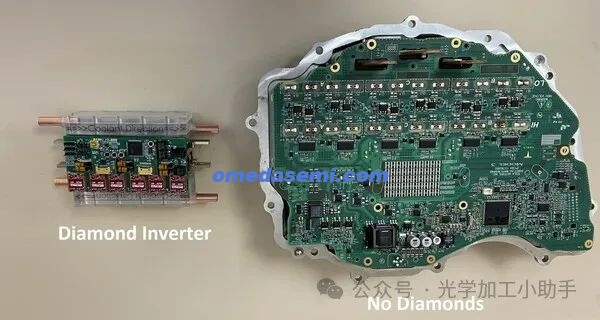
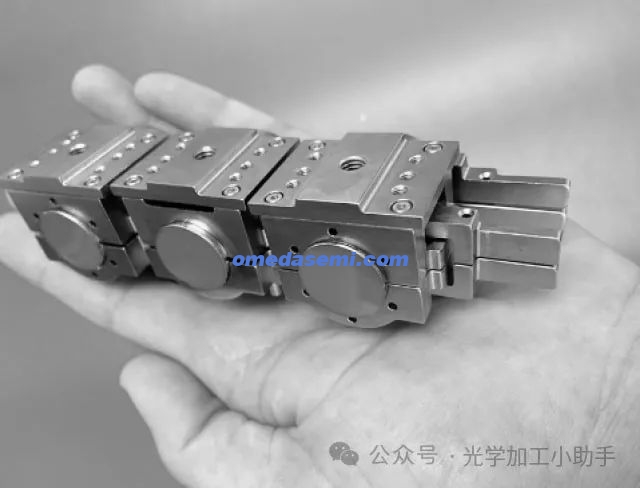
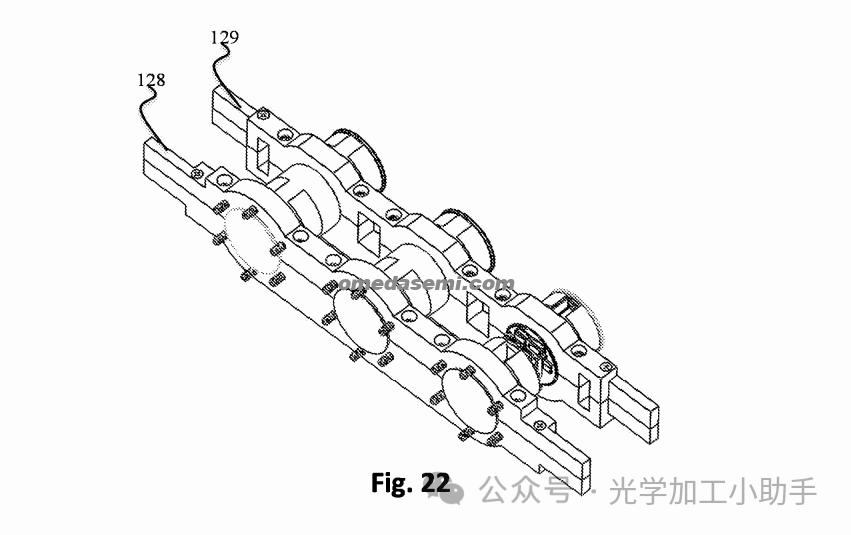
😀有没有觉得左边的图跟右边的产品长得有点像😎
相信大家对这个照片一定还有一定的印象,左边是diamond foundry的汽车电源逆变器,右边是特斯拉的电源逆变器,diamondfoundry的逆变器的核心创新点在于使用了创新的金刚石晶圆材质,本文小编将和大家分享一下diamondfoundry的英仙座逆变器,基于单晶金刚石晶圆的汽车电源逆变器设计。
让我们顺着作者的思路,了解他的设计。干货比较硬,更适合功率半导体行业的技术人员阅读。
如果你也爱好 金刚石,半导体,光学,光纤,硅光集成等技术及应用,可以添加小编,一起畅聊技术,市场和应用。
免费获取原文,请联系小编,如果您有关于金刚石的需求和问题,也请和小编沟通
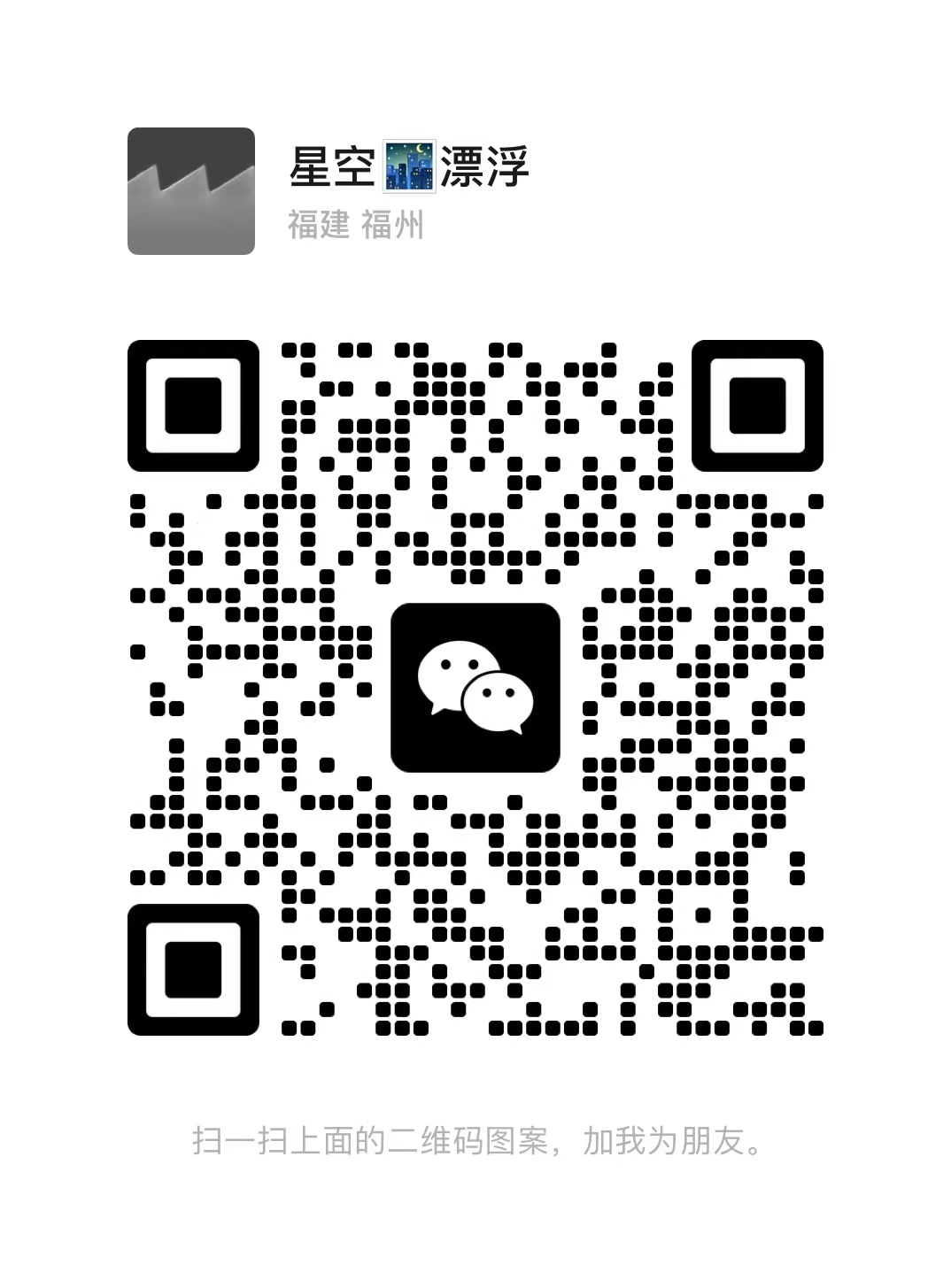
摘要
功率器件电子系统包括热管理配置,其中电力电子芯片连接到铜基板上,单晶金刚石基板连接到铜基板上。铜衬底夹在金刚石衬底的第一面和电力电子芯片之间。
背景
提高电动汽车电力电子系统的能源效率
绝大多数功率逆变器架构包括将来自电池的直流电压转换为与电力牵引电机兼容的三相交流格式。如今,功率转换范围为 50 至 250 kW(峰值 400 kW),具体取决于型号。未来几年将看到MW系统(卡车运输业,海上运输,更重要的是空中电动汽车)的出现。每相需要两个安装在所谓的“半桥”拓扑中的电源开关。在运行过程中,由于三相以 120 度角移位,因此始终有两个开关同时闭合 (ON),其他四个开关断开 (OFF)。
为了评估逆变器的效率,导通损耗的计算方法是:开关闭合时的电压差乘以流入开关的电流,当然再乘以6(3×2=6个开关)。产生的功率损耗水平很高,设计人员一直试图降低功率损耗以增加行驶里程或减小电池尺寸。在设计功率牵引逆变器时,其他一些考虑因素,如引线键合应力和容量、栅极驱动器性能以及整体系统尺寸和成本,也是等式的一部分。最终,到目前为止,降低功率损耗的经验法则是“使用更多的硅表面积或使用更好的散热器”。这两个“建议”都有很大的缺点。由于“ON”状态电流在更多的开关之间共享,因此考虑使用更多的硅开关确实降低了功率传导损耗,从而降低了功耗,但开关损耗也会相应增加,尤其是对于IGBT。缺点是要使用的指数表面连接、电源路径中薄弱环节(如引线键合)的成倍增加、芯片之间的差异、导致有害寄生电感的物理距离扩展以及难以将每个芯片与其配套芯片完美同步,最终以不必要的复杂性和部署工作效率低下而告终。成本考虑已经完成,以证明这一学说是错误的。
另一方面,冷却策略多年来一直是实验和研发研究的兴趣所在。设计人员不仅关注芯片改进,还认为降低芯片的工作温度可能是提高电源效率、降低成本和提高可靠性的途径。尽管这种直觉当然是正确的,但如今确保令人满意的结果的可用材料是迄今为止无法获得的。
由于功率硅的电路径和热路径是相同的,并且都具有相当大的规模,因此从字面上断开它们以将热路径引导到出于安全原因需要电气隔离的液体冷却剂以及需要尽可能短且有弹性的电气路径是极具挑战性的。这种断开机制(“电介质”)是通过图1A-1C所示的技术和工艺实现的,这些技术和技术在过去四十年中并没有真正显着发展,尽管被广泛采用,但结果很差。
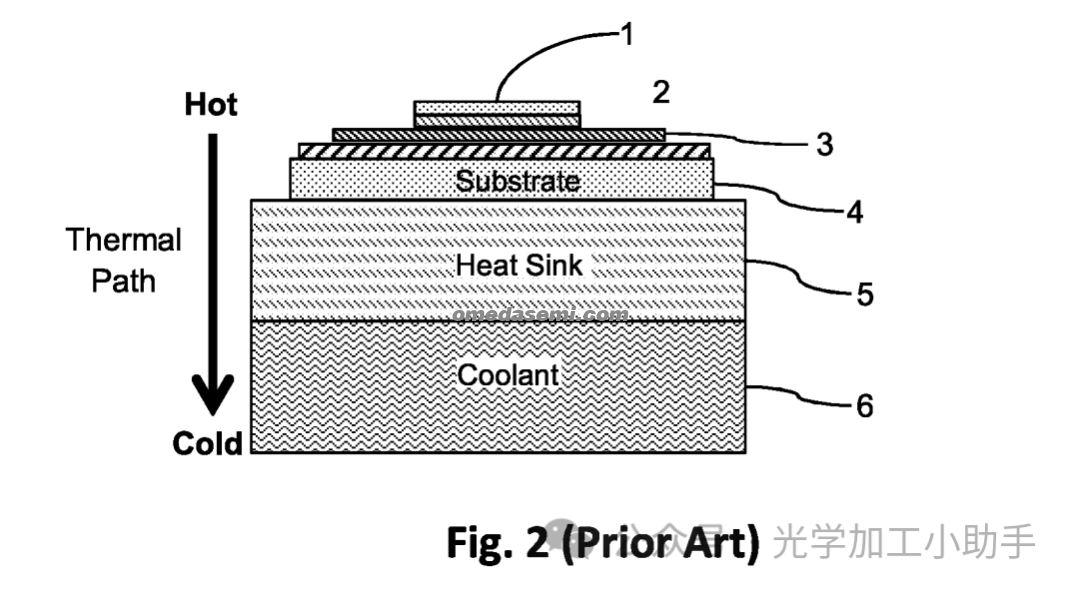
图2描绘了功率器件的通用架构。通常,该器件包括一个硅芯片1,该芯片通过附件2连接到铜布局3,铜布局通过基板4和介电材料5与冷却剂6热耦合。电流主要在铜布局3中横向流动,但主要从芯片1垂直流过附件2、布局3、基板4和电介质5。这种结构的特点是在硅芯片1和冷却剂6之间的热路径中,二维矢量热传播相对较差。例如,如果冷却剂6的温度约为80°C,则由于热路径中的热阻,芯片1的温度通常为175-200°C。图2的常见架构可以通过图3A所示的简化热阻Rth模型进行分解,并总结在图3、B所示的表格中。
