结构的一半,沿悬臂方向切割,并将边界条件“对称性”应用于横截面。在对打印结构进行初步评估后,在 COMSOL 中创建了一个经过调整的模型 ® ,该模型具有缩短的悬臂 (480 μm) 和调整后的杨氏模量 (5.9 GPa)。将该模型提取的模拟数据与实测数据进行比较。该模型还用于计算形成应变片(Ti 和 Au)的薄堆叠金属膜的电阻变化。因此,Au 的电阻率设置为 52 nΩ*m,这是通过在 3D 打印测试结构上进行的 4 探针片电阻测量提取的,该结构涂有加速度计应变计中使用的相同金属堆栈。在COMSOL ® 模型中,Ti的电阻率为545 nΩ*m,但其电阻率比Au大得多,预计不会对导电产生重大影响。我们在 COMSOL ® 模型中添加了“电流”模块,并对作用在整个结构上的加速度范围为 0.2 × g 至 1 × g 进行了扫描,并乘以 Q 因子来模拟共振时的证明质量和悬臂位移。计算出的薄层金属膜的电阻变化始终低于测量值,这可能是因为 COMSOL ® 模型只考虑了电阻的几何变形。使用该模型,计算了施加在悬臂和金属应变片上的应变及其相对电阻变化。基于此,使用 COMSOL 模型计算出标距系数等于 2,该 ® 模型对应于电阻变化纯几何的 Ti/Au 堆栈的预期标距系数,而不是我们在加速度计中测量的实际标距系数 3.5。
为了估计设备沿 x 轴和 y 轴的加速度分量的交叉响应,我们使用了 COMSOL® 模型,并计算了沿 y 轴(垂直于悬臂)和 x 轴(平行于悬臂)的交叉响应分别为 1.5% 和 22%。沿 y 轴的加速度会引起质量的旋转,从而引起两个悬臂的相反弯曲,从而导致相反的阻力变化。因此,通过在惠斯通电桥配置中适当布置两个电阻器,可以进一步减少 y 轴加速度对 z 轴测量的影响。沿 x 轴的加速度会引起类似于 z 轴加速度引起的质量旋转。通过实施加速度计设计,将悬臂的中性轴与证明质量的中心对齐,可以最大限度地减少这种加速度的影响(图 S8.1,补充信息)。通过这种方式,由于 x 轴加速度引起的证明质量旋转被最小化。我们的模拟表明,这可以将沿 x 轴的交叉灵敏度降低到 0.3%,而不会影响沿 z 轴的响应度(参见补充信息,第 S8 节)。为了证明这种设计是可以制造的,我们实施并3D打印了精细的加速度计结构(图S8.2,补充信息)。
加速度计的表征
测量装置包括一个压电振动器(TA0505D024,Thorlabs,美国)、一个锁相放大器(H2FLI 50 MHz,Zurich Instruments,瑞士)和一个激光多普勒测振仪(OFV-551,Polytec,德国)和控制器(OFV-5000,Polytec,德国),如图5a所示。为了校准,用激光多普勒测振仪测量压电振动器对电刺激的机械响应。首先,将3D打印的MEMS加速度计与使用双面胶带打印的载玻片一起安装在压电振动器上。然后,表征了压电振动器为加速度计提供的机械驱动。激光多普勒测振仪测量加速度计支撑柱顶面的振荡速度,加速度可以通过将其乘以角频率来计算。压电振动器驱动频率扫描在1.4至2 kHz之间,电压幅度范围为1至7 V rms 。压电振动器机械振动的频率和振幅由驱动信号的频率和振幅决定。对每个加速度计重复此表征:(1)在将每个加速度计设备安装到压电振动器上后,以及(2)在加速度计设备的稳定性测量完成后。图5b显示了施加到每个加速度计上的平均加速度与驱动电压在其特定谐振频率下的幅度的一致线性行为。压电振动器可产生高达0.9 × g(8.8 m/s 2 )的加速度。我们观察到不同设备之间施加的加速度变化最大为 20%,但每个设备的最大变化仅为 8%。这一观察表明,双面胶带的耦合效率可能与安装过程有关,并影响施加的加速度。然而,在支撑柱的顶面上而不是在压电振动台表面上进行校准,使我们能够将加速度计的机械和电气响应与直接施加在悬臂连接处的机械刺激进行比较,从而避免了双面胶带对设备计算响应度的任何影响。在对压电振动器进行表征后,加速度计的探测电极与探头接触,从而与测量装置电连接。锁相放大器产生驱动压电振动器的正弦信号和施加到加速度计应变片传感器的正弦信号。压电振动器以与校准期间相同的频率扫描和电压驱动。同时,施加到应变片传感器的信号在4至4.6 kHz的频率范围内进行扫描。该正弦信号与电阻变化(也是正弦波)相乘,在两个新频率下产生信号,分别位于原始信号的加法和减法处:在我们的例子中,分别为 2.6 和 5.4 kHz。在下混频(2.6 kHz)下解调信号会产生与传感器电阻变化成正比的电压分量。
图5:测量设置和压电振动器校准。
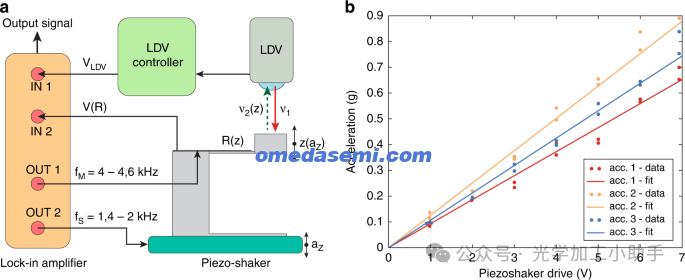
a 用于测量 3D 打印 MEMS 加速度计响应度的设置示意图。锁相放大器用于驱动压电振动器,通过缩混从电阻器中提取信号,并解调激光多普勒测振仪信号。b 压电振动器施加的加速度是用三个装置支撑柱顶部的激光多普勒测振仪在1.775 kHz频率下在不同的驱动电压下测量的。图中显示了相应的线性拟合。可以看到不同设备之间的变化约为 ±10%。
本文引自“Micro 3D printing of a functional MEMS accelerometer”