本文分享一篇文章关超低损耗氮化光波导制造的基础,具有极低损耗和低吸收(405-2350nm)波段的Si3N4的材料的制造流程。本文的作者为上海交大的纪幸辰老师,小编看完这边文章后,被纪老师在超低损耗氮化硅光波导方向的研究成果所折服,因此分享给大家,知识传递才有价值,因此小编将他分享给更多的人。(在此感谢老师的无私指导)
本文的特点:
采用 PECVD技术来沉积Si3N4薄膜
一般fab厂都有PECVD设备,且由于LPCVD为高温沉积,因此得出来的膜层具有较大的应力,无法做的很厚(可以通过多次退火实现),PECVD由于为等离子增强低温沉积,因此得出来的膜层质量相对于LPCVD有较大的损耗
本文作者采用PECVD+CMP+RTA/炉退火退火技术,有效的优化了PECVD得出的Si3N4质量,同时也有效的降低了损耗。
4.Si3N4的表面膜层的粗糙度影响波导的损耗--需要CMP,Si3N4的膜层的致密性影响波导的损耗--需要退火。(作者在文中提供了退火前后,cmp前后的对比数据)
本文专业性较强,小编写的如果有不对的地方,敬请指出
划重点:
针对氮化硅光波导--我们可以提供
1.Si+Sio2(湿法热氧)+Si3N4(PECVD/LPCVD)晶圆(LPCVD最大12寸)
2.CMP+快速退火
3.一站式服务
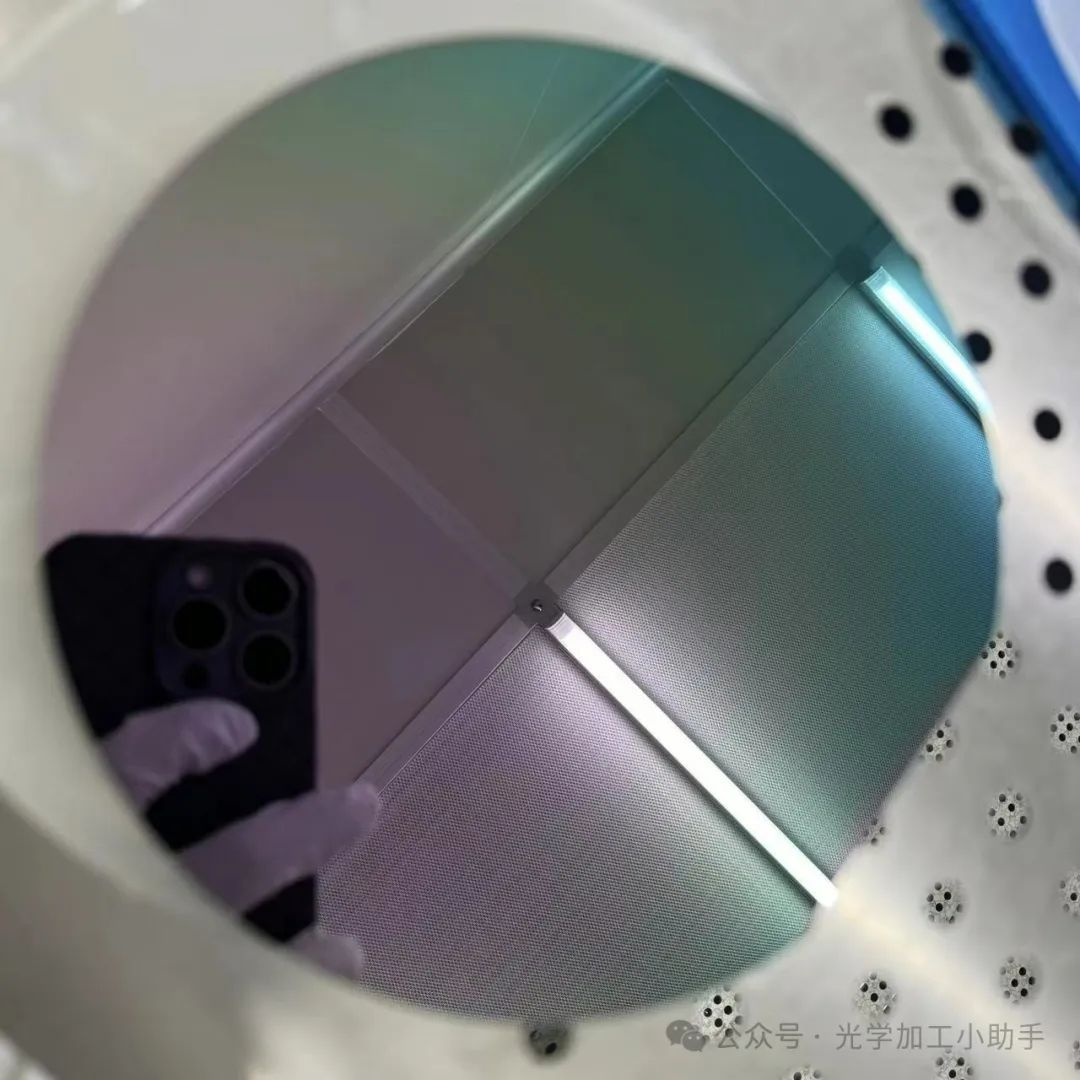
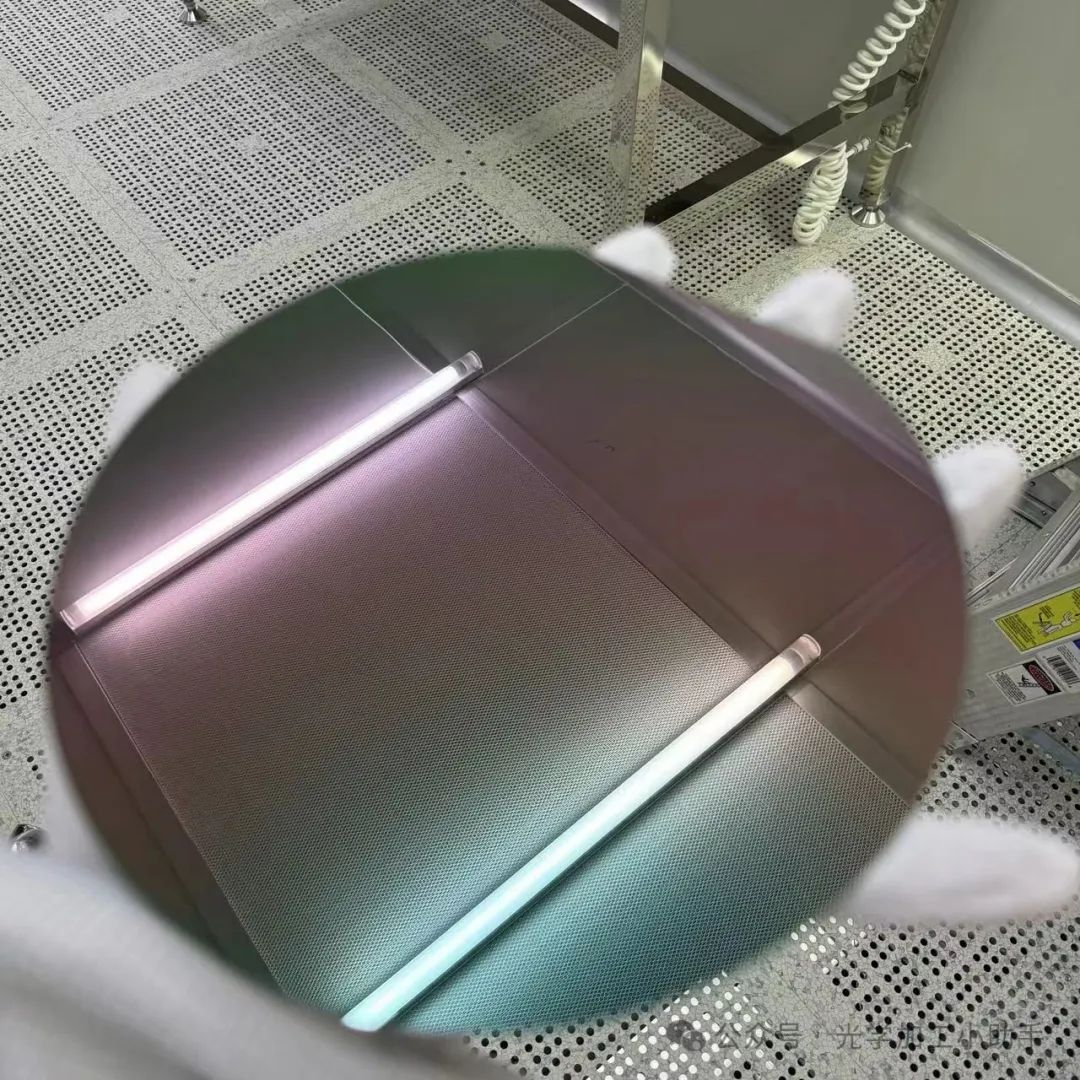
我们为客户提供晶圆(硅晶圆,玻璃晶圆,SOI晶圆,GaAs,蓝宝石,碳化硅(导电,非绝缘),Ga2O3,金刚石,GaN(外延片/衬底)),镀膜方式(PVD,cvd,Ald,PLD)和材料(Au Cu Ag Pt Al Cr Ti Ni Sio2 Tio2 Ti3O5,Ta2O5,ZrO2,TiN,ALN,ZnO,HfO2。。更多材料),键合(石英石英键合,蓝宝石蓝宝石键合)光刻,高精度掩模版,外延,掺杂,电子束直写等产品及加工服务(请找小编领取我们晶圆标品库存列表,为您的科学实验加速。
EBL代工(非晶硅,TiO2,SiO2,GaN,Ta2O5,Al,Au,GaAs(PCSEL)...更多材料体系),母版制作,铬版销售,纳米压印,DUV光刻超结构服务,
可见光近红外波段超透镜仿真设计
请联系小编免费获取原文,也欢迎交流半导体行业,工艺,技术,市场发展!
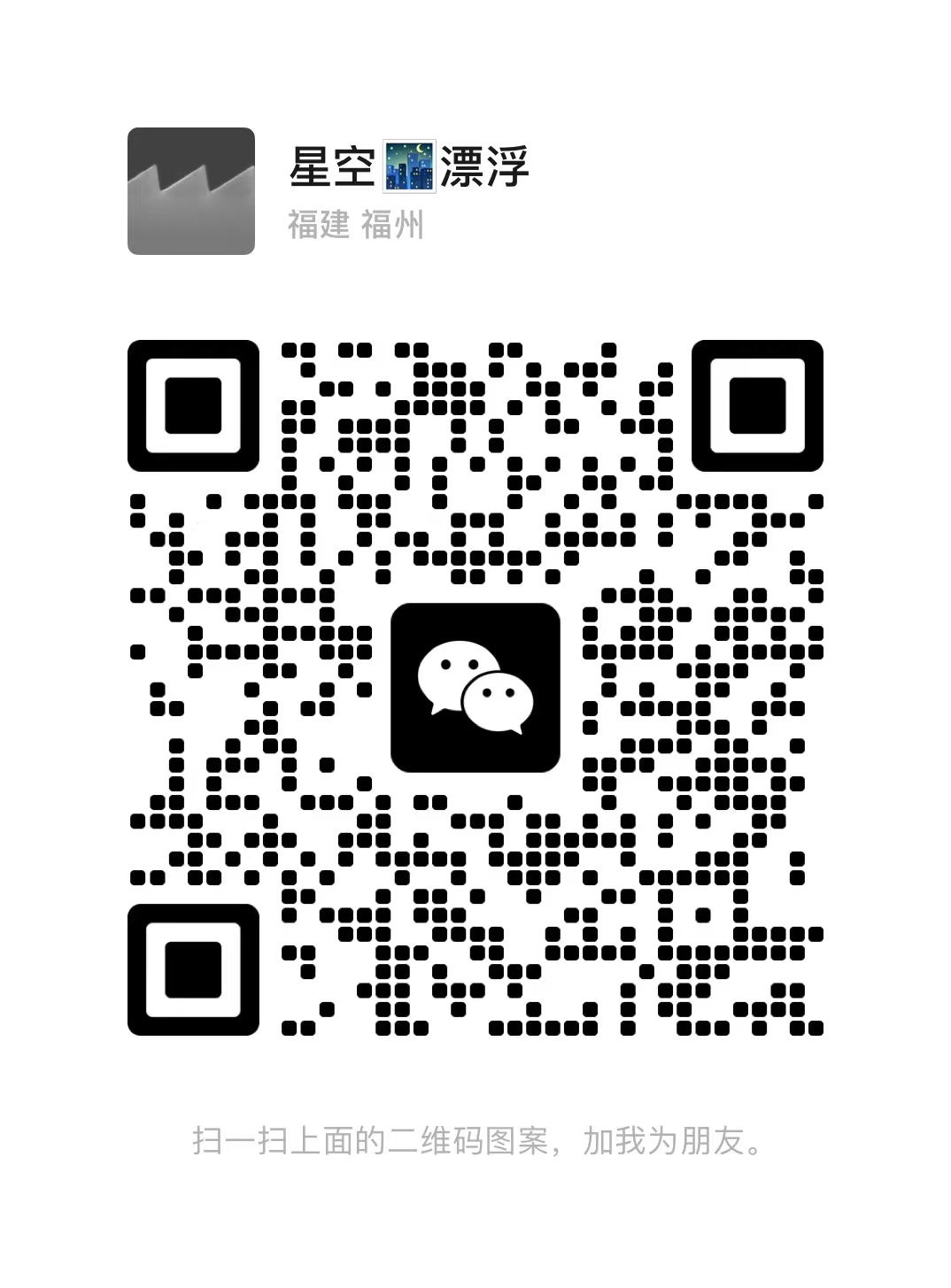
基于与铸造厂兼容的沉积膜的超低损耗氮化硅光子学
摘要:代工厂使用的氮化硅 (Si3N4) 光子器件的制造工艺需要低温沉积,这通常会导致高传播损耗。在这里,