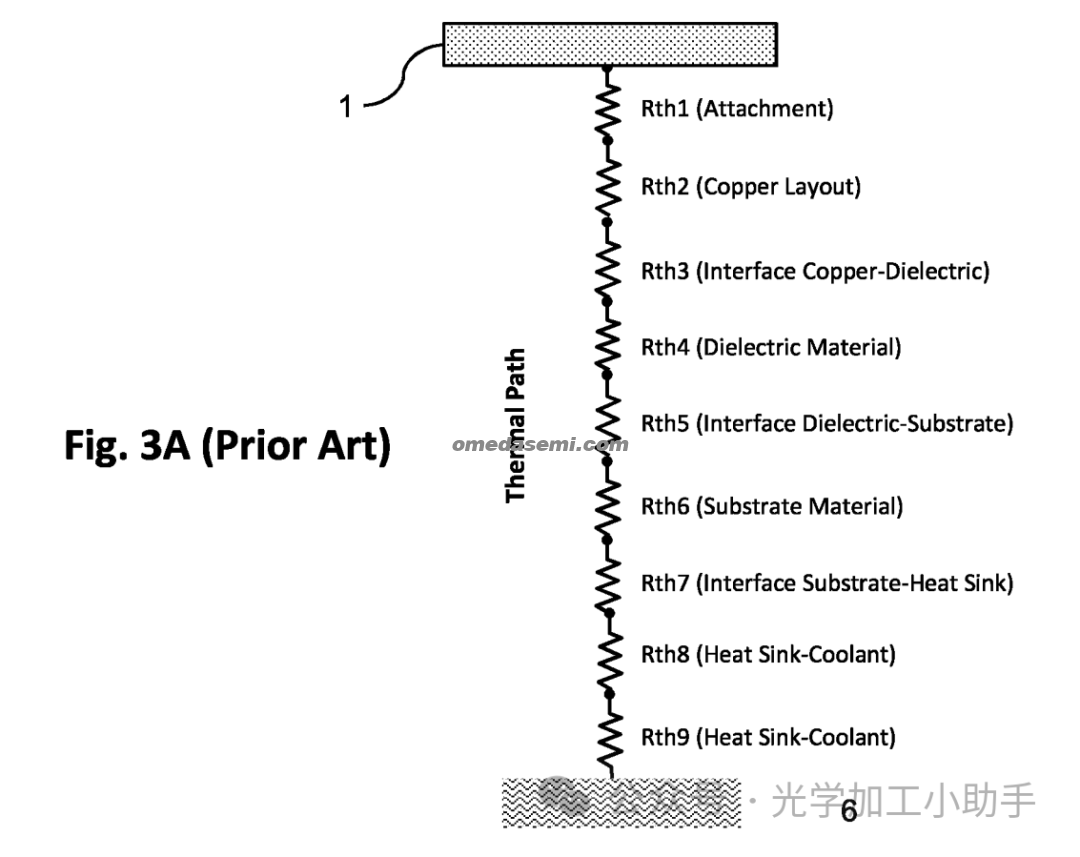
图 3 显示芯片 1 和冷却剂 6 之间的热阻 (Rth) 分为 3 大类:
1)介电材料5(Rth4):介电材料具有广泛的性能和特性,必须确保最佳导热性,以达到4 kV量级的汽车隔离要求,持续1分钟,因此决定了材料厚度Rth。
2) 基板和机电一体化(Rth2、Rth6、Rth8):基板具有机械坚固性和芯片安装性,以及外露表面,确保通过逆变器系统(机电一体化)冷却液的热连续性。
3) 面连接点是安装在一起的不同元件的连接点,可分为 3 大类:
a) 焊接或烧结扩散 (Rth1),根据所使用的材料、界面厚度和导热性提供最佳导热性。
b) 陶瓷在金属上的沉积涂层(例如,Al 2 O 3 火焰喷涂涂层),根据孔隙率和渗透率,诱导出具有自身Rth(Rth3,Rth5)的材料间界面;
c) 压力接触 (Rth7),其中 2 个表面压在一起以形成热路径(通常也是电路径)。这种类型的界面高度依赖于施加的压力、共面性、粗糙度和表面的几何形状。它通常性能较差,并随着时间的推移而退化。
虽然不直观,但液与固表面接触 (Rth8) 属于这一类别,但根据所采用的策略,它更稳定,质量/性能更好。平面上的层流效率降低,因为只有冷却剂表面与固体接触的少数分子会携带要提取的卡路里。其余的液体不积极参与冷却。湍流会产生更大的表面接触面积和更多的载流子,但需要实施一种特殊的机制,从而导致材料和系统体积的增加(即薄翅片)的更大使用。如上所示,总 Rth 与冷却液的结更像是材料特性、技术和表面积的集合,而不是单一维度问题。有很大的进展余地。
详细说明
Diamond Foundry 的新型单晶金刚石晶圆的出现以及现已证明的体积扩展和成本降低使电动汽车电力电子技术取得了重大进步,将行驶里程提高了 5.3%,使用寿命远远超过 300,000 英里。
电动汽车 (EV) 电力电子设备的散热越来越受限,电子架构的潜在范围也受到可用材料的限制。功率半导体开关中引起的热应力对半导体和逆变器公司来说是一个艰难的要求,直到绝望。整个行业的工程师在他们的电子设计中使用的材料一直无法真正满足推进电动汽车电力电子设备所需的特性,特别是包括将极端导热性与极端电压绝缘相结合的材料。
单晶金刚石 (SCD) 是一种最极端的材料——在多个维度上,每个维度都有一个决定性因素——特别是它结合了极端的导热性和极端的电绝缘性。SCD 具有出色的介电性能,包括 5.7 的低介电常数、35 GHz 时低于 0.0001 的损耗角正切和 MV/cm 的高介电强度。这意味着 20 um 的 SCD 可以绝缘 20 kV,同时提供高达 3,000 W/mK 的导热系数。
位于加利福尼亚州南旧金山的 Diamond Foundry, Inc. 已实现晶圆尺寸的单晶金刚石生产,涵盖了所有商业相关计算机和电力电子芯片所需的芯片尺寸。
电力牵引逆变器的困境
电动汽车的动力牵引逆变器(PTI)是电动汽车的关键元件。由于其复杂性、电气和热应力以及最终成本,PTI 一直是电动汽车实施中最薄弱的环节之一,在这个新兴市场的早期发展中存在显着的失败,当然也是 OEM 采用的技术入门壁垒。驾驶条件和风格通常会对逆变器的有源组件及其周围元件产生巨大的电气和热应力,如果处理不当,会导致寿命急剧缩短,最终导致系统故障。
由于定制子系统要求、大功率电子、材料科学、机电一体化和热管理的复杂集成加剧了复杂的设计和制造,功率逆变器的发展一直缓慢且渐进。功率密度无疑是现代功率逆变器性能的关键指标,强调技术和效率。作为参考,最先进的设计表现出 33 kW/L(特斯拉 Model 3 为 12 L,4.8 kg,400 kW)和 36 kW/L(奥迪 e-Tron 为 5.5 L,8 kg,200 kW)。
