本文小编今天分享一篇文章,和前面小编的文章类似,同样是来自韩国的Junsuk Rho老师团队,只不过本文的应用的波段为紫外波段,和前面类似文章采用的纳米压印和 复合聚合物层,但是应用于紫外波段,本文作者采用了zro2作为聚合物上层的涂层,进一步改善在紫外波段的折射率。
详细工艺细节分析看前文 ,本文仅作分享,不做额外赘述
12寸紫外光刻纳米压印超透镜--工艺深入分析---用于可见光超光子学的高折射率原子层-聚合物混合超表面的可扩展制造
划重点:
我们为客户提供晶圆(硅晶圆,玻璃晶圆,SOI晶圆,GaAs,蓝宝石,碳化硅,金刚石),镀膜方式(PVD,cvd,Ald)和材料(Au Cu Ag Pt Al Cr Ti Ni Sio2 Tio2 Ti3O5,Ta2O5),光刻,高精度掩模版,外延,掺杂,电子束光刻等产品及加工服务(请找小编领取我们晶圆标品库存列表,为您的科学实验加速。
EBL代工,母版制作,铬版销售,纳米压印,DUV光刻超结构服务,
面向头部企业,研究单位等单位的可见光近红外波段超透镜仿真设计(从仿真设计到demo样品,国内前五设计团队,经验丰富,算法超前)
请联系小编免费获取原文,也欢迎交流半导体行业,工艺,技术,市场发展!
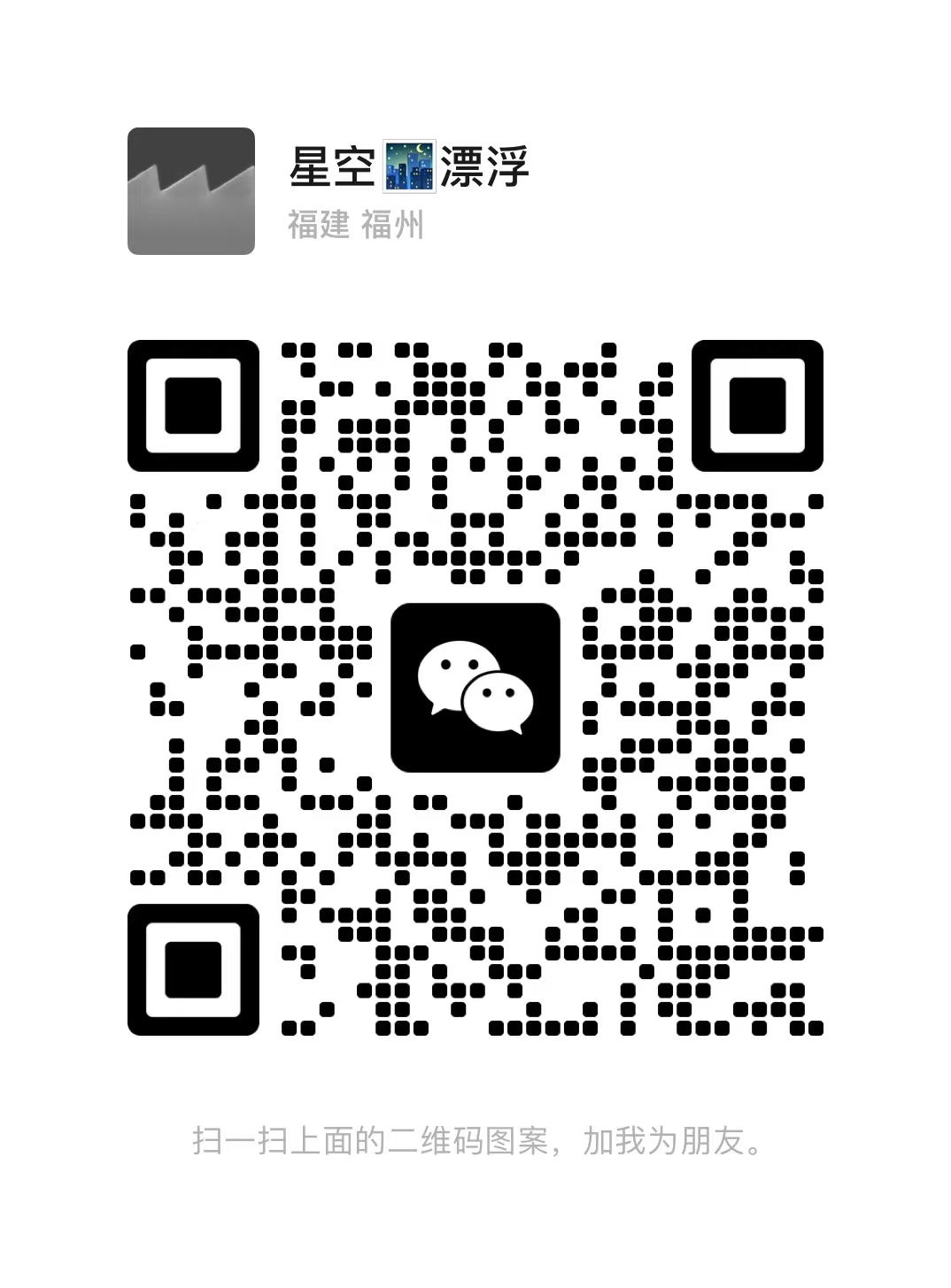
摘要
超透镜具有出色的光调制性能,人们对其进行了研究,不仅可以取代传统的笨重且重的折射透镜,还可以对其进行扩展。然而,它们的工作波长很少覆盖紫外线(UV)范围,因为紫外线透明材料稀缺,并且纳米图案化技术图案化面积小、成本高且产量低。这项研究克服了这些限制,成功批量生产了厘米级高效的紫外超透镜。UV 超透镜设计工作波长为 325 nm,数值孔径为 0.2。氟化氩光刻技术用于制作 8 英寸的母版印模,其中 300 个超透镜以高分辨率排列成阵列。制作好的母版印模可以使用晶圆级纳米压印光刻技术进行重复复制。为了提高效率,我们开发了一种二氧化锆-聚合物混合材料,它是可扩展的、易于制造的、紫外线透明的高折射率材料。实验结果证实,批量生产的超镜头可以作为理想的成像系统,平均测量效率为 45.1%。
介绍