PECVD+CMP:我们展示了仅通过降低波导表面粗糙度,使用代工厂兼容工艺即可实现低至 0.42 dB/cm 的传播损耗。
PECVD+CMP+RTA/炉退火:通过使用快速热退火 (RTA) 和炉退火对制造的器件进行后处理,我们分别实现了低至 0.28 dB/cm 和 0.06 dB/cm 的传播损耗。
这些低损耗与使用高温、高应力 LPCVD 膜的传统器件相当。我们还调整了器件的色散,并证明这些器件可用于线性和非线性应用。展示了低阈值参数振荡、宽带频率梳和窄线宽激光器。我们的工作证明了基于代工厂的可扩展光子系统的可行性。
1. 简介
迄今为止,
超低损耗氮化硅 (Si3N4) 波导和谐振器几乎完全使用高温沉积的薄膜进行演示,而代工厂则主要依赖低温沉积的 Si3N4 薄膜。
高温沉积采用低压化学气相沉积 (LPCVD),而低温沉积采用等离子增强化学气相沉积 (PECVD)。
PECVD Si3N4 是代工厂中最常用的薄膜,用作绝缘体或化学屏障层,然而,这些薄膜的高传播损耗限制了它们在光子学中的应用。由于需要高温和高薄膜应力,LPCVD Si3N4 不用于代工厂。因此,降低 PECVD Si3N4 光子器件中的损耗对于将光子器件与电子设备集成至关重要,这可用于实现高性能、可扩展的系统并实现系统级创新[1]。
此前,人们曾尝试通过化学方法改变薄膜成分来降低 PECVD Si3N4 薄膜的损耗[2–5]。通过降低沉积过程中的铵浓度,损耗已降至 1.5 dB/cm[2]。然而,这些损耗对于大多数光子应用来说仍然太高。研究人员还用氘代前体替代了传统前体,以降低薄膜损耗,损耗已降至 0.3 dB/cm[6]。然而,这些方法需要特殊的前体和沉积工具,而这些在铸造厂并不常见。
2. 薄膜沉积和波导制造
这里我们展示了通过物理降低波导表面粗糙度,在标准 PECVD 工艺中可以实现低损耗。制造过程示意性地如图 1 所示。我们使用 PECVD 在 350°C 下一步将 Si3N4 沉积到热氧化的 4 英寸硅晶片上。用于沉积的气体是氮气 (N2: 1425 sccm) 稀释的硅烷 (SiH4: 20 sccm) 和纯氨 (NH3: 30 sccm) 的混合物,工艺压力为 1900 mTorr。等离子体频率在功率为 200 W 的高频 (13.56 MHz) 和功率为 160 W 的低频 (100 kHz) 之间交替。两个频率的持续时间分别为 8 秒和 12 秒。上述参数确保 Si3N4 薄膜的沉积具有非常低的薄膜应力和高均匀性。测试晶圆上的 Si3N4 薄膜测量到的应力为 93.4 MPa,拉伸应力比高温沉积的 LPCVD Si3N4 薄膜低一个数量级以上。低应力使我们能够沉积更厚的薄膜而不会出现任何开裂。