功率半导体主要由两个因素驱动:导热性(冷却它们的路径)和导电性(承载大电流的路径)。尽管电气路径已经研究多年,并取得了或多或少的成功,但热路径一直是主要挑战。
除了需要高导热性和导电性外,功率半导体还需要与环境的其他部分电气隔离,因为它们承载高电压;这是一项安全要求。不幸的是,电压隔离栅(如DBC基板)通常表现出较差的导热性。常见的隔离栅,如高导热化合物表现出 2 到 5 W/mK,最先进的氧化物,如氧化铝 (Al 2 O 3 ) 显示出 24 到 28 W/mK,更现代的氮化铝 (AlN) 实际上提供 150 到 180 W/mK,因此在确保电气隔离所需的厚度上,半导体结温 (Tj) 和冷却机制(通常是液态乙二醇)之间保持了相当大的不希望的热差。
与MCU、逻辑、存储器和DSP芯片等其他耗散器件不同,硅绝缘栅双极晶体管(Si IGBT)和碳化硅金属氧化物半导体场效应晶体管(SiC MOSFET)等功率半导体在其底部具有相同的电气和热路径。当今确保Si IGBT和SiC MOSFET的电气绝缘和高载流能力的最常见解决方案是直接键合铜(DBC)基板。不幸的是,它们不能提供高载热能力。
金刚石基电力电子
由于其卓越的性能,金刚石和金刚石基解决方案一直是功率半导体开发人员的广泛应用。有人称其为半导体应用的“圣杯”。这是自然界中唯一已知的具有超高导热性和超高带隙的材料。与导电的石墨烯(碳的另一种同素异形体)不同,金刚石是一种优质的隔离器。Diamond Foundry 现在为一个非常古老的问题提供了一个实用且成本合理的解决方案:如何有效地实现功率半导体的冷却路径,同时确保介电隔离。
钻石的优点早已广为人知,事实上,这并不令人惊讶或新奇。新的和颠覆性的是,Diamond Foundry现在已经成功地生产了适用于所有芯片芯片尺寸的高质量单晶金刚石晶圆;b. 将成本降低到汽车电力电子所需的水平;c.充分利用新型金刚石晶圆功能的新型电力电子架构。
我们团队以及其他团队先前的研究表明,金刚石可将各种半导体的峰值温度降低多达 20%,在此期间,这种降低可将功率效率提高 10%。
SCD晶圆可以通过多种方式在开关半导体器件结点附近使用:替代直接键合铜(DBC)衬底中的陶瓷(例如氧化铝(Al 2 O 3 )、氮化铝(AlN)、氮化硅(Si 3 N 4 ));更换新型分立式封装中的散热器;允许使半导体晶圆变薄。SCD晶圆允许基于任何和所有半导体技术的逆变器尺寸、重量和成本降低,而不需要“押注”一种获得商业牵引力的新型半导体形式。
保持较低结温的重要性
功率半导体开关中产生的热应力会导致故障和能效损失。根据一般经验,温度每升高10°C,半导体的预期寿命就会缩短一半,例如,碳化硅功率开关的耐高温硅设计从175°C降至200°C。与具有几乎恒定的V-温度系数的IGBT不同,MOSFET(包括SiC)的 ce(sat) RdsON是一个正的温度依赖参数(TDP),这意味着RdsON会随着温度的增加而增加。
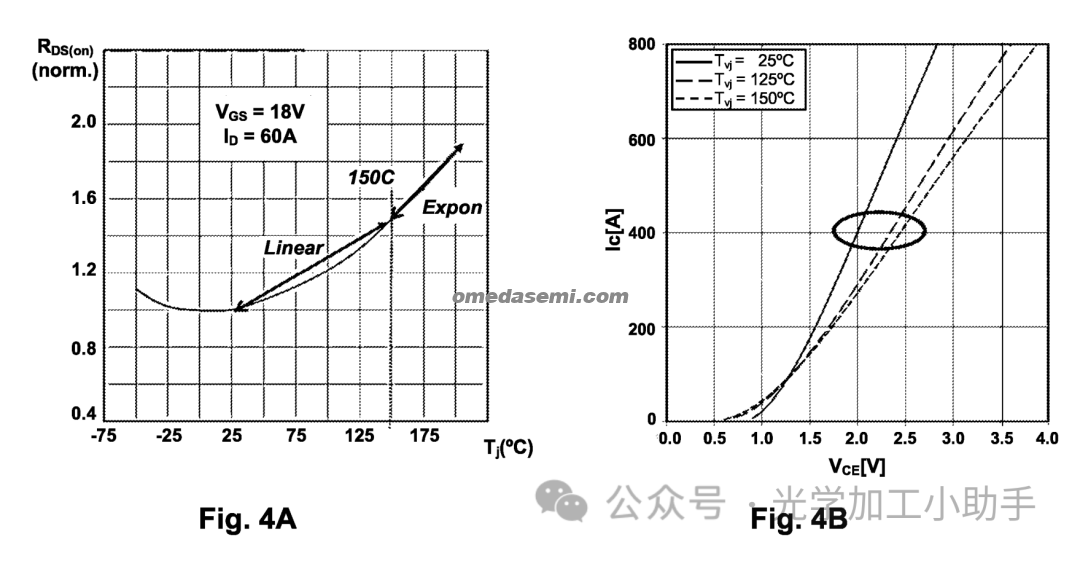
图4A示出了普通SiC器件的归一化RdsON。由于典型的 RdsON 在 25 C 时指定为 1(例如,7 mOhm),因此它在 150 C 时增加 45% (10.39 mOhm),在 175 C 时增加 64% (11.64 mOhm),在 200 C 时增加 90% (12.87 mOh)。RdsON 与 Tj 的增长分为线性(25 至 150 C)和指数区域(150 至 200 C),这意味着对于相同数量的电流 (400 A),功率传导损耗在 25 C 时为 1120 W,在 100 C 时为 1359 W,在 150 C 时为 1662 W,在 175 C 时为 1863 W,在 200 C 时为 2060 W。