.紫外线 (UV) 光是肉眼看不见的,但紫外线光学为我们周围的世界提供了新的见解。紫外分光光度法和圆二色性 (CD) 光谱已被用于估计各种化学反应和生物功能 [1]、[2]、[3]、[4]。紫外光学成像可以实现纳米结构的高分辨率成像 [5], [6]。紫外光刻因其大规模生产能力和高分辨率图案化能力而在半导体行业中至关重要[7]、[8]。此外,紫外光学对于量子光学、光疗、灭菌、数据存储和防伪等各种应用至关重要[9]。
迄今为止,紫外光调制一直依赖于传统的反射或折射光学器件。然而,它们体积大、重,并且光调制自由度低,导致功能、多样性、可制造性和操作带宽有限。超表面最近因其非凡的光调制能力、亚波长分辨率、易于集成和紧凑的外形而成为一种新策略[10]、[11]、[12]、[13]、[14]、[ 15]。它们的多功能设计允许各种应用,例如透镜 [16]、[17]、[18]、[19]、全息术 [20]、[21]、[22]、[23]、[24]、[25]、结构颜色[26]、[27]、[28]、[29]和生物传感器[30]。然而,由于紫外超表面的长期挑战,以前的超表面的工作波长很少延伸到紫外区域,并且大部分保持在可见光和红外区域。
紫外超表面的主要瓶颈是紫外透明材料的稀缺以及纳米图案技术的高成本和低产量。传统介电材料,例如硅 (Si) 基材料、二氧化钛 (TiO 2 ) 和氮化镓 (GaN) 等,具有较小的带隙,导致在 UV 区域具有较大的吸收和较低的透射率[31]。迄今为止,新材料如氮化硅(Si 3 N 4 )[32]、五氧化二铌(Nb 2 O 5 )[33]、氧化锌(ZnO)[34]和氧化铪(HfO 2 )[35]已被用作UV超表面;然而,这些紫外线透明材料不可扩展或易于制造。以往的紫外超表面的制造方法涉及用于高分辨率图案化的电子束光刻,导致成本极高、产量低且制造工艺复杂。因此,大型紫外超表面无法使用以前的方法制造,距离实际应用还很远(补充说明1)。为了克服这些限制,纳米压印光刻(NIL)已被积极用于降低制造成本并提高产量[36],[37],[38],[39],[40],[41],[42] ,[43],并且光刻已被用于制造晶圆级的大面积超表面[44],[45]。最近,使用光刻和纳米压印光刻大规模生产可见超透镜[46]。然而,紫外透明材料的低制造兼容性和低图案分辨率仍然阻碍了紫外超表面的晶圆级制造。