16
基于与铸造厂兼容的沉积膜的超低损耗氮化硅光子学
摘要:代工厂使用的氮化硅 (Si3N4) 光子器件的制造工艺需要低温沉积,这通常会导致高传播损耗。在这里,
PECVD+CMP:我们展示了仅通过降低波导表面粗糙度,使用代工厂兼容工艺即可实现低至 0.42 dB/cm 的传播损耗。
PECVD+CMP+RTA/炉退火:通过使用快速热退火 (RTA) 和炉退火对制造的器件进行后处理,我们分别实现了低至 0.28 dB/cm 和 0.06 dB/cm 的传播损耗。
这些低损耗与使用高温、高应力 LPCVD 膜的传统器件相当。我们还调整了器件的色散,并证明这些器件可用于线性和非线性应用。展示了低阈值参数振荡、宽带频率梳和窄线宽激光器。我们的工作证明了基于代工厂的可扩展光子系统的可行性。
1. 简介
迄今为止,
超低损耗氮化硅 (Si3N4) 波导和谐振器几乎完全使用高温沉积的薄膜进行演示,而代工厂则主要依赖低温沉积的 Si3N4 薄膜。
高温沉积采用低压化学气相沉积 (LPCVD),而低温沉积采用等离子增强化学气相沉积 (PECVD)。
PECVD Si3N4 是代工厂中最常用的薄膜,用作绝缘体或化学屏障层,然而,这些薄膜的高传播损耗限制了它们在光子学中的应用。由于需要高温和高薄膜应力,LPCVD Si3N4 不用于代工厂。因此,降低 PECVD Si3N4 光子器件中的损耗对于将光子器件与电子设备集成至关重要,这可用于实现高性能、可扩展的系统并实现系统级创新[1]。
此前,人们曾尝试通过化学方法改变薄膜成分来降低 PECVD Si3N4 薄膜的损耗[2–5]。通过降低沉积过程中的铵浓度,损耗已降至 1.5 dB/cm[2]。然而,这些损耗对于大多数光子应用来说仍然太高。研究人员还用氘代前体替代了传统前体,以降低薄膜损耗,损耗已降至 0.3 dB/cm[6]。然而,这些方法需要特殊的前体和沉积工具,而这些在铸造厂并不常见。
2. 薄膜沉积和波导制造
这里我们展示了通过物理降低波导表面粗糙度,在标准 PECVD 工艺中可以实现低损耗。制造过程示意性地如图 1 所示。我们使用 PECVD 在 350°C 下一步将 Si3N4 沉积到热氧化的 4 英寸硅晶片上。用于沉积的气体是氮气 (N2: 1425 sccm) 稀释的硅烷 (SiH4: 20 sccm) 和纯氨 (NH3: 30 sccm) 的混合物,工艺压力为 1900 mTorr。等离子体频率在功率为 200 W 的高频 (13.56 MHz) 和功率为 160 W 的低频 (100 kHz) 之间交替。两个频率的持续时间分别为 8 秒和 12 秒。上述参数确保 Si3N4 薄膜的沉积具有非常低的薄膜应力和高均匀性。测试晶圆上的 Si3N4 薄膜测量到的应力为 93.4 MPa,拉伸应力比高温沉积的 LPCVD Si3N4 薄膜低一个数量级以上。低应力使我们能够沉积更厚的薄膜而不会出现任何开裂。