图4B显示了典型现代IGBT的V ce(sat) 。400 A 时的传导损耗在 25 C 时为 800 W,在 125 C 时为 920 W,在 150 C 时为 1000 W(没有进一步的数据)。在EV的逆变器频率工作(15 kHz)下,导通损耗约占器件累积导通开关损耗的60%。这主要是由于IGBT的所谓“尾部效应”,它与硅芯片的表面积直接相关。表面越大,开关损耗越大。IGBT的总累积导通和开关损耗在25°C时为1375 W,125°C时为1580 W,150°C时为1720 W。值得注意的是,尽管与 SiC 相比,SiC 与 IGBT 相比效率优势非常小,但即使是 SiC 与 IGBT 的主要成本(约 5×),SiC 的采用趋势也是不可逆转的,这突显出实现成本被削弱,有利于性能和电动汽车的续航里程增益。
由于车载EV的冷却液温度设置为80°C,因此这里的挑战是使Tj尽可能接近冷却液,以消除Tj在指数区域和部分线性区域(对于SiC)引起的不必要的传导损耗,并允许减少IGBT的芯片表面积。IGBT等双极性结构在正向电流方面具有相当强的弹性,只要不触发温度依赖性闩锁条件。人们普遍认为,高达1000 A/cm2的电流密度设定了限值,IGBT制造商在温度范围内通常保持在该限值的80%至90%。在闩锁条件下控制IGBT的结温,可以大幅减小芯片有效面积,从而成比例地影响IGBT自诞生以来一直遭受的开关损耗。正确应用的热管理解决方案(如金刚石铸造解决方案)可以以 1/5 的成本实现现代 SiC 和古董 IGBT 技术在电动汽车频率开关范围 (10-20 kHz) 中的均衡。
对EV续航里程的具体影响
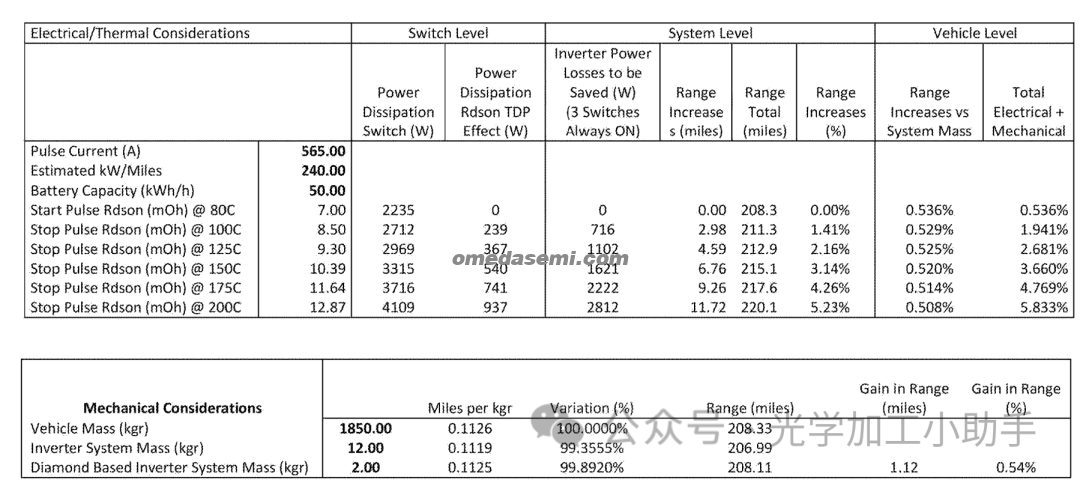
图5总结了根据当今标准转换为标准EV轿车范围的三相250kW逆变器系统的功率传导损耗。研究了 80 C(冷却液)至 200 C Tj 范围内每相电流 400 A(峰值 565 A)诱导损耗。
“要节省的逆变器功率损耗”列显示了在不同 Tj 下要从电池中节省的能量,并根据电池容量相应地计算范围。假设电源开关 Tj 可以保持在冷却液温度 (80 C) 附近,则每次电池充电可节省高达 2812 W 或 11.72 英里或 5.33% 的续航里程。
这项研究是保守的,因为它没有考虑再生节能,估计是这些数字的 15-20%。这包括与IGBT相关的快速恢复二极管(FRD)的功率损耗、温度依赖性损耗、SiC MOSFET本征二极管的热依赖性损耗(其性能与温度的关系较差)以及相关电路(如栅极驱动器和辅助元件)的减少。这种比例的尺寸减小为直接集成逆变电机提供了可能性,消除了电缆长度和端子中的功率损耗,占电池容量的几分之几。
超越温度:为电动汽车电力电子设备实现单一外形架构
结合 Diamond Foundry 现在提供的单晶金刚石晶圆非凡的导热性、电压绝缘性和晶圆表面处理性能,实现了新颖的器件和系统设计以及更高效的组装工艺,这是业界尚未有机会追求的 GaN、SiC 和 IGBT 硅芯片。
特别是,Diamond Foundry 的 SCD 晶圆使单外形功率逆变器能够超过 1000 kW/L(例如,0.4 L 系统的功率为 400 kW)。这带来了更高的系统效率、损耗和系统成本降低,从而转化为节能和电动汽车续航里程的延长。
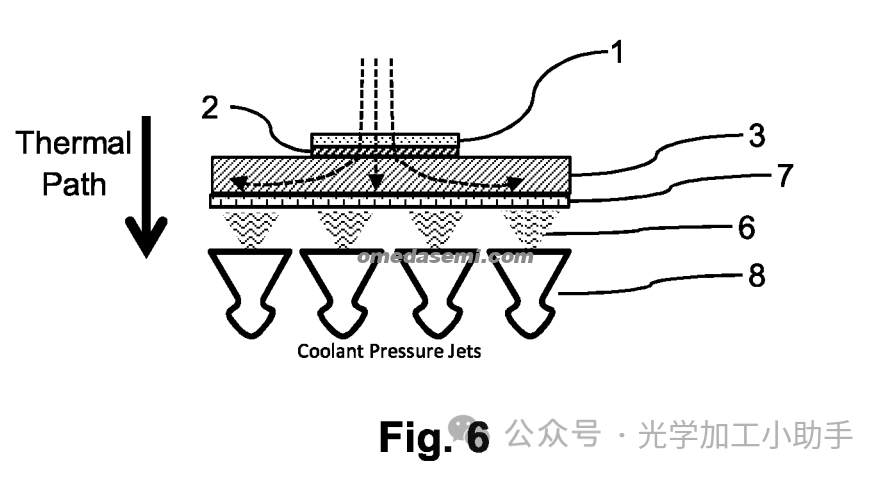
根据本公开的各方面的新颖的热管理结构如图6所示。这种配置将热阻元件从 9 个大幅减少到 4 个。在这种配置中,半导体芯片1通过银附件2连接到铜基板3上。铜基板2扩散键合到SCD晶圆7上。用于在构成热路径的简化元件数量之间附着的扩散过程现在减少到纳米级,确保从半导体芯片 1 通过金刚石芯片 7 到冷却剂 6 的自由热传播。使用 SCD 晶圆 7 可实现更三维的热传播,如虚线箭头所示。
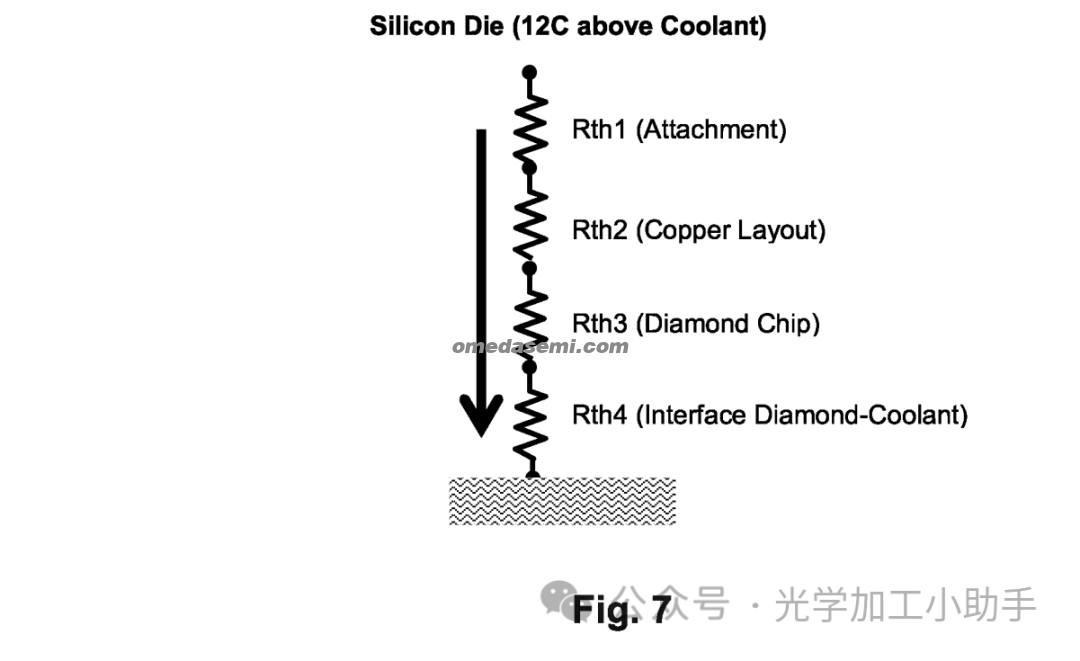
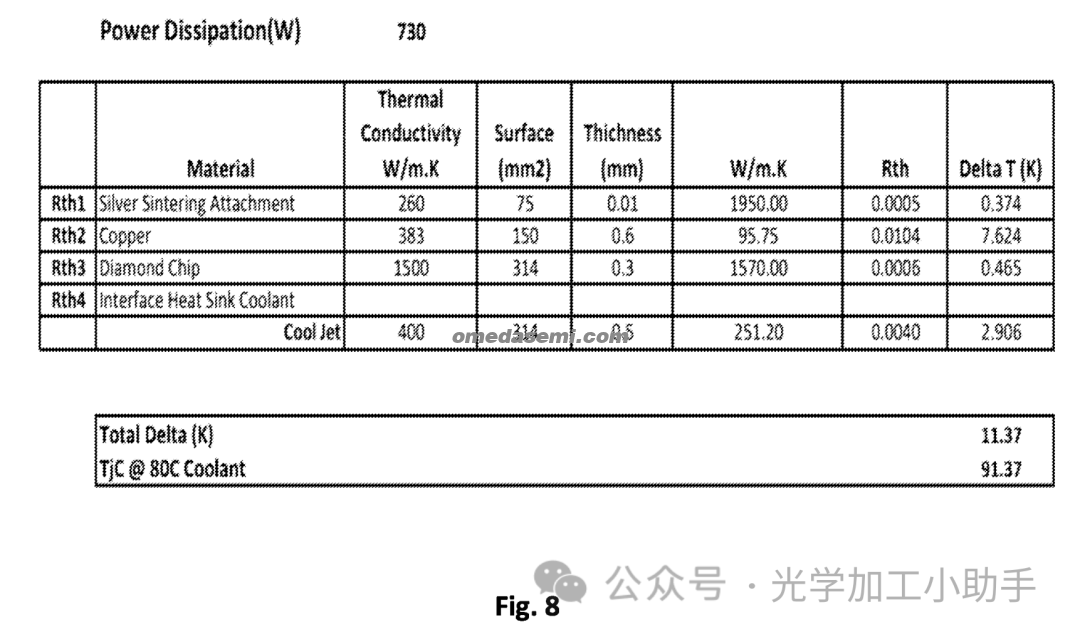