在这项研究中,我们通过引入晶圆级纳米压印紫外超表面平台和紫外透明二氧化锆(ZrO 2 )-具有高折射率的聚合物混合材料来克服这一长期存在的挑战(图1)。1)。我们使用高速电子束光刻来制造带有单个 4 厘米 UV 超透镜图案的掩模版。使用氟化氩 (ArF) 扫描仪和制造的掩模版在 8 英寸硅晶圆上制造具有 1 厘米 UV 超透镜阵列图案的母模。应该指出的是,ArF 扫描仪具有足够高的 40 nm 分辨率来图案化 UV 超透镜。尽管 ArF 扫描仪价格昂贵,但我们的方法可以使用 NIL 实现极低成本和高通量的制造。ZrO 2 – 聚合物混合材料可以使用压印树脂作为最终结构。通过在树脂结构上涂覆 15 nm 的 ZrO 2 层,光被强烈限制在 ZrO 2 薄膜内,从而在目标波长下实现 80% 的高转换效率325纳米。验证了所制造的超透镜的衍射极限聚焦和成像性能。由于主印模和复制模具都是可重复使用的,因此我们的制造方法可以实现大面积 UV 超表面的低成本和高产量制造。
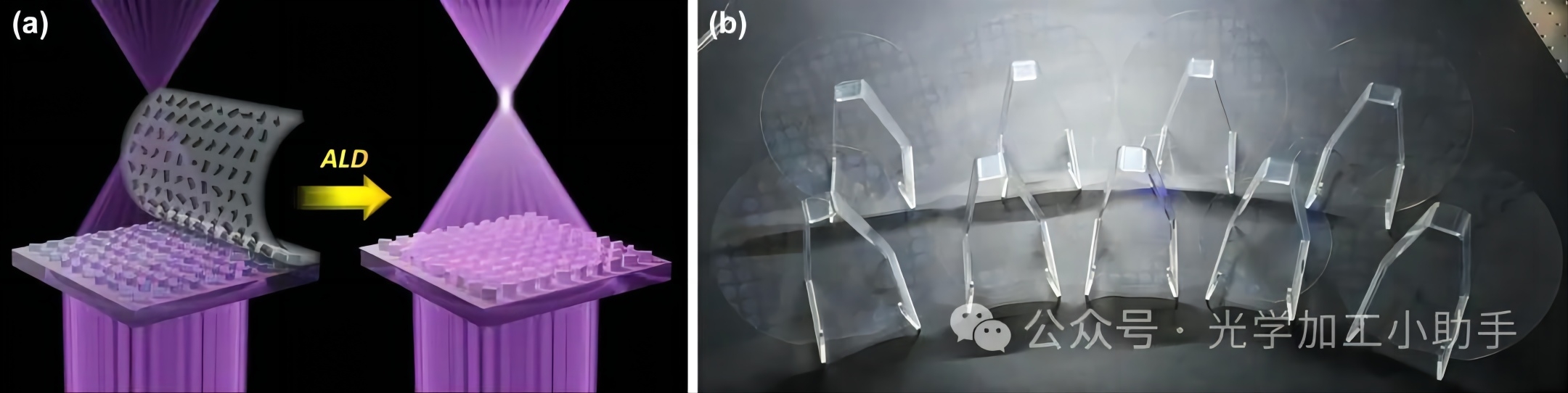
图 1. 高效晶圆级压印 UV 超表面平台。(a) 用于提高效率的 ZrO 2 聚合物杂化材料的制造示意图。(b) 在 4 英寸、6 英寸和 8 英寸晶圆上量产的 1 厘米 UV 超透镜照片。
结果
紫外光全相位调制的设计原理
这项工作的主要目标是通过涂覆高折射率材料,使用印刷树脂本身作为超原子,从而以低成本和高产量制造 UV 超表面。间原子的构成材料应具有足够高的折射率(n)以很好地限制光,并具有足够低的消光系数(k)以最大限度地减少紫外线区域的吸收。然而,传统的可印刷材料,如 UV 和热压印树脂,折射率较低,约为 1.5(补充说明 2)。为了提高有效折射率,我们提出了一种高折射率原子层-聚合物杂化材料;然而,由于TiO 2 的高紫外吸收,以前的混合材料在紫外区域不透明。因此,我们提出了一种ZrO 2 -聚合物混合材料,其中印刷的超表面薄薄地涂有高折射率材料以增加有效折射率。这种高折射率材料必须满足几个条件:首先,折射率必须足够高,即使是薄膜,也能很好地限制光线;其次,带隙必须足够宽才能透紫外光;第三,必须使用原子层沉积(ALD)来沉积高折射率材料,以在超表面的所有侧面上形成均匀的薄膜。