本文向大家分享一篇关于双光子3d打印的实际案例,设计,制造和测试,就像我们前面提到的那样,双光子打印在微米外径尺度的制造具有无可比拟的优势,同时由于其能够一次打印多个透镜,因此其可以省去微小透镜高精度定位组装的麻烦。下面就看下利用双光子打印的2透镜和3透镜成像系统。
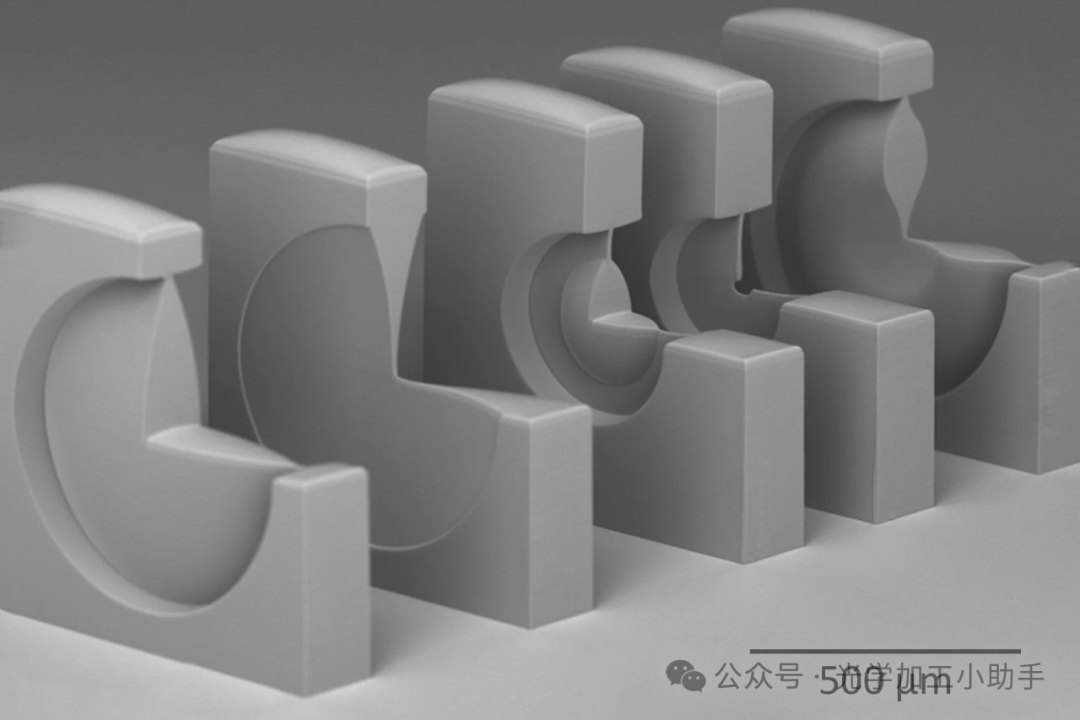
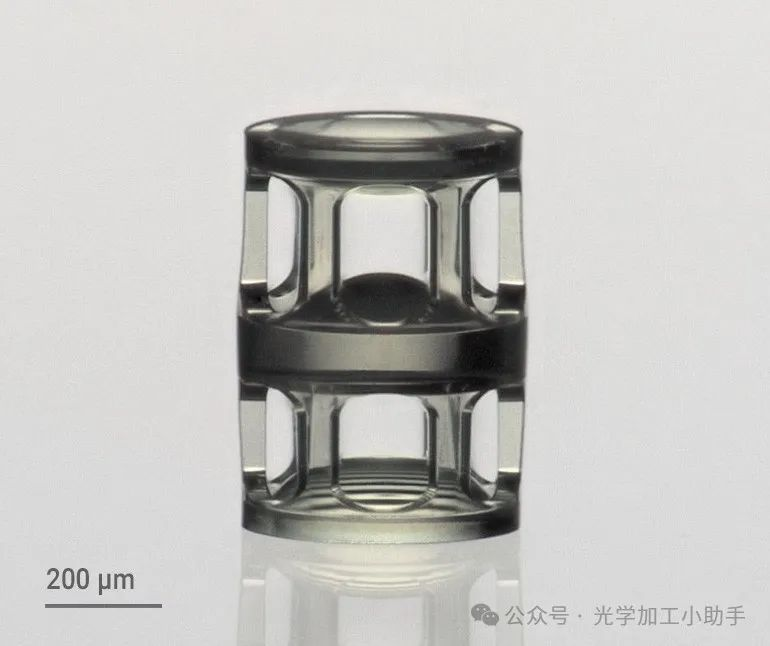
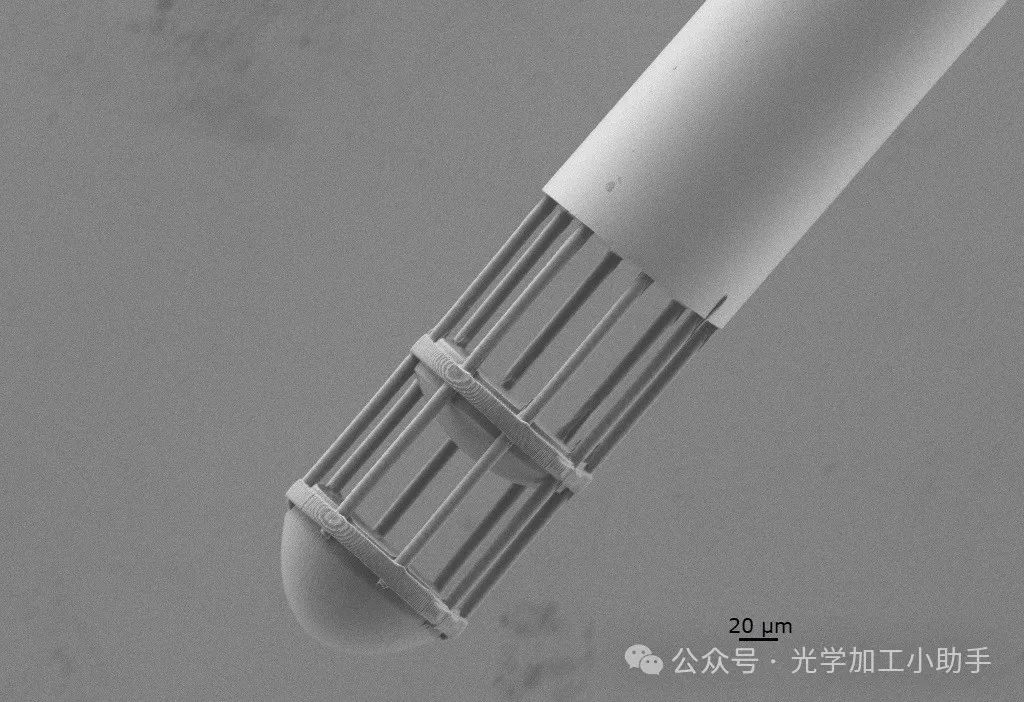
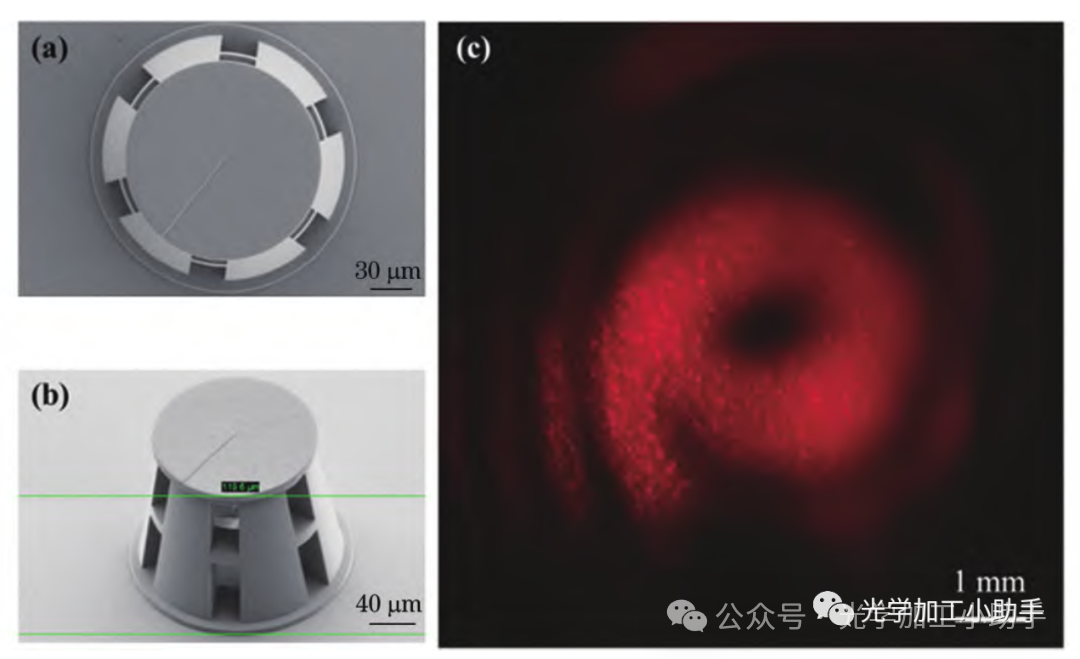
当然,另外一方面,由于是3d打印,不同于传统的微纳加工光学透镜的方式的限制,其可以制造非常复杂的曲面,球面,非球面,自由曲面,大na曲面等。
正如曾经某个单位曾经问的那样,什么是微米尺度复杂光学曲面的最好的加工方式,比对了很多,小编觉得双光子3d打印具有巨大的优势。
划重点(双光子3D打印代工)
在光纤端面亦或其他基底材料上通过双光子3D打印的方式一直是科研工作者研究的关注点,但是由于高精度双光子3D打印的设备极其昂贵,技术也较为前沿,许多科研工作者乏于寻找可靠的,高效率的加工提供商。
小编也很有幸,曾经见到国内有团队已经实战在光纤端面做各种结构,并且得到了客户满意的效果。
因此如果您有需求,可以联系小编为您推荐成熟的双光子3D打印企业,加速您的创新。
如果你也爱好 半导体,光学,光纤,硅光集成等技术及应用,可以添加小编,一起畅聊技术,市场和应用。
看原文请联系小编免费领取

摘要
我们通过灰度光刻技术演示了3D打印的非球面单透态和双透镜微光学元件,并表征和评估了其出色的形状精度和光学性能。典型的双光子聚合 (2PP) 3D 打印工艺会在结构中产生光学表面不希望的步骤。我们利用双光子灰度光刻 (2GL) 来制造无级透镜。为了展示 2GL 工艺,比较了球面和非球面单透镜的聚焦能力。通过迭代设计过程,非球面透镜的表面偏差最小化,并且无法通过共聚焦显微镜测量任何不同的步骤。我们设计、打印和优化直径为 300 μm 的空气间隔双合透镜。优化后,双合体顶部透镜的残余形状偏差小于100 nm,底部透镜的残余形状偏差小于20 nm。我们用 USAF 1951 分辨率测试表检查光学性能,发现分辨率为 645 lp/mm。