一个或多个加压冷却液射流8将冷却液6输送到金刚石晶圆7的暴露表面,提供垂直冲击流,比层流、湍流或湍流“薄翅片”解决方案具有更高的性能。图7中描绘的相应热阻模型和图8中描绘的表和图8总结了这些优点。
由于总 Rth 的显着降低(比现有技术 ̃0.11 降低 0.0155),硅芯片 Tj 现在与锁定位置的冷却剂温度密切相关,在冷却剂上方约 12 C 处产生一个 Tj“钳位”,与图 5 中描述的相比,可以显着节省传导损耗, 优化逆变器设计的机械几何形状,并减少所需的有源硅芯片表面。
如图 6 所示的先进材料和热管理技术可大幅降低热阻和减小逆变器尺寸,为大幅延长电动汽车的续航里程、降低成本和极致的可靠性铺平道路。此外,该技术具有可扩展性,可适应对高功率效率和可靠性至关重要的类似市场(即发电、充电站、电网平衡等)。
400 kW 功率逆变器设计介绍:
1) 单开关说明
在本例中,单开关结构从19.5×0.6 mm镀银(Ag)铜顶部基板102连接到20×0.3 mm SCD芯片104开始。接下来,如图10所示,将三个晶体管(例如IGBT或MOSFET)连接到顶部基板上,例如,使用Ag烧结技术。
作为示例,而不是作为限制,MOSFET106可以是在8×8 mm硅芯片上形成的130 A 1200V碳化硅(SiC)MOSFET器件。接下来,如图11所示,三个导电支柱结构108用于MOSFET的大电流电源路径(V L转换器)的漏极连接被连接到顶部基板上。作为示例,而非作为限制,支柱结构可以是6毫米宽的镀银铜柱。接下来,如图12所示,将导电的(例如铜)夹子110安装在三个SiC MOSFET的顶部,并烧结形成用于MOSFET源极连接的高电流电源路径。
如图13所示,夹子被安装并连接到MOSFET的源极焊盘连接上,例如,使用烧结技术。与MOSFET106的电气连接可以通过将MOSFET上的顶垫112烧结到夹子110上的相应突起114来实现,如图14所示。安装薄柔性印刷电路板(PCB)116以形成用于MOSFET栅极连接118的栅极路由器,如图15所示。PCB116上的导电延伸120与栅极连接118电连接,例如,通过引线键合122,如图16所示。薄型柔性PCB栅极驱动器电路124和电流检测电路126被添加并与栅极路由器116互连,如图17所示。该器件的等效原理图如图18所示。
随后,图17所示类型的两种相同结构可以背靠背排列,将SCD芯片104朝外对齐,如图19所示,然后将环氧树脂127复合,如图20所示。图20所示的环氧树脂器件可用于半桥逆变器或用于单向电机控制a,即所谓的半H桥。设备每侧的源110可以反并联连接。该器件的每一侧也可以与二极管并联,以分流反向电流。半桥器件也可以集成到使用同步整流器的开关模式电源中。
两个半桥逆变器器件可以布置在一起,形成一个完整的H桥,用于电机控制或作为电源转换器,如AC-AC转换器、DC-DC转换器或DC-AC转换器。
三个半桥器件可以并联排列,如下图21所示,以构成三相逆变器装置。每个器件都与位于每个半桥器件两侧的源区域之间的栅极控件对齐。这种平行布置允许在每个半桥器件之间形成短距离刚性连接。如图22所示,图21所示类型的三个半桥器件可以经由母线128、129进行刚性连接。对于三相逆变器装置,可以连接三个半桥器件128的一侧的漏极,并且可以连接每个半桥装置的另一侧的电源129。脊母线128可以构成三相电源逆变器的VBUS(+)母线,脊母线129可以形成三相电源逆变器的VBUS(−)母线。母线在半桥设备之间提供电气连接和结构刚度。