为了满足上述所有条件,我们选择ZrO 2 作为紫外高折射率材料。ZrO 2 薄膜的光学性质通过椭圆光度法测量(补充说明3)。在紫外区域,ZrO 2 薄膜具有超过2.2的高折射率(n)和接近于零的消光系数(k)(图2b)。ZrO 2 薄膜具有 6.195 eV 的宽带隙,这使得它对紫外光透明(图 2)。2c,补充说明 4)。
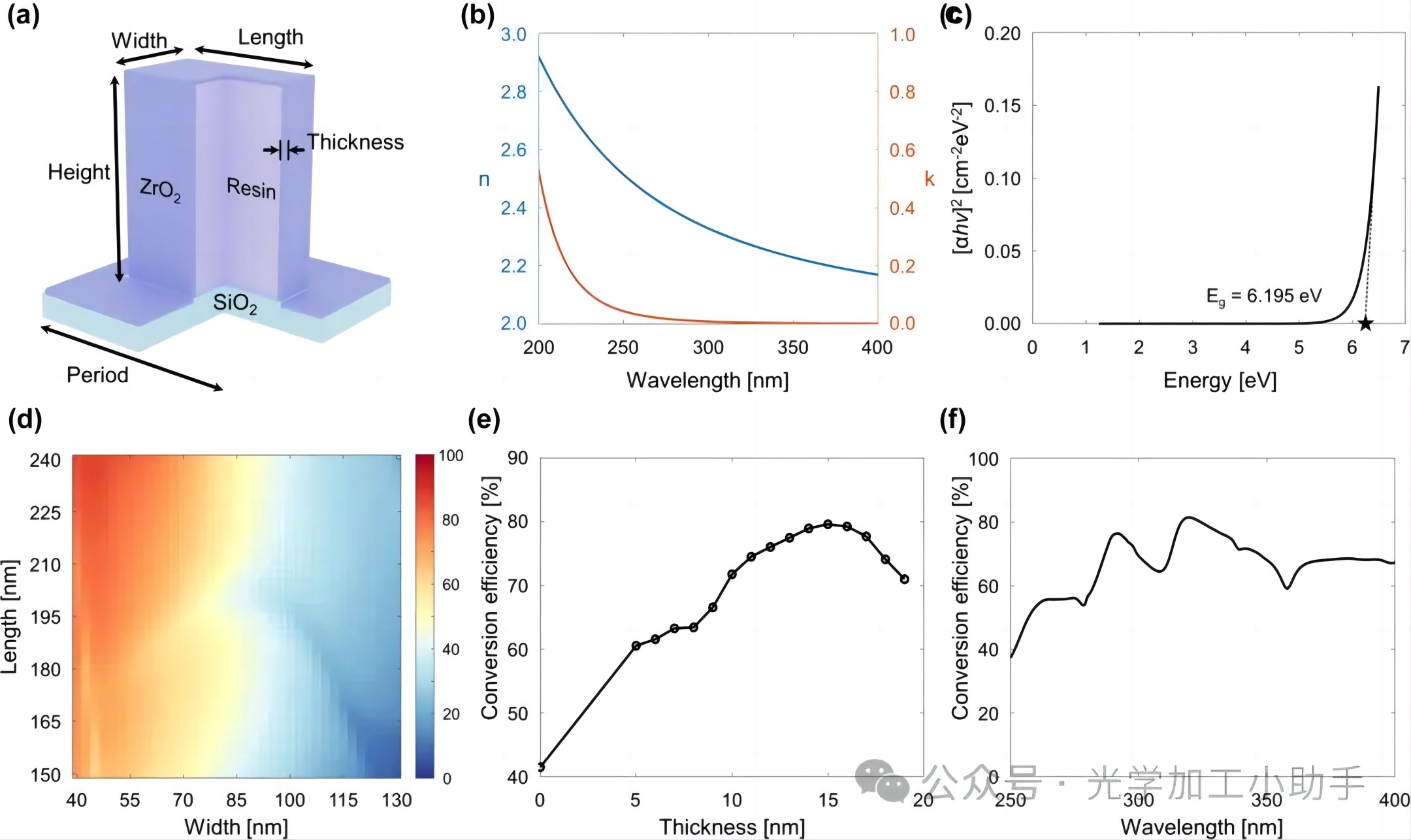
图2 高效紫外元原子的设计与模拟。(a) 混合元原子结构的配置。长度:240纳米;宽度:60纳米;高度:550纳米;周期:280 nm;厚度:15纳米。(b) 测量的 ZrO 2 薄膜的光学性能。蓝线:折射率;橙色线:消光系数。(c) 计算出的 ZrO 2 薄膜的光学带隙。(d) 在固定高度 (550 nm)、周期 (280 nm) 和 ALD 厚度 (15 nm) 的情况下,在 325 nm 波长下模拟元原子的转换效率。(e,f) 不同的模拟转换效率图 - (e) ALD 厚度从 0 nm 到 19 nm,(f) 波长从 250 nm 到 400 nm。
所提出的制造工艺示意图如图 3 所示。首先,使用高速电子束光刻制备用于 ArF 光刻的掩模版(图 3a)。使用 ArF 光刻和制作的掩模版,在 8 英寸硅晶圆上制作了带有超透镜阵列图案的主印模(图 3b、c、e)。接下来,用硬质聚二甲基硅氧烷(h-PDMS)溶液旋涂制作好的母模,以40 nm的高分辨率复制反转图案,因为它具有高模量(∼9N/mm 2 )[ 48]。随后,将聚二甲基硅氧烷(PDMS)旋涂到 h-PDMS 层上。在这两个过程中,h-PDMS 和 PDMS 均通过加热至 70℃ 来硬化。该印模是通过将固化的 h-PDMS 和 PDMS 从母模上分离而制造的(图 3f)。随后将传统的紫外线固化树脂 (MINS-311RM) 旋涂到制作好的印模上,然后用二氧化硅基材覆盖。压印树脂在适当的压力和紫外线下固化。将印模与固化树脂分离后,进行反应离子蚀刻(RIE)以去除固化树脂的残留层(详细信息参见方法,补充说明10)。最后,使用 ALD 在树脂结构上沉积一层 ZrO 2 薄层,形成混合材料(图 3d、g,补充说明 11)。