1. 引言
从 1990 年代开始 [ 1–5] 2PP 3D 打印成为一种主要的微纳加工方法,因为对更高分辨率 [ 6– 11] 、精度 [ 12, 13] 和最终尺寸 [ 14-16] 的竞争巩固了其在研究中的地位。鉴于高灵活性和分辨率,2PP 3D打印技术服务于许多领域,例如光子晶体 [ 17–19] 、超材料 [ 20–25]、波导 [ 26]、生物细胞支架 [ 27–29]、微针和流体 [ 30, 31]、内窥镜 [ 32, 33] 和量子技术的集成 [ 34–37]。具有工业应用的一个大型研究领域是微光学领域[ 38–41]。在这里,自由曲面光学元件 [ 42– 45]、堆叠镜头 [ 46, 47] 以及镜头阵列 [ 48– 51] 为以前无法达到的尺寸范围内的高分辨率相机提供了机会。3D打印是一种高度通用的制造方法,通常没有设计限制。这对于3D打印光学元件[41,52]尤为重要和有用,因为在透镜设计中可以改变更多的参数,从而允许简单的非球面透镜或复杂的多自由曲面光学元件,如[42-47]和本出版物所述。所有结构都在一个步骤中打印,无需对齐。设计过程从材料参数开始,特别是折射率和色散[53,54]。在尺寸方面,我们选择所有光学元件的外径为300 𝜇m�m ,最小的光学特征在几十微米范围内。光刻胶的收缩通过迭代设计过程得到补偿 [ 16],从而获得高光学性能所需的亚波长形状精度。
2. Fabrication 2. 制造
3D打印镜头是使用市售的Nanoscribe Quantum X(Nanoscribe GmbH Karlsruhe,德国)微纳加工系统制造的。印刷工艺基于双光子吸收,用于聚合液体和透明光刻胶(Nanoscribe IP-S)。780 nmnm 的超短光脉冲由倍频放大的掺铒光纤激光器产生,并由数值孔径 (NA) 为 0.8 的 25 倍放大显微镜物镜聚焦,在小空间区域产生高光强度,其中光刻胶通过双光子吸收硬化,称为体素(体积像素)。可以通过在光刻胶中移动体素来创建任意 3D 结构。体素的运动通过两个振镜控制,这些振镜在 x 和 y 方向上扫描表面。z方向的运动是使用压电平移级实现的。透镜采用浸入式激光光刻印刷模式制造:将一小滴液体抗蚀剂放在玻璃盖玻片上,随后将书写物镜降低到抗蚀剂中。这样,激光束的聚焦就得到了液体光刻胶相对于空气的较高折射率的帮助。在将液体抗蚀剂涂在基材上之前,使用丙酮、异丙醇和氧气等离子体清洁玻璃五分钟,以确保最大的附着力。