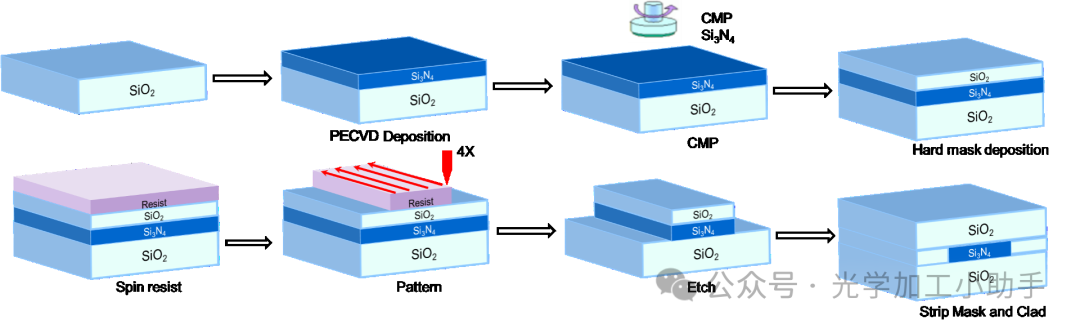
图 1. 我们的低温 PECVD Si3N4 制造工艺示意图。此处的工艺步骤与 CMOS 电子产品完全兼容。
我们基于沉积的 PECVD 膜设计了高限制波导,以实现强色散工程。从图 2 中可以看出,强模式与顶面重叠,PECVD 膜的粗糙度可达几纳米[7,8]。
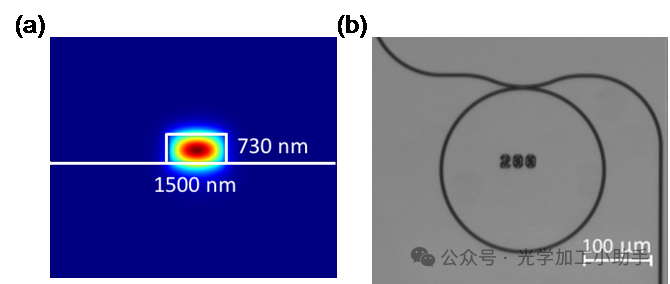
图 2. 制造的器件的模式模拟和显微镜图像。(a)730 nm 高和 1500 nm 宽的波导的模式模拟,显示该模式在我们选择的几何形状中受到高度限制。(b)115 µm 半径环形谐振器的顶视图光学显微镜图像。
为了减少 PECVDSi3N4 顶面的散射,我们使用化学机械平坦化 (CMP) 来平滑表面,因为粗糙度通常会导致高损耗。我们在图 3 中展示了抛光步骤之前和之后的原子力显微镜 (AFM) 扫描。均方根 (RMS) 粗糙度从抛光前的 1.36 nm 降低到抛光后的 0.20 nm。为了降低侧壁的粗糙度并保护抛光的顶面,我们在 CMP 之后使用 PECVD 沉积的 SiO2 硬掩模,并使用氧气流量更高的干法蚀刻工艺。事实证明,这种蚀刻工艺可以大大减少蚀刻过程中的聚合过程并降低粗糙度[9]。我们使用 ma-N 2403 光刻胶通过电子束光刻对器件进行图案化,并使用多通道写入算法进一步降低光刻本身造成的侧壁粗糙度[9,10]。最后,我们用 PECVD 沉积的 2 μm SiO2 覆盖器件,以保护波导。制造的器件由半径为 115 μm、高度为 730 nm、宽度为 1500 nm 的谐振器组成,这些谐振器与相同宽度和高度的波导耦合。这些尺寸确保了高限制性。
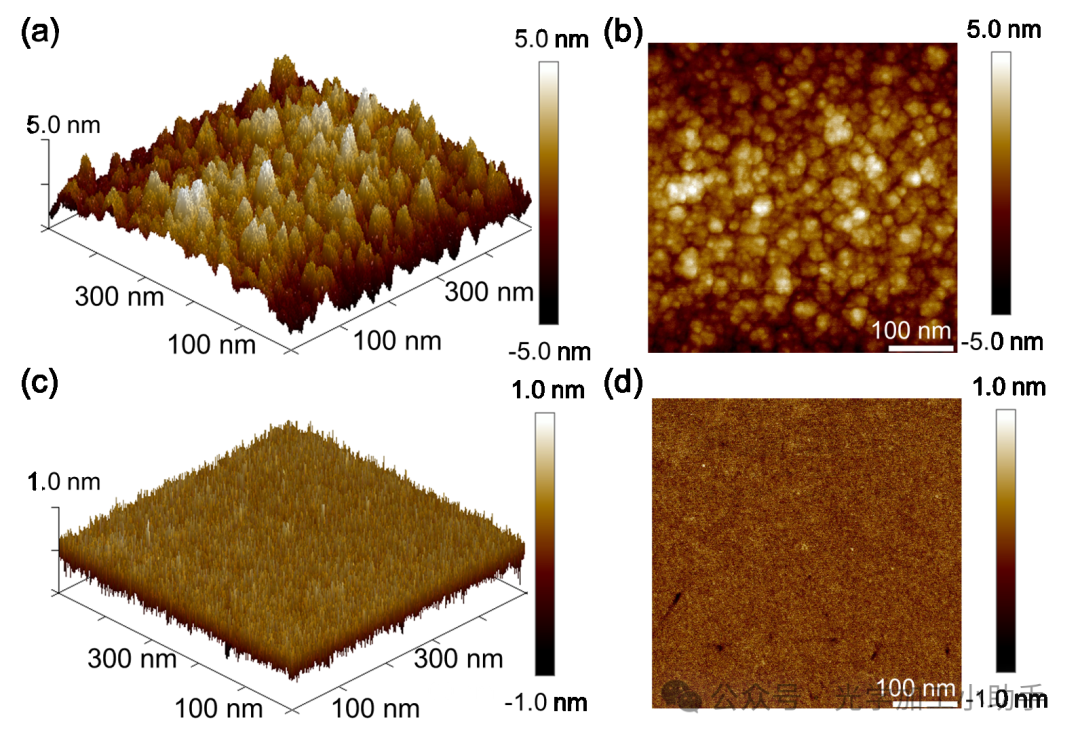
图 3. PECVDSi3N4 顶面的 AFM 测量。(a) CMP 之前顶面的 3D AFM 扫描,RMS 粗糙度为 1.36 nm,相关长度为 27.6 nm。(b) CMP 之前 Si3N4 顶面的 2D 图像,缩放至 -5.0 –5.0 nm,RMS 粗糙度为 1.36 nm。(c) CMP 之后 Si3N4 顶面的 3D 图像,RMS 粗糙度为 0.20 nm,相关长度为 2.96 nm。(d) CMP 之后 Si3N4 顶面的 2D 图像,缩放至 -1.0 –1.0 nm,RMS 粗糙度为 0.20 nm。请注意 (a) 和 (c) 上不同的比例尺。