单晶金刚石芯片 (SCD) 104 允许对每个半桥器件中的 MOSFET 进行有效冷却。冷却块130可以耦合到三相逆变装置的每一侧,如图22所示。每个半桥装置可以包括用于辐射冷却的散热片或用于液体或蒸发冷却的流体界面。冷却块130可以实现为冷却喷射冷却液块,以提供冷却液和SCD表面之间的热传导。如图24所示的冷却喷射冷却液块利用文丘里效应将冷却液喷射到SCD表面上,从而在冷却液和SCD之间产生高流速和大量接触。如图所示,冷却液在冷却进气口131处进入冷却块130。冷却液充满冷却液进气腔132,到达压缩室133。冷却液通过文丘里管134的速度增加,并沿着钟形喷嘴135的表面扩散,形成冷却液射流羽流,撞击SCD104。冷却液射流羽流可被引导到 SCD104 的MOSFET106下区域。冷却液分散在 SCD104 上,将热量从MOSFET106和 SCD104 带走。热冷却液通过回油腔136向上循环,在那里它可能会离开冷却块130,并且可以在返回冷却液进气口131之前进行冷却。冷却液可以通过散热器和翅片块的膨胀和辐射冷却来冷却。
冷却块130可以包括多个罩式喷嘴135,例如且不限于,每个MOSFET106一个。如前所述,每个喷嘴135可以位于其中一个MOSFET的正后方,并将冷却液的射流引导到MOSFET正后方的SCD104上。冷却液 O 形圈密封件 137 可防止冷却液从 SCD104 周围逸出。
下面图26的前视图描绘了面向三相逆变器安装的冷却块侧面的视图。如图所示,冷却块可以包括三个钟罩喷嘴135,每个喷嘴被配置在半桥器件的三个MOSFET之一的后面。回流腔136可以位于钟形喷嘴135之间的空间中。图27示出了根据本公开的各方面所述的冷却块的回流侧的剖面图。如图所示,该冷却液块包括三个喷嘴组件139,它们耦合在一起以冷却三相逆变器。根据本公开的方面,冷却剂块可以包括足以冷却逆变器装置的任意数量的喷嘴组件,包括半桥装置。每个相应的半桥装置的一侧都有一个回油腔136,并且每个回油路径都连接在一起,允许冷却液流向冷却液出口138。
图28示出了利用两个冷却液块的三相逆变器,其中三个冷却液块安装在三相功率逆变器的每一侧,并配置为冷却三相逆变器中三个半桥器件中每个装置的一侧。图29描绘了一个完整的三相逆变器组件,其中安装了电机相电源连杆140。电机相电源联动器140连接每个半桥器件的漏极和源极,使得电流仅在半桥器件的一侧处于导通状态时才流动。图30描绘了安装在三相逆变器上的两个冷却液块,该逆变器具有与电机相电源连杆140耦合的电机相紧固件141。图31示出了集成的大容量电容器和其它无源电路142,它们可以耦合到与电机相紧固件141相对的一侧的三相逆变器。
图32描绘了根据本公开的各个方面完成的带冷却块的三相逆变器的自上而下的视图。如图所示,所述三相逆变器包括电机相紧固件141、母线129、128,冷却块130包括冷却液入口131和冷却液出口138。图33示出了根据本公开的各方面完成的带冷却块的三相逆变器的侧视图。在侧视图中,还可以看到电机相电源联动器140、半桥器件143和无源电路142。
根据本公开的附加方面,三相逆变器装置可以集成到电动汽车中,例如电动汽车、飞机、直升机、火车、轮船或潜艇。
图34描绘了一种包括本公开各方面的三相逆变器的简单电动汽车。如图所示,简单的电动汽车可以包括三相逆变器和冷却液块组件201耦合到三相电动机202。电动机202的每一相可以导电耦合到三相逆变器201的电动机相紧固件上。电动机202的输出轴可以耦合到差速器(和任选的齿轮箱)203,该差速器被配置成将转速施加到连接驱动轮205的轴204上。三相逆变器从电池或其他电源206获取直流(DC)电力,并将其转换为三相功率,电动机202可以将三相功率转换为其输出轴的转速。控制器208可以耦合到三相逆变器,并被配置成控制相位以操作电动机。电池或其它电源206可以从充电电路207接收电力,充电电路207可以接收来自外部电源的电力,例如来自墙上插座的交流电。充电电路207可以是例如AC-DC转换器,并且可以利用本公开中描述的半桥器件。三相逆变器的冷却液块可以耦合到包括散热器209和冷却液泵210的冷却液系统。为了稳定性,电动汽车还可以包括额外的车轮211。
图35描绘了简单的直接驱动电动汽车,例如电动摩托车。与图34中描绘的电动汽车不同,直驱电动汽车省略了差速器,取而代之的是电动机202直接驱动驱动轮205。根据本公开的方面,直接驱动的电动汽车可以包括用于每个驱动轮205的电动机202和三相逆变器201。根据本公开的各方面,直接驱动车辆可以包括具有相应电动机和逆变器的任意数量的驱动轮。根据本公开的一些附加方面,多个电动机可以耦合到一个三相逆变器。