在这项工作中,使用、组合和解释两种不同的印刷方法,如下所述。典型的2PP 3D打印工艺如图1(a)所示。首先将 3D 模型切割成水平切片,然后将每个切片剖面线剖面线切成平行剖线。然后,将恒定大小的体素沿剖切中的剖面线移动,直到完成,然后向上移动到下一个剖面。这种方法可以创建任意的 3D 结构,但透镜表面表现出与切片距离大小相当的小垂直步长。减小切片距离会减小步长,但代价是打印时间会延长。第二种方法,即双光子灰度光刻(2GL),当使用与2PP印刷技术相同的切片和影线参数时,通过调制打印过程中的激光功率,提供更好的形状精度。无阶梯表面的制造是激光的功率调制对应于体素的尺寸调制[图1(b)]。利用体素尺寸的这种变化,使聚合体积与设计结构更好地匹配,无需共聚焦显微镜测量任何步骤。由于体素对表面的调制和尺寸适应,与2PP 3D打印相比,我们可以使用2GL使用更大的切片距离,并且仍然达到所需的形状保真度。[ 51 ] 给出了两种制造微光学元件的技术之间的直接比较。在撰写本文时,Nanoscribe Quantum X 的 2GL 仅允许创建 2.5D 形状,不包括悬垂部分。因此,2GL工艺不需要3D模型。相反,灰度图像用作地形图,其中灰度值表示打印区域的厚度。两种打印方法的组合应用于非球面双合体的制造。详情在下面的相应部分中给出。
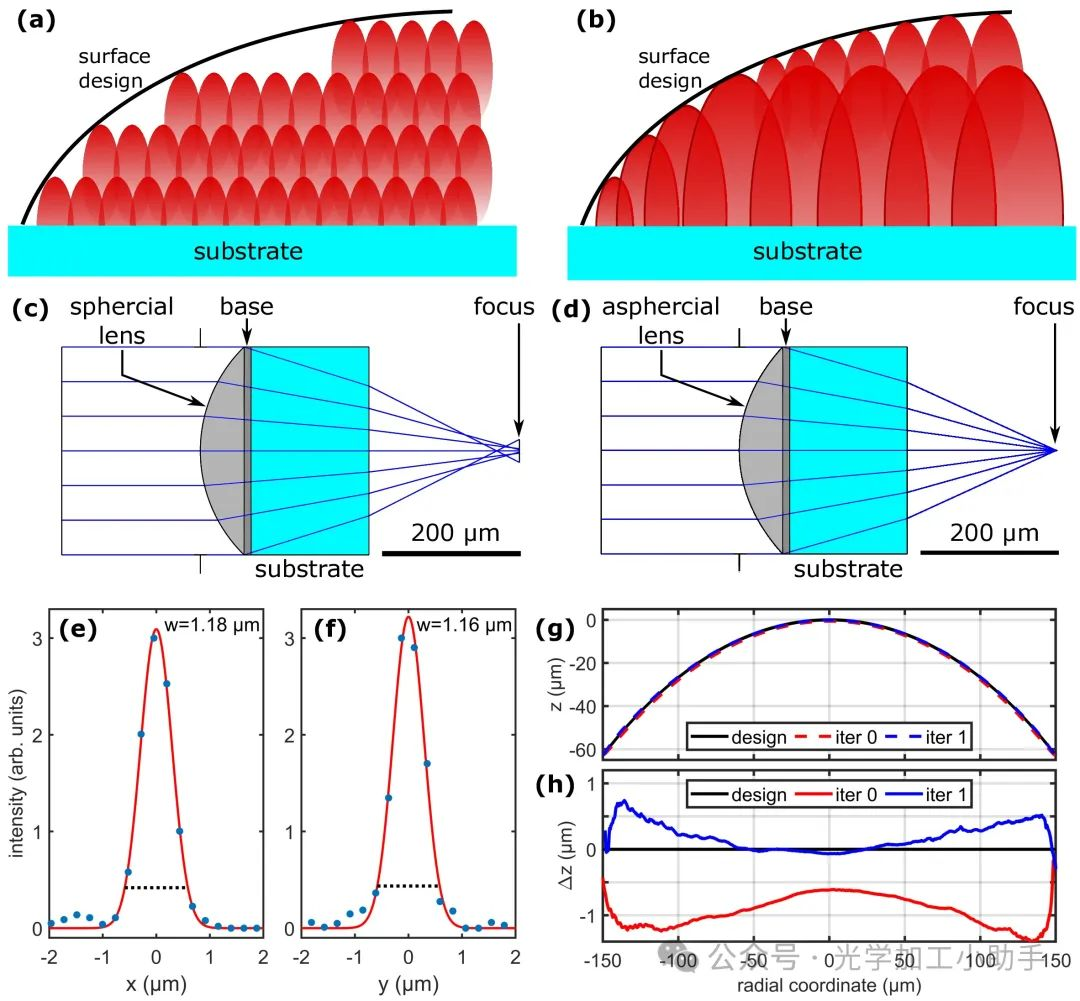
图 1.(a) 双光子聚合 (2PP) 3D 打印工艺和 (b) 双光子灰度光刻 (2GL) 2.5D 打印工艺中典型体素位置示意图。球面 (c) 和非球面 (d) 聚焦透镜的光学设计。两款镜片的直径均为 300,厚度约为 73,
𝜇m�m 包括 10 𝜇m�m 𝜇m�m 厚底座。透镜颜色为浅灰色,底座颜色为深灰色,基材颜色为浅蓝色。(e) 和 (f) 非球面焦点在 x 和 y 方向上的光束轮廓,包括红色的高斯拟合以及 1/𝑒21/�2 黑色虚线标记的强度。(g) 非球面图案形状与印刷品的比较。(h) 在优化过程中使用多项式函数拟合的非球面透镜的偏差曲线。“ITER 0”和“ITER 1”是指印刷品的未更改和第一次迭代。