3. 基本损耗提取与讨论
品质因数是谐振相对于其中心频率的锐度的量度。它表示谐振器存储能量的能力,可以写成[11,12]:

式(1)中定义的品质因数为加载品质因数,腔体的固有品质因数与传输损耗直接相关,可写为[13,14]:

Tm 是谐振归一化传输最小值,±符号对应于欠耦合和过耦合条件。图 4 显示了用于测量品质因数和频率梳生成的实验装置的示意图。我们在此制造和测量的谐振器的高度为 730 nm,宽度为 1500 nm,弯曲半径为 115 µm。我们测量的固有品质因数为 724,000,对应的传播损耗为 0.42 dB/cm。在图 5(a) 中,我们展示了在宽波长范围内测得的谐振和归一化传输光谱。据我们所知,这是迄今为止在与代工厂兼容的标准 PECVD 薄膜中报告的最低传播损耗。
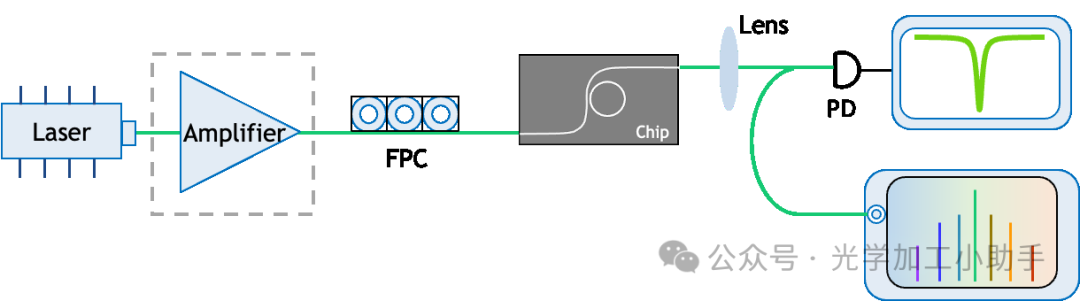
图 4. 测量透射光谱和谐振腔线宽以表征品质因数并产生频率梳的实验装置示意图。FPC:光纤偏振控制器;PD:光电探测器;OSA:光谱分析仪。请注意,透射测量不需要放大器。
为了最大限度地减少表面散射损耗和体积损耗,我们对薄膜进行了快速热退火 (RTA) 后处理。通过 RTA,我们实现了更高的固有品质因数,超过 100 万,相当于 0.28 dB/cm 的传播损耗。RTA 已成功应用于微电子行业,并且与 CMOS 技术特别相关,特别是在植入退火、氧化以及源极和漏极接触结等步骤中[15,16]。该工艺通过驱除结构微孔中捕获的非键合原子和分子氢来减少损耗,并进一步使薄膜致密化[17,18]。我们在 800 °C 下对包覆的器件进行 5 分钟的 RTA。在图 5(b) 中,我们展示了在宽波长范围内测量到的谐振和归一化透射光谱。热预算低于大多数 CMOS 电子产品的容差,可用于进一步降低带有微加热器或掺杂剂的器件的损耗。
我们表明,通过对代工厂兼容器件进行炉内退火后处理(适用于热预算较高的器件),传播损耗可与使用高温、高应力 LPCVD 膜制造的器件相媲美。炉内退火不同于 RTA,温度更高(高于 1000 °C [19–24]),退火时间更长(几个小时)。我们在 1150 °C 的氮气环境中对包覆器件进行 3 小时的退火,没有观察到任何缺陷或裂纹。我们实现了 470 万的品质因数,这相当于 0.06 dB/cm 的传播损耗。在图 5(c) 中,我们展示了在宽波长范围内测量到的谐振和归一化透射光谱。
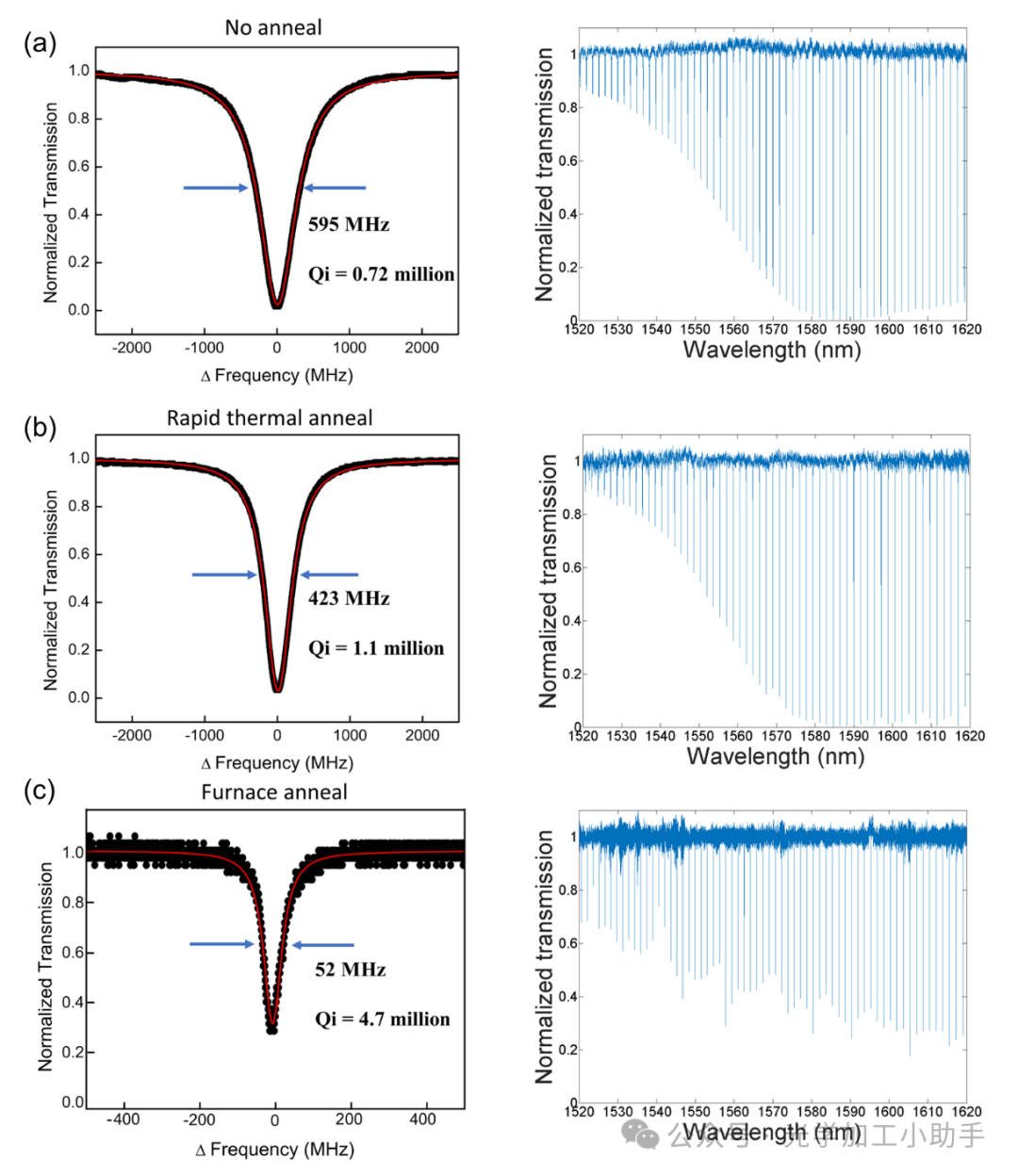