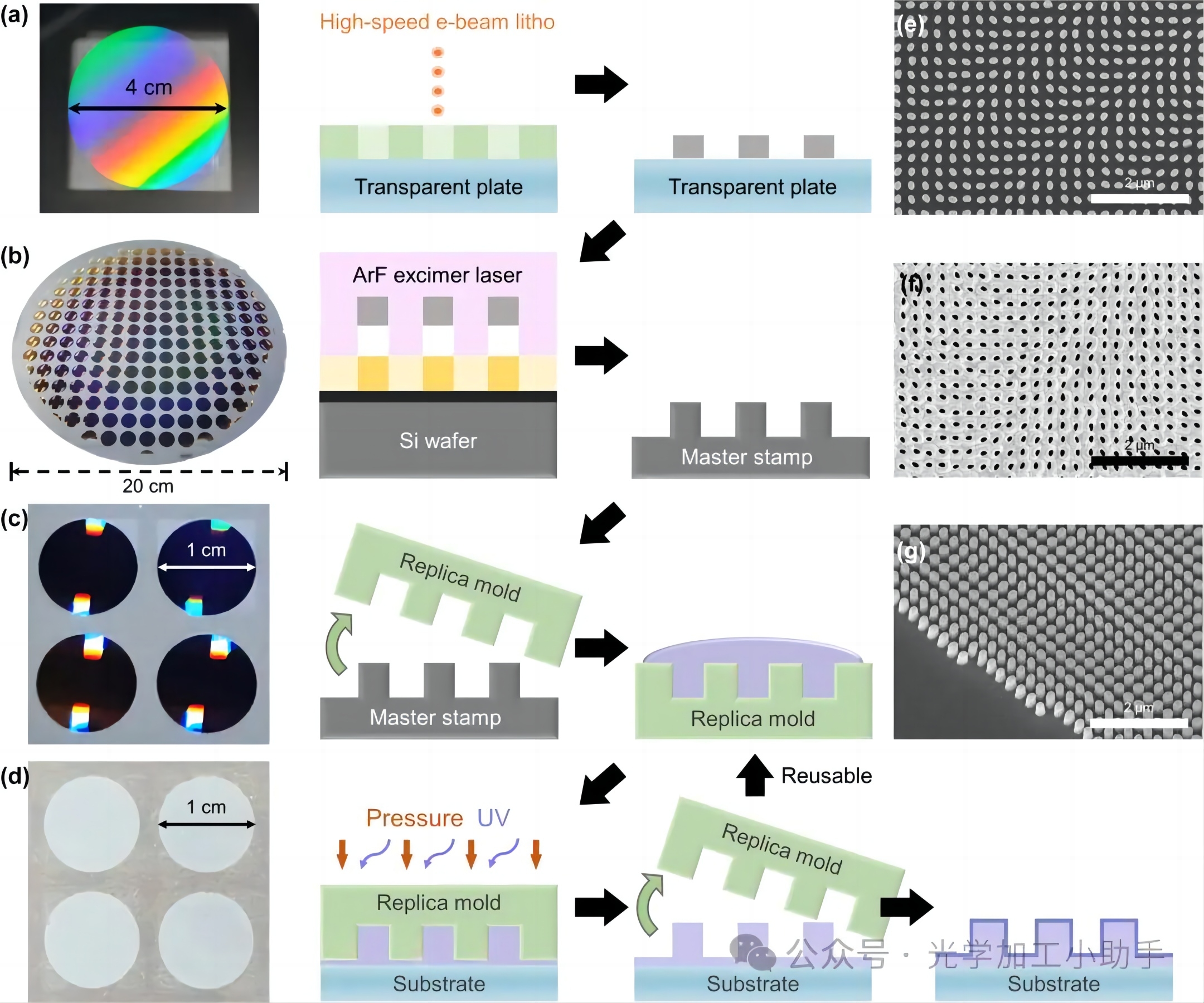
图 3. 晶圆级制造高效 UV 超表面的制造示意图。制作好的 (a) 十字线、(b,c) 主印章和 (d) 超透镜的照片。(e) 主印模、(f) 复制模具和 (g) 超透镜的扫描电子显微镜 (SEM) 图像
我们的制造方法允许以低成本和高吞吐量对紫外混合超表面进行大型高分辨率图案化。我们的工艺利用高速电子束光刻、ArF 光刻、NIL 和 ALD 系统。高速电子束光刻可以实现大面积的高分辨率图案化,但价格昂贵。因此,采用ArF光刻技术制作8英寸的母模,其中通过移动基板来连续曝光单个掩模版的图案。值得注意的是,ArF 光刻具有 40 nm 的高分辨率,足以制造设计的紫外元原子。然后使用 NIL 以极低的成本和高吞吐量复制主印模图案。由于通过旋涂和工艺压力将残留层调整到最低限度,因此即使图案面积很大,压印树脂也可以在 5 分钟内固化。此外,掩模版、主印模和复制模具可重复使用,这降低了成本并提高了产量(补充说明12)。由于这项工作中使用了传统的纳米压印树脂,因此该方法可以转移高度高达 1 μm 的结构(补充说明 13)。最后,ALD 通过形成可扩展且易于制造的混合材料,使印刷树脂结构能够用作最终结构。所有制造步骤均与成熟且众所周知的半导体制造方法兼容;因此,我们的方法不需要额外的设施。
UV超透镜的设计与演示
超表面必须满足透镜方程才能将光聚焦在一个焦点上。因为我们使用了几何相(PB 相),所以元原子会旋转以获得特定角度所需的相。相位分布由设定参数得出:直径 D = 1 cm,焦距 fl = 2.4 cm,数值孔径 NA = 0.2。生成的相位图如补充说明14所示。我们通过模拟和测量证实了UV超透镜的聚焦能力(图4a)。在仿真中,采用角谱法沿z方向传播电场。图 4f 和 4g 是用于表征超透镜的光学测量装置。如图4f中的聚焦测量装置示意图所示,线性偏振器(LP)和四分之一波片(QWP)用于控制偏振状态并产生圆偏振光,包括物镜在内的显微镜部分舞台上的镜头(OL)、QWP、LP、镜头和sCMOS相机用于放大通过超透镜(图中缩写为ML以表达简短术语)的图像并沿z轴进行机械扫描。