激光扫描速度为200 mm/smm/s ,切片和影线距离分别为1 𝜇m�m 和0.2 𝜇m�m 。此外,2GL印刷镜片的多层衰减为0.8。该参数可以在 0 和 1 之间调整,并确定制造过程中的功率调制程度。支撑结构采用 2PP 工艺打印,剖面角偏移量为 90 ∘∘ ,这是 2GL 结构所没有的。非球面聚焦透镜的打印时间为 7minmin 次,双合透镜的打印时间为 15 minmin 次。纯粹使用2PP打印技术制造结构,并且仍然达到相似的形状精度,我们预计这些时间会增加[51]。打印后,通过将样品浸入显影液(mr-dev 600,微光刻胶技术)中25minmin ,然后 minmin 将5浸入异丙醇中并用氮气干燥,除去剩余的未聚合光刻胶。本文中介绍的所有光学结构都印在 170 𝜇m�m 厚的玻璃基板上。
3.球面和非球面聚焦透镜
在本节中,我们将简要概述最基本的 3D 打印光学聚焦组件,即单透镜。直径为 300 𝜇m�m 且厚度为 63 𝜇m�m 的球面和非球面透镜都打印在具有上述 2GL 工艺参数的 10 𝜇m�m 厚基层之上。光学设计和光线追踪仿真使用 ZEMAX OpticsStudio 进行,镜头分别如图 1(c) 和 (d) 所示。对于非球面透镜,我们在球面设计中添加了该术语 𝑎2⋅𝑟2�2⋅�2 ,其中 𝑟� 是透镜的半径,并由 𝑎2=0.6383mm−1�2=0.6383mm−1 OpticsStudio 确定,以实现与球面透镜相比更小的焦点。
通过焦平面上的强度拟合高斯函数来比较焦距 217 𝜇m�m 处的聚焦能力。我们确定 1/𝑒21/�2 球面透镜在 x 和 y 方向上的强度宽度 w 分别为 1.61 𝜇m�m 和 1.65 𝜇m�m 。对于非球面透镜,我们测量 1.18 和 1.16𝜇m�m [图 1(e) 𝜇m�m 和 (f))。在这里,虚线表示 1/𝑒21/�2 -intensity 宽度。仿真结果显示,球面透镜的值为w=1.13𝜇m�m ,非球面透镜的值为0.98 𝜇m�m ,仅比测量值略小。