图 5. (a) 未经退火处理的器件在 1600 nm 左右测量到的半峰全宽 (FWHM) 为 595 MHz,并且在很宽的波长范围内测量到归一化透射光谱。(b) 经过快速热退火处理的器件在 1600 nm 左右测量到的半峰全宽 (FWHM) 为 423 MHz,并且在很宽的波长范围内测量到归一化透射光谱。(c) 经过炉退火处理的器件在 1600 nm 左右测量到的半峰全宽 (FWHM) 为 52 MHz,并且在很宽的波长范围内测量到归一化透射光谱。
我们发现,对于制造前的器件,体损耗大于表面散射损耗,可低至 0.33 dB/cm,而对于制造后退火的器件,体损耗与表面散射损耗相当,可低至 0.04 dB/cm。我们通过比较两种不同结构与界面具有不同模式重叠的损耗来提取损耗贡献。h1、h2、h3 分别是两种不同波导宽度下光场与波导芯、顶部和底部表面以及侧壁的重叠[25]。这些参数是使用 FEM 模拟(使用 COMSOL 执行)计算得出的。我们还使用 Payne-Lacey 模型[26]将散射损耗与表面的 RMS 粗糙度 (σ) 和相关长度 (Lc) 关联起来,这两者均从 AFM 测量中提取。这里用于提取损耗贡献的方法与参考文献[9]中使用的方法类似。我们发现,对于模式与界面完全重叠的情况,散射损耗在 SiO2/Si3N4 顶部界面和 Si3N4/SiO2 底部界面处分别为顶部散射~ 0.0002 dB/cm 和底部散射~ 0.0024 dB/cm。不同热处理的表面散射和体积损耗估计值(如表 1 所示)取自下面的公式 3 和公式 4:
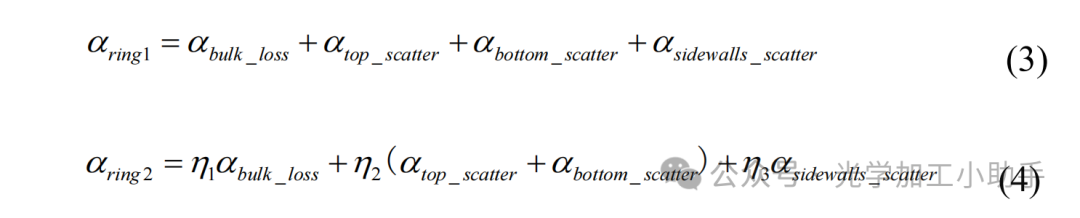
我们发现,经过 RTA 和炉内退火后,体损耗和表面散射损耗均减少了,这表明热处理改善了薄膜的化学和物理性质。从表 1 和公式 3 可以看出,如果消除表面散射损耗,则可以将传播损耗降低至 0.33 dB/cm。通过在 800 °C 下进行 RTA 后处理,可以将传播损耗降低至 0.23 dB/cm。如果在更高温度下进行 RTA 以分解键合氢,则可以进一步降低传播损耗。通过炉内退火后处理,如果消除表面散射损耗,可以将这些器件中的传播损耗降低至 0.04 dB/cm。
表 1. PECVD 薄膜中提取的表面散射和体损耗贡献。
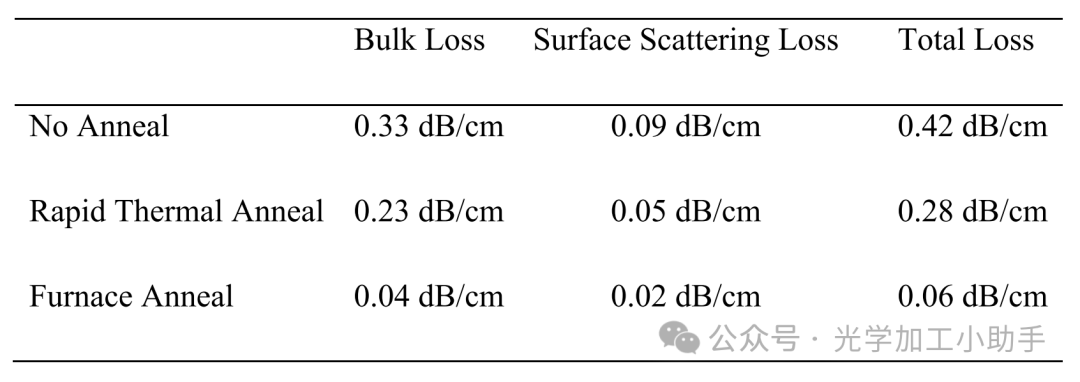
无需任何后加工热处理而制造的结构表现出 87% 的高限制性和 0.42 dB/cm 的低传播损耗。高限制性对于调整波导色散以实现非线性过程中的相位匹配以及更紧密的弯曲是必要的,从而允许大规模光子系统所需的小尺寸。我们将这项工作中实现的限制因子和传播损耗与在代工厂兼容 PECVD 平台中实现的其他最先进工作进行了比较,这些工作无需任何热处理,如图 6 所示[2,3,5,27–