在这部分中,舞台上的一对LP和QWP用作分析器,滤除与入射光相反的圆偏振光。为了清楚地展示UV超透镜的聚焦能力,我们将z范围从22毫米裁剪到26毫米,实验透镜的焦距与理论透镜的焦距匹配得很好。此外,我们还测量了制造的超透镜的绝对聚焦效率(定义为聚焦光量与入射光量之比),以评估其性能(图 5)。在 4 英寸晶圆上制造的 UV 超透镜的平均聚焦效率为 45.1%,标准偏差为 7.5%。由于晶圆内每个位置的蚀刻速度、硬掩模高度和邻近效应不同,测量的效率会发生变化。图 4b 显示了理论和实验上的归一化焦点和焦平面的线扫描图。半高全宽 (FWHM) 值约为 1.2 μm,测量的艾里斑和理论艾里斑非常相似,证明了我们的 UV 超透镜的衍射极限性能。计算出的斯特列尔比为 0.954,这表明我们的超透镜类似于完美的衍射极限系统。调制传递函数描述了使用透镜解析的空间频率,如补充说明 15 所示。为了确认我们的 UV 超透镜的成像能力,我们使用 1951 年美国空军负目标进行成像表征。具体来说,我们选择在第 6 组和第 7 组中显示元素 1 至 6(图 4c)。图4c中的红色和蓝色垂直虚线显示了成像目标的分辨能力。图4d和e显示了通过垂直切割获得的归一化强度图,实验设置如图4g所示。
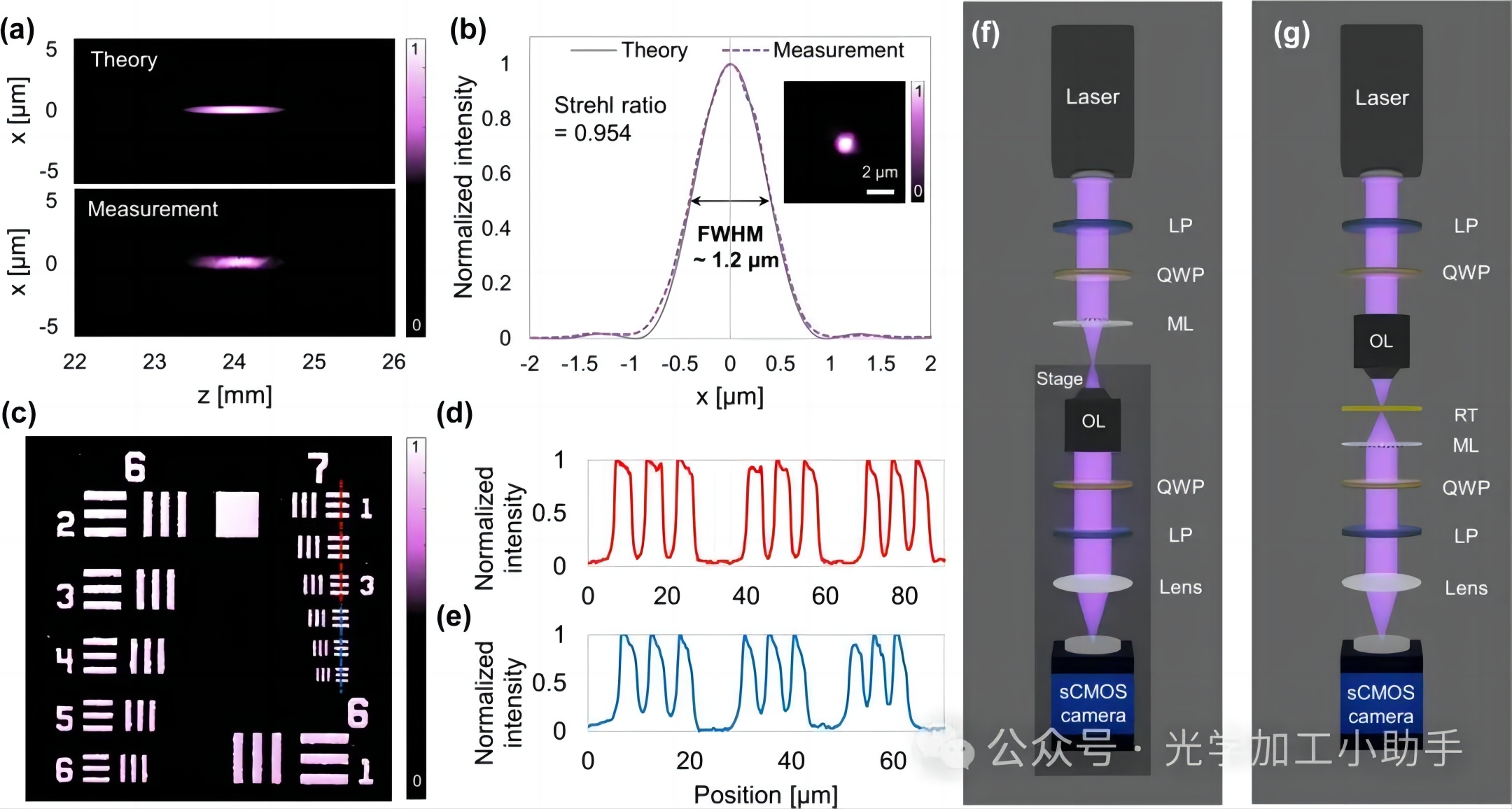
图 4. 所制造的 UV 超透镜的光学特性。(a) x-z 平面上标准化的模拟和测量的强度分布。(b) 模拟和测量焦点的归一化横截面强度分布。灰色虚线是模拟数据,紫色实线是测量数据。实验测量的焦点的归一化强度分布显示在右上方。(c) 使用超透镜拍摄焦平面中物体的 1951 年美国空军负分辨率目标图像。(d) 对应于图 4c 中红色虚线的目标第 7 组元素 1 至 3 的垂直切割的归一化强度。(e) 对应于图 4c 中蓝色虚线的目标第 7 组元素 4 至 6 的垂直切割的归一化强度。(f) 聚焦测试的光学装置示意图。(g) 对 1951 年美国空军分辨率目标负片进行成像的光学装置示意图。
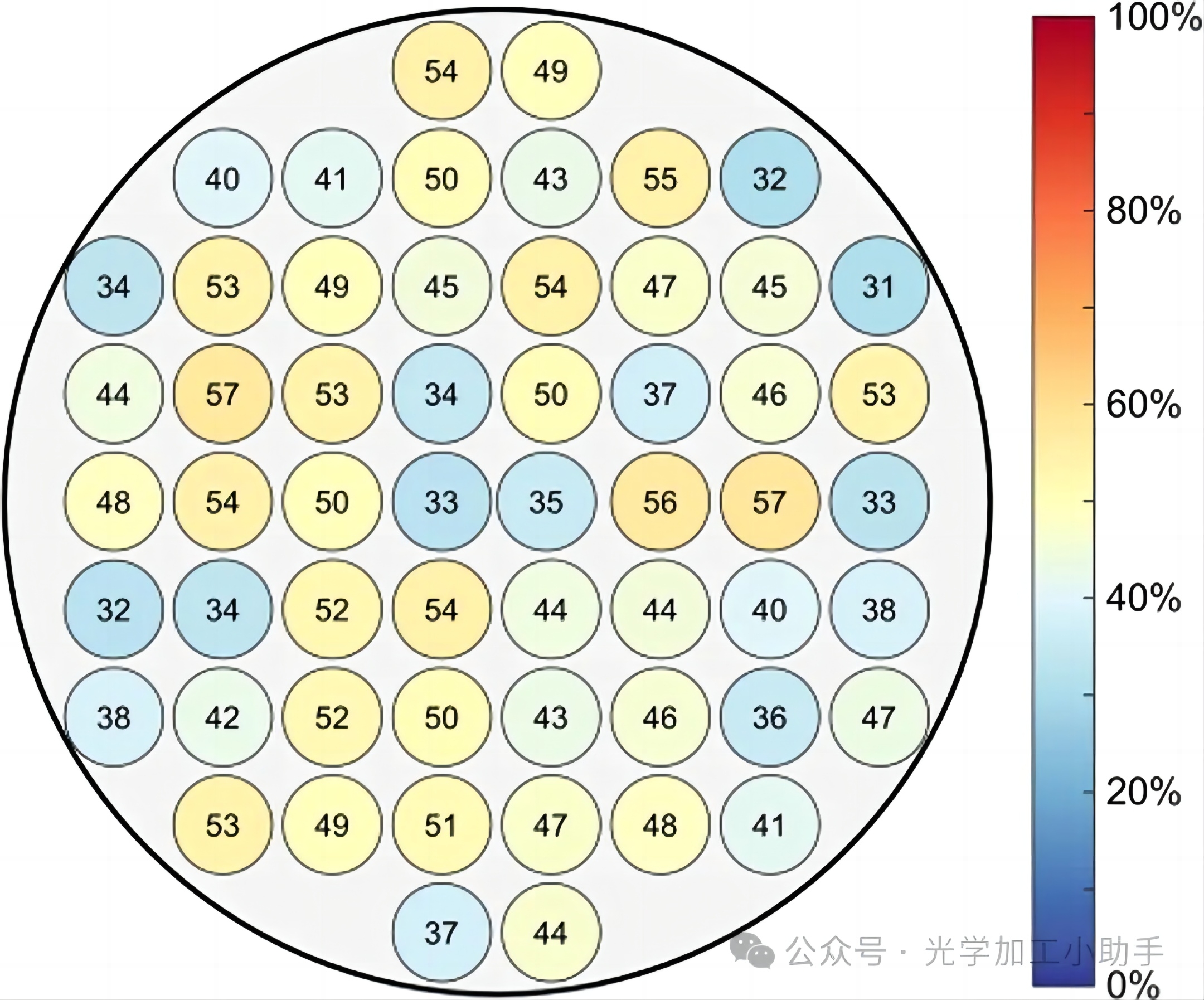