图1(g)和(h)给出了印刷非球面透镜与设计的比较。这里的“iter 0”和“iter 1”分别是指原始设计的印刷和第一次迭代设计的印刷。当打印结构偏离所需形状超过500时,我们创造了一个适应的设计 nmnm ,可以预先补偿测量的偏差。将 12 阶多项式拟合拟合到测量的轮廓上,确定与设计的偏差,然后将其添加到原始设计中。这是第一次迭代设计,其中的轮廓也如图 1(g) 和 (h) 所示。第一次迭代的偏差在整个镜头轮廓上减小, nmnm 并且仅超过镜头外部的 500。这种通过地形测量迭代结构设计的方法是一种非常强大的技术,将在下一节中详细使用。
由于切片距离为1 𝜇m�m ,因此可以预期与典型的2PP工艺具有相同大小的步骤。由于采用了 2GL 工艺,在图 1(g) 和 (h) 所示的配置文件中看不到此类步骤,这标志着光学元件的出色用例。由于散射更少和波前精度更高,我们预计光损耗会更少。光学性能将在即将到来的空气间隔双合透镜示例中讨论。所有镜头表面均使用共聚焦显微镜(纳米焦点μsurf expert)使用50倍放大倍率物镜测量,数值孔径为0.95。
4. 空气间隔双峰
聚焦光学系统只需要很少的光学活性表面,例如,如上所述的非球面单透镜。光学成像需要更复杂的设计,包括更具光学活性的表面。在本节中,我们将描述和解释设计,分析形状,并检查包含两个非球面透镜的空气间隔双合透镜的光学性能。
4.1 设计
使用ZEMAX OpticsStudio软件创建的空气间隔双合透镜的光学活性表面的设计如图2(a)示。来自离透镜系统无限远的物体的平行光线通过 170 𝜇m�m 厚的玻璃基板透射,并在基板末端撞击直径为 100 𝜇m�m 的孔径,然后进入底部透镜。底部透镜用于加宽光路,以便根据高达 30° 的不同视场角优化顶部透镜,从而实现 60° 的设计视野。由于 2GL 工艺的 2.5D 限制(没有悬垂表面),两个镜头都具有平底和非球面弯曲的顶面。系统的焦距为275,f𝜇m�m 值为3.181,数值孔径为0.154。两个透镜在光学活性非球面周围有一个厚度恒定的环,用于将顶部透镜固定在基板上[图 2(b) 和 (c)]。对于底部透镜,恒定厚度的环有助于测量重要的光学活性表面,并减少通常在透镜边缘最大的形状偏差,参见例如[16]。透镜的光学活性表面的直径分别为114𝜇m�m 和243 𝜇m�m ,整个光学系统的总直径为300 𝜇m�m ,总厚度为197 𝜇m�m 。由于底部和顶部透镜之间存在气隙,因此我们引入了将透镜连接到玻璃基板的支撑结构[图3(a)]。