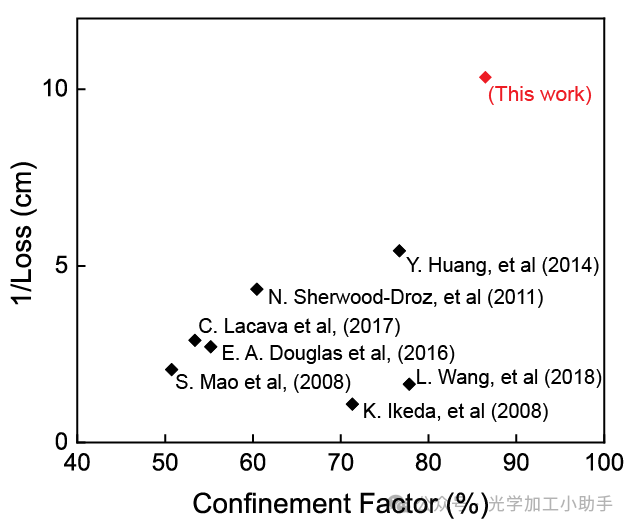
图 6. 本研究与其他基于 PECVD 平台的先进研究相比,实现了损耗和限制。包括本研究在内的所有分数均针对未经任何热处理制造的器件[2,3,5,27–30]。
4. 色散工程
我们表明,可以通过炉内退火进行后处理来调整器件的色散。为了设计色散,我们使用 J.A. Woollam M-2000 和 IR-VASE 仪器,从 200–1690 nm 和 1.7–34 μm 波长范围内的椭圆偏振法推导出 PECVD Si3N4 薄膜的 Sellmeier 方程。我们在图 7(a) 和图 7(b) 中显示了退火前后 200-1750 nm 的测量光谱。我们对 300–2000 nm 波长范围内的光谱进行拟合,以获得炉内退火前后 Si3N4 的以下 Sellmeier 方程。
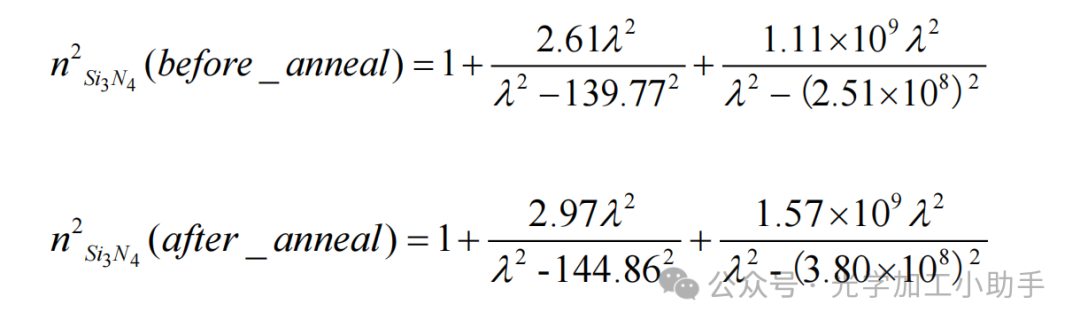
单位为纳米。图 7(c) 显示了基于 Sellmeier 方程的氮化硅谐振器(横截面积为 730 nm x 1500 nm,弯曲半径为 115 µm)退火前后的模拟色散。虚线将异常群速度色散 (GVD) 区域与正常 GVD 区域分开。可以看出,横截面积相同(730 nm x 1500 nm)的器件在退火前表现出正常 GVD,在退火后表现出异常 GVD。
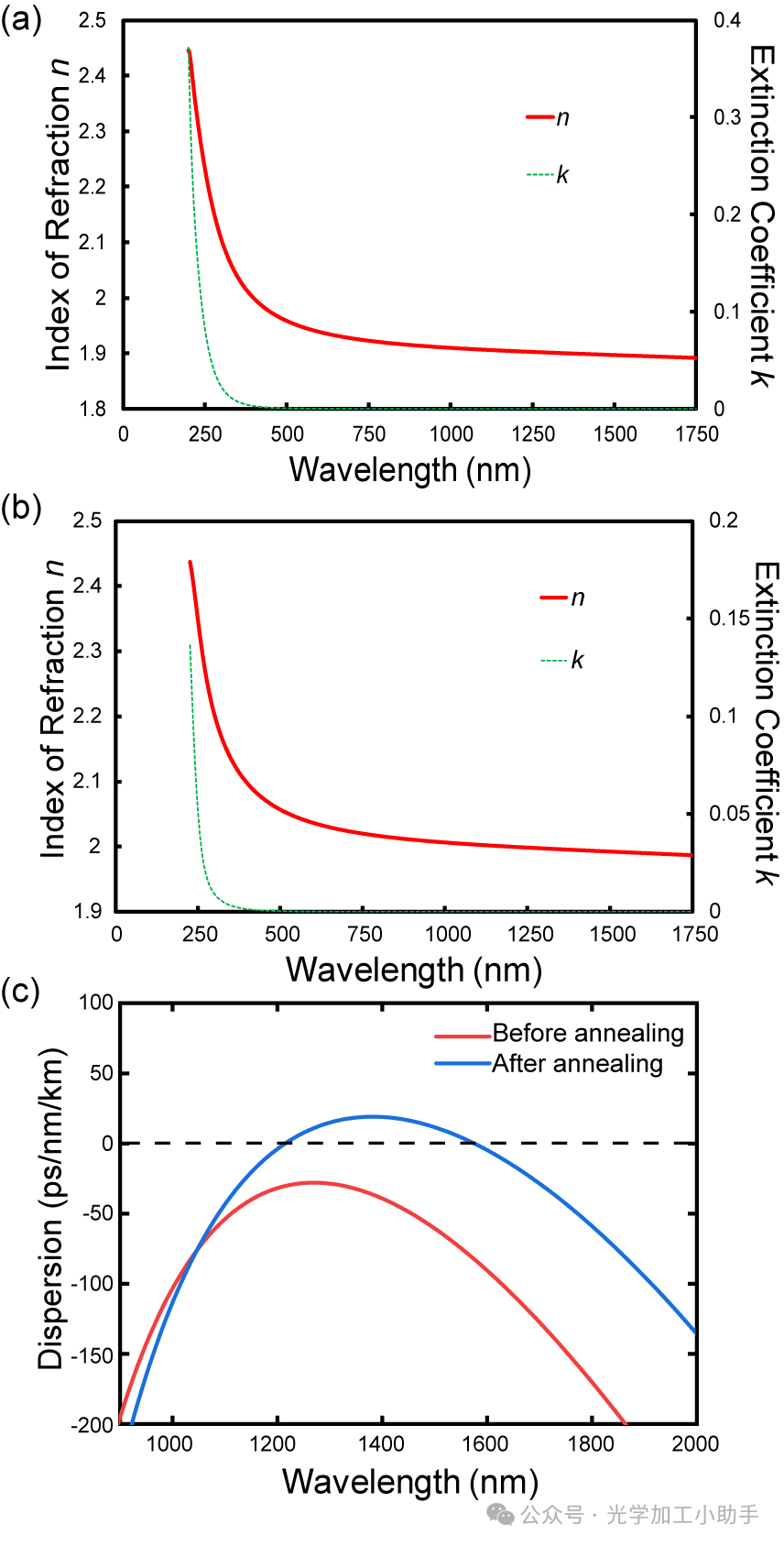
图 7. (a) 退火前波长范围 200–1750 nm 的折射率 n 和消光系数 k。(b) 退火后波长范围 200-1750 nm 的折射率 n 和消光系数 k。(c) 退火前后横截面积为 730 nm ´1500 nm、弯曲半径为 115 µm 的氮化硅环形谐振腔的基本 TE 模式的色散模拟。虚线将异常群速度色散区与正常群速度色散区分开。
5. 线性和非线性应用
我们利用我们设计色散的能力,使用经过炉退火后处理的代工厂兼容设备演示了低阈值参数振荡和频率梳生成。我们展示了梳状生成过程的演变,并在图 8 中观察了使用 1550 nm 泵浦波长向各种梳状状态的转变。随着谐振器中功率的增加,我们看到由于退化的四波混频,主边带在参数增益峰值处形成,如图 8(a) 所示。我们在图 8(b) 中展示了向微型梳状物的转变,最终在图 8(c) 中展示了片上泵浦功率为 202 mW 的宽带频率梳状物的转变。测量的参数振荡阈值低至 3 mW,接近理论极限 2.7 mW。