图 5.测量在 4 英寸晶圆上制造的超透镜的绝对聚焦效率。
讨论
总之,我们利用高速电子束光刻、ArF光刻、NIL和ALD成功批量生产了厘米级UV超透镜。高速电子束光刻用于在厘米级上对单个掩模版进行图案化,而ArF光刻用于制造主印模,其中掩模版图案以阵列形式复制在8英寸晶圆上。晶圆级 NIL 能够以极低的成本和高吞吐量重复复制主印模。最后,ALD用于ZrO 2 -聚合物杂化材料,其转化效率显着提高。值得注意的是,与块状材料不同,混合材料具有可扩展性且易于制造,并且其性能与块状材料相似。与之前使用纳米颗粒嵌入树脂压印超透镜的作品不同,这项工作使用纯传统压印树脂来创建纳米结构。这种方法具有易于图案转移、高产量和适合大面积加工等优点。所制造的UV超透镜在325 nm的目标波长下实现了48.5%的聚焦效率,并且通过最小化制造误差可以进一步提高效率。所制作的超透镜的艾里斑测量值与理想艾里斑一致,并且通过对1951年美国空军负目标进行成像验证了所制作的超透镜的高成像性能。我们相信,我们的方法将成为紫外超透镜商业化的根本一步,并提供一种用超光学取代传统紫外光学的好方法。
方法
折射率测量:使用椭圆偏振光谱仪(M-2000,J.A.Woollam)测量ZrO 2 薄膜和压印树脂的折射率。使用柯西模型测量并拟合 s 和 p 分量之间的幅度比和相位差。
数值模拟:使用基于有限元的商业软件(COMSOL Multiphysics 6.0)来计算元原子的光学性质。所有模拟均在周期性边界条件下的 xyz 空间内进行。
掩模版的制造:使用高功率电子束光刻(JBX系列,JEOL Ltd.)使用正性光致抗蚀剂(FEP系列,Fujifilm Ltd.)来制造用于超透镜的掩模版。使用四甲基铵 (TMAH) 来显影曝光图案。使用电子束蒸发器沉积 70 nm 厚的硅化钼层。
主模的制造:ArF光刻(XT-1900Gi,ASML)用于使用正性光刻胶(FEP系列,Fujifilm Ltd.)将掩模版图案转移到Si基板上。TMAH 用于开发曝光图案。