它由八根柱子组成,两端由两个环连接,以实现与基材和透镜的最佳附着力,并提高机械稳定性。在显影过程中,需要在设计中留出间隙以去除未聚合的光刻胶。第二个支撑结构(图3(a)的底部)用作光圈光阑的辅助装置,并放置在底部镜头的正下方。它被设计成一个截断的锥体,底座直径为100, 𝜇m�m 与孔径相匹配。在调整用于表征光学性能的光学显微镜装置的虹膜光阑时,这可作为参考,如下所述。
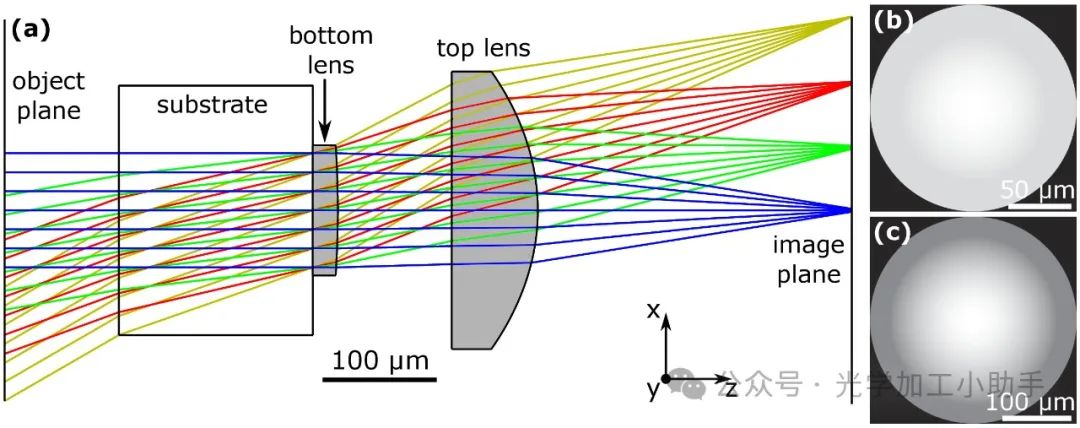
图2.空气间隔双峰的光学设计。(a) 通过透镜系统的光束路径,不同颜色的光线表示不同的视场角(0° 至 30°,步长为 10°)。(b) 和 (c) 分别是非球面底部和顶部透镜的灰度图像。
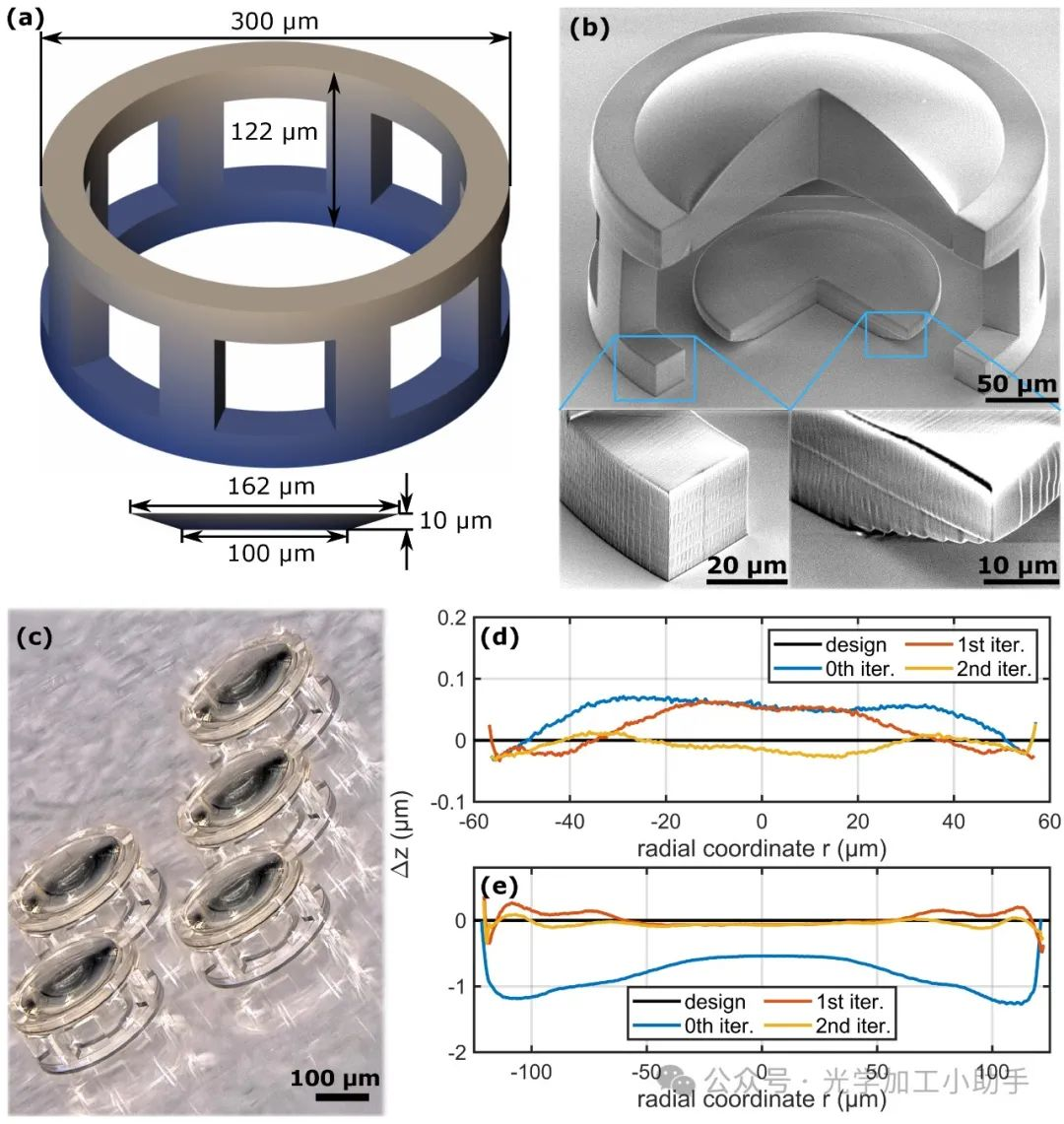
图3.3D印刷的空气间隔双峰。(a) 顶部透镜的支撑结构设计以及底部透镜下方设计的基本结构的侧视图。(b) 空气间隔双峰的扫描电子显微镜图像,该双峰被打印出四分之一的切口,以更好地说明内部结构。顶部镜头和底部镜头的支撑结构的放大图如下图所示。(c) 五个空气间隔的双峰的光学图像。(d) 和 (e):底部透镜 (d) 和顶部透镜 (e) 的零次、第一次和第二次迭代设计偏差,请注意 x 轴的不同缩放。
4.2 形状分析与校正
为了说明空气间隔双合体的透镜表面的形状,我们打印了结构的 3/4 版本,以便对内部进行研究,例如,通过使用扫描电子显微镜 [图 3(b)]。两个镜头的表面是光滑的,没有台阶或其他类型的结构错误。下面的两张小图像显示了原始结构在更高分辨率下的放大。在右下角的图像中可以区分不同的书写模式[图3(b)],其中底部是用典型的2PP工艺打印的,并显示了z方向的步骤,而顶部则由2GL工艺打印,没有任何步骤。特别是左图说明了 90° 剖面偏移角在 2PP 工艺中的使用以及 1 的切片距离 𝜇m�m 。
图3(c)给出了五个空气间隔双峰的示例概述。结构清晰,表面光滑,表明制造过程的可重复性高。
使用前面描述的迭代设计过程优化了两个透镜的形状。我们利用测量的轮廓和设计之间的差异来创建一个新设计,随后将其打印为第一次迭代。然后重复此过程。为了创建第二次迭代的设计,我们将原始设计和第一次迭代的测量轮廓的差异添加到第一次迭代的设计中。