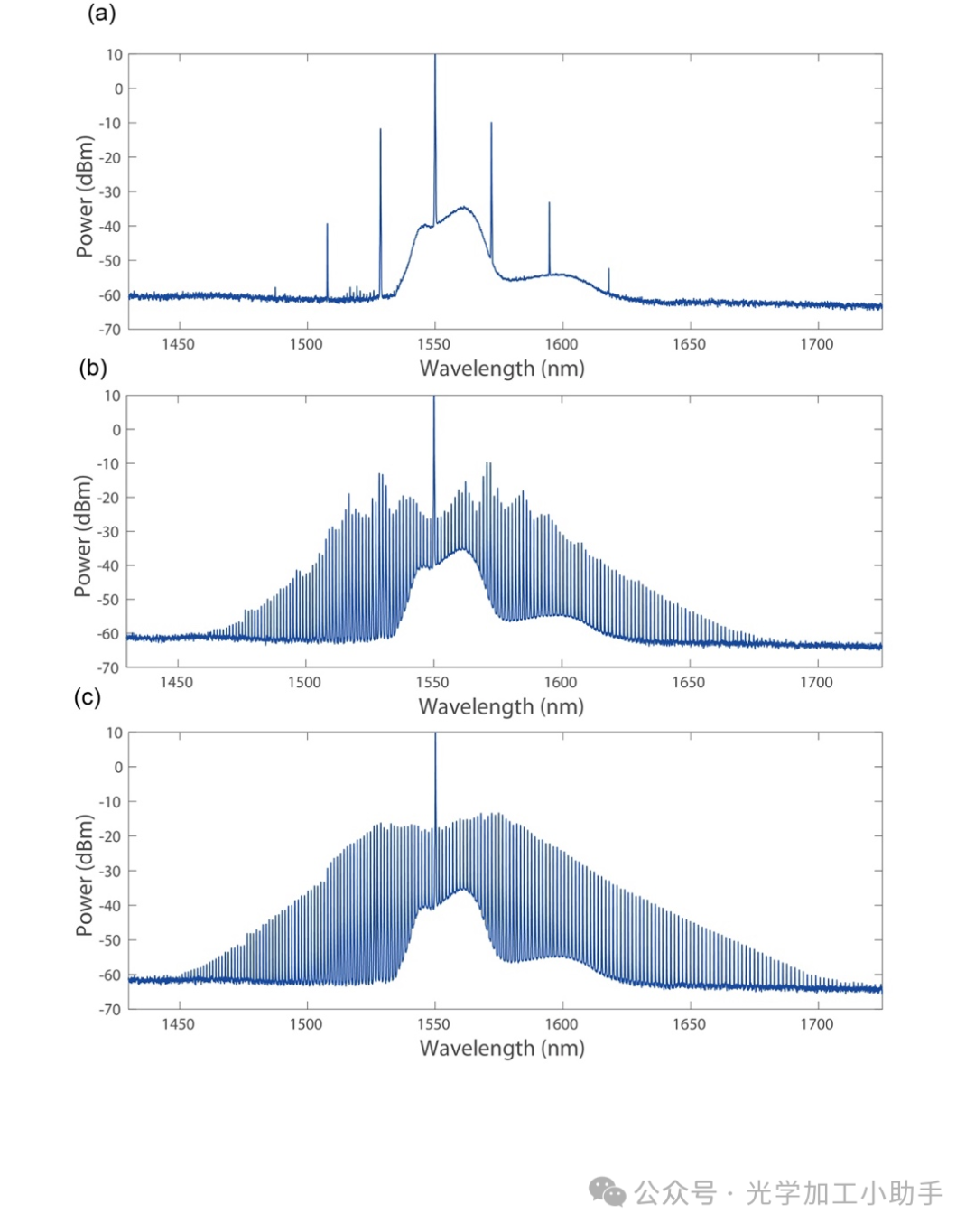
图 8. 频率梳生成过程的演变。(a)由于简并四波混频,在参数增益峰值处形成主边带。(b)微型梳的形成。(c)片上泵浦功率为 202 mW 的宽带克尔频率梳。
我们证明了使用相同的设备可以实现多模法布里-珀罗激光二极管 (FPL) 的模式崩塌。因此,由于 FPL[31] 对耦合损耗的稳定性增强以及高品质因数谐振器的强反馈,我们获得了单波长发射激光。该系统由商用单横模 FPL (Thorlabs FPL1001C) 和高品质谐振器组成,如图 9 所示。
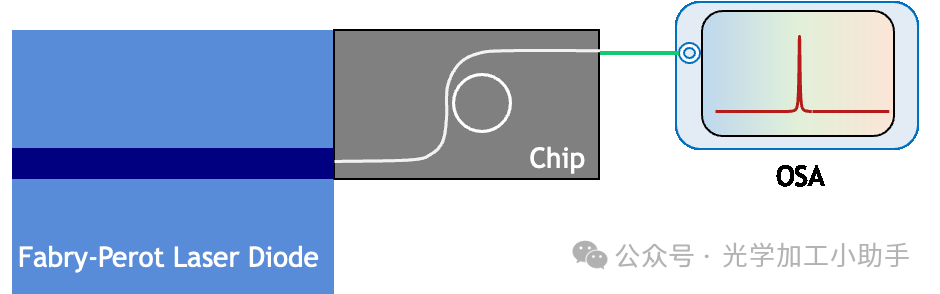
图 9. 激光测量实验装置示意图。商用单横模法布里-珀罗激光二极管 (Thorlabs FPL1001C) 与高品质因数谐振器耦合。激光光谱用光谱分析仪 (OSA) 测量。
来自高品质因数谐振器的反馈信号导致 FPL 激光器自注入锁定,从而产生具有单纵模发射和窄线宽的锁定激光器。图 10 显示了解锁自由运行激光器和锁定激光器的光谱。边模抑制比 (SMSR) 至少为 29 dB,线宽测量值低于光谱分析仪的分辨率极限。我们计算出的固有线宽在 1 -10 kHz 范围内。对于此计算,我们考虑了自由运行激光器的 Schawlow-Townes 线宽和由于自注入锁定导致的线宽减小,其过程与参考文献 [31] 中所述类似。此处设备的耦合结构为倒锥形,可以针对与 FPL 的耦合进行优化,因此可以通过改进耦合实现更好的 SMSR 和更窄的线宽。
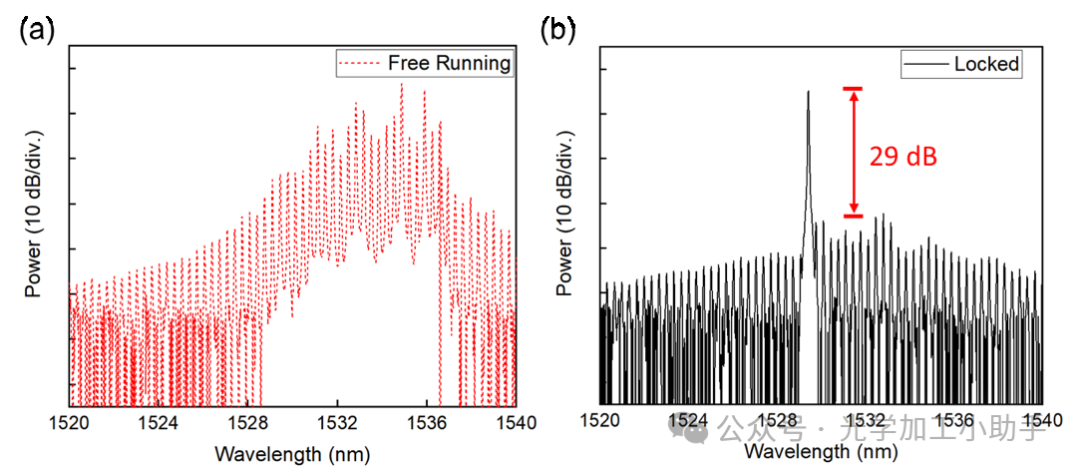
图 10. (a) 未锁定自由运行激光器的光谱。(b) 锁定窄线宽激光器至环形谐振腔的光谱。边模抑制比 (SMSR) 至少为 29 dB。
6. 结论和讨论
我们的工作证明了直接从代工厂获得超低损耗设备的可行性。我们表明,这些代工厂兼容的设备无论是否经过简单的后处理步骤,都可以用于需要超低损耗和色散的线性和非线性应用。展示了低阈值参数振荡、宽带频率梳和窄线宽激光器。提取了我们设备中损耗的基本极限,并证明其与 LPCVD 薄膜中的损耗相当。我们的工作为基于代工厂的可扩展光子系统提供了一条有希望的道路。
最近,在环境大气中以 400℃ 退火的反应溅射氮化硅膜已被证实可实现低至 0.54 dB/cm 的传播损耗[32]。光学频率梳[32]和绝缘体平台上铌酸锂的混合集成[33,34]已成功演示,这使得反应溅射成为另一种有前途的低损耗氮化硅膜生产方法。由于反应溅射装置中的损耗目前受到侧壁粗糙度散射而非 H 键吸收损耗的限制[35],这些装置可以进一步受益于我们在此开发的工艺和技术。