纳米压印光刻:母模涂有用于脱模 h-PDMS 的液相自组装单层 (SAM) 溶液。h-PDMS 使用 3.4 g 乙烯基甲基硅氧烷(VDT-731,Gelest)、18 μL 铂催化剂(SIP6831.2,Gelest)、0.1 g 调节剂(2,4,6,8-四甲基-2,4)制备,6,8-四乙烯基环四硅氧烷,Sigma-aldrich)、2g甲苯和1g固化剂(HMS-301,Gelest)。PDMS 是通过将 PDMS(Sylgard 184 A,Dow Corning)与固化剂(Sylgard 184B,Dow Corning)混合来制备的。将含氟表面活性剂((十三氟-1,1,2,2-四氢辛基)三氯硅烷)通过在130℃下汽化涂覆10分钟的方式涂覆在软模具上,形成防粘层。使用UV固化树脂(MINS-311RM,Minuta Tech)作为压印树脂。样品在紫外线照射下以 2 bar 的压力进行压制(IMDE04-A01,Jungang Automation Technology)。
反应离子蚀刻条件:O 2 进行反应离子蚀刻(Plasma Therm 790系列),在功率200W、压力10mTorr、操作时间5分钟下蚀刻固化树脂的残留层。
光学测量:使用显微镜表征超透镜的焦点。使用 325 nm 激光(XRM1 紫外(325 nm)非偏振 He-Cd 激光系统)产生入射光。使用两个 LP(Edmond Optics,UV 线栅线性偏振器 17-153)和两个 QWP(Thorlabs AQWP05M-340)来产生和过滤圆偏振光。焦点通过 OL (Thorlabs LMU-15X-UVB) 放大,并使用 sCMOS 相机 (Pco panda 4.2 BI UV) 捕获。我们以 0.01 毫米的间隔测量了 400 个 z 扫描图像,并使用电动平移台 (Thorlabs DDS100)。负分辨率目标(Thorlabs R3L1S4N)用于成像测试。
ZrO 2 沉积条件:使用等离子体增强 ALD 站(NexusBe,Nexus Plaminar 系列)沉积 ZrO 2 薄膜。四(二甲氨基)锆(TDMAZr)用作Zr前体,氧等离子体(350W,1托)用作反应物。沉积过程包括 3 秒 TDMAZr 脉冲、30 秒氩气吹扫、10 秒氧等离子体暴露和 30 秒氩气吹扫,温度为 ALD 室,温度为 90 °C。每个周期的生长率为 2.8 Å。