迭代优化过程的结果如图3(d)和(e)所示,表明了底部和顶部透镜与设计的偏差。对于需的形状,底部透镜的表面最初偏差高达 70, nmnm 经过两次迭代后可以减少到 20 nmnm 以下。对于顶部透镜,原始结构在中心表现出 0.5 的形状偏差, 𝜇m�m 𝜇m�m 在透镜边缘增加到约 1.2 [图 3(e)]。第一次迭代消除了中心的大部分偏差,但在镜头边缘仍显示出较大的偏差,这在第二次迭代中得到了改善。镜头主要区域的剩余偏差低于0.1𝜇m�m ,只是在靠近边缘的最外侧增加到更高的值。我们还测量了两个透镜的空间均方根粗糙度Sq,它们通常在4nmnm 到15之间 nmnm 。
4.3 光学性能
我们研究了空气间隔双合体的光学性能。用于成像表征的显微镜装置如图4(a)所示,前面已经描述过[16]。扩散板由白色 LED 照亮,该 LED 由消色差透镜准直。这允许均匀的强度分布进入以下设置。随后,光线通过显微镜物镜聚焦到空气间隔的双峰上。透射光由第二个物镜收集,并由镜筒透镜聚焦到CMOS传感器上。我们在第一个物镜和空气间隔的双峰之间放置了一张美国空军 1951 年的分辨率测试图。为了模拟孔径光阑,将直径可调的光圈插入光束路径中。选择直径和位置,使得虹膜的清晰图像投射到底部透镜支撑结构的底部,并与设计的孔径光阑直径 100 相匹配 𝜇m�m 。
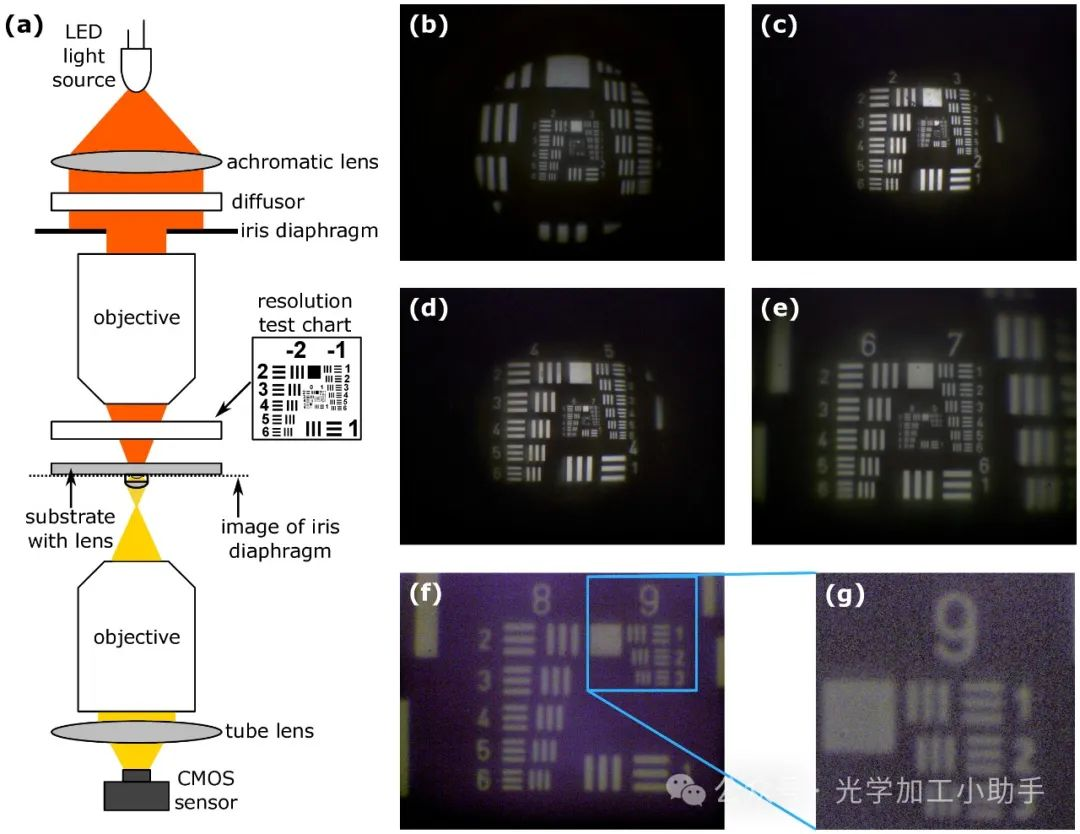
图4.空气间隔双峰的成像性能。(a) 用于测试成像性能的光学显微镜设置,如先前在 [ 16 ] 中使用的那样。(b)-(f) 美国空军 1951 年分辨率测试图表的不同放大倍率,从 (b) 中第 0 组和第 1 组的内线开始,一直到 (f) 中的第 8 组和第 9 组。(g) 放大(f),显示图表第9组的最小元素,对应于645的分辨率 lp/mmlp/mm 。(b)-(f) 在相机传感器上具有相同的尺寸。
空气间隔双峰的成像质量可以通过图4(b)至(g)所示的分辨率测试图表的不同组来检查。为了获得更高的放大倍率图像,目标和空气间隔的双峰之间的物体距离减小了。图4(b)显示了最低放大倍率,并显示了高清晰度和对比度。观察到的桶形畸变和小的色差是意料之中的,因为空气间隔的双合透镜仅设计用于 550 波长 nmnm ,并且由单一材料制成。