图36示出了直接驱动电动汽车的替代实施例。在所示的车辆中,三相逆变器201驱动,电动机202连接到推进器、液体螺杆或其它装置,用于通过液体220产生推力。该实施例可以实现许多车辆,如飞机、轮船、潜艇、直升机、四轴飞行器等。在某些实现中,多个电动机202和逆变器201可以包括在同一冷却剂回路上,并共享一个散热器209和冷却剂泵210。
附图简介
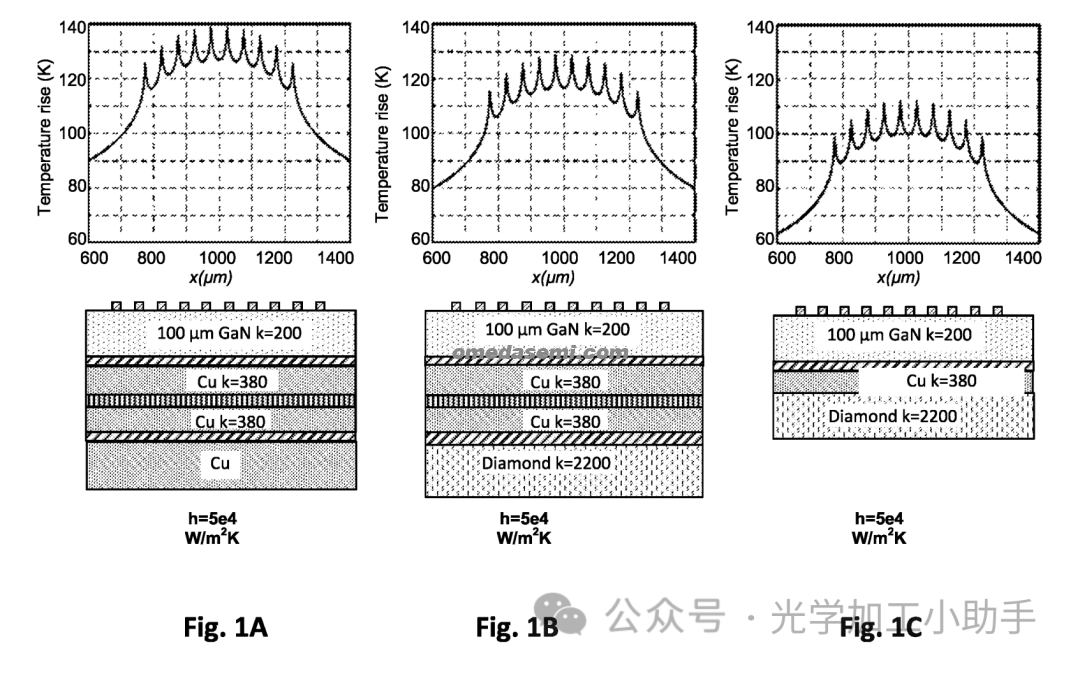
图1A-1C描绘了不同晶圆类型的热分布图和侧面原理图,显示了在现有技术实现中将金刚石添加到电力电子器件中的一般影响。
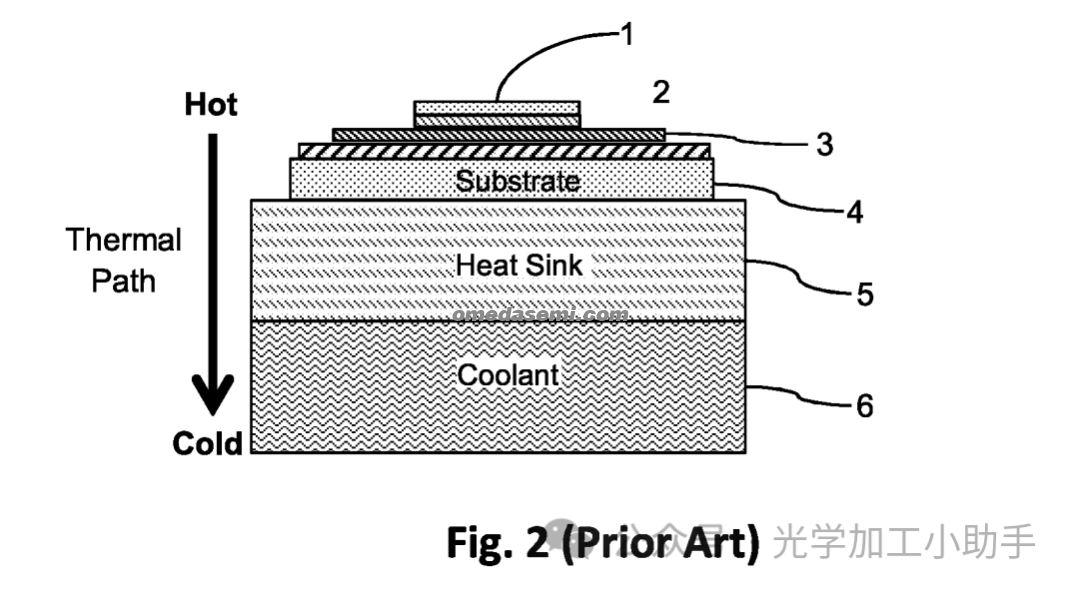
图2描绘了现有技术中功率器件中电/热路径的横截面图。
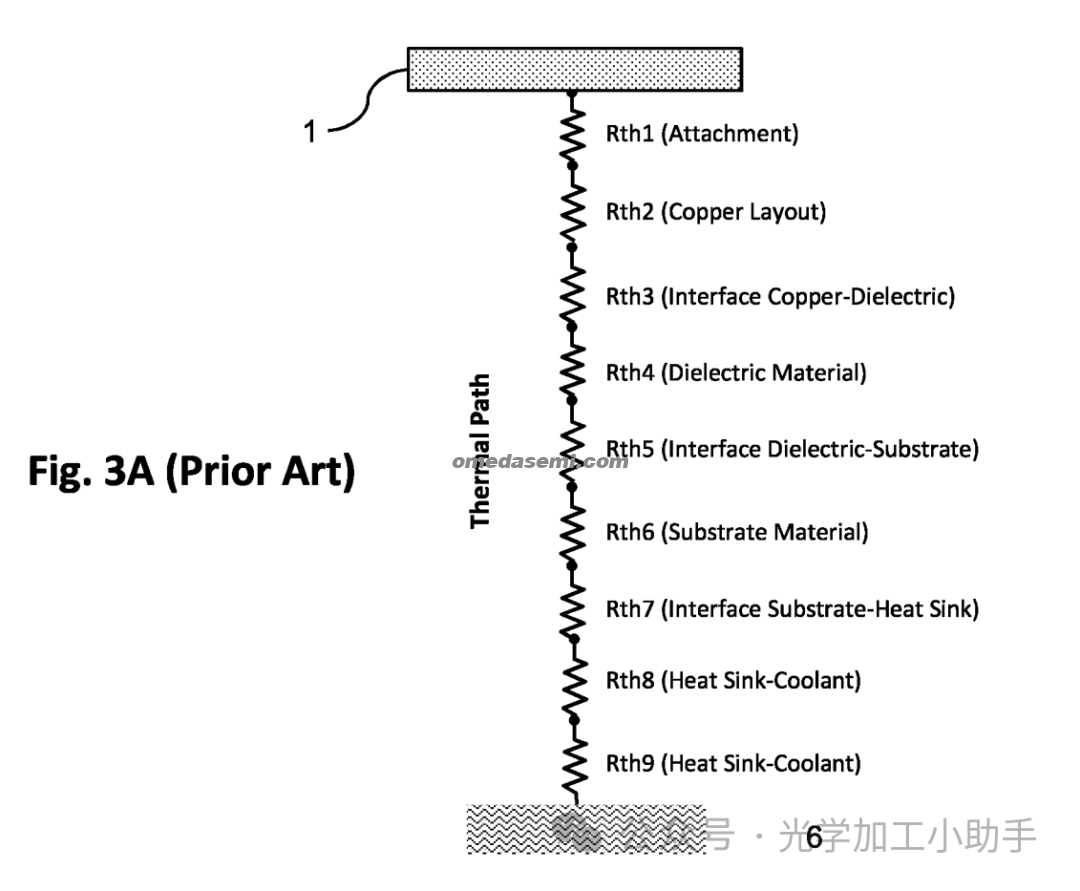
图3A是现有技术中功率器件中电/热路径的热阻Rth模型表示。
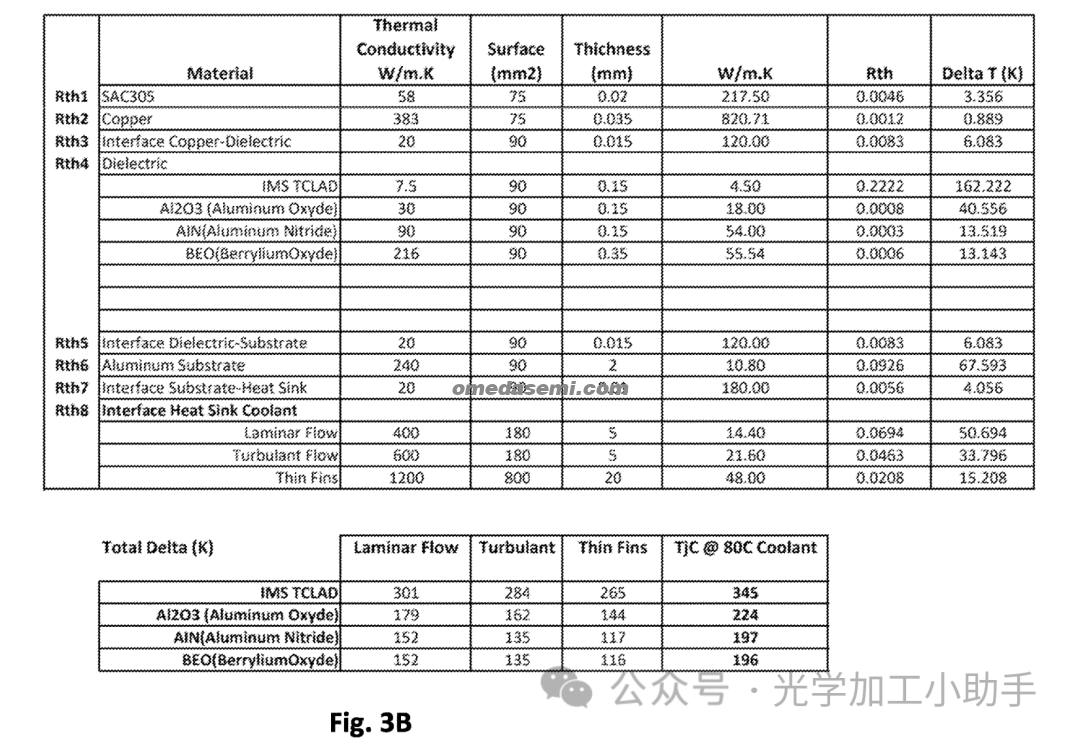
图3B是包含用于计算现有技术中功率器件中电/热路径的示例的热阻的相关值的表格。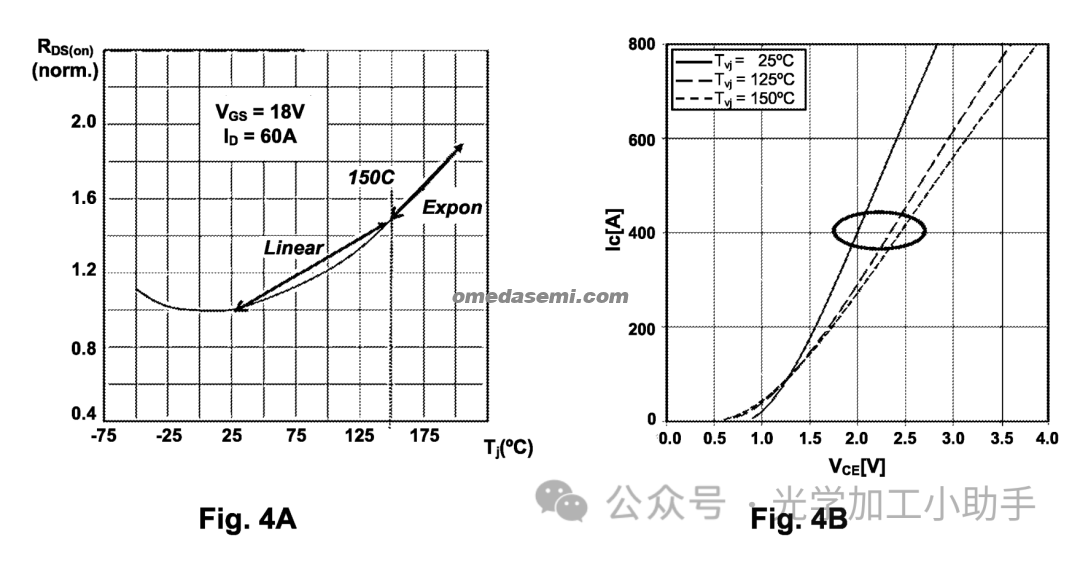
图4A是显示典型碳化硅(SiC)功率器件的归一化导通电阻(RdsON)与温度的关系的折线图。
图4B是描绘典型IGBT器件集电极和发射极两端(V CE(sat) )的饱和电压与温度的关系的折线图。
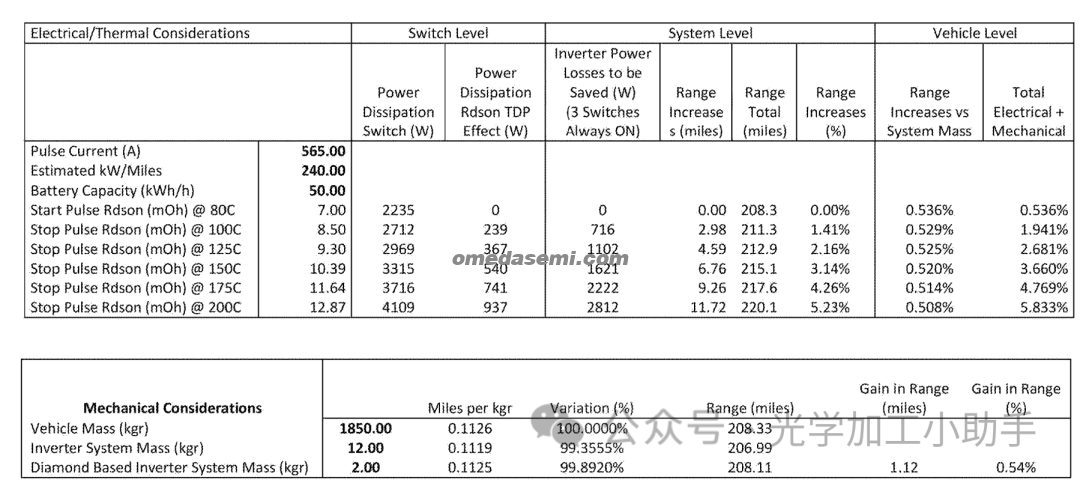
图5是根据现行功率器件标准转换为标准EV轿车续航里程的三相250kW逆变器系统的功率传导损耗汇总表
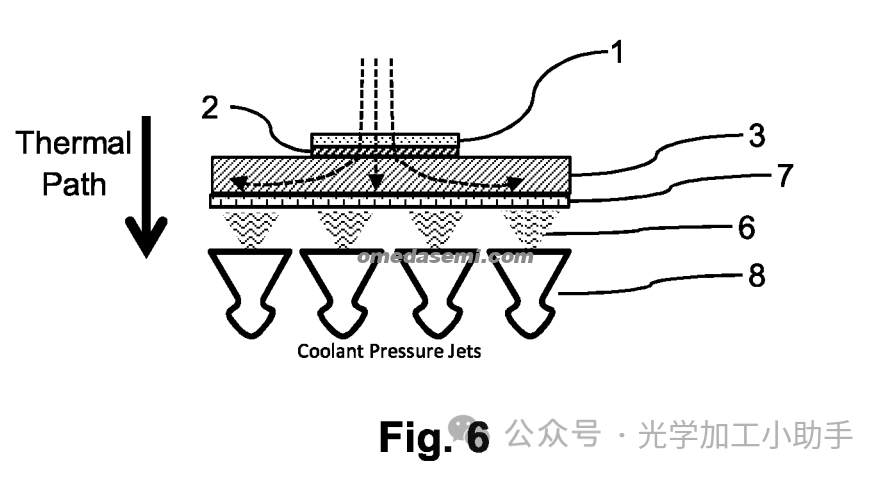
图6是根据本公开的各个方面改进的热-电路径功率器件的横截面图。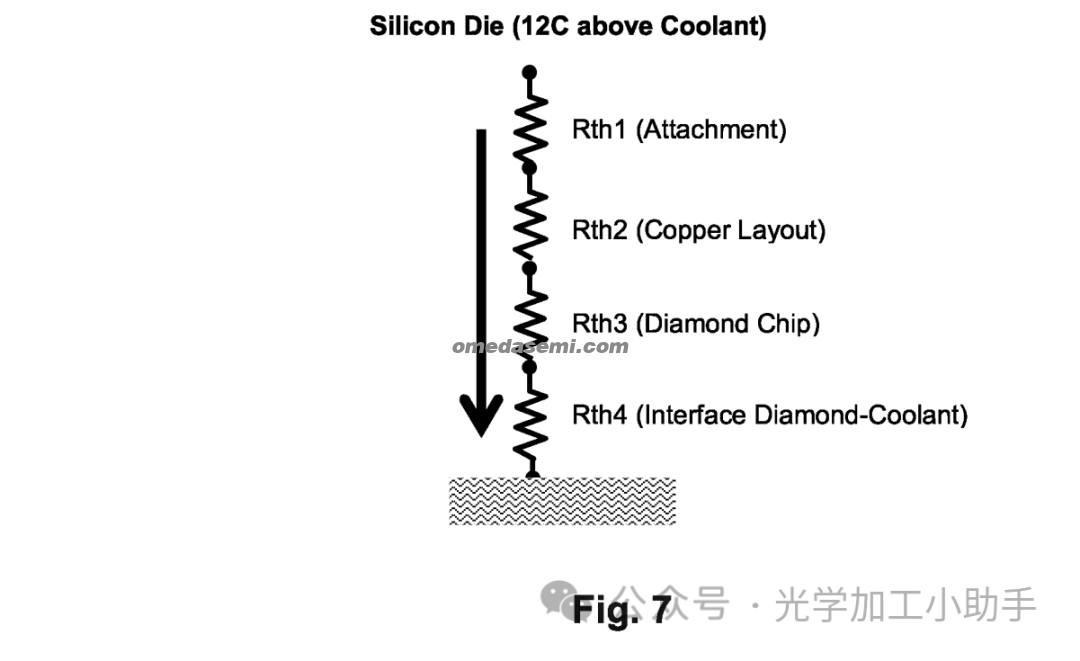
图7是根据本公开的各方面改进的电/热路径功率器件的热阻Rth模型表示。
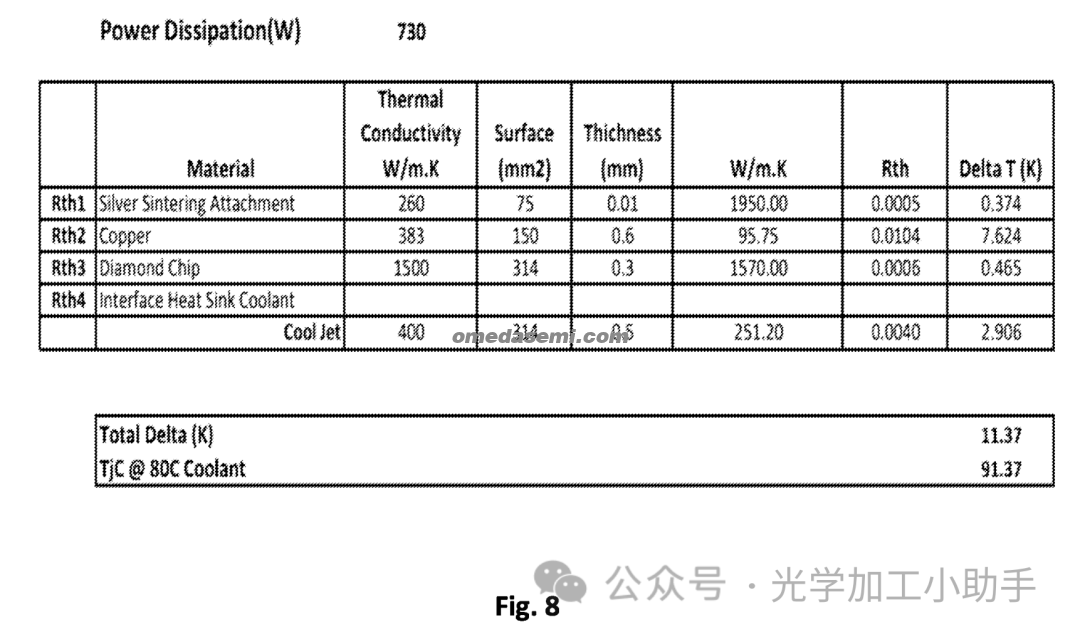
图8是包含用于计算改进的电/热路径功率器件的热阻的相关值的表格。
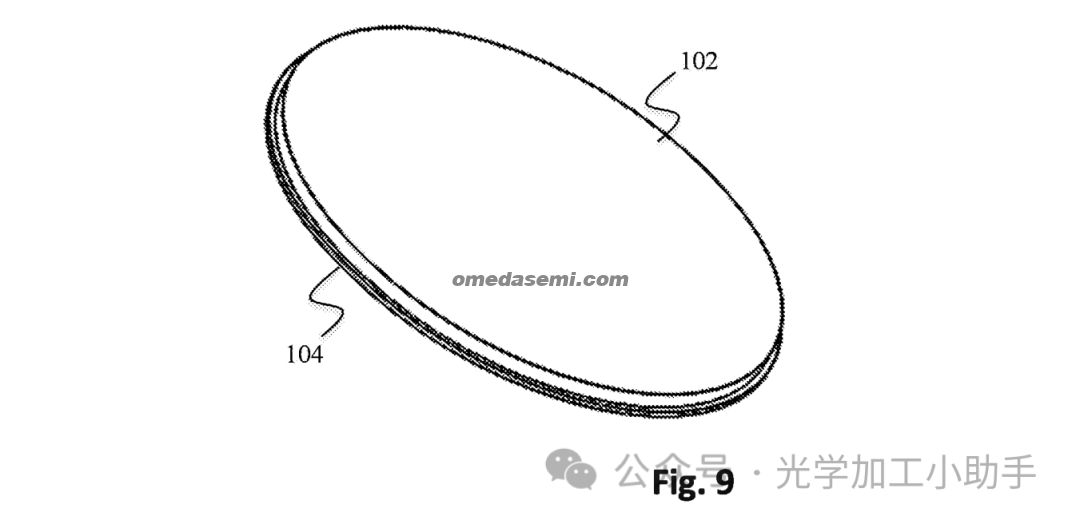
图9是根据本公开的各方面改进的热电路功率器件的制备方法过程中基板的四分之三视图。
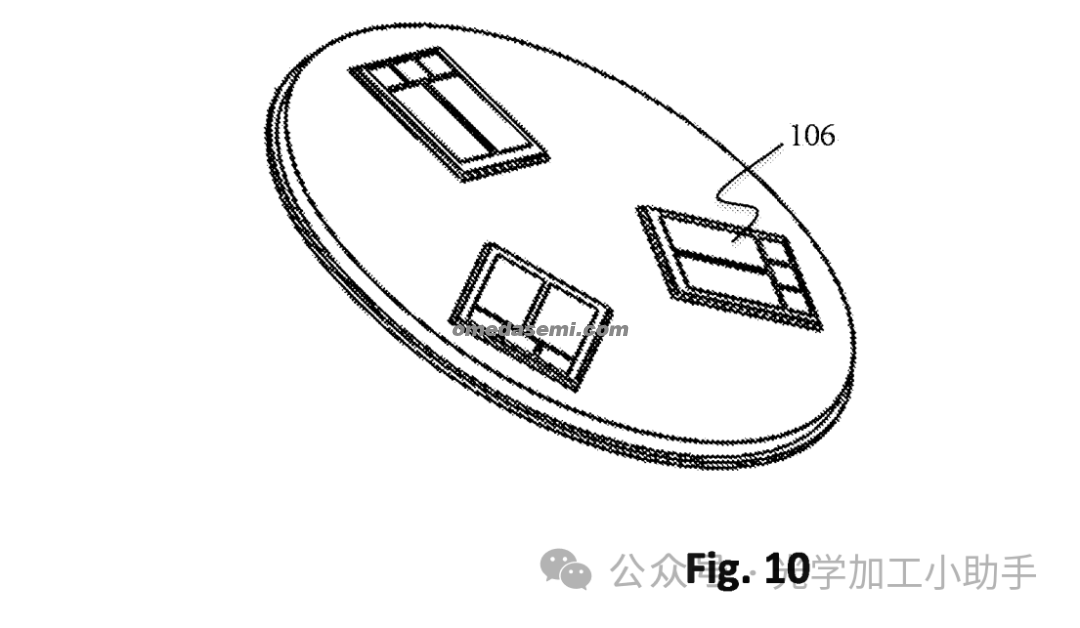
图10是根据本公开的各方面改进的热电路功率器件的制造过程中附着在基板表面的晶体管的四分之三视图。
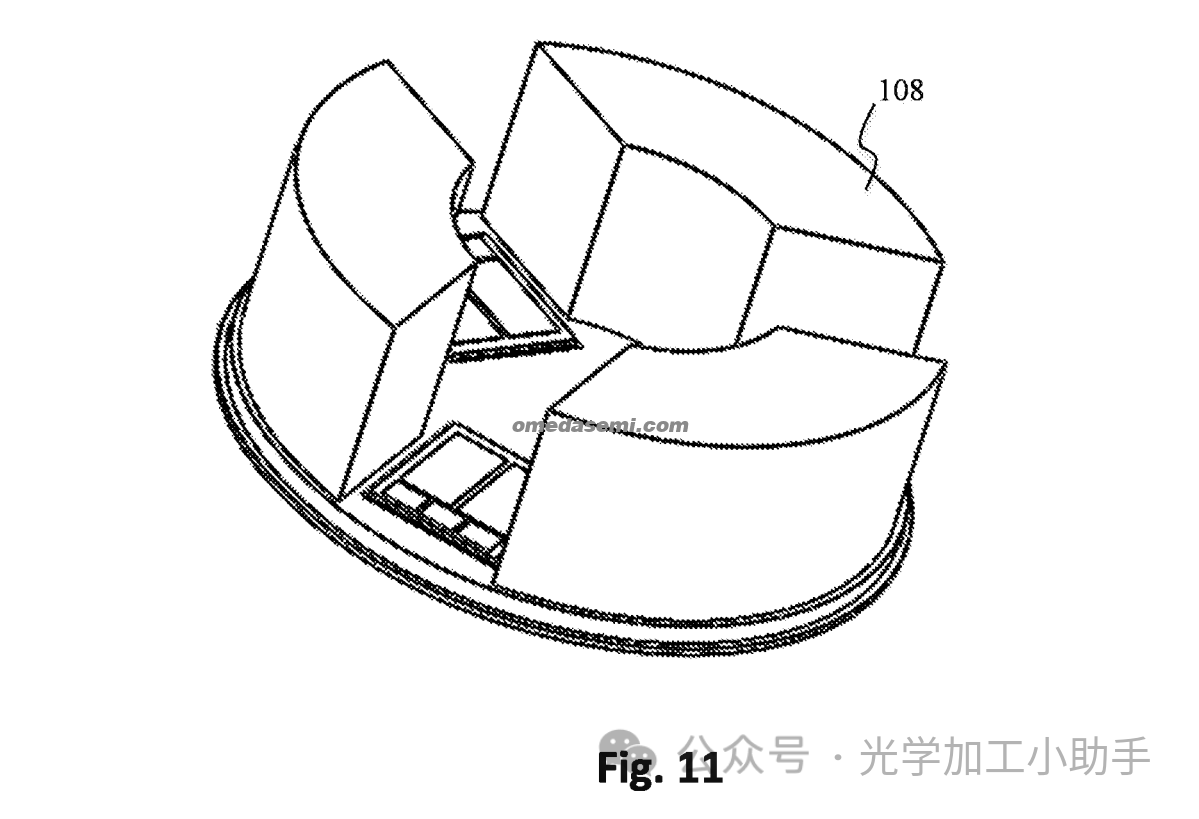
图11是根据本公开的各方面在制造改进的热电路径功率器件的过程中耦合到晶体管器件之间基板的导电柱结构的四分之三视图。
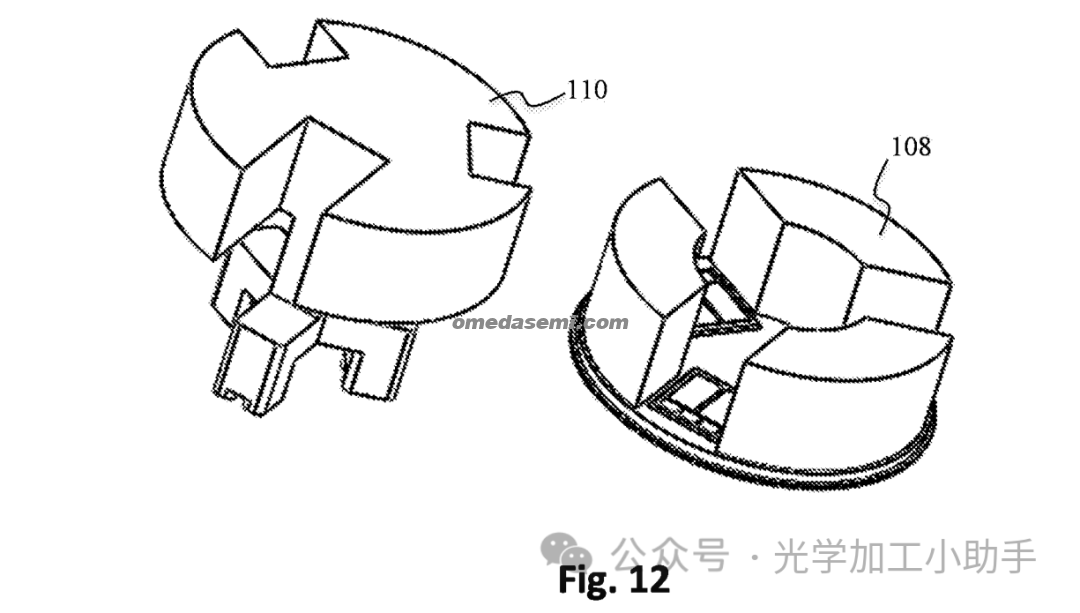
图12是并排、四分之三视图描绘的导电夹和基板在制造过程中具有导电柱的改进的热电路径功率器件。
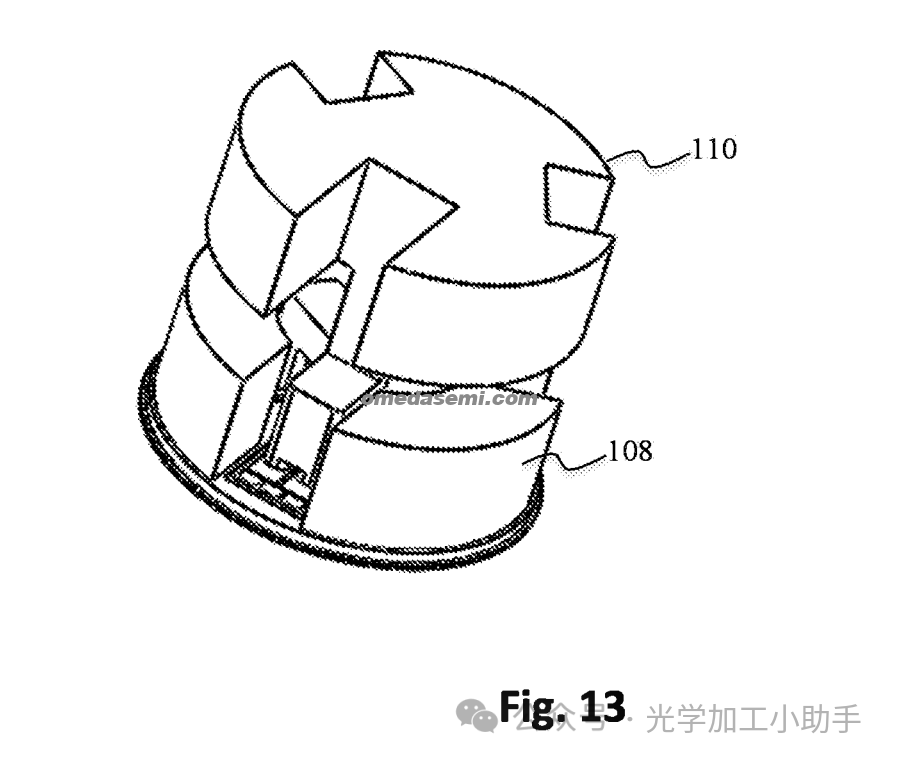
图13是四分之三的视图,描绘了在根据本公开的方面制造改进的热电/路径功率器件期间安装并连接到基板上的晶体管的导电夹。
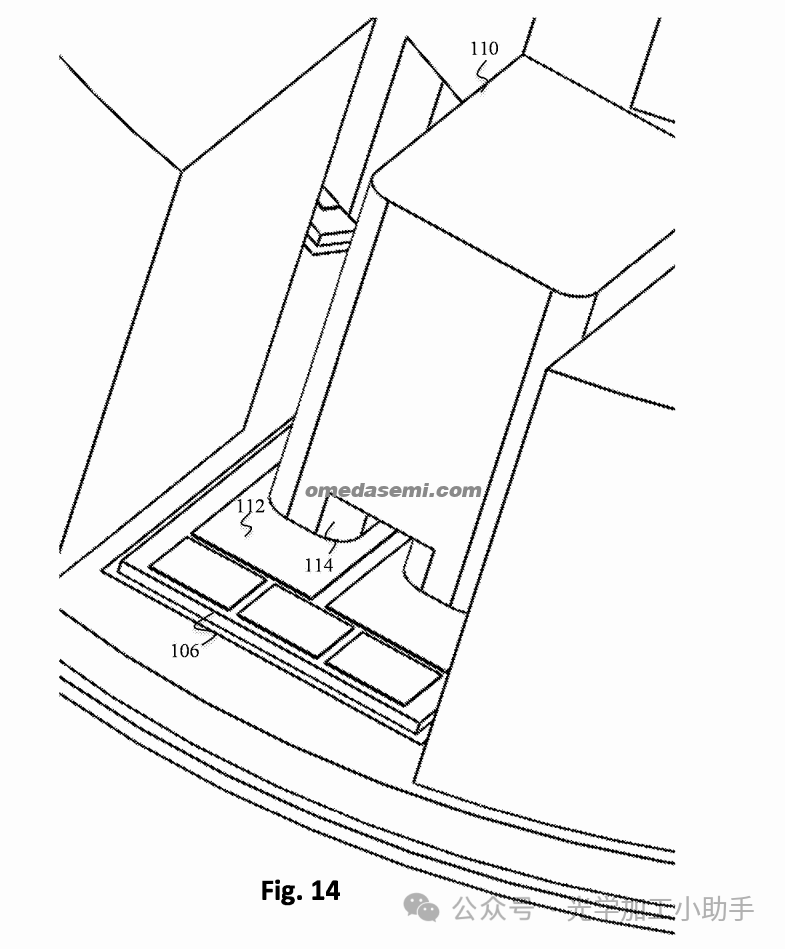
图14是四分之三的剖面图,显示了根据本公开的各方面改进的热电路径功率器件的制造过程中导电器件的安装和连接到晶体管。
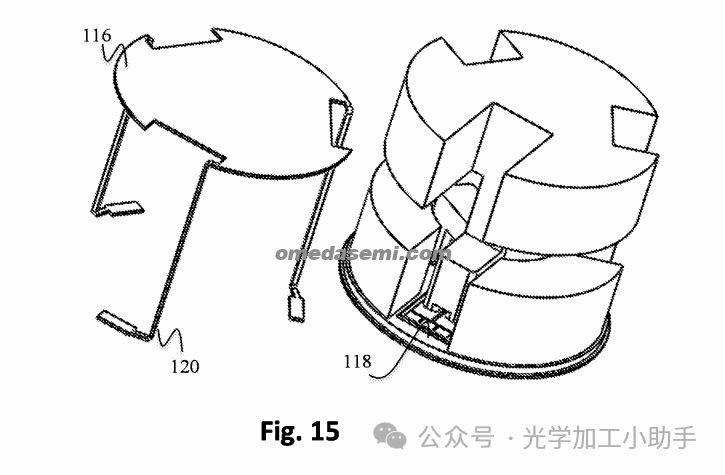
图15是并排的四分之三视图,显示了根据本公开的各方面在制造改进的热电路径功率器件过程中用于栅极连接和基板夹组件的薄柔性印刷电路板(PCB)。
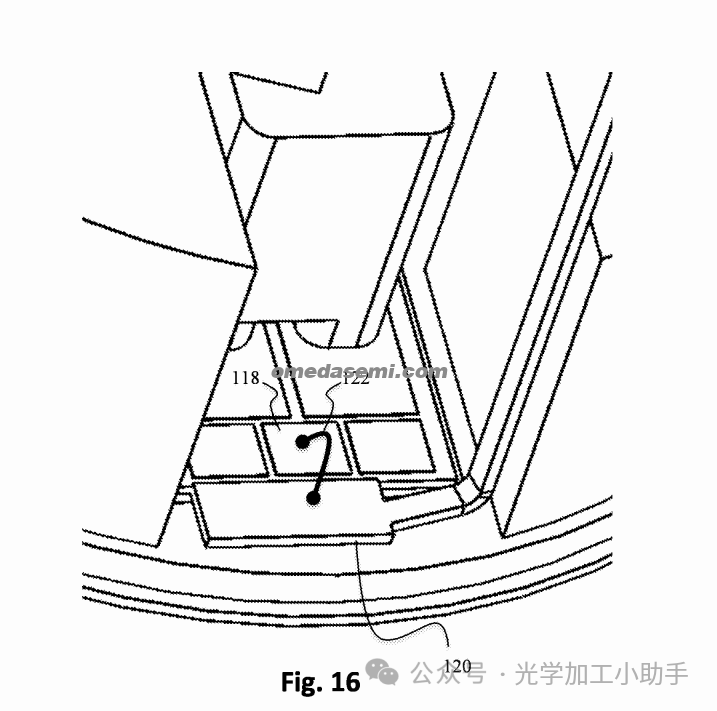
图16是根据本公开的各方面在制造改进的热电路功率器件的过程中形成的薄柔性(PCB)和晶体管焊盘的四分之三的切开视图。
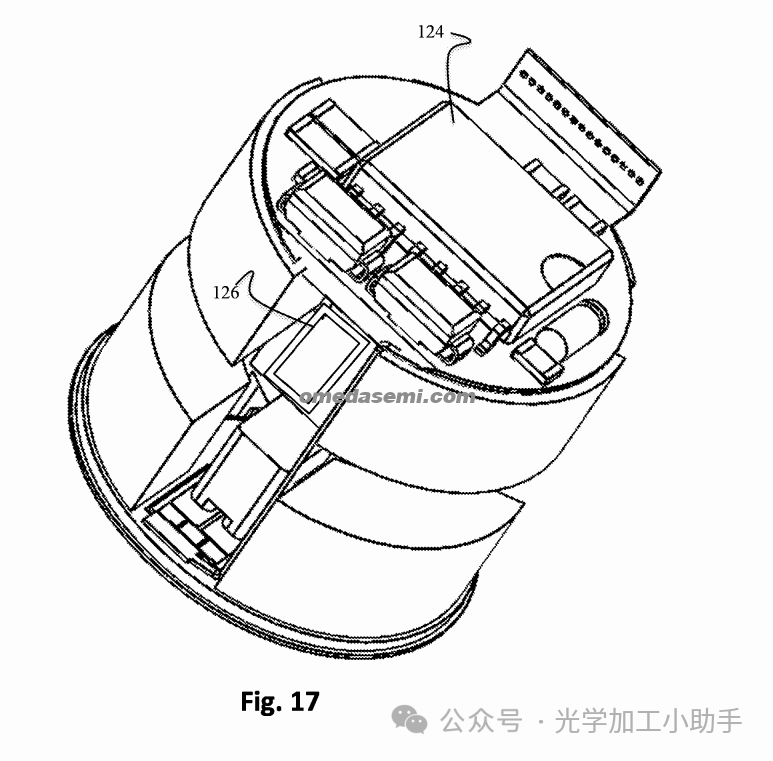
图17是四分之三的剖面图,显示了在制造改进的热电路功率器件期间,安装在薄柔性PCB上的栅极驱动器、控制和传感电路,这些电路耦合到基板夹组件上。
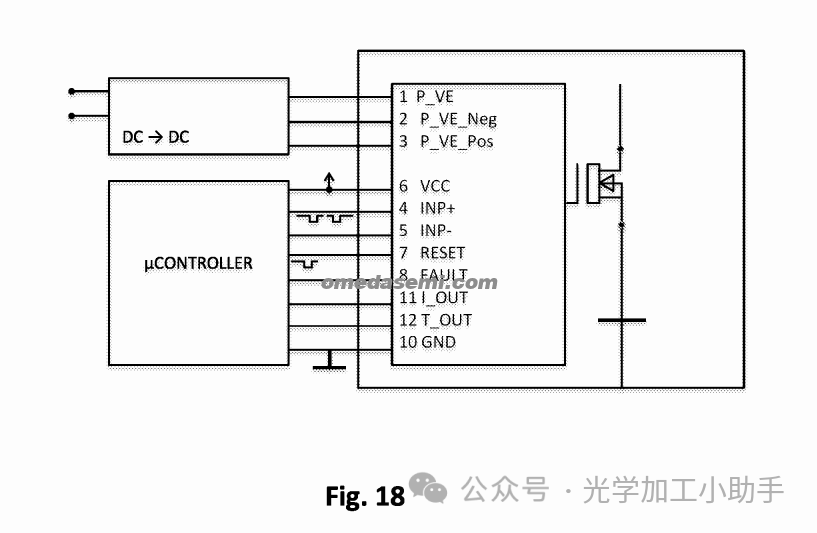
图18是根据本公开的各方面描述薄型柔性PCB上的栅极控制电路布局示例的电路图。
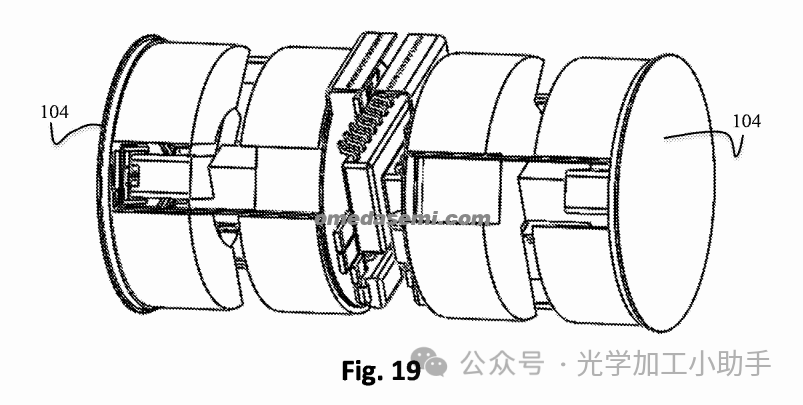
图19是根据本公开的各个方面,描绘了两个改进的热电路径功率器件以背靠背配置排列,从而创建改进的半桥器件的示意图。
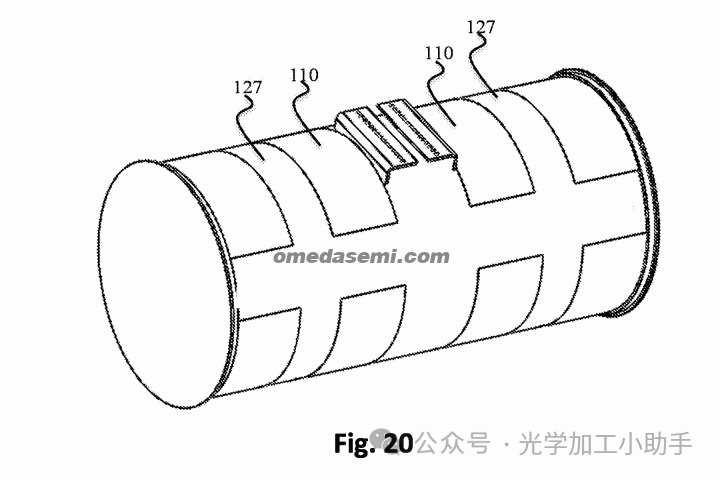
图20是描绘根据本公开的各方面改进的半桥装置的区域中环氧化合物的形成的图。
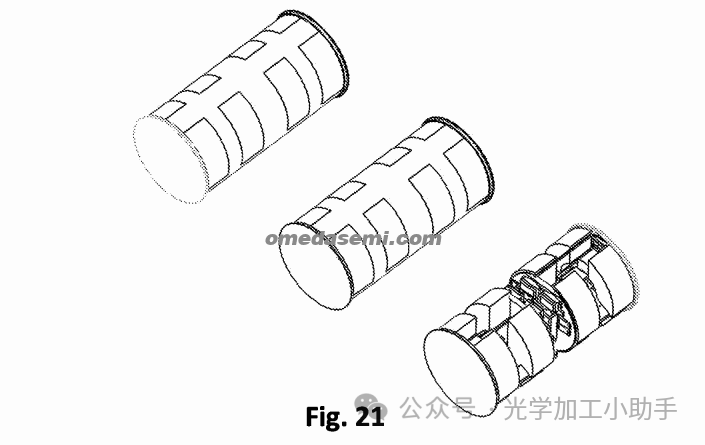
图21是描述根据本公开的方面以并联配置排列的三个改进的半桥装置的示意图。
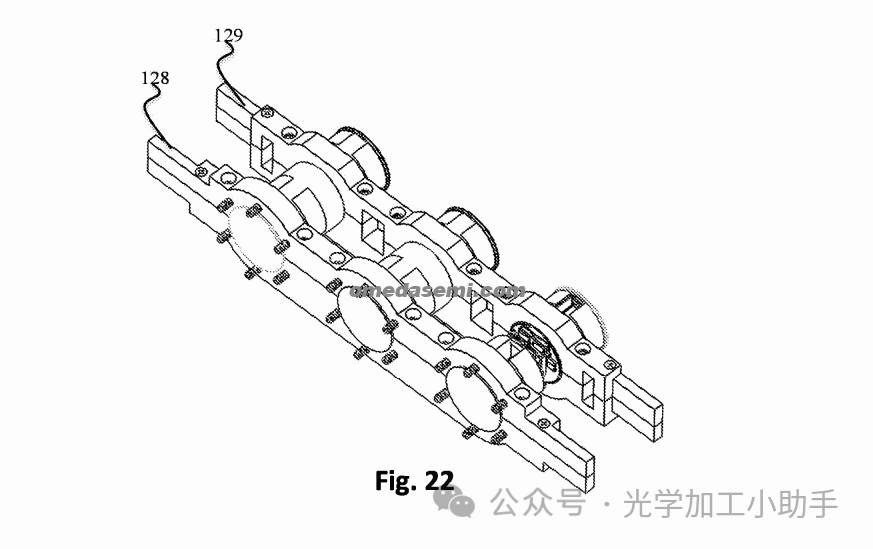
图22是根据本公开的实例,描绘了以并联配置刚性连接三个改进的半桥器件的母线的示意图。
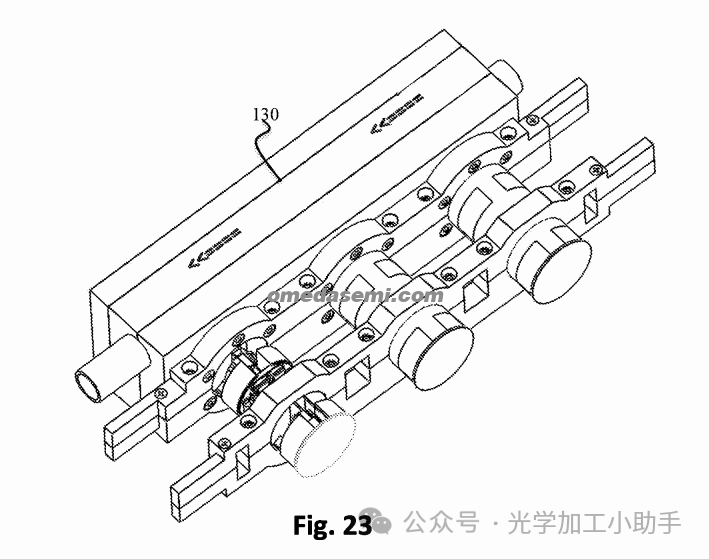
图23是描绘根据本公开的各方面安装在经由母线连接的三个改进的半桥装置上的冷却射流冷却剂块的示意图。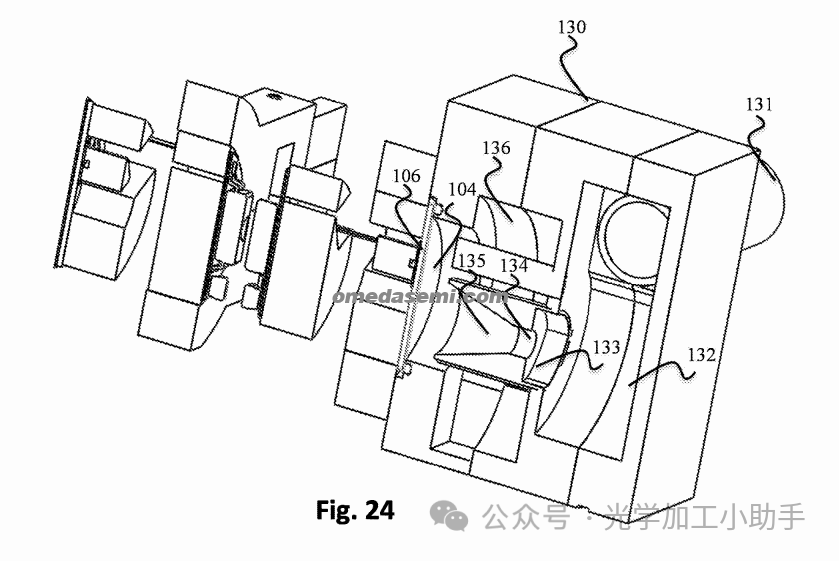
图24是根据本公开的方面安装在冷却喷射冷却剂块上的改进型半桥装置的剖面侧视图。
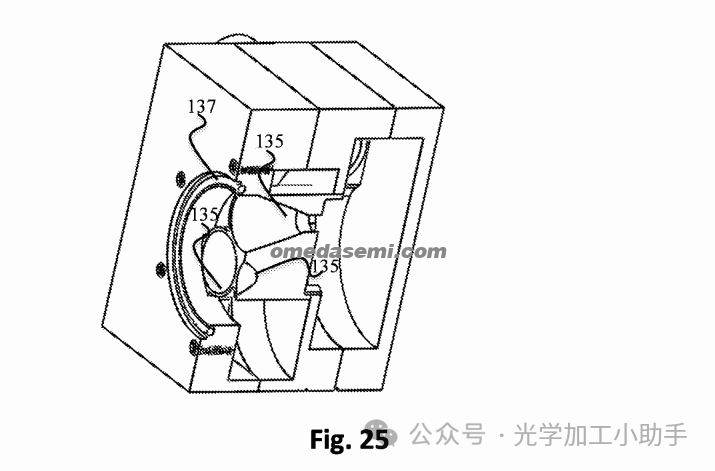
图25是根据本公开的各个方面提供的单个冷却射流冷却块的剖面图。
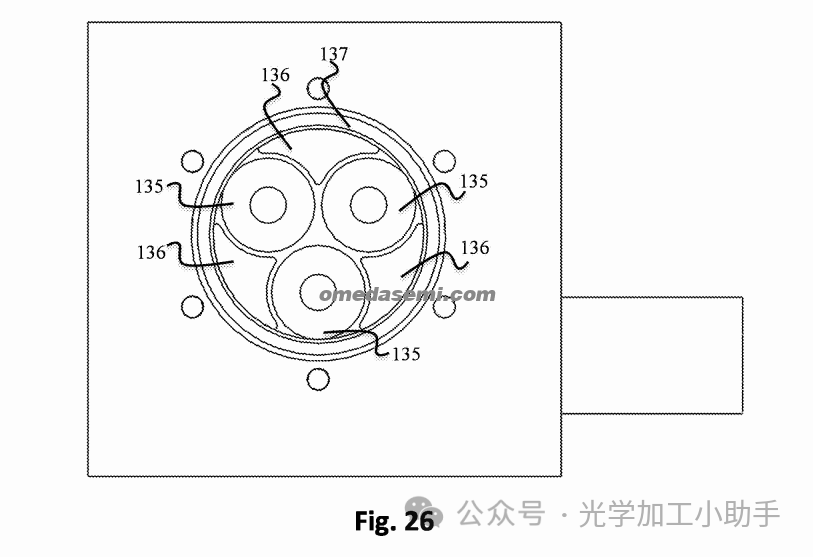
图26是根据本公开的方面面向半桥装置安装的冷却射流冷却块的侧面的剖面图。
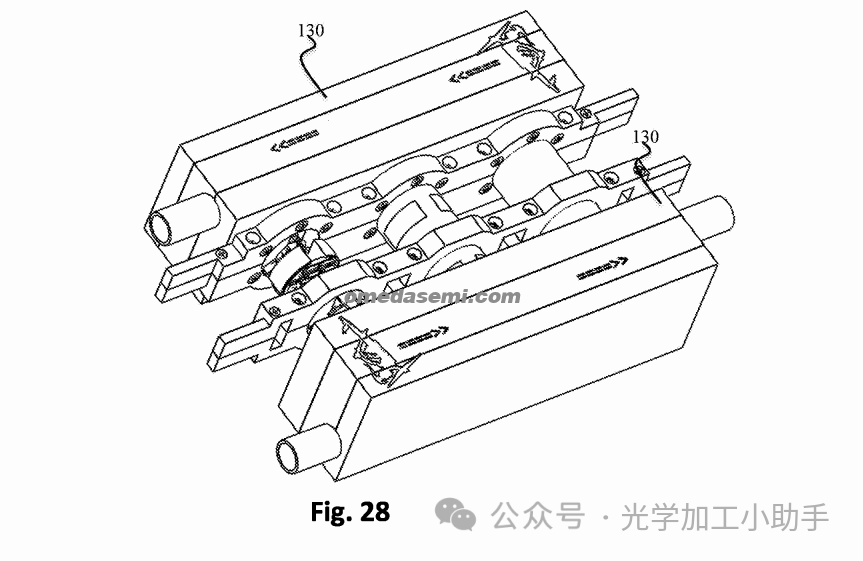
图28是示出两个冷却液块的示意图,根据本公开的各方面,一个安装在三相电源逆变器的每一侧。

图29是描绘根据本公开的各方面安装电机相电源联动装置的已完成的三相逆变器组件的示意图。
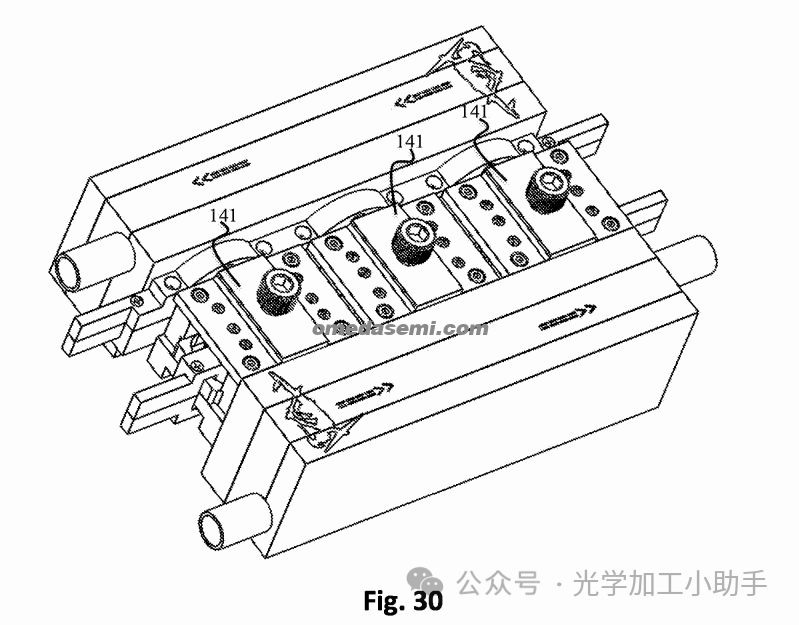
图30描绘了根据本公开的方面,安装在三相逆变器上的两个冷却剂块具有耦合到电机相电源连杆的电机相紧固件。
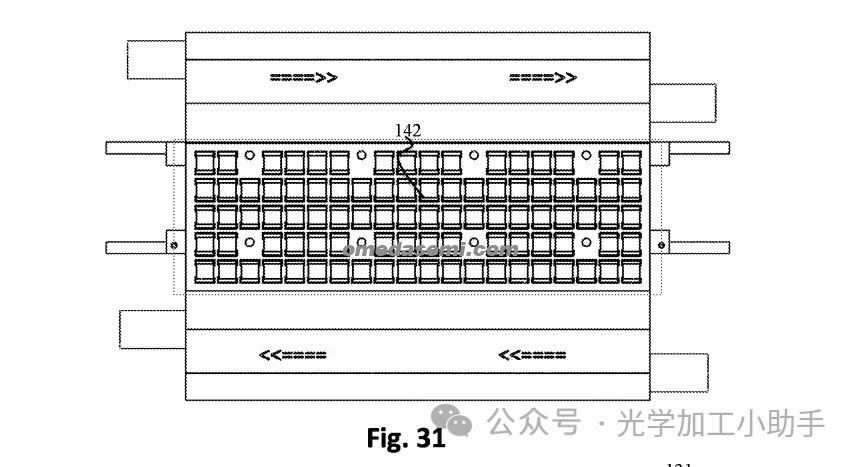
图31示出了根据本公开的方面,集成大容量电容器和其它无源电路,它们可以耦合到与电机相紧固件相对的一侧的三相逆变器上。
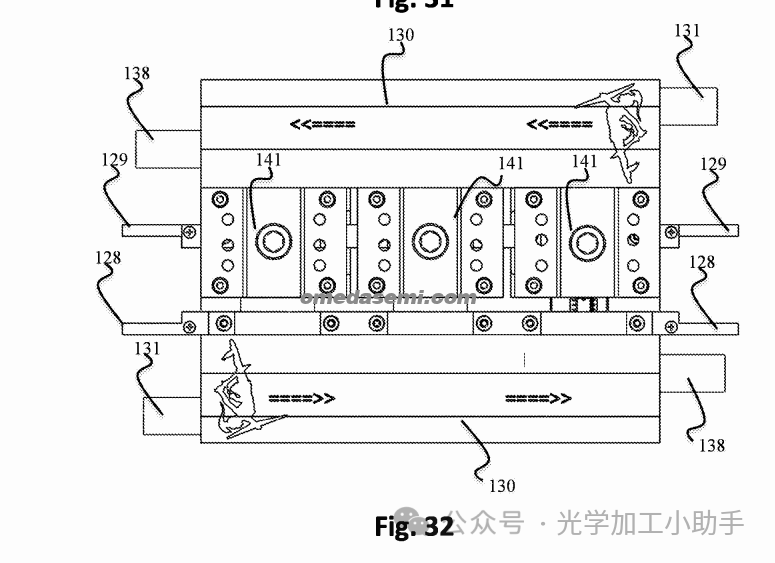
图32描绘了根据本公开的各个方面完成的带冷却块的三相逆变器的自上而下的视图。
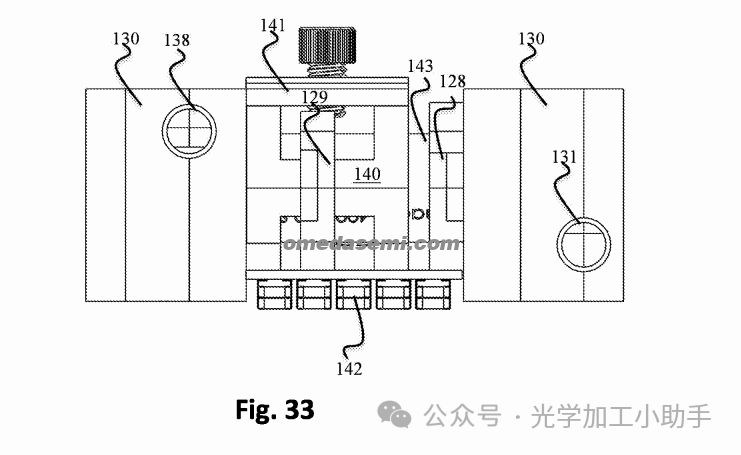
图33示出了根据本公开的各方面完成的带冷却块的三相逆变器的侧视图。
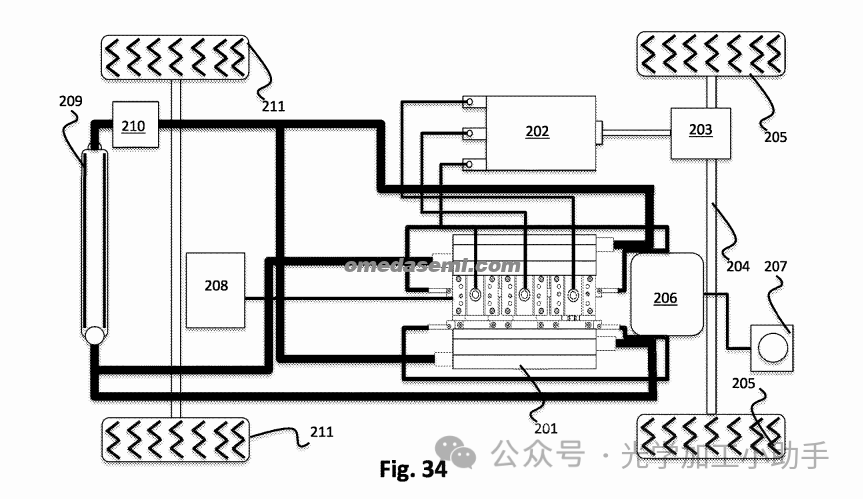
图34描绘了一种简单的电动汽车,包括根据本公开的各方面改进的三相逆变器。
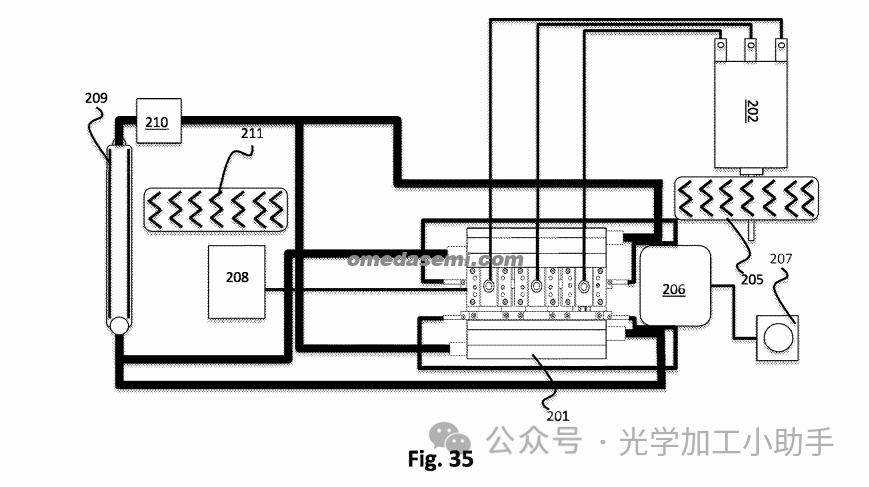
图35是根据本公开的各个方面描绘了使用改进的三相逆变器的简单直驱电动汽车的布局图。
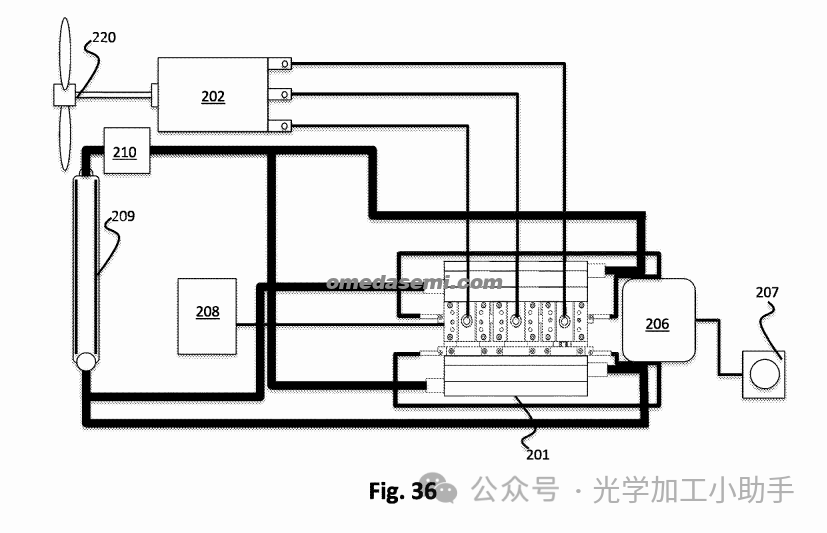
图36是示出根据本公开的方面使用改进的三相逆变器的直接驱动电动汽车的替代实现的布局图。