在图4(c)至(e)所示目标的较高放大倍率下,桶形畸变减少,显示第2组和第3组、第4组和第5组以及第6组和第7组。在这里,我们观察到高对比度和清晰度,尽管测试图表在图像边缘失焦。对于第 6 组和第 7 组,图像没有失真,也没有观察到大的像差。空气间隔的双峰可以解析目标的最高群数,即图4(f)中给出的8和9。在这里,对比度不如较小的放大倍率那么强,并且蓝色调覆盖了图像,这可能是由杂散光引起的。图4(g)给出了第9组的切口,显示了空气间隔双峰的出色分辨率,对应于645的分辨率 lp/mmlp/mm ,其中线的宽度为0.775 𝜇m�m 。市售的 USAF 1951 分辨率测试图表只能获得第 3 组中的第 9 个,这仍然可以解析,这强调了所提出的双峰的光功率。这些测量结果表明了空气间隔双合透镜的出色光学性能和质量。
5. 结论与展望
我们介绍了多种微光学元件的设计、制造和优化。球面和非球面单透镜突出了通过双光子灰度光刻工艺进行的无级打印。在这里,聚焦能力符合预期,并且通过迭代设计过程纠正表面形状的偏差。此外,我们设计了一种视场角为60°的空气间隔双合透镜,表现出出色的形状精度和光学性能。纠正光刻胶收缩的迭代设计过程只留下与所需形状的微小偏差,即底部透镜小于 20 个,较大的顶部顶部透镜小于 100 nmnm nmnm 个。空间均方根粗糙度Sq小至4nmnm .空气间隔双合透镜具有出色的光学性能,具有高清晰度和图像中心高达 645 lp/mmlp/mm 的分辨率。将高形状精度和小表面粗糙度与高分辨率相结合,显示了2GL打印方法在微光学元件上的强大功能。在这项研究中,我们没有考虑折射率的局部变化,如果在印刷过程中使用不同的激光功率,就会产生折射率的变化[55]。虽然它应该只对折射微光学元件起次要作用,但由于切片距离非常小,但了解和研究这种变化可以进一步推动光学能力,并为设计人员提供更多的自由度。由于更复杂的光学设计实现了更多的反射表面,因此可以使用抗反射涂层 [ 56] 或结构化表面 [ 57] 来减少反射损失。未来,可以使用双光子灰度光刻工艺打印多种材料,从而实现更灵活的参数和复杂的设计,如消色差和复消色差[58]。特别是对于量子技术中的应用,例如将3D打印腔耦合到单光子发射器,灰度光刻可以改进现有设计[